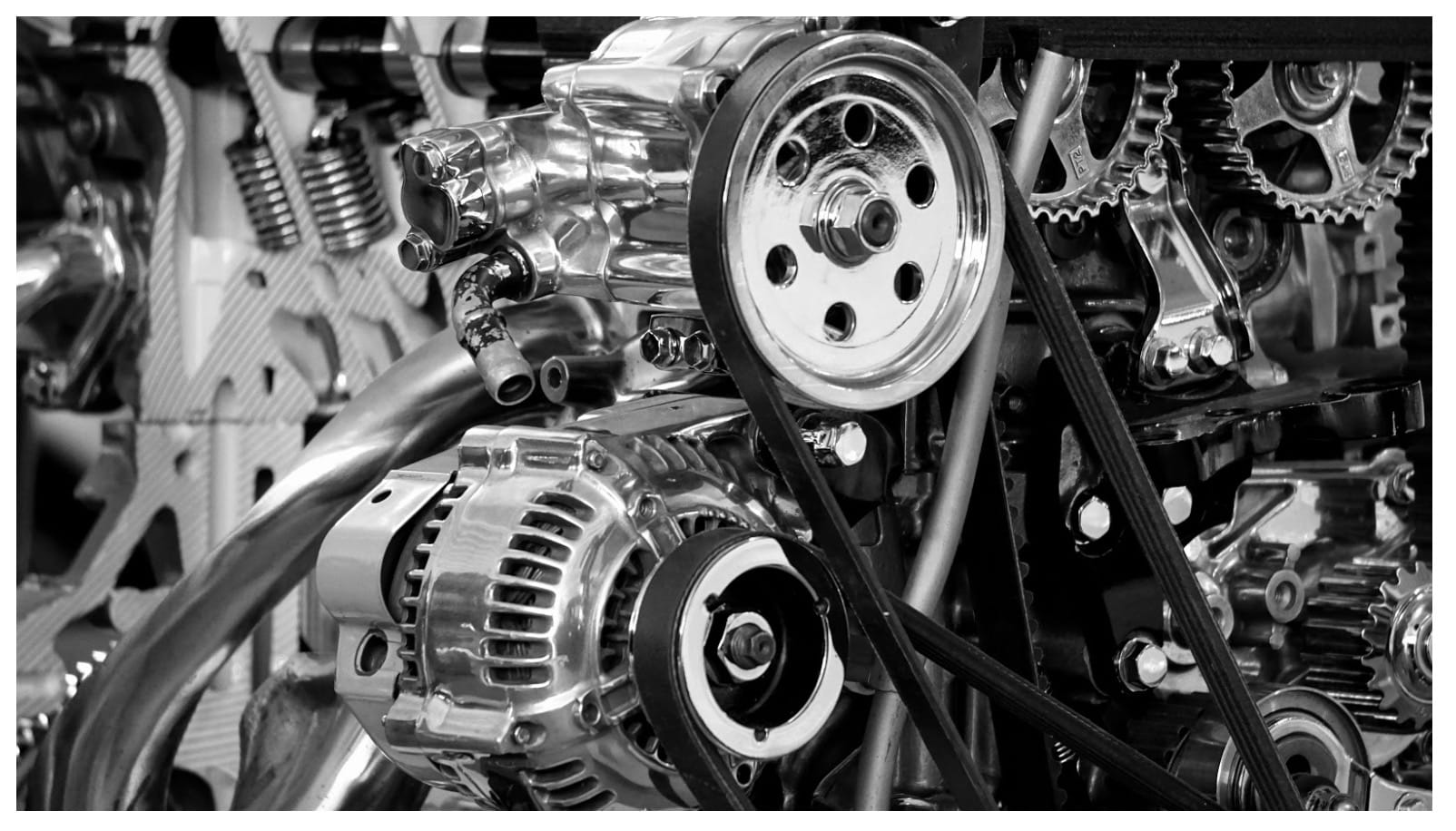
You need to create a solid foundation to build a house. The same holds true when it comes to managing products, changes, manufacturing, and purchasing. With no good foundation, the solution will be sloppy and unstable. The reason why Excel and spreadsheets based solutions are weak is because they don’t provide a solid function to manage data. Excel files contain a bunch of unstructured data that can be often duplicated, cannot be referenced and controlled for transactions.
To establish a proper foundation of product data management is the beginning of any solution to manage Bill of Materials, Changes, manufacturing planning and purchasing. Every single manufacturing companies should be able to establish their data management grounds to control the information about the product(s) this company is developing.
While asking to manage companies, I often get the question about “Where to start?”, For many people trying to bring a solution, it is unclear how to jump from messy Excels spreadsheets to something more organized.
This is the reason to speak first about the definition of an Item (sometimes called “Part”). The debates about a proper name are endless, so for the purpose of this conversation, let’s agree on an “Item” as a term.
The item represents anything you can develop, purchase, or order from other companies to build. The simplest way to think about items is to separate them into two larger categories:
1- Standard Items
2- Engineering Items
The first group is simple and represents everything you order off the shelf. Think of screws, resistors, eclectic motors, paint and anything else your product is using “as is” and you can classify them as standard items
Engineering items are sometimes more complex to understand. You think about them as anything that you are creating. The main difference is that you will be managing changes (and revisions) for any engineering item you do. Engineering items are composed of other items – standards or other engineering items.
Items and Catalogs
OpenBOM is managing items using the catalog mechanism. Catalogs are fundamental building blocks of OpenBOM for data organization. Catalogs help you to define all items and add any properties that will hold information about the items (e.g. Cost, Manufacturer Name, Description, etc.).
A single catalog is already a good starting point, which means all data about items will be centralized, identified with a part number and descriptive properties will provide a single version of the truth about the item.
Once you get you first catalog setup, you obviously start thinking about how many catalogs you need and how properties in each catalog are different to represent different types of items (eg. mechanical, electronic, etc.)
Organizing data and creating catalogs
Data organization is not happening overnight. It is a gradual process that requires time, analyzing of your product data, attributes, and access control. So, I suggest you think about creating catalogs is a gradual process of organizing your data.
As a general rule, simplicity is the most powerful tool in your way of organizing catalogs. Start with a small number, think about how many catalogs you really need and use item classification as the foundation of catalogs you create.
Here is an example of a catalog in OpenBOM
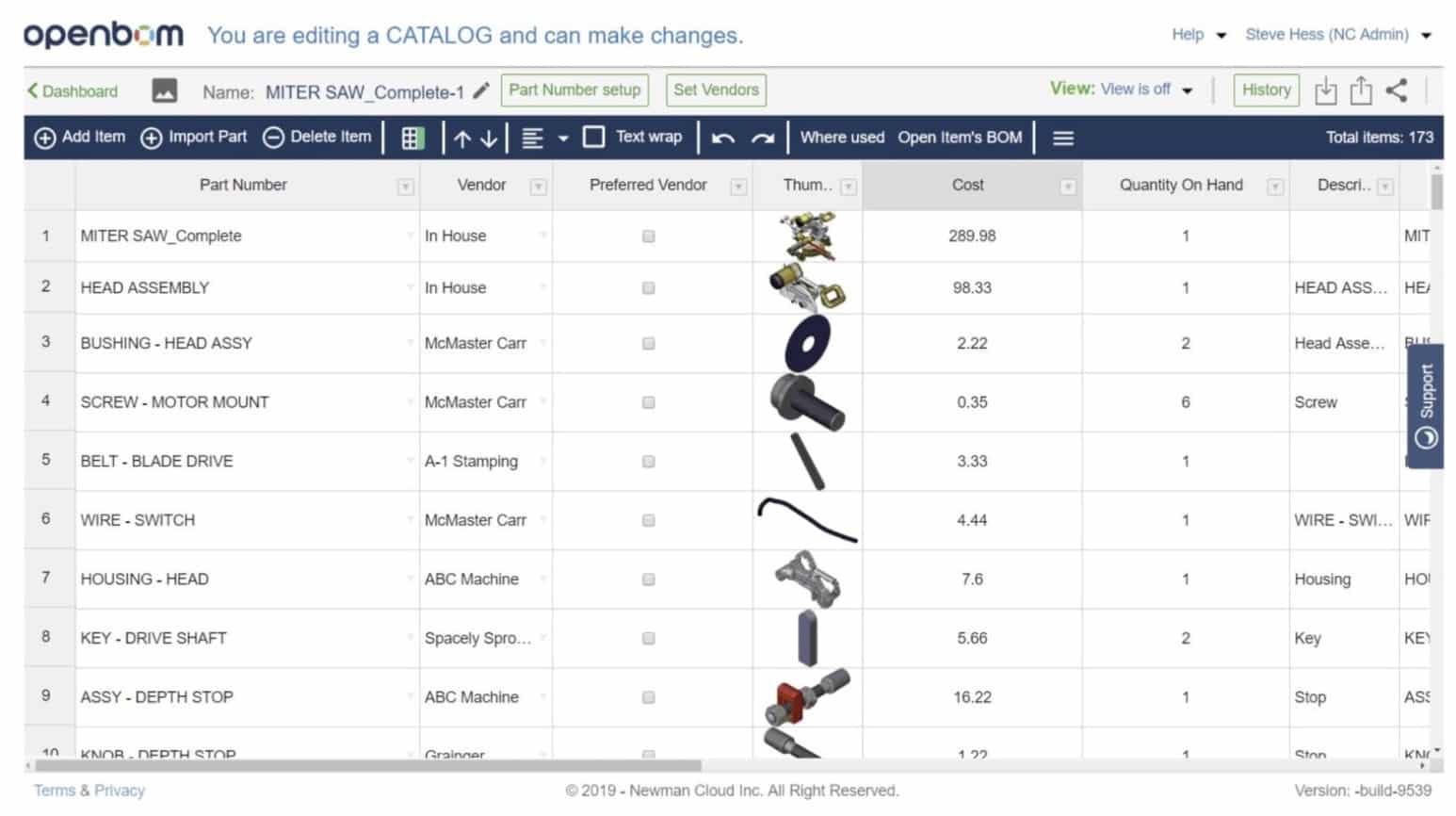
How to Create a Catalog in OpenBOM?
There are 3 ways to create catalogs and manage data about items.
- Manually in OpenBOM – You can create a Catalog from scratch and define a few parts there to build your first BOM directly in OpenBOM. See how to do it in this article here.
- Importing from spreadsheets – You can use OpenBOM’s function to import your pre-existing data from Excel to create a Catalog. Learn the best practices of doing this here.
- From CAD – You can also create BOMs from a CAD system using OpenBOM and later transform it into a Catalog. Read this article to see how to do it here.
Search and Items
While the easiest way to access items is to open a catalog and scroll, filter, search, my recommendation is to use the OpenBOM Item(s) Search dashboard. It is much easier and intuitive to use. Also, it gives you access to ALL items regardless of how many catalogs you have. Also, it gives you an easy way to slice and dice the data as well as to navigate at the same time. Ultimately, it is your choice and OpenBOM supports multiple ways to access and manage the data
Here is an example of the part search dashboard.
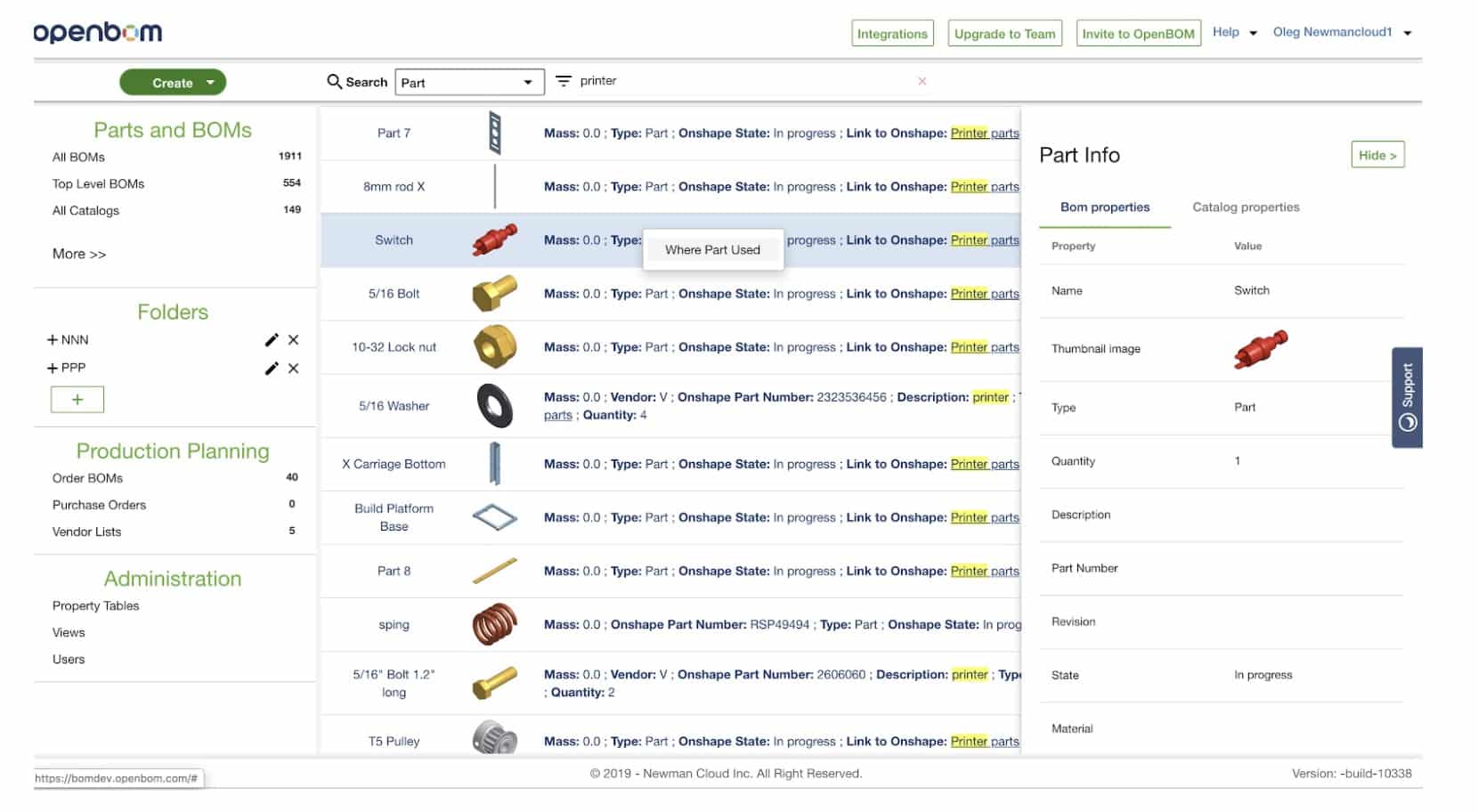
Data Sharing
OpenBOM gives you the easiest possible way to share information about items with anybody you need. Because of the multi-tenant nature of OpenBOM data management, you can share a catalog with any users on OpenBOM platforms as well as any user can share the data with you. It opens a tremendous amount of opportunities to optimize your development processes by organizing data and stopping duplication and sharing data using emails and Excel files.
Any contractor or supplier can provide you with the catalog of items shared on OpenBOM, as well as you can share data with your customer or OEM manufacturing partners.
Conclusion
OpenBOM gives you an easy and scalable way to organize your data foundation of product management – items. It is absolutely flexible and allows you to define every possible variable (properties) for each item. It includes standard properties you can think about (text, numbers, and pic lists) but also attach files and links to other information located in different systems and online.
Check how easy you can start management items by registering for FREE to create an OpenBOM account and import some of your Excels. Learn more about how OpenBOM helps customers to escape Excels and start managing items and related product data.
Best, Oleg @ openbom dot com.
Want to learn more about PLM? Check out my Beyond PLM blog and PLM Book website
Read OpenBOM customer reviews on G2 Crowd to learn what customers are saying about OpenBOM.
Join our newsletter to receive a weekly portion of news, articles, and tips about OpenBOM and our community.