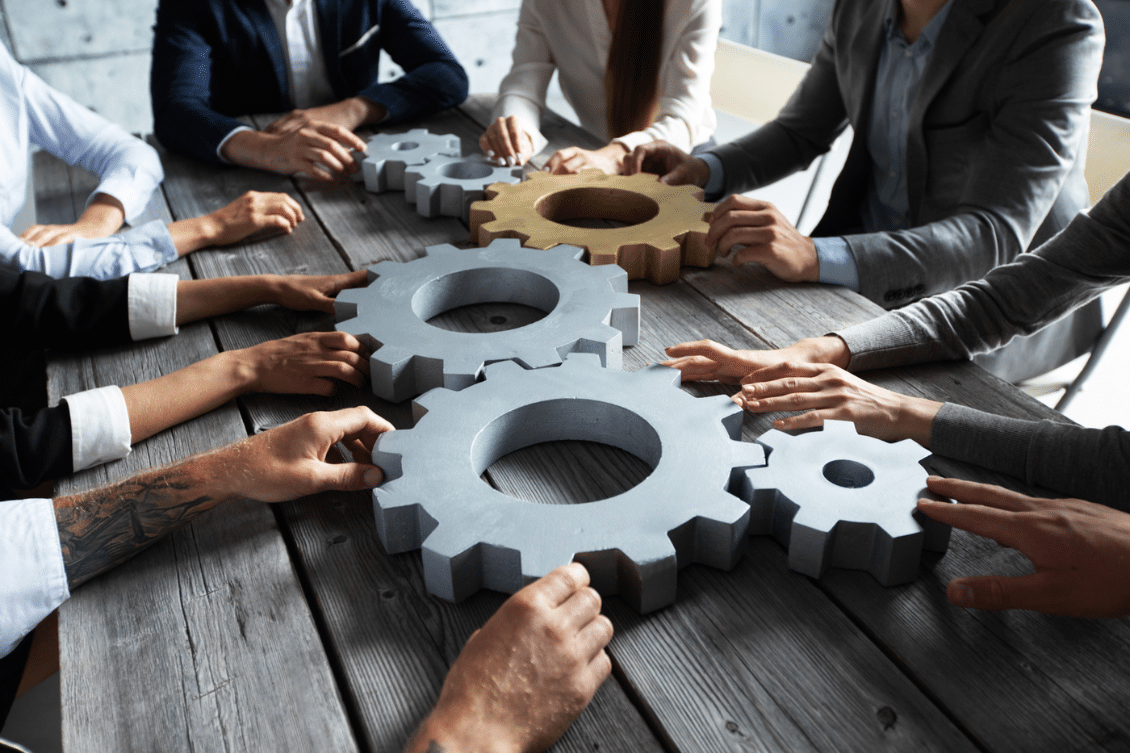
Product development and manufacturing is a team activity. Every product development, engineering, or manufacturing company is familiar with the need for efficient communication between engineers, departments, contractors, suppliers, and customers. The collaborative effort is hard. It requires communication between multiple data silos (raw materials, engineering BOM, inventory management, manufacturing BOM, and many other applications and data sources). Multiple silos are really a big problem for every engineering and manufacturing team. It can be design silos (mechanical, electronics, software) or it can be company department or even cross-company silos – contractors, suppliers, and customers. Smaller companies are struggling to keep everyone on the same page with the lack of IT resources and appropriate systems. However, the problem is not getting smaller with enterprise companies where the problem of multiple enterprise applications exists and presents the same (or sometimes even bigger) challenges in communication.
Companies are trying to keep track of who is doing what and when including corresponding product data (CAD desktop applications) and enterprise applications (eg. material requirements planning, etc.) can bring many data sources – 3D field, bill of materials, etc.), but it works really badly. Existing applications from emails to spreadsheets, from local databases to cloud file storage, from emails to instant messaging and specialized applications such as enterprise resource planning are not very helpful to manage the silos such as engineering bills of materials, manufacturing bills, supply chain data, and many other resources. Companies are trying to coordinate their activities and not lose sight of the data, changes, and related activities.
The result of the struggle is usually presented in multiple “excel dumps” that used as a medium to collaborate between people and data. Once the data is edited or decision is taken, the data is sunched back in source applications (systems of record).
The system of Engagement is a recent trend in the industry that helps manufacturing companies solve the problem. Jos Voskuil speaks about it in his article – System of Engagement as a new PLM paradigm that is going to change the way companies work and use existing data assets. The following picture gives you an idea of the problem.
Now let’s talk about how the modern system of engagement approach is helping solve the problem.
What is a System of Engagement?
System of Engagement is an approach that focuses on leveraging technology to improve efficiency by allowing users to collaborate in real-time. This means that all members involved in the process can view and update information simultaneously, regardless of location. In addition, a system of engagement also helps reduce errors and minimize delays due to manual data entry or lack of communication between departments.
For many OpenBOM customers, we bring pain relief by stopping you from endlessly thinking about how to coordinate between different people and sending them information at the same time. OpenBOM’s real-time collaboration paradigm allows you to share data in real time and make changes simultaneously. Learn more about OpenBOM BOM collaboration patents – OpenBOM announces second patent for multi-member collaboration.
The Benefits of OpenBOM Collaborative Applications
OpenBOM is a great example of a collaborative application that utilizes data collaboration technology. OpenBOM provides manufacturers with the ability to access, manage, and share product data across their entire organization in real-time. It also offers powerful collaboration capabilities such as change tracking, role-based view sharing, and document collaboration making it easier for teams to stay connected even when working remotely. On top of all this, OpenBOM also helps reduce costs by streamlining processes and eliminating unnecessary steps such as manual data entry or back-and-forth emails between departments. Integration with all engineering and CAD systems and Enterprise Applications using iPaaS Nexus demonstrates how OpenBOM can seamlessly integrate multiple data sources together.
Integrating System Of Engagement into Your Manufacturing Process
Integrating OpenBOM into your existing manufacturing process requires careful planning and execution but can yield impressive results once deployed properly. First, you must identify which areas require improvement in order to determine what process would be most beneficial for your company. For many small and medium-sized companies that we are working with, design to purchase process brings the most benefits.
Once these areas have been identified, the next step is to implement an appropriate solution such as OpenBOM that meets the needs of your company while integrating seamlessly with existing systems and processes. Finally, provide training for all personnel involved so they understand how they will be using the new system and how it will benefit their workflows going forward. OpenBOM onboarding training is the opportunity for your company to get up to speed quickly.
Conclusion:
System Of Engagement is a new trend that is coming to revolutionize the way manufacturers operate by allowing teams to collaborate more easily than ever before via collaborative applications like OpenBOM. Learn more from OpenBOM customer stories. By utilizing OpenBOM technology, companies are able to reduce costs while improving efficiency through real-time communication between departments and streamlined processes that eliminate manual data entry or back-and-forth emails between team members. Read an interview with Jonathan Drori, Chief Engineer of Tomcar describing how OpenBOM helped Tomcar. With careful planning and proper implementation strategies in place, manufacturers can reap the rewards from implementing a System Of Engagement within their existing processes quickly and easily!
REGISTER FOR FREE to learn how OpenBOM can help your company today.
Best, Oleg
Join our newsletter to receive a weekly portion of news, articles, and tips about OpenBOM and our community.