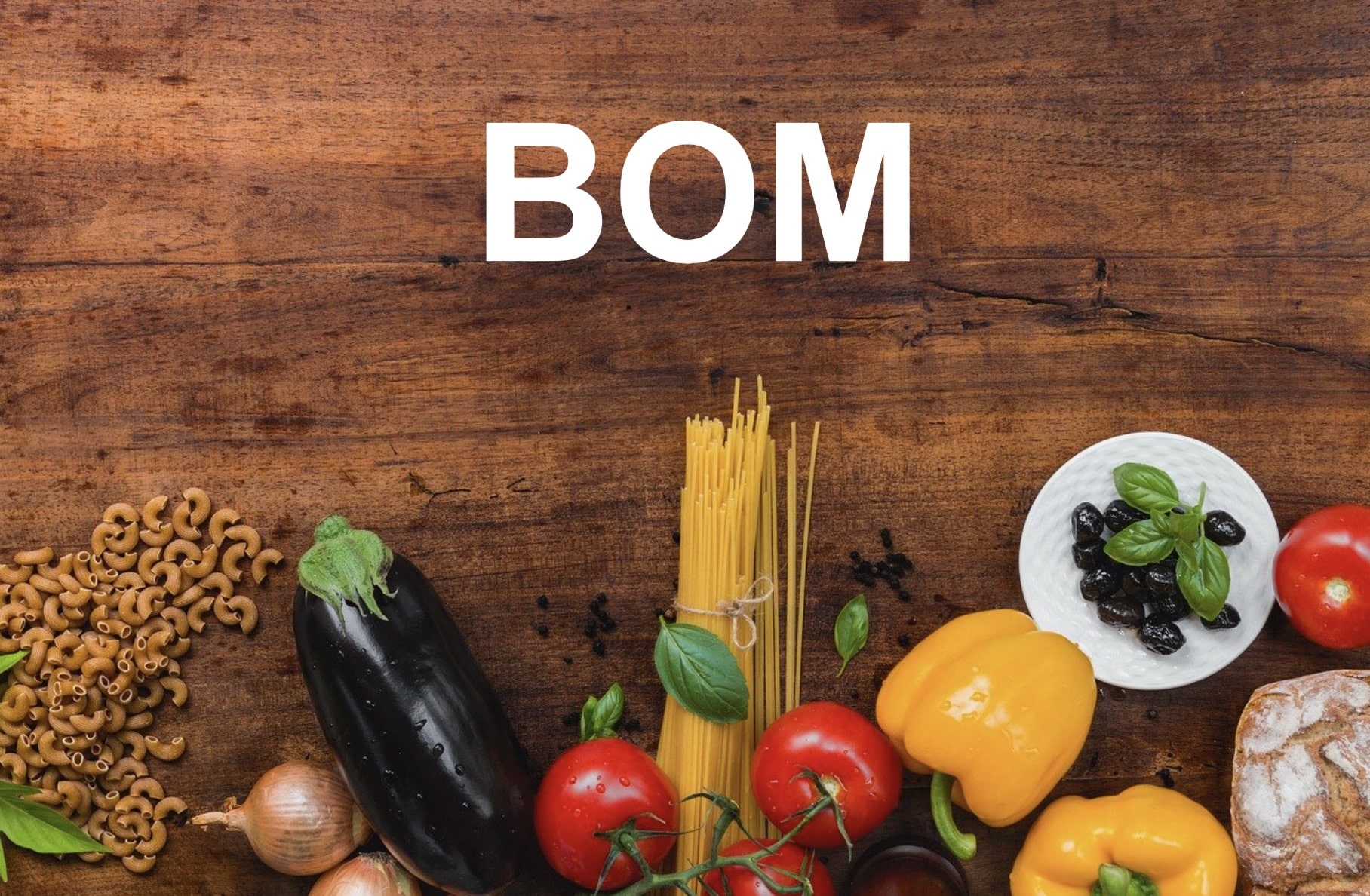
To begin the process of manufacturing, you have to calculate expenses, do resource planning, and do system items. Every case is different, so it’s challenging to calculate the exact prices and not forget any data, such as descriptions or stock numbers.
What is clear is that by adding up exact expenses of maintaining infrastructure and knowing resources, you can increase efficiency and reduce the risks of losses. Proper planning will prepare your business for future challenges.
Using the BOM tool means ensuring you haven’t forgotten any information, and have direct access to parts online. BOM provides value and acts as a resource guide, helping to plan every single move. Want to know more? Then let’s learn how to make a bill of materials!
Forming an extensive list of items for development is a top priority. It includes the production-related documents, sub-assemblies quantities and numbers, supply plan, and other necessary features a business needs. A document has to contain information on how to acquire resources. Let’s see step-by-step directions to know what has to be added to the list.
BOM work order planner helps to simplify management and the development process, leading manufacturers and businesses related to the supply industry have to consider BOM as a powerful tool and see how to make a Bill of Materials.
Quick Start Guide on How to Create a Bill of Materials
The type of BOM you create depends on your brand and business. Individuals focus on two separate types for a brand. The first one is used to build prototypes, requiring additional changes with time. The second one is designed for mass production.
Crucial aspects to focus on are:
- Level of item — level indicates a rank of each item, helping any department to understand current processes;
- Notes — leaving notes is a great way to add extra information that may have been left out;
- Description — component or equipment must have a detailed description, that way you can fully understand a product and avoid confusion;
- Number assignment — every element has to be assigned a specific number; by using number assignment, it would be convenient for all individuals and departments taking part in manufacturing;
- Naming — items, raw material, equipment, and assembly should be correctly named; a component should receive a unique name that lets you quickly identify it. Less time will be wasted when trying to cross-reference each component;
- Phases — a product has a lifecycle that goes through several phases; you may name phases to indicate that a product is not fully ready for a launch or has been tested. By using phases, you can track progress and achieve the greatest results;
- Type of procurement — by using type of procurement, departments can see how to acquire each required element;
- Quantity — it shows the number of required items; quantity helps to calculate the expected costs with maximizing accuracy;
- Reference designators — it shows how an asset fits in a process of manufacturing;
- Units — all components should be assigned proper units like inches or ounces; it’ll help create accuracy when making purchases.
Main Types of Bill of Materials
Before you start, it is crucial to know that you may face various types. How you make a document will depend hugely on what you choose. Here are seven different options:
- Assembly
- Configurable
- Sales
- Service
- Single-level
- Multi-level
- Flattened-level
Let’s talk about the last three levels in more detail. Levels could help your business ensure accuracy when we speak about the management of product structures.
Single-Level Bill of Materials
The single-level structure is the simplest structure of components. It is perfect for products that are not complex. When you have one level of items, components, equipment, raw goods, and assemblies, a single-level type is outstanding. It is not an appropriate option for complex goods, as using it for complex processes can make it difficult for you to track progress. If you need an advanced decision, you may utilize a multi-level method for complex stuff.
Multi-Level Bill of Materials
This is a structure that is more sophisticated and contains several levels required for manufacturing. You can implement a detailed list of all constituents and see a relation between goods.
The sub-parts, ingredients, and completed parts are a part of the multi-level type. From production to delivery, every step is mentioned here. If you wish to have a very smooth and efficient process for complex item production, it could be your choice.
Flattened Bill of Materials
The flattened-level structure is relatively new compared to the previous examples. It includes different parts, and constructions numbered together. What makes it different is that all quantities and the total of all constituents are shown at once.
All elements and respective quantities despite a given level have to be present. Getting a summed quantity helps you understand what is needed to create your brand. A flattened-level structure is essential for complex projects.
It is important to remember that you technically would like to have a multi-level Bill of Material structure and have the capability to turn it automatically in the flattened list with Quantity rollup across multiple levels.
What to Include in a Bill of Materials
To create the final product and prepare a Bill of Materials, individuals need to include all of the components. The parameters to add to your list remain the same, meaning that each line of BOM (to be more useful) has to cover:
- Names of required raw goods — whatever elements you want to include in your final product, names have to be included first. Add a specific name and any details that might be relevant to the production process;
- Variant code — it’s a certain code specific to an item; putting a variant code facilitates activities, allowing users to identify goods;
- Description — all components must be described in detail; it helps to get rid of any confusion, making sure proper equipment will be purchased appropriately. When you provide sufficient information about goods, it will facilitate the assembling work;
- Quantity — always specify the quantity you require to make purchasing more efficient;
- Units of measurement — a part/item should be assigned a unit, as the measured unit depends on what you are making;
- Product color — a tactic that is useful for goods that have a specific color or different variants; it helps to avoid making common mistakes.
To simplify work, you may start adding more details. Additional parameters to include:
- Lead Time — time needed to complete manufacturing;
- Scrap Factor — the percentage of wasted raw elements;
- Done Criteria — parameter shows a number of steps required to assemble components;
- Rollup Cost — an approximation of the total amount you have to spend.
Details you include will depend on what you want and on the type of project you want to build. Complex projects will require more details. Each of the used parameters may affect your business decisions.
Example BOM to Get Started
While creating a BOM is not difficult it can be a daunting task at first. My best examples of Bill of Materials are always coming from food recipes, which is, in fact, a very typical example of BOMs. So, here is an example to help you get started. For simplicity, consider that you want to bake cakes for your business.
The first step is to list components required for baking a cake (it will be your item master’s list. In OpenBOM we usually define it as a catalog).
- Flour
- Eggs
- Milk
- Sugar
- Margarine
- Baking powder
- Baking tray
- An oven
For each item, you need to define additional information such as vendor, cost, unit of measures, etc. Prices with a unit of measure are fundamental because they will allow us to define how to calculate the total cost. You need to also include tools (eg. Oven, Baking tray, etc.).
It is very useful to capture the price (cost). I have never seen a single manufacturer that said that cost is not important.
- Flour: $3
- Box of Eggs: $2
- Milk: $3
- Sugar: $4
- Margarine: $4
- Baking Powder: $0.5
- Baking Tray: $50
- Oven: $500
The list below can give you an idea of the unit of measures. Examples are packet, tray, carton, etc. For simplicity, items that should not be quantified (eg. kg, gallon, etc.) can be defined with EA (each) unit of measure.
The foundation of the bill of materials is a list of products you need to buy. Here is a list of the number of products you need for the cake cooking:
- 1 Packet Flour
- 1 Tray of Eggs
- 1 Carton of Milk
- 1 Packet of Sugar
- 1 Packet Margarine
- 1 Packet Baking Powder
- One Baking Tray
- Oven
Once you create a bill of materials it will look like a structure similar to the following one. It will include a calculated cost, quantities, and additional information. It might be a simple example, but these principles are the same for any product you want to build. Apply similar principles when making complex projects, the basic requirements will put you on the right track!
In the picture below, you can see a sample BOM of the candy box that contains 2 types of candies.
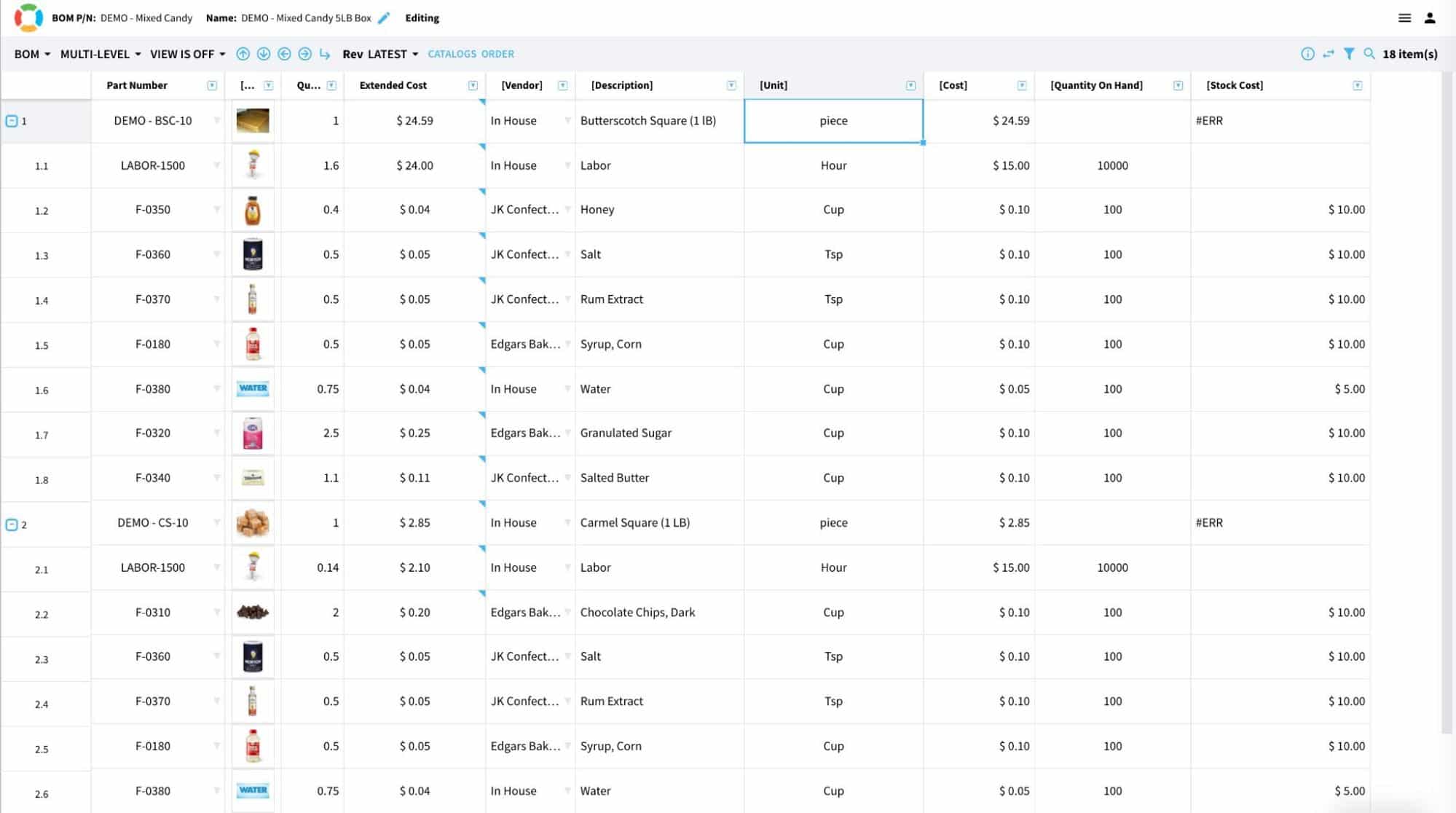
Conclusion
BOM is a great way to ensure efficiency when building your project. It provides a visual representation of all raw items, equipment, and assemblies needed for you to get the final product. The document allows you to calculate costs, reduce expenses, and increase the quality of your brand. The type you choose will depend on the product you manufacture.
BOM can provide overall direction as well as help to handle all operational aspects of production, performance, and implementation. You can ease your life and use OpenBOM production management software to make informed decisions for complex projects. Several of our additional features can make a bill of materials much more valuable, get in touch to learn more!
REGISTER TO OPENBOM for Free and Request your 14-day trial to test all OpenBOM has to offer.
Best, Oleg
Join our newsletter to receive a weekly portion of news, articles, and tips about OpenBOM and our community.