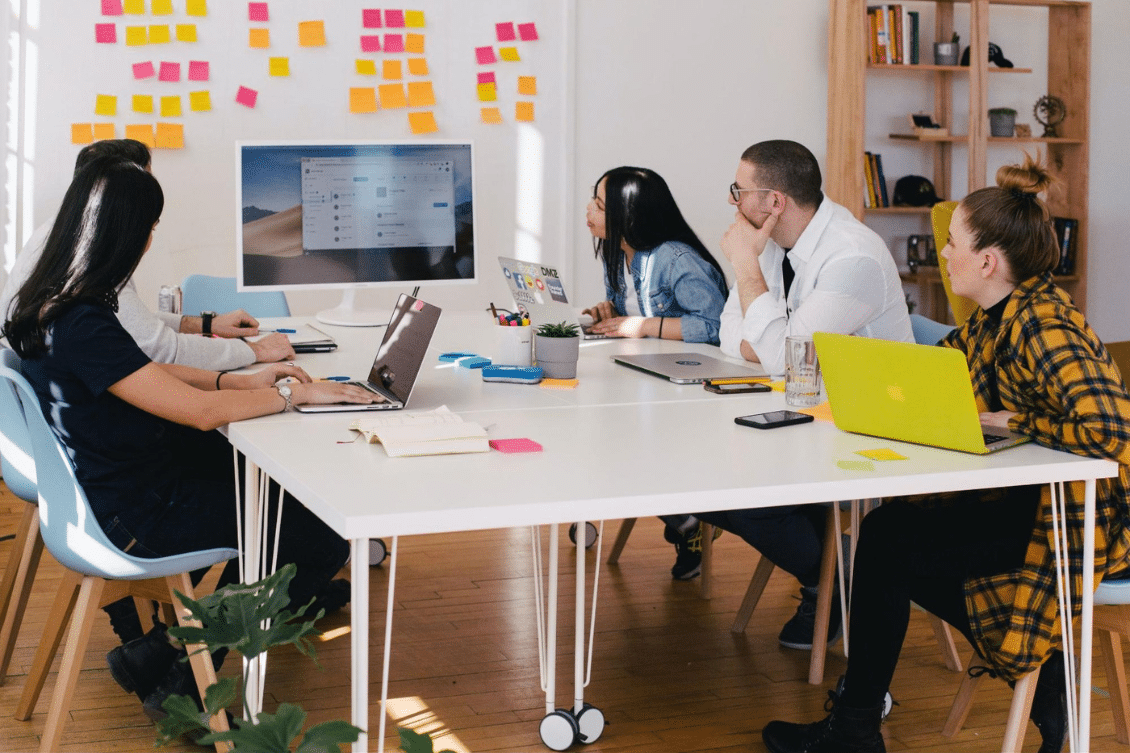
Companies of all sizes have limits on what their team is able to achieve. Manufacturers have realized that they need to leverage the strengths of other companies in order to improve their results. One partner that manufacturers lean on is their contract manufacturing partner.
It is no longer a secret that collaborating with your supplier leads to improvement. McKinsey found that “leaders in supplier development and innovation tend to beat industry trends by ~2x in growth and other metrics.” Yet why do so many manufacturers fail to properly collaborate with their suppliers when the benefits are so clear?
In today’s post, we will look at how manufacturers should be approaching collaboration with suppliers to better leverage their services and knowledge.
Goals of Supplier Collaboration
The main goal to collaborate with your supplier is to improve your business as a whole. This all depends on what your company is looking to achieve. This can be developing more products, decreasing your cost of goods sold (COGS), minimizing quality defects, and more.
Companies that collaborate should not just think of themselves, they should think of the other party. Another main goal of the collaboration is to help your supplier grow as well. If you are able to help your supplier grow then they will be able to hire more people to support you, purchase additional machines, and more. All of these parts that help the supplier grow will also help your company as well.
Here are the main advantages of improving collaboration with your supplier.
- Decrease supply chain risks
- Improve payment terms
- Gain the competitive advantage
- Decrease costs
- Improve quality
- Increase capacity
- Improve your satisfaction
Challenges of Collaborating with your Supplier
Like anything else, collaborating with suppliers has its challenges. Some of them are quite fundamental and can not be fixed. The solution is not necessarily to improve collaboration but instead to change your supplier or change your supply chain strategy. However, you might have a good supplier but still struggle with collaboration. These are the most common challenges of collaborating with your supplier.
Lack of a Leader
No matter what you are trying to push forward, there needs to be a leader that takes control of the project. For collaborating with suppliers, there needs to be someone who sets the strategy of improving collaboration that can bleed through the organization. Make sure there is a leader.
No Change Management Process
Another common problem is that there is no change management process between you, the manufacturer, and your supplier. One reason why manufacturers lose trust in their suppliers is that the supplier made changes behind their backs or they did not communicate these changes properly.
Providing your supplier with a process to go from creating change requests to accepting changes will enhance collaboration. This will also prohibit any unauthorized changes from being made.
Lack of Proper Tools
A lack of proper tools leads to working in separate data silos. I know, we all love spreadsheets and your supplier is very familiar with them. However, there is no traceability to changes or revisions. All of these can lead to basic mistakes in working with old data. If you are using a tool, like OpenBOM, then bring on your supplier as well.
How to Improve Supplier Collaboration
If you are ready to take the steps forward to improve your collaboration with your supplier then here are some things that you will need to review.
What is the Strategy?
Before you proceed, you need to define what you are looking to accomplish. Are you looking to improve your costing, your lead time, your quality, or your new product introduction (NPI)? Depending on what your strategy is, you will need to build tactics to be successful.
Improve Communication to Build Trust
The sharing of information must flow freely from one organization to another. Also, improving the way you share data will also improve your overall communication and trust with your supplier. Providing the proper tools to share data will help improve trust with your supplier.
Transparency into the Supply Chain
The majority of manufacturers do not have visibility past their tier 1 supplier. In order to collaborate you must have the entire view of your supply chain. If your contract manufacturer is not willing to provide this then collaboration will be difficult.
How to Start Improving Collaboration with your Supplier Today?
The big step to improving collaboration with your supplier is to provide them with the tools in order to succeed. One of the biggest trends in manufacturing is transitioning to the cloud and starting your digital transformation journey.
OpenBOM is a cloud-based PDM & PLM platform to manage your engineering and manufacturing data. Companies from startups to Fortune 500’s use OpenBOM to create a centralized database to bring in, store and manage their manufacturing data. With this infrastructure, users also use OpenBOM to streamline both their change management and PO processes.
If you need to improve the way you manage your data and processes, contact us today for a free consultation.
Regards,
Jared Haw
Join our newsletter to receive a weekly portion of news, articles, and tips about OpenBOM and our community.