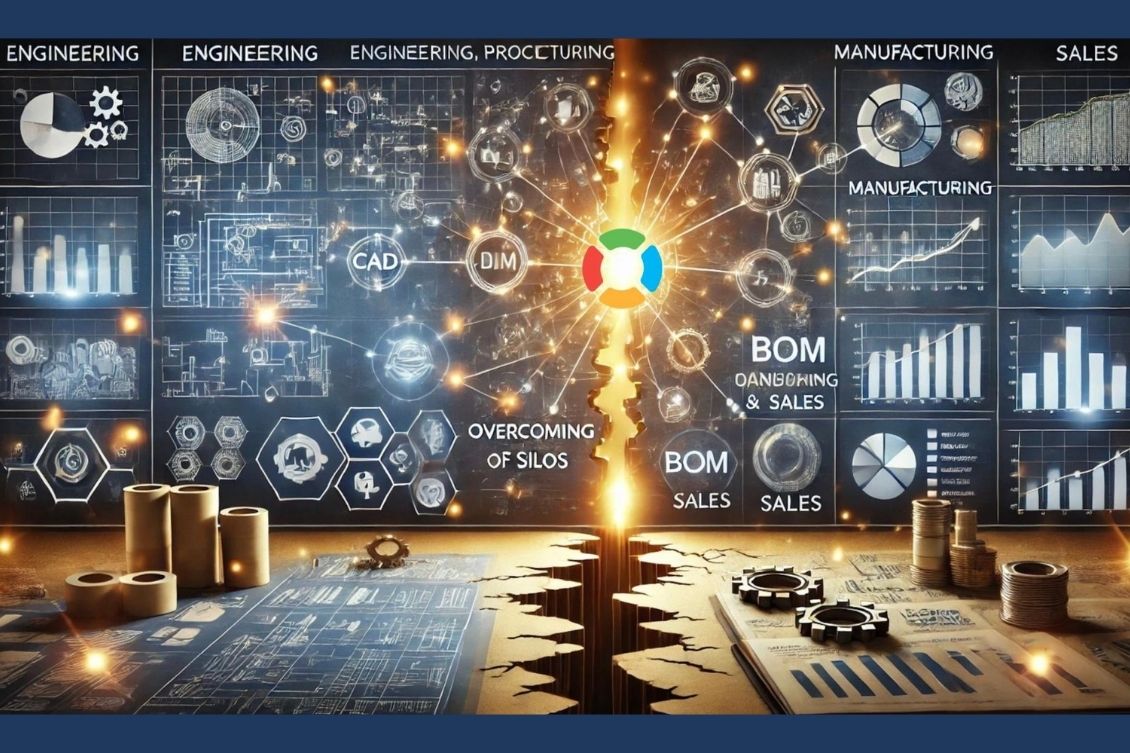
Engineering isolation hurts production and business. In many manufacturing companies, engineering operates in its own silo – disconnected from production and business functions. While this separation may seem natural due to the specialized nature of engineering work, it often leads to inefficiencies, miscommunication, and costly delays.
The reality is that product design doesn’t exist in a vacuum. Decisions made in engineering directly impact production timelines, procurement processes, and business outcomes. When these functions don’t share data seamlessly or collaborate effectively, companies face inaccurate BOMs, missed deadlines, and frustrated teams.
At the same time, a seamless flow of information between engineering and business teams is essential. Engineering data is no longer confined to CAD systems or siloed spreadsheets; it must connect with procurement, operations, sales, and other departments to drive efficiency, reduce errors, and streamline decision-making.
In this blog, we’ll explore why this siloed approach persists and why breaking down these walls is critical for driving agility, improving decision-making, and staying competitive in today’s fast-paced market.
“Over the Wall Manufacturing” Gaps and Challenges
“Over-the-wall manufacturing” was the old way of doing things where engineers and production teams worked in isolation. Engineers would focus solely on designing a product, and once they were done, they’d throw the designs “over the wall” to the production team and wait for them to build it. The problem?
There was little to no communication between the two sides. When production teams ran into issues—like design flaws or parts that were hard to manufacture – it often meant delays, costly rework, and plenty of frustration. Instead of working together to solve problems upfront, engineers and manufacturers were stuck reacting to issues after the fact. This siloed approach made it clear that real collaboration and better communication were essential to avoid all the back-and-forth and wasted time.
The roots of this process are going back years. Traditionally, engineering teams work in CAD systems, developing 3D models and drawings, producing detailed designs, approving drawings, creating part lists (bill of materials), and… looking at how to send it to manufacturing (or customers, contractors, sales) However, this data and the entire process often remains isolated, leading to challenges:
- Manual Data Transfers: Exporting and re-entering data between CAD, ERP, and Excel can result in errors.
- Lack of Real-Time Visibility: Other departments lack up-to-date access to engineering information.
- Data Inconsistency: Misalignment between design changes and business processes causes costly delays.
What are the alternatives? Although “export excel” and “export PDF/STEP” files are available in all systems, the entire process is cumbersome and questionable. This is where we meet many of our customers.
At OpenBOM we wanted to create a better way for companies to connect different departments and roles by making data easily available and seamlessly shareable with everyone else. Let me talk about it in more detail.
Unified Data for Engineering and Business Teams
The foundation of everything we do at OpenBOM is a data platform – a new way we invented to organize information, make this platform flexible, and able to manage product information in a robust, easy, and (at the same time) very simple way. The flexibility and robustness of the model are combined with a simple “spreadsheet” like user experience. OpenBOM creates a unified data model that integrates engineering, manufacturing, procurement, and sales information. Here’s how we do so:
Graph-Based Flexible Data Model
The OpenBOM data model is built on a graph-based, flexible architecture that enables seamless connections and relationships between various data elements across the product lifecycle. Unlike traditional hierarchical or tabular data models, OpenBOM’s graph-based approach allows for dynamic linking of items, BOMs, and related objects, creating a web of interconnected data. This flexibility supports multiple views and representations, such as engineering, manufacturing, and service BOMs, while maintaining a single source of truth.
The foundation of this model is a simple idea of a “data object” that can be anything you like. Predefined data objects such as “Design Projects”, “Item Catalogs”, “Bill of Materials”, “Vendors”, etc. can be extended by customers in real-time and allow to add other “custom objects” such as “Requirements”, “Products”, “Projects”, “Tasks”, and many others. The model is highly extensible, enabling users to define custom properties, establish object references, and manage complex product structures with ease.
By leveraging this graph-based data model, OpenBOM facilitates real-time collaboration, enhances traceability, and supports the digital thread, empowering teams to manage and evolve product data efficiently.
Seamless CAD Integration
OpenBOM integrates natively with popular CAD tools like SolidWorks, Autodesk Fusion 360, PTC Onshape, and many others. When engineers design parts and assemblies, OpenBOM automatically extracts the data using the “One Click BOM” command. The data extracted, included:
- BOMs (Parts, Assemblies, Quantities)
- Item Properties (Materials, Cost, Specifications)
- References and Attachments (PDFs, Drawings, Documents)
This ensures that engineering teams don’t need to manually export data, and the latest design information is always available. The outcome of that is a very simple data representation, visual, and connected. On one side, it is simple and similar to “spreadsheets” (everyone loves), but on the other side, it has all links, files, revisions, 3D preview, hierarchical and graph visualization.
Collaborative and Connected Bill of Materials
The heart of OpenBOM’s platform and data model is its flexible, real-time xBOM management system. Unlike static spreadsheets, OpenBOM provides:
- Real-Time Updates: Any changes made to a BOM are instantly visible across departments.
- Multi BOM Types: Each department and function can tailor the BOM model (xBOM) to create multiple BOM representations (engineering, manufacturing, sales, maintenance, etc)
- Multi-View BOM: Different teams can see BOMs in views tailored to their needs by limiting what attributes each user will see, be able to edit, etc.
- Real-Time Collaboration: OpenBOM’s unique collaborative methods allow multiple users to edit and see updates in real-time (similar to Google Spreadsheet). Teams can work together on the same data, ensuring alignment.
Real-Time Data Accessibility Across the Business
OpenBOM breaks down borders between organizations and ensures that critical engineering data flows seamlessly across the business. For example:
- Procurement: Purchasers get instant access to accurate part numbers, suppliers, and quantities for ordering.
- Operations: Manufacturing teams use BOMs to plan production schedules and optimize processes.
- Sales: Sales teams can access product configurations and costs to respond quickly to customer requests.
This approach allows everyone to get the information and most importantly to do it with the user experience that reminds everyone of special spreadsheets rather than a complex database (aka PLM) This unified approach ensures that everyone is working with the same accurate, real-time data.
Enhancing Decision-Making with Analytics and Traceability
OpenBOM’s data model doesn’t just connect engineering with the business; it provides a set of very specific functions that help you to perform valuable insights and improve decision-making:
- Cost Rollups: Automatically calculate the total cost of products and assemblies, helping procurement and finance teams optimize budgets.
- Analytic “Where Used” and Other Queries: Out-of-the-box functions allow you to make structured queries to perform analytical requests such as “What parts are not used anywhere” or “What is the most important supplier?”
- Change Management: Track revisions and changes to product data is supercritical and OpenBOM ensures traceability across all changes done in all data objects (eg. Catalogs, BOMs, etc)
- Inventory, Production, and Contractors Visibility: Connect vendor information to parts and BOMs to streamline supplier selection and ordering processes. The data connects and becomes available in financial systems, MRP/ERP, and CMs.
With OpenBOM, businesses gain full visibility into their product data, enabling faster, data-driven decisions.
Conclusion:
Manufacturing companies and engineering teams demand connected, real-time information that flows effortlessly between engineering and the rest of the company. OpenBOM product lifecycle management software goes beyond a traditional product data management systems focused on the management of files, but provides you with a tool to convert your product development process into a robust business system capable of containing both engineering and product data together with information needed for inventory control, supply chain management, quality management, product quality, and supports data sharing for entire organization. Unlike traditional PLM software, OpenBOM introduces functions that are typically available in enterprise resource planning software – managing inventory and purchasing (we will talk about it in a different article).
OpenBOM delivers exactly that, breaking down silos and enabling teams to collaborate seamlessly. The vision of OpenBOM is simplicity combined with robust data management. By ensuring engineering information is always accurate, accessible, and up-to-date, OpenBOM empowers businesses to make smarter decisions, reduce costs, and drive success.
OpenBOM is the solution that bridges the gap between engineering and business. Are you ready to experiment with OpenBOM and see how it will take care of your data? REGISTER FOR FREE and start your trial today.
Best, Oleg
Join our newsletter to receive a weekly portion of news, articles, and tips about OpenBOM and our community.