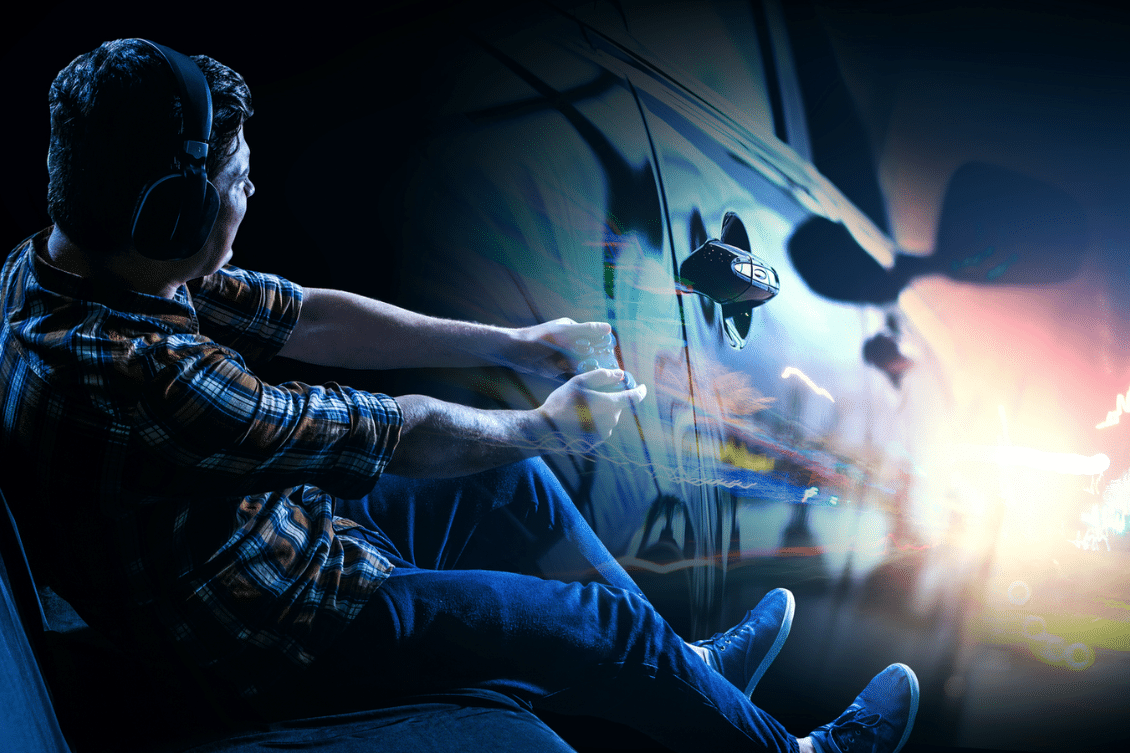
Bills of Materials (BOMs) are crucial for product development and product lifecycle management, as they define the basis for managing product information in manufacturing organizations. Industrial companies call BOMs by different names, but fundamentally, BOMs are the foundation of any product development and manufacturing process. It includes all information needed for design, engineering, production planning, inventory, and cost. Organizations are looking for different BOM representations – engineering BOM, manufacturing BOM, production BOM, supply chain processes, and others. Without having all elements of BOM in a comprehensive way, you cannot expect your product development efforts to be effective and to bring the desired results – a fast new product development process where all members of the team are working together and delivering the best new product.
Dual Role of BOM Management Architecture?
Engineering.com article When Bills of Material Hinder Product Development written by Lionel Grealou speaks about enterprise BOM architectures.
Bills of Material (BOMs) are essential for managing product deliverables in manufacturing organizations, but they can sometimes hinder operations due to rigid or obsolete design choices. BOMs should be flexible and dynamic, focused on managing product modularity and variability. The enterprise BOM approach, which involves integrating BOMs across the organization, can reduce complexity and improve efficiency. However, it also poses challenges due to the need to balance data segregation and synchronization.
Effective BOM management requires aligning BOMs with organizational design, adopting a platform approach to maximize data reuse, and establishing data governance and stewardship capabilities. BOMs can hinder operations if they rely on manual, file-based processes, have limited data continuity across domains, or use overlapping and poorly integrated enterprise systems. A multi-view BOM approach may also be challenging if it assumes the same velocity and timing across all enterprise functions.
Here is an important passage outlining the important role of BOM management as a function to support collaboration and new product development:
Some business leaders misinterpret the purpose of BOMs. It is not about building a static representation of products; instead, it is about a flexible and dynamic approach to managing product modularity and variability. BOM management practices cover aspects of both product and business-related capabilities. This includes considerations such as how companies: Operate and drive product and process changes; Generate and test innovative ideas, concerting concepts to development initiatives; Collaborate across internal functions and with external parties; Configure their product options and variability across alternates, substitutes, features, colors and more; Source components, materials, and associated services; Industrialize products and scale production; Simulate and track revenue and productivity; Track product changes and drive associated decisions and mitigations; Reuse components and optimize supply chains.
What is really interesting is to see how the list of activities and tasks covers the full scope of a typical NPDI (new product development introduction) process.
The article made me think about the dual role of the BOM management function in a complex enterprise organization and attempts to balance between two goals – (1) to have a full representation of the data, fully traceable and covering all aspects of product definitions and connection all lifecycle states; (2) to provide a BOM service to engineers to perform product development goals and realizing the idea of modularity and variability.
Enterprise PLM systems seem to be focusing on both. As a result, most enterprise PLM systems are serving as SOR (system of records) for product information and missing the second goal to help engineers and everyone else in the organization to engage in designing the best product using the most accurate information in the fastest way. Many companies are complaining about complexity of use of PLM for NPDI and opt-out for Excels and other DIY tools to help them with NDP.
NPDI Process and BOM Collaboration Function
My absolute favorite passage from the article speaks about the Siemens survey published by CIMdata:
Following a survey commissioned by Siemens, CIMdata reported on the “Importance of an Enterprise BOM.” Interestingly, according to the results, “Almost half [of the industrial respondents] said their BOM management approach hurts their business, even though 22 percent say they already have an enterprise BOM capability.” This suggests that core challenges relate to how BOM management practices are implemented.
For all manufacturing organizations, New Product Development and Introduction (NPDI) function is a critical process that ensures companies can deliver new products within the shortest period of time. It is a vital process for businesses striving to maintain their competitive edge in a modern market. Efficient BOM management is a core function of this process. The inefficiency of this function can make companies miss their deliveries and slow them down.
At the same time, a large number of enterprise organization is suffering from the ineffectiveness of existing enterprise PLM tools. While these tools are comprehensive to hold product information as SOR (systems of record), they fail miserably when used to manage new product development. The usability of the tools, combined with the complexity of processes and enterprise integrations makes these tools suboptimal and pushes engineering teams to use a variety of tools such as custom Excel spreadsheets and local data management solutions for collaborative work needed for the NPDI process. Even more, the gaps in providing analytics such as early visibility on BOM costing and supply chain management analysis hinder engineering teams even more.
Here are some hypotheses we developed at OpenBOM, on how to help NPD teams of large enterprise companies to develop better, faster, and cheaper using OpenBOM patented BOM collaboration methods.
1. Centralize BOM data for NPDI
A centralized BOM management system can streamline communication among all stakeholders and enhance collaboration. This approach allows for real-time access to BOM data, which can significantly reduce the chances of errors and miscommunication. This BOM data can be easily updated in real-time and provide full traceability of the new product
2. Multi-Tenant BOM With Instant Data Sharing and Simultaneous Editing
Transitioning to a cloud-based multi-tenant BOM management system can offer numerous benefits. Cloud-based platforms provide real-time access to BOM data from anywhere, allowing stakeholders to work collaboratively and make informed decisions. Data can be instantly shared and multi-tenant characteristics of the system can help companies to share data across multiple stakeholders in different companies involved in NPDI.
3. Foster Cross-Functional Collaboration
Encouraging cross-functional collaboration is essential for effective BOM management. By involving various departments, such as engineering, manufacturing, procurement, and quality assurance, organizations can ensure that all aspects of the product development process are considered. This collaborative approach can help to identify potential issues and roadblocks early, reducing the likelihood of costly mistakes and delays in the NPDI process.
4. Seamless data integration with existing engineering and enterprise systems
By supporting broad and seamless data integration with engineering (CAD) and enterprise PLM and enterprise resource planning ( ERP) systems or records, the new NPDI tool can ensure, engineering teams will be getting easy access to all information without being involved in the complexity of existing SORs (system of records).
5. Leverage Automation and AI
Embracing automation and artificial intelligence (AI) in BOM management can lead to increased efficiency and reduced human error. Automated systems can help identify discrepancies and potential issues in BOM data, allowing for faster resolution. Furthermore, AI can be utilized for predictive BOM creations (copilots), cost analytics (BOM costing), offering insights into potential component shortages (supply chain analytics) or cost fluctuations that may impact the product development process.
Conclusion
Rethinking BOM management is a crucial step toward improving the efficiency of the NPDI process. By centralizing BOM management, implementing cloud-based systems, fostering cross-functional collaboration, employing a modular BOM approach, leveraging automation and AI, and maintaining accurate and up-to-date BOM data, organizations can significantly enhance their product development processes. It is important to separate the existing system of records (SOR) from this novel approach to enable easy and collaborative fast-running processes. These improvements can lead to reduced lead times, increased efficiency, and better collaboration among team members, ultimately contributing to the organization’s success in the competitive marketplace.
REGISTER FOR FREE and check how OpenBOM can help you.
Best, Oleg
Join our newsletter to receive a weekly portion of news, articles, and tips about OpenBOM and our community.