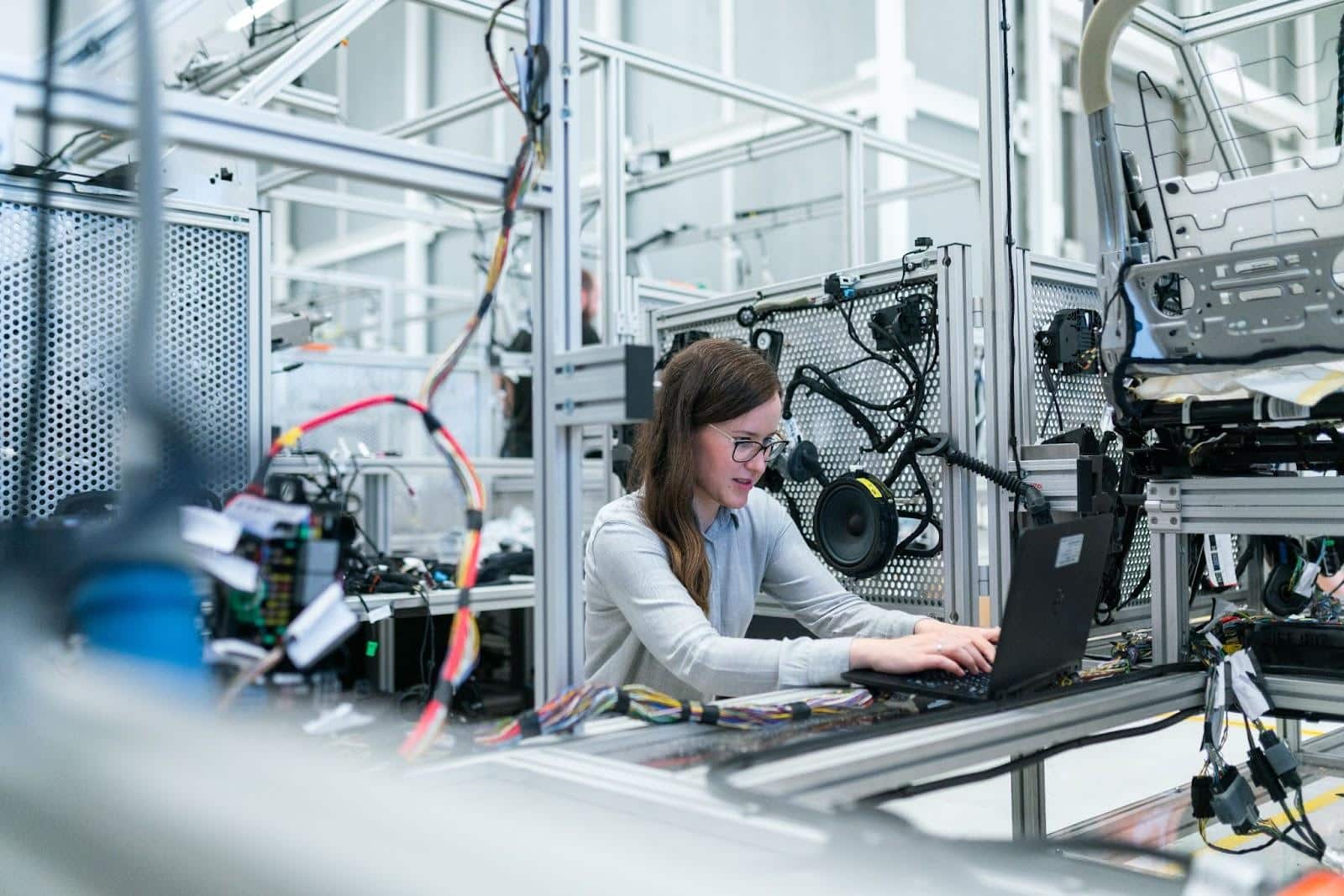
As the global supply chain complexities grow, so do the risks associated with manufacturing. Manufacturing companies, their contract manufacturers, and their suppliers have all been negatively affected by the economic downturn.
We have always known having alternative suppliers was important to limit our exposure to a single supplier shutting down. Unfortunately, not many manufacturing companies had alternative suppliers. If they did, it was just a contact in their phone in case the apocalypse came. But once that day came, their alternative supplier was not properly prepped to quickly take over production or to support a transition period.
The main problem is that the alternative contract manufacturer (CM) or supplier was not prepped because they did not have the product data in order to proceed quickly. This post will go over the traditional way of handing over files to your CM vs how sharing files with your CM should be done.
Traditional Way of Sharing Files
Traditionally speaking the first and only time you share product data with your CM would be during the request for quotation (RFQ) step. Usually, that was done as a data dump. Meaning you organize all of your data into folders, zip it up, and send it to your CM via Google Drive, Dropbox, or by whatever means.
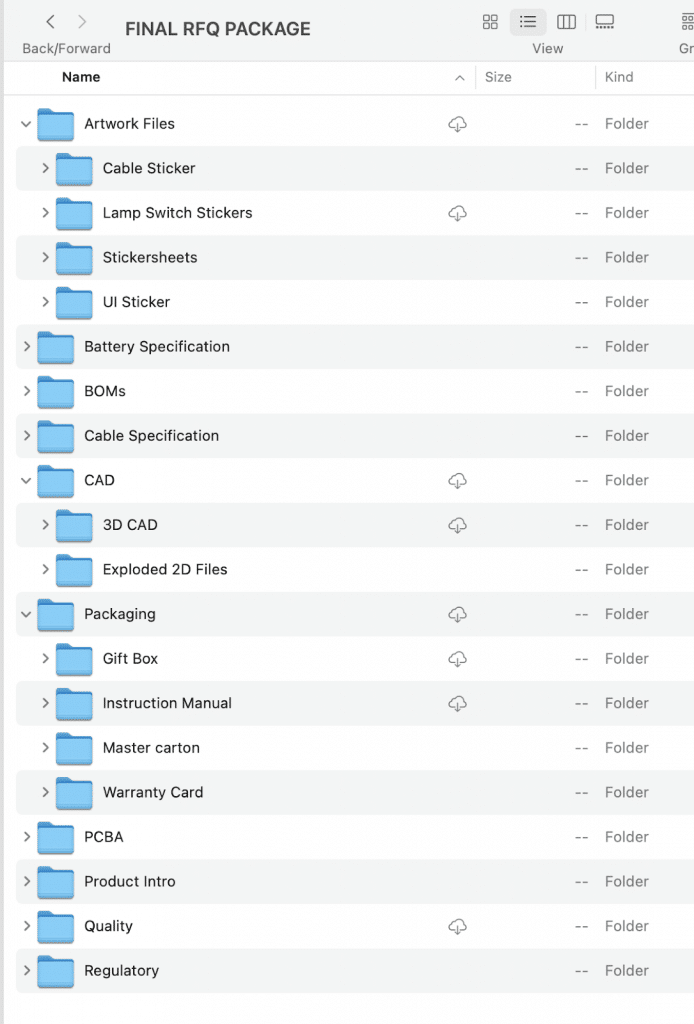
Here are some of the folders and the information included.
Artwork Files
Whether it’s marketing material, your logo, or a sticker from a certification agency, the artwork is important. It is important to share the Ai or PDF file of the location and of the content related to the sticker.
BOM
Your bill of materials (BOM) holds the manufacturing knowledge of your product. The BOM is also the tool your CM will reference most frequently. Everything should be reflected in the BOM. Unfortunately, the BOM is usually not treated with the respect it deserves. Failing to manage your BOM correctly is the first step of poorly sharing data with your CM and keeping everyone on the same page (or BOM).
CAD Files
Sending CAD files to your CM also needs to be taken seriously. Similar to BOMs, sharing and naming CAD files are usually not done correctly. It’s common for manufacturing companies to create a folder called CAD files and send it to the CM. Manufacturing companies will also name these CAD files in a few ways, such as:
- Revised Date_Part Number_Part Name.STEP (20221014_SH6532_Controlbox.STEP)
- Part Number.STEP (SH6532.STEP)
There are also a few more varieties but these are the most common. While these are common and can help the CM during the original RFQ, it is not sustainable going forward. Parts change, parts are added, specifications change and by the time you want your alternative supplier to re-quote or start tooling, the data they were working with might be outdated.
Quality & Assembly
Detailed files on how to check the quality and how to assemble the product are important. There needs to be standard operating procedures (SOPs) and standard inspection procedures on how to check the quality and how to assemble the product.
Traditional Way – Traceability and Accountability Problems
Sending files and managing data using excels has been the norm. Excels are widely used by everyone and they are easy to read and use. Unfortunately, when it comes to the risks of using Excel, there are many limitations. Here are the problems of sharing data the traditional way:
- Create data silos
- No single source of truth or centralized system
- No automatic sharing
- No integrations with CAD systems
As a result, you rely on sending product data to all parties. Whenever there is a change, you need to quickly email all stakeholders.
If all stakeholders are not using the most updated files then you can expect the following:
- Purchase incorrect parts
- Unable to properly plan production
- Outdated specifications, quality requirements, and assembly instructions
- Not knowing your costs
The biggest problem of this method is the absence of traceability and accountability for the information exchange. Old data can be easily passed without tracked in the history.
Modern way to share data using OpenBOM
The way manufacturing companies share data today is different. They still share the BOM, CAD files, artwork, quality requirements, assembly steps, and more. However, the execution is different. Today, it is done by automatic data sharing rather than emails. Let’s dive in a bit more.
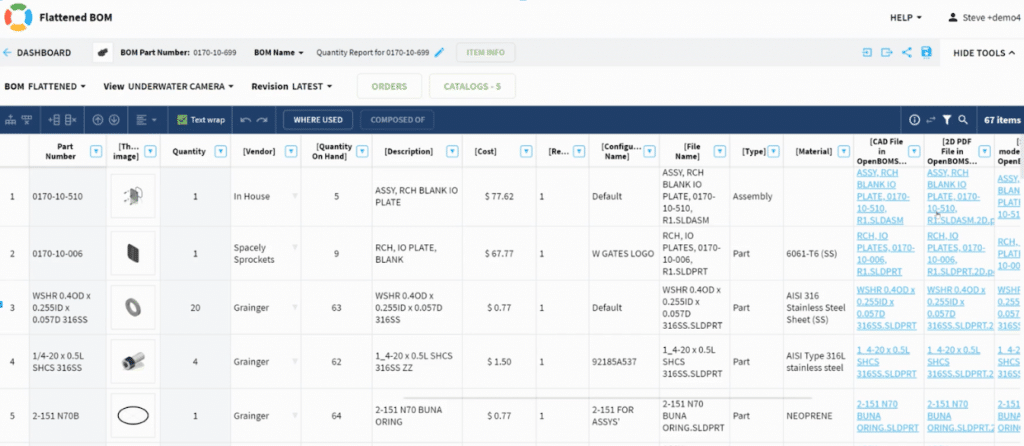
The Importance of the BOM
As stated earlier, the BOM holds the manufacturing knowledge of the product. The most successful companies today are those that understand the importance of collaboration. Bringing everyone together using the same data eliminates those mistakes that are present using different data silos.
Today, manufacturing companies use the BOM to connect everything. Let’s look at CAD files.
Why do you need a separate folder for CAD files when you can link derivative files to the BOM?
Meaning the STEP, STL & PDF files of a CAD file are embedded in the BOM. When there is a change to the CAD file then the file on the BOM is automatically updated as well. Share the BOM then everyone has access to the CAD files.
This is not just the case for CAD files but all other spec sheets, your SOPs, quality requirements, and more.
Lastly, different contractors, team members, and suppliers need different data. Maybe you don’t want your supplier to see certain data. And that’s fine, you can limit access rights. So, the supplier can only see what you want them to see.
What can you do today?
If you are looking to gain a competitive advantage and navigate through difficult economic times then digital transformation is for you. The digital transformation will keep all of your product data together and manage your revisions and create an ECR/ECO process. Your solution is a centralized platform that connects your team, contractors, and suppliers.
OpenBOM is a cloud-based PDM & PLM platform to manage your engineering and manufacturing data. Companies from startups to Fortune 500’s use OpenBOM to create a centralized database to bring in, store and manage their manufacturing data. With this infrastructure, users also use OpenBOM to streamline both their change management and PO processes.
If you need to improve the way you manage your data and processes, share data instantly, or collaborate with contractors and suppliers, contact us today for a free consultation.
Regards,
Jared Haw
Join our newsletter to receive a weekly portion of news, articles, and tips about OpenBOM and our community.