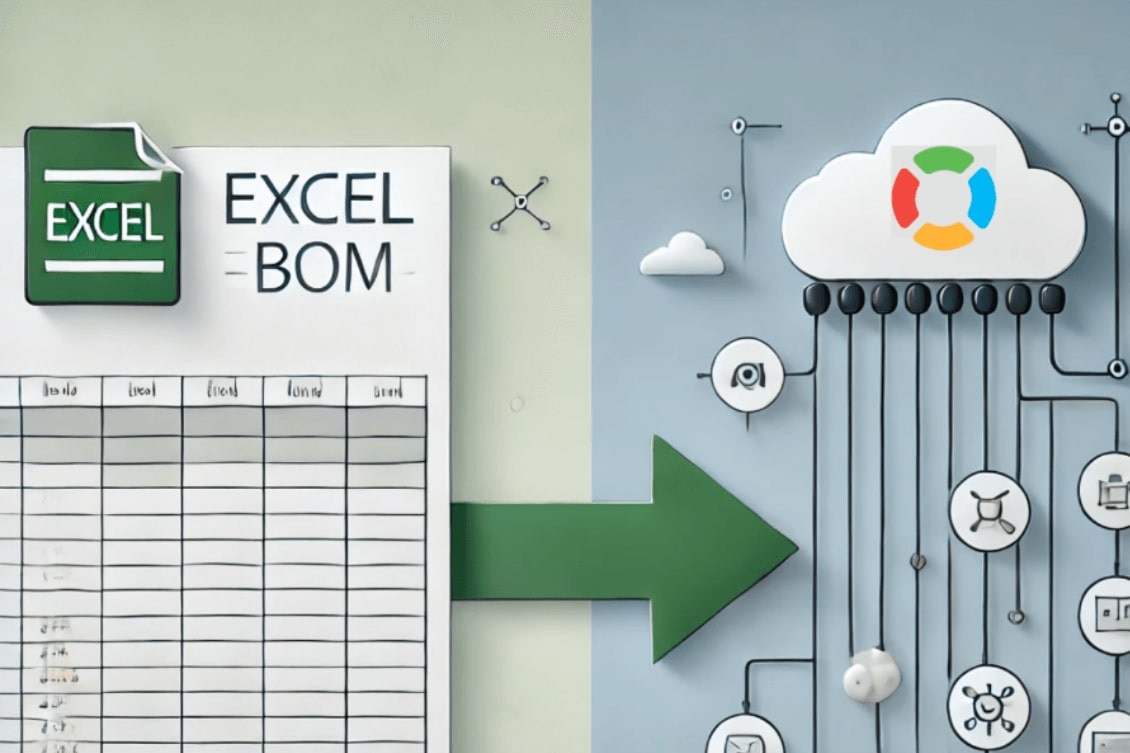
Manufacturers usually start to manage their Bill of Materials (BOM) in Excel, but as businesses grow and the complexity of products increases, so do the limitations with Excel. Excel-based BOMs are prone to errors, suffer from version control issues, and can be cumbersome when it comes to collaborating across teams or suppliers. These inefficiencies can slow down production, cause costly mistakes, and lead to missed opportunities for improvement.
Transitioning to a digital BOM system offers a smarter, more efficient way to manage product data. With a digital BOM, manufacturers can automate data entry, ensure real-time collaboration, and gain greater control over their product lifecycle. But how do you make the switch from Excel to a digital solution?
In this blog, we’ll walk you through three essential steps to successfully transition from an Excel-based BOM to a digital BOM system, helping you unlock better accuracy, speed, and collaboration across your manufacturing processes. Let’s get started!
Step 1: Evaluate Your Current BOM Management Process
Before making the leap to a digital BOM system, it’s essential to first assess your current BOM management process. This evaluation will help you understand the limitations of your existing system and pinpoint areas where a digital solution can bring the most value. Here’s how you can get started:
Using Excel for BOM management may seem like a straightforward solution, but it can lead to significant challenges as your product and production complexity grows. Common pain points include:
- Manual Errors: Data entry in Excel is often done manually, leading to human errors such as incorrect part numbers, quantities, or materials.
- Version Control Issues: Multiple versions of the same BOM can exist in different locations or among different teams, leading to confusion and miscommunication.
- Lack of Collaboration: Excel files can be difficult to share and update in real-time, making collaboration between engineering, procurement, and production teams inefficient.
- Time-Consuming Processes: Managing large BOMs in Excel is slow and cumbersome, especially when changes need to be tracked or updated across multiple documents.
By evaluating these limitations, you’ll better understand why a switch to a digital BOM system is crucial for streamlining operations and reducing risks.
Identify Key Areas for Improvement
Next, look for specific areas where a digital BOM can offer immediate improvements:
- Data Accuracy: With a digital BOM, you can automate data entry and validation, significantly reducing human error.
- Collaboration: Digital BOM systems allow for real-time updates, making it easier for multiple teams to access the most current information.
- Integration with Other Systems: Unlike Excel, digital BOMs can integrate with your ERP, CAD, or other business tools, ensuring that data flows seamlessly between platforms.
- Version Control: A digital BOM provides a single source of truth, eliminating the confusion caused by multiple, outdated versions of your BOM.
Understanding these areas of improvement will help you focus on the specific benefits you want to achieve, such as faster time-to-market, fewer errors, or better supplier collaboration.
Set Goals for the Transition
Once you’ve assessed the current state of your BOM management process, it’s time to set clear goals for the transition:
- Efficiency Gains: How much time do you want to save by automating your BOM processes? Setting a measurable goal here can help you track success.
- Reduction in Errors: Aim to significantly reduce the number of errors and discrepancies that typically arise with Excel-based BOMs.
- Improved Collaboration: Consider how you can enhance collaboration between teams, especially when it comes to tracking changes, managing approvals, or sharing BOMs with suppliers.
By defining your goals upfront, you’ll be able to evaluate the success of the transition and ensure the new system meets your needs.
Step 2: Choose the Right Digital BOM Solution
Once you’ve evaluated your current BOM management process and identified areas for improvement, the next step is selecting the digital BOM solution that best fits your needs. With so many options available, it’s crucial to focus on the features and capabilities that will have the biggest impact on your operations. Here’s how to approach this critical step:
Research Digital BOM Solutions
Begin by exploring the various digital BOM platforms on the market. These can range from standalone BOM management tools to solutions integrated with broader ERP or CAD tools. Consider the type of system that aligns best with your existing processes and long-term business goals.
Popular options include cloud-based platforms like OpenBOM, which allow for seamless collaboration and real-time updates, which also integrates directly with your CAD system.
When evaluating solutions, prioritize the features that address the limitations of your current system and meet your future requirements:
- Ease of Use: A user-friendly interface ensures your team can adopt the system quickly and effectively without steep learning curves.
- Collaboration Tools: Look for platforms that allow multiple users to access and edit the BOM simultaneously while tracking changes in real-time.
- Integration Capabilities: Ensure the solution can integrate with the tools you already use.
- Automation and Accuracy: Automation features, like BOM generation directly from CAD, reduce manual work and eliminate errors.
- Scalability: Choose a system that can grow with your business, accommodating more complex products and larger teams as your needs evolve.
Most modern companies offer free trials or demos, allowing you to test the platform before committing. Use this opportunity to simulate how you can be using the system. Also, focus on the return on investment (ROI) the solution will provide. A good digital BOM platform can save you money by reducing errors, improving efficiency, and streamlining collaboration, making it a worthwhile investment in the long run.
Step 3: Plan and Implement the Transition
After evaluating your needs and choosing the right digital BOM solution, the final step is to plan and implement the transition effectively. At OpenBOM, we offer onboarding which is a structured approach to help you build a process around OpenBOM that you can deploy company wide.
Your plan should include these 3 phases
- Phase 1 – Prepare: An assessment of your company’s specific needs, preparation and organization of your data, and setup
- Phase 2 – Build: A live end-to-end process walkthrough, personalized instruction, and E-learning materials and help guides
- Phase 3 – Handoff: A live hands-on practice session, review that your company’s needs were met, and final solutions to any other issues
Train Your Team
Introducing a new tool means your team will need time to learn and adapt to the digital BOM system. Effective training is key to ensuring they can take full advantage of the platform’s features.
Here are two things you can do to help implement your digital BOM with your team:
- Conduct Hands-On Training: Schedule sessions where team members can practice tasks such as creating, updating, and sharing BOMs within the new system.
- Assign a Champion: Designate a team member to become a system expert who can help train others and answer questions as they arise.
Proper training helps reduce resistance to change and ensures your team is confident in using the new tool. Reinforce how the digital BOM system supports larger business goals, such as faster production timelines or improved collaboration with suppliers. When the entire organization understands the value of the new system, they’ll be more engaged in adopting it.
Conclusion
Switching from an Excel BOM to a digital BOM is more than just a change in tools, it’s a transformation in how you manage and collaborate on product data. By evaluating your current processes, choosing the right digital BOM solution, and planning a thoughtful implementation, you can unlock significant benefits for your business.
A digital BOM not only reduces errors and streamlines workflows but also empowers teams to collaborate more effectively, respond faster to changes, and scale with confidence as your business grows. While the transition may require some effort upfront, the long-term advantages far outweigh the challenges.
The future of manufacturing is digital, and adopting a digital BOM is a key step in staying competitive in today’s fast-paced industry. Do you want to see how OpenBOM’s digital BOM works? Reach out. We are happy to talk.
By: Jared Haw
Join our newsletter to receive a weekly portion of news, articles, and tips about OpenBOM and our community.