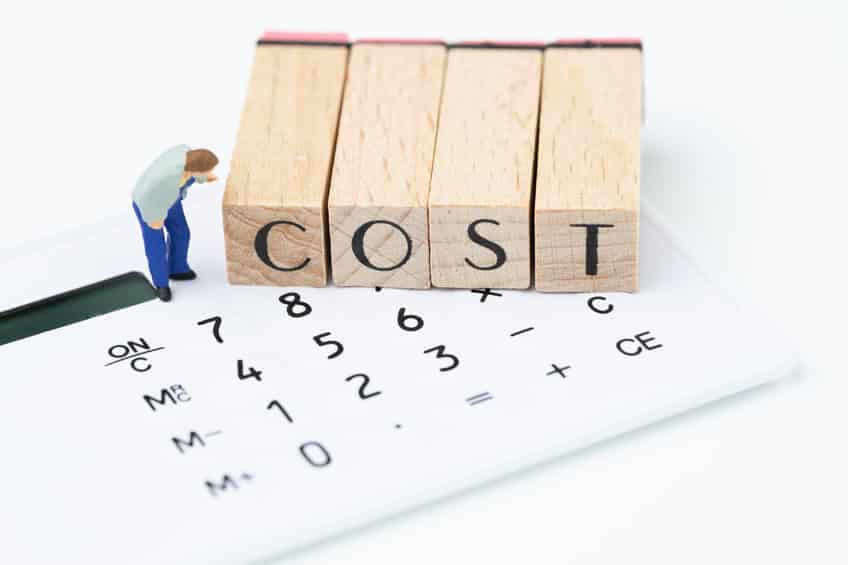
Cost is always on the top of the minds of every manufacturing company. Try to find someone in a manufacturing business that’ll tell you that cost is not important and you’ll end up with an empty list. However, cost management is a complex problem and it requires a collaborative effort to manage. Cost is a result of many functions – design decisions, component cost, labor, and many others. To manage them all together is hard. Especially when the work is done by many people and organizations at the same time.
In this blog post, we will discuss how OpenBOM can be used to help simplify and improve your manufacturing workflow. We will also provide examples of customers that are using OpenBOM and can give you an idea of how to get the most out of OpenBOM for your business.
The complexity of Product Cost Management
Traditional ways of cost management are static and can only be applied once the product design is basically done and the product is moving to manufacture. It happens not because companies have bad intentions to ignore the cost, but because managing cost when the data about the product is still fluid is really hard and it requires an extremely efficient collaboration. You have essentially 3 factors that you need to bring together:
- A unified bill of materials representing an entire product, including all disciplines and sometimes also sales and marketing, for example, to manage packaging and other disciplines such as transportation and many others
- A single source of truth about all components with cost information and sometimes some other pieces of data such as packaging, transportation, alternative suppliers, and many other pieces of data.
- An easy way to perform the cost calculation based on the information about components, production scale, and specific set of suppliers
Rollups and Product “Cost on Steriods”
OpenBOM provides you with a unique way to define formulas to calculate the cost and perform rollups. While it might sound like a simple function, it is not. OpenBOM is capable of collecting the data from multiple items (with Part Numbers), choosing a preferred supplier (vendor/manufacturer), and calculating the cost based on the product structure (BOM) including some special conditions such as, for example, purchased assemblies. The last thing is extremely important because it allows keeping an entire BOM while skipping parts and components from assemblies that were purchased for a specific price. You can read more about it in OpenBOM documentation – Formula and calculations.
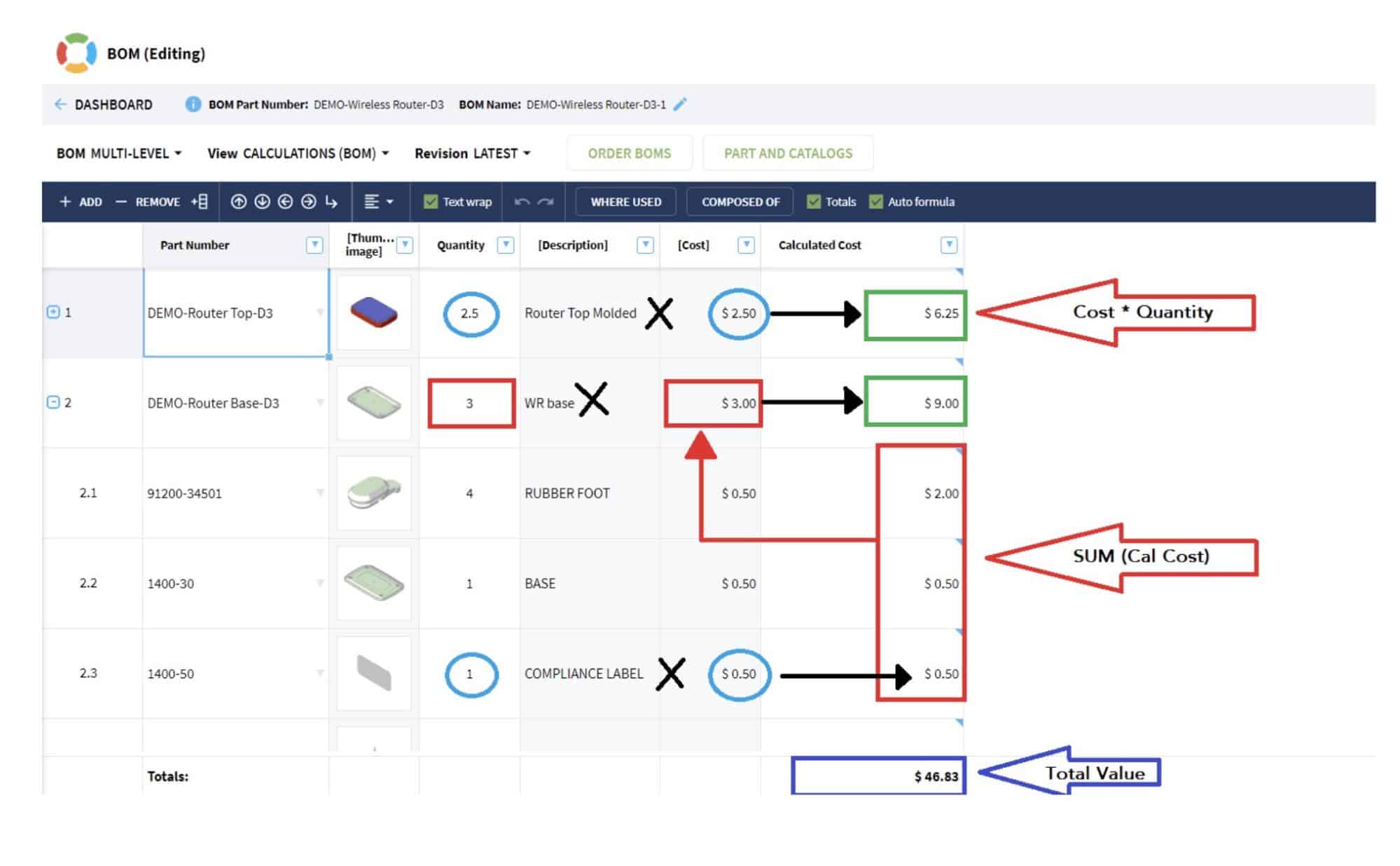
The picture above can give you an idea of how flexible rollup calculations can be using OpenBOM.
Customer Examples – Electronics, Consumer Goods, and Chocolate
What is common between manufacturers of electronic devices, consumer goods, and chocolate? Product cost! All these companies are extremely concerned about how to stay in control of the product cost and how to predict and manage it in the modern competitive manufacturing environment.
Fascia’s Chocolate – we understand the unit economics of our chocolates!
Let me start from the story of Connecticut-based Fascia’s Chocolates which manages ingredients and product recipe process using OpenBOM.
OpenBOM is so much simpler than Excel. As material costs have been changing so much lately, it’s comforting to know that when I change an ingredient cost in one place, it updates in all of our product recipes. We love how OpenBOM rolls up the cost of all the ingredients to the top-level finished product. And it’s more than just cost that Fascia’s is keeping track of in OpenBOM. As our business has expanded to much more online orders, we use OpenBOM to not only keep track of costs but for weight! The BOM is our recipe. We add labor, timing, overhead, shipping, everything that goes into the delivery of our products to our customers.
Kuva Systems – Cost and Inventory Forecast
Kuva System relies on OpenBOM to forecast component demand and costs and manage inventory.
“OpenBOM quickly produced an accurate and complete Bill of Materials from our CAD models”, says Ethan S, “something we had been struggling with our non-integrated Google sheets based process.” Kuva strives to deliver the best value in the continuous methane detection space and has recently increased demands on both internal and external planning and manufacturing. As we moved into manufacturing, we just didn’t have an accurate BOM with reliable pricing, vendors, and lead times,” says Ethan, “we didn’t know how much our product cost. We started with a complete BOM in OpenBOM, then looked towards costing, forecasting, and manufacturing planning.
Learn more about the Kuva experience here.
Bird Guard – Flexible Data and Cost Calculate
Bird control company, Bird Gard, purchased OpenBOM to answer the most important question any manufacturing company can have, how much does their product cost to build? While their existing Microsoft Dynamics ERP had many features, it could not answer that question.
Bird Gard buyer, Heather Heath, explains, “Given the challenges and shortages in the component pipeline, we are buying far into 2022 and our Microsoft Dynamics Great Planes system just doesn’t offer the flexibility around cost management and forecast modeling that we need.”
Early on, Heather discovered OpenBOM’s flexible modern data model.
OpenBOM is amazingly effective and technologically advanced utilizing a multi-discipline bill of materials, managed entirely in OpenBOM. As the prices of components are forever changing, we need to know how much it costs today AND what it will cost in the future. I love how I can easily add a property, as many properties as I need, to manage costs and other information about Bird Gard items, our existing system just could not do that.
Learn more about the Bird Guard experience here.
Conclusion
OpenBOM data modeling flexibility combined with formula and calculation support is at the core of OpenBOM uniqueness when it comes to cost management. Most systems are just too rigid to manage different attributes, combine them in formulas and apply hierarchical costing rollup. OpenBOM does it easily and once you update a central catalog with item data, everything is recalculated at your fingertips.
Want to check how OpenBOM can help? REGISTER FOR FREE, start a 14-day trial instantly to explore all features.
Best, Oleg
Join our newsletter to receive a weekly portion of news, articles, and tips about OpenBOM and our community.