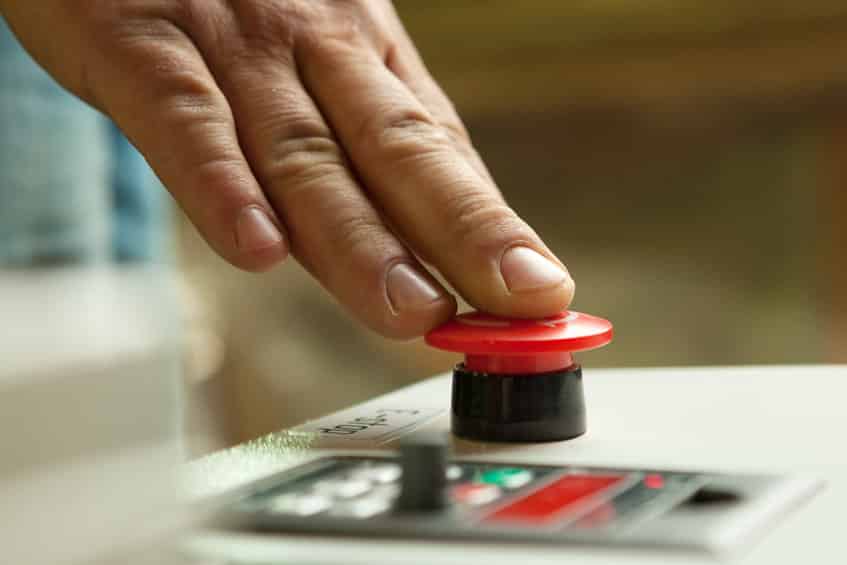
During the manufacturing process, your contract manufacturer (CM) or supplier will often refer to your bill of materials (BOM). This is because the BOM holds the knowledge of the product you are manufacturing. Therefore, the end product and all of the parts fabricated or procured are made as a result of the data provided in the BOM. So, the data provided in the BOM is important.
However, for some reason, especially for SMBs, the BOM is usually overlooked If it is not updated, not detailed enough, and not shared with the appropriate people.
Here are the main issues that will happen if you do not provide your CM with a proper BOM.
Incorrect Quote
The BOM will be shared with the supplier during the request for quotation (RFQ) process. Based on the drawings, BOM, and other requirements, your CM will provide you with a quote. If the items on the BOM are called out incorrectly, you will receive a quote that does not properly reflect the part you need.
If you do not have materials and other items called out, your CM might assume and make incorrect assumptions which lead to the quote being wrong as well.
Purchase Incorrect Parts
For each line item, your BOM will have the quantity, supplier, manufacturing part number (if relevant), and other info to purchase or fabricate the part. If these are not up-to-date then you will procure the wrong quantities or purchase the wrong parts.
Data Inconsistencies
The BOM also calls out the finish and color of each item. If the BOM does not have the most updated finishes or colors then the end product will not look like it should
Another common example is the inconsistencies between the product data on 2D drawings vs the BOM. For example, if your 2D drawings call out for aluminum 6061 but the BOM has aluminum 5052 then which one is correct? Confirming this takes time, especially if it’s done on multiple items.
Delays
Doing things right the second time always takes longer than doing it right the first time. The same is for the BOM. If certain items are incorrect then it takes time to correct them. Sometimes you don’t figure this out until the prototype step.
Making a prototype depends greatly on the industry and product you are making. You might be looking at a week to a month or two to make a prototype. If your BOM is not updated then you just threw all that time and money to create a prototype out the window. Unfortunately, this happens a lot.
For another example, delays can also come up if you opened tooling and called out a plastic resin that is no longer the correct resin. Or, if you opened your tool without specifying a need for a texture. Both these can result in tool modifications or new tools which end in increased costs and longer lead times.
If at the start of your RFQ process, you provide a BOM that is not correct, you have set yourself up for multiple problems. All of these issues will result in:
- Increased costs
- Excess or not enough inventory
- Long lead times
- Quality problems
What Can You Do Today?
During the life of a product, there will be multiple revisions and change requests that must be managed. It is easy to lose historical data or fail to share changes with the correct team members. A centralized platform that connects your team, contractors, and suppliers is your solution.
OpenBOM is a cloud-based platform to manage your engineering and manufacturing data. Companies from startups to Fortune 500’s use OpenBOM to create a centralized database to bring in, store and manage their manufacturing data. With this infrastructure, users also use OpenBOM to streamline both their change management and PO processes.
If you need to improve the way you manage your data and processes, contact us today for a free consultation.
Regards,
Jared Haw
Join our newsletter to receive a weekly portion of news, articles, and tips about OpenBOM and our community.