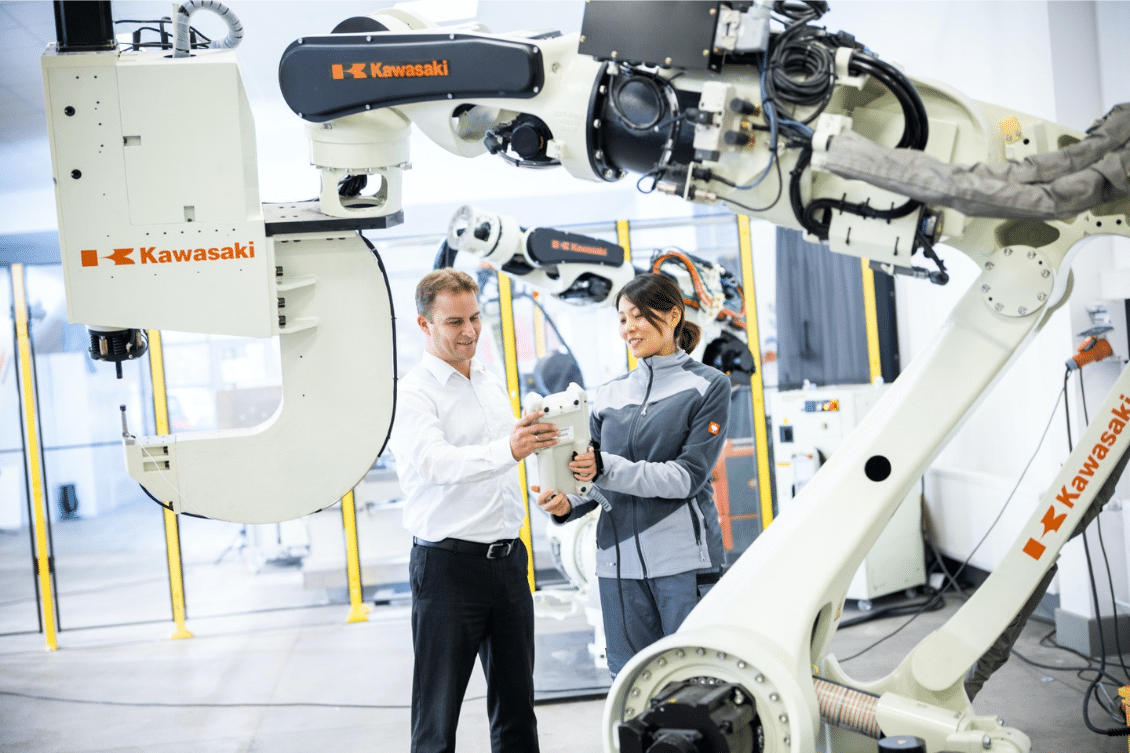
In today’s fast-paced manufacturing landscape, companies are continually striving to outpace their competitors and bring innovative products to market quicker than ever. The key to achieving this lies in establishing effective partnerships that can provide the necessary expertise and resources. One such partnership that holds immense potential is the collaboration between manufacturing companies and contract manufacturers (CMs).
By understanding the value of partnering with CMs, manufacturing companies can leverage their expertise, experience, and infrastructure to streamline their new product development (NPD) process and achieve accelerated product launches.
In this blog post, we will explore how CMs can support you during NPD to transition you from development to production as efficiently as possible. We will delve into the unique advantages that CMs bring to the table, their ability to bridge critical gaps in knowledge and resources, and the strategic benefits that arise from this symbiotic relationship.
In our previous blog, Agile New Product Development Using OpenBOM, we introduced to you how we see agile product development at OpenBOM.
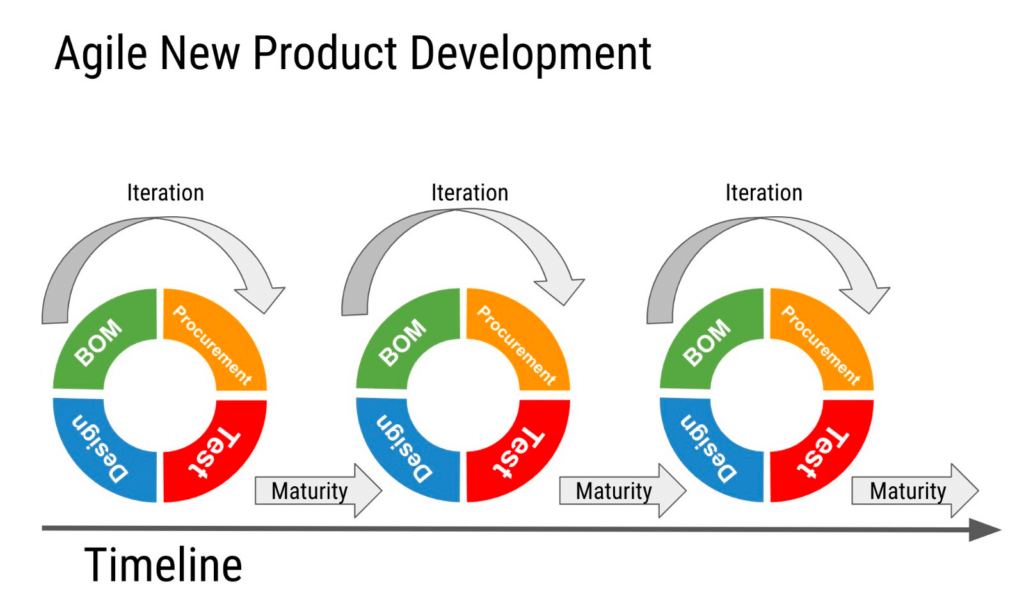
So in this picture, when does your CM get involved, and how can they add value? Let’s break each part down to see the value of the CM.
Design
During the early stages of design, a CM will not be heavily involved. A CM gets more involved after there is a known demand for the product the manufacturer is developing. With that being said, if a manufacturer is making a number of products with a CM, it is common for the CM to collaborate with the manufacturer early in the design stage because of their historical success with selling products in their market.
In most cases, a CM will get involved after the proof of concept and after there has been some initial demand created in the market. It’s only necessary for the CM to get involved once you know there will be sales.
The main focus of your CM collaborating with you during the design phase is to optimize parts for production and accelerate the speed from development to production.
BOM
The most important manufacturing document for your CM will be the bill of materials (BOM). Depending on how your supply chain is set up, your CM might take on responsibility for updating and managing the BOM. The main reason for this is that if you are using a CM then you are essentially giving them the keys to own your supply chain. Naturally, the CM can take responsibility for managing the BOM as a result.
But this is not necessarily a good thing nor is it recommended. You should take responsibility for your BOM.
During the development process, your CM will be responsible for making changes and updating the BOM. This makes it easy for your CM to make an unapproved change.
Since the BOM is looked at as one of the most important manufacturing documents then it’s advised that the company who owns the product also owns the BOM.
The CM will have a significant influence on the evolution of the BOM from design to production and through all the rolling changes. However, they should not be the party to make changes to the BOM. Therefore an approval workflow for the manufacturer to accept a change request from the CM is necessary.
Procurement
Your CM partner will most likely be the one who leads the majority of the steps related to procurement. If you are using multiple different suppliers and you are assembling the final product in-house then your team will have control over the procurement process.
However, if you outsource production to a CM then you are mainly responsible for placing a PO. Upon receipt of the PO, your CM will be responsible for purchasing parts, managing lead times, managing the quality, planning final assembly, and more.
If this is the initial pilot run then it will be more of a collaborative effort to make sure your initial units are being built.
Test
The CM will take responsibility for testing all products before they leave the production facility. However, who is responsible for creating the quality documents and standard inspection procedures (SIPs)?
The quality of the product is designed in the product. You can’t have a poorly designed product go through a number of crucial tests and expect it to pass. With that being said, the purposes of these quality tests are to ensure that a product was built according to the specifications provided. If you start to see recurring quality problems but the product meets all the specs then you’ll have two decisions. First, revise the quality requirements and secondly, propose a change to the design to eliminate the quality issue.
During the testing phase, the CM will lead the initial quality tests. However, if there is a quality problem then the CM will figure out the root cause and they can make some requests for changes. However, the manufacturer is responsible to accept all changes that eliminate the quality issue.
How Can Your CM Help With NPD?
Trying to successfully launch your product is no easy feat. Along the way, numerous roadblocks can hinder progress. Having a reliable CM by your side equipped with the expertise and capabilities to seamlessly transition your product from development to manufacturing becomes an invaluable asset.
While trying to transition your product from development to production, there are four roadblocks that can slow you down if you don’t have the right resources. These four roadblocks are:
- Prototype To Scale Up
- Increased Costs
- Quality Issues
- Managing Data
If you are working with a qualified CM then they will be able to navigate through these roadblocks. Here is how a CM can help you to navigate through each roadblock.
Prototype To Scale Up
Creating prototypes serves as a crucial milestone during the development process. These prototypes are not only instrumental in showcasing the concept to investors, executives, and key accounts but also play a vital role in establishing a compelling crowdfunding campaign and other marketing activities.
The tools, materials, and methods used to build these prototypes will differ substantially from those used in mass production. So, how can you bridge the gap between prototypes to production?
This is where your partnership with a CM will pay dividends. During a pivotal stage, known as design for manufacturing (DFM), your CM will guide you through the processes of optimizing all the parts and processes for production. Some of the key activities done during DFM are the following:
- Part Optimization for Mass Production
- Tool and Die Design
- Identify Parts with Potential Quality Problems
- Implement Cost Down Project
Increased Costs
In the majority of industries, especially manufacturing, manufacturers strive for exceptional quality but are hesitant to pay the costs associated with higher-quality materials and production methods. But in manufacturing, what is the relationship between a more expensive product and quality?
During the product development process, price is usually not on your mind. What is on your mind is getting the product to function properly at any cost. While not tracking your costs during development will lead to your production cost being quite high. This might come as a shock once you request quotes from CMs.
A capable CM will be able to view the BOM and other product data you have provided them during the request for quotation (RFQ) step and identify costs that are too high. The costs can be high for a number of reasons, such as:
- Over-engineered
- Using wrong materials
- Tolerances called out are unnecessarily tight
- Using incorrect processes
Quality Issues
Quality does not come out of nowhere. It is an inherent characteristic of a product long before it reaches mass production. To put it differently, if the design is flawed then you will have quality problems with the product.
It can be difficult for a manufacturer to design a product without knowing exactly what the manufacturing processes will be. A CM with expertise in the manufacturing methods, materials, processes, and more that go into making your product gives them the advantage to optimize your design for production.
To eliminate the risk of defects through the production process, your CM should provide you with DFM to optimize all parts before production.
Managing Data
In order to navigate through all of these roadblocks, you need one thing, and that is a way to enable collaboration. You might have a great product with great sales, but if you don’t communicate properly with your CM then you will not be able to navigate through any of the previous three roadblocks.
Throughout the stages of development, it is important to establish a way to effectively manage data related to your product. This is particularly important during the early stages of development to properly capture all changes and revisions made to your product. This can lead to purchasing incorrect parts during prototypes or not knowing what you built and scrapping through old emails to figure it out.
Unfortunately, this is far too common in manufacturing companies and the end result is always the same, a pushed-back launch date which does not really fit well with agile development.
The way you send data and communicate with your CM is important. If you are working with a CM in China then the normal way to share data are excels, emails, and WeChat.
Establishing a unified source of truth is pivotal as it enhances collaboration. This centralized platform ensures that all product, engineering, manufacturing, design, and CAD data are stored and managed together.
What Can you do Today?
Companies are looking at ways to implement agile development. This is great. However, the tools companies use need to also support agile development. You can’t continue to use Excel and expect to improve your speed from development to production.
Digital transformation will help you to transform your processes to keep all of your product data together. To have a centralized platform that connects your team with your contractors is extremely important to set up modern digital processes to save time and money.
OpenBOM is a cloud-based PDM & PLM platform to manage your engineering and manufacturing data. Companies from startups to Fortune 500s use OpenBOM to create a centralized database to bring in, store, and manage their manufacturing data. With this infrastructure, users also use OpenBOM to streamline both their change management and PO processes.
If you need to improve the way you manage your data and processes, share data instantly, or collaborate with contractors and suppliers. Contact us today for a free consultation.
Regards,
Jared Haw
Join our newsletter to receive a weekly portion of news, articles, and tips about OpenBOM and our community.