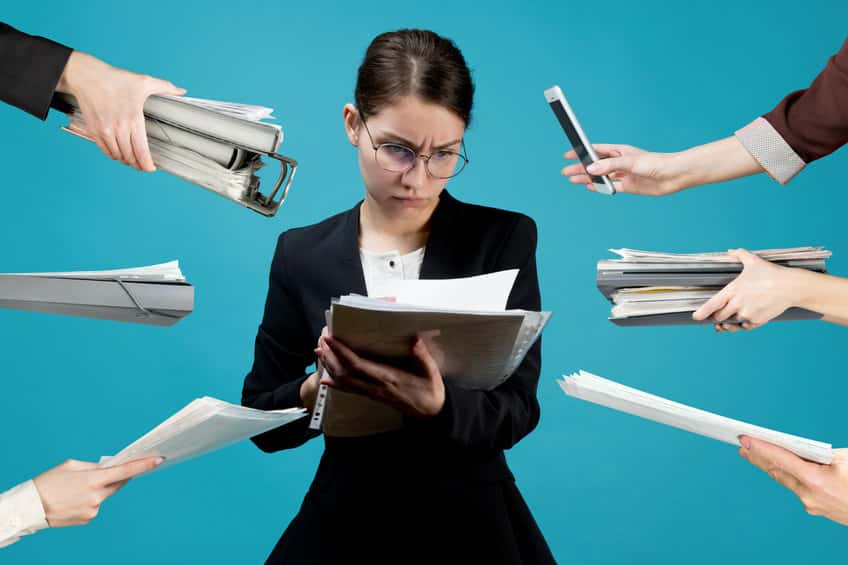
In the era of advanced manufacturing, collaborative engineering, Industry 4.0, and advanced business process management, is there still a need for a BOM clerk? This is an important question to consider as businesses move towards automation and streamlined workflows. We’ve been discussing BOM management with many prospects and customers and the question of BOM creation is one that always drives a lot of controversy and debates.
In this blog post, we’ll take a look at the process of BOM creation, the people that are involved in this process, and future trajectories of the manufacturing environment that can change the process and make it more collaborative and streamlined.
BOM Creation Process
Bill of Materials is the lifeblood of every engineering and manufacturing process in the company. Therefore, defining a Bill of Materials is one of the most important steps. While an organization has multiple silos of the information – design, production planning, and maintenance, the information in the BOM is connecting these silos.
An important step in organizing the information and product structure (BOM) management is to create and update bills of materials as your team is progressing with the design, engineering, prototyping, and procurement tasks. This process can be complex and involves activities from multiple people (engineers, planners, manufacturing engineers, and purchasing agents).
The main source of BOM is design information, which lays the foundation of BOM data entry. However, not everything is defined in the design. Therefore, once the design is completed, it only provides an initial set of data for a BOM. Additional information needs to be added by other people (eg. cost, vendor information, supplier part number, etc.) Once a BOM is completed it must be approved and used for product and procurement purposes.
Who creates a BOM?
The question of who creates a BOM is one of the hardest to ask. Different people are ‘touching’ BOM, but there is no single person who does all data entries. In the old school manufacturing companies, the role of BOM clerk was designated to a person who was responsible to pull data from multiple reports and create a bill of materials. It was (still is) the work that requires a lot of manual “copy-paste” from multiple places – CAD reports, Inventory reports, catalogs from distributors, and many others.
The main challenge of the process is manual updates. Each time someone touches the BOM and updates the information, it potentially introduces a problem or just a typo (mistake). Multiple mistakes are accumulating and in the end, it slows down the process or leads to mistakenly ordered parts, components, and jobs.
Introducing BOM management software can solve the problem of BOM creation. First, OpenBOM provides a robust and seamless integration with design (CAD) tools allowing you to pull the data and seamlessly create a BOM (the updates are fully integrated). Other pieces of information can be defined as well and centralized in the item record, which defines a single source of truth for an item.
Does BOM creation need teamwork?
An important element of the BOM creation process is collaboration. This is where teamwork is really the key to making the work efficient and on time. In the manual work organization, each step in the BOM creation process requires manual interaction, sending Excels and later synchronizing them together.
OpenBOM real-time collaboration and simultaneous editing allow you to create a BOM within minutes from the CAD system, share it with all team members and accomplish the task without pulling multiple Excel files and sending them by email.
Conclusion
Old habits die hard. With the lack of good BOM management tools and collaboration methods, companies need to hire special people to perform the routine work of BOM creation, modification, and validation. Mistakes in the Bill of Materials are costly and when found later in the production and manufacturing process will cause delays, increased cost, regulatory and compliance risks, and many other problems.
OpenBOM is a modern collaborative SaaS BOM management, which is available on-demand and can be accessed by multiple people – team members, engineers, production planners, procurement agents, contractors, and suppliers.
OpenBOM will help you to ensure that the data you have in the BOM is up to date (thanks to all CAD integrations) and validated and approved by everyone who needs to see it.
So, ultimately, OpenBOM will put your old “BOM clerk” out of the job and will streamline the information flow inside of the company and across the value chain.
REGISTER FOR FREE and start a free 14-day trial to check how OpenBOM can help you today.
Best, Oleg
Join our newsletter to receive a weekly portion of news, articles, and tips about OpenBOM and our community.