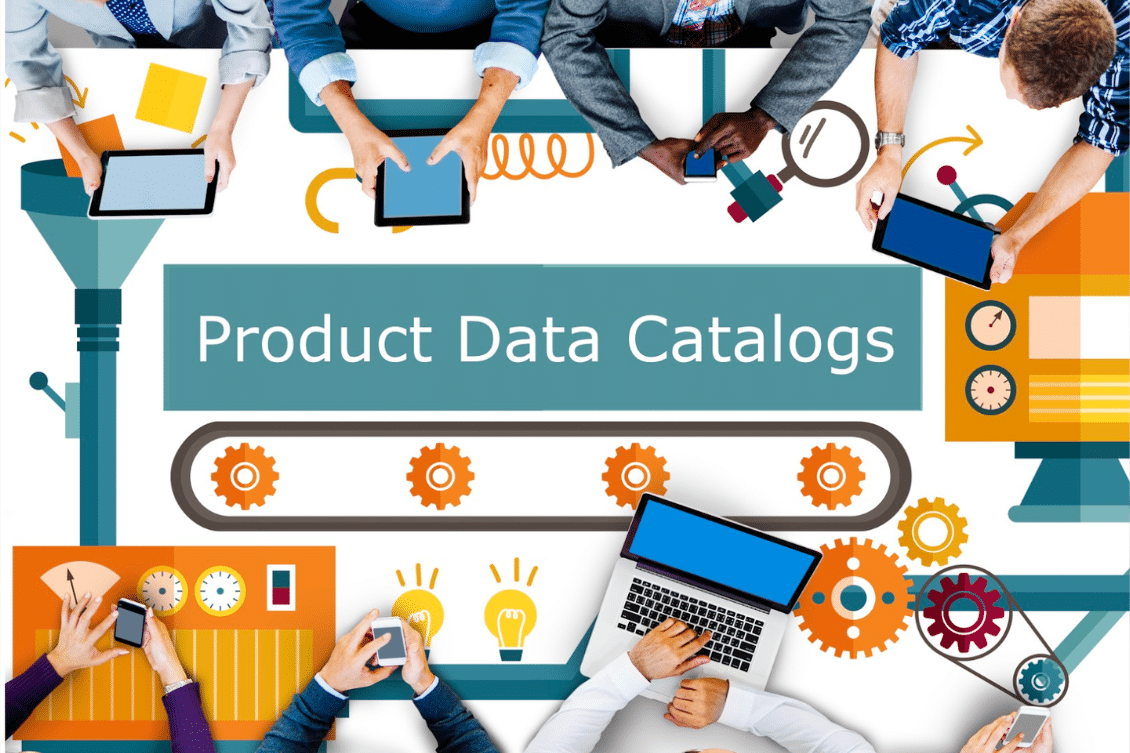
In the age of digital transformation, data is at the heart of every business. It’s the fuel that powers everything from design and engineering to production, manufacturing, and supply chain. Unfortunately, industrial companies are not good at data organization. It is siloed in Excel, old documents, and different proprietary data management solutions. That’s where digital data organization comes in. In this blog post, we’ll explore why thinking about how to organize company data is the first step in digital transformation and why it is critical for making it successful. Let’s discuss how to create a well-organized data structure, improve data quality, and, as a result, support a better decision-making process.
Digital Transformation and Digital Processes
Manufacturing organizations are looking at how to digitally transform their operations. For many companies, it means changing the way they think about their data assets. You can ask yourself, what is the big deal about digital transformation? No one is using drawing boards these days and all information is already digital in documents that can be stored in a digital format in any place we want. Would it be a proper way to think about digital transformation? What if I dump my documents in one of the public cloud file storages or, alternatively (if I’m concerned about the security) in one of a company SharePoint sites?
Digital Documents, But Not Digitally Managed Processes
You can store information in digital documents, but unfortunately, that will not give you the much-desired benefits. The main reason for that is simple. Such information will live in their “analog envelopes” such as documents. The only way to deal with documents is to distribute or see them online (or offline). The problem is that these documents don’t represent a ‘digital value’ and cannot be used to build digital processes. You can use them to build document processes, but that would not be the same. The same can be said about multiple databases that exist in your organization. All your MS Access databases, Lotus Notes, and legacy solutions store data in proprietary data formats – all these systems manage data, but not allowing you to focus on the core elements of digital transformation – information flow and digitally managed processes.
Digital transformation starts with a few fundamental steps that will allow you to re-think the way you manage data. There are three things that represent a foundation of the digital transformation process: (1) a single source of truth; (2) a system of data catalogs; (3) data integration.
The first one allows you to ensure that every piece of the information managed by your company always has a master record. For example, if you have an item with a specific Part Number, you want all other properties of this item to be managed in the way so you will always know what correct description, suppliers, prices, history of revisions, etc. That will allow us to refer to this information in all other places.
Data integration is a set of processes that allows you to connect pieces of information together, to ensure data is flowing between people and systems, and eliminate all manual processes that require data to be re-entered, re-typed, or manually transformed. All these processes lead to mistakes and cost a lot to your company in the future.
A system of data catalogs is a fundamental element of digital transformation architecture that allows you to organize all information, and make it searchable and available to everyone. In this article, I will speak about the importance of data catalog organization as a first step in your digital transformation process.
Data Catalog – A Foundation of Digital Transformation
Building and maintaining a well-organized data catalog is critical for companies looking to optimize their operations and streamline their decision-making processes. The key element of OpenBOM data management is a connected set of data catalogs. Here are the main elements of how the digital catalog organized by OpenBOM can help:
- Data catalogs enable a manufacturing company to manage its data assets efficiently, providing a centralized location for storing and accessing information.
- Connected data catalogs link various data sources, making it easier to search and discover relevant data, which fosters collaboration and knowledge sharing.
- Data catalog can be customized in real-time to meet the unique needs of a company, regardless of what data they manage and where this data is coming from.
This is how OpenBOM Catalogs can help you to organize product-related information:
- Centralized Repository for product data assets: OpenBOM Catalogs act as a centralized hub for managing all your company’s product data assets, ensuring that all stakeholders have access to the information they need when they need it. This not only simplifies data management but also promotes collaboration and coordination among team members. The foundation of this repository is a set of catalogs with the classification of items and all item attributes.
- Easy Integration with Existing Systems: OpenBOM Catalogs can be easily integrated with your existing data management systems, allowing you to leverage the power of a connected data catalog without the need for a complete overhaul of your current infrastructure. OpenBOM integrates with engineering systems (MCAD, ECAD, etc.) as well as many other solutions including building RESTful data connections.
- Customizable Structure: With OpenBOM, you can customize your data catalog to suit the specific needs of your organization. It includes setting up properties and links enabling you to build a customer-specific data organization. This flexibility allows you to create a data management solution that is tailored to the unique requirements of your manufacturing business and connects teams, contractors, and suppliers together.
- Improved Data Discovery: OpenBOM Catalogs make it easy to search and discover relevant data across your organization. By connecting various data sources and streamlining the search process, team members can quickly access the information they need, which leads to better decision-making and increased productivity.
- Enhanced Collaboration: By providing a connected data catalog that is accessible to all team members, OpenBOM fosters collaboration and knowledge sharing. With easier access to relevant data, employees can work together more effectively, leading to better outcomes for your organization.
Conclusion:
Digital transformation in every manufacturing company starts from the proper granular organization of product data, connecting all pieces of data together, integrating it with legacy and other data sources using integration, and making it widely available to everyone. OpenBOM Catalogs offer a powerful solution for managing and organizing your company’s product data. By providing a centralized repository for data, seamless integration with existing systems, customizable structure, improved data discovery, and enhanced collaboration, OpenBOM can help you streamline your data management processes and optimize your organization’s decision-making capabilities.
REGISTER FOR FREE and check how OpenBOM can help.
Best, Oleg
Join our newsletter to receive a weekly portion of news, articles, and tips about OpenBOM and our community.