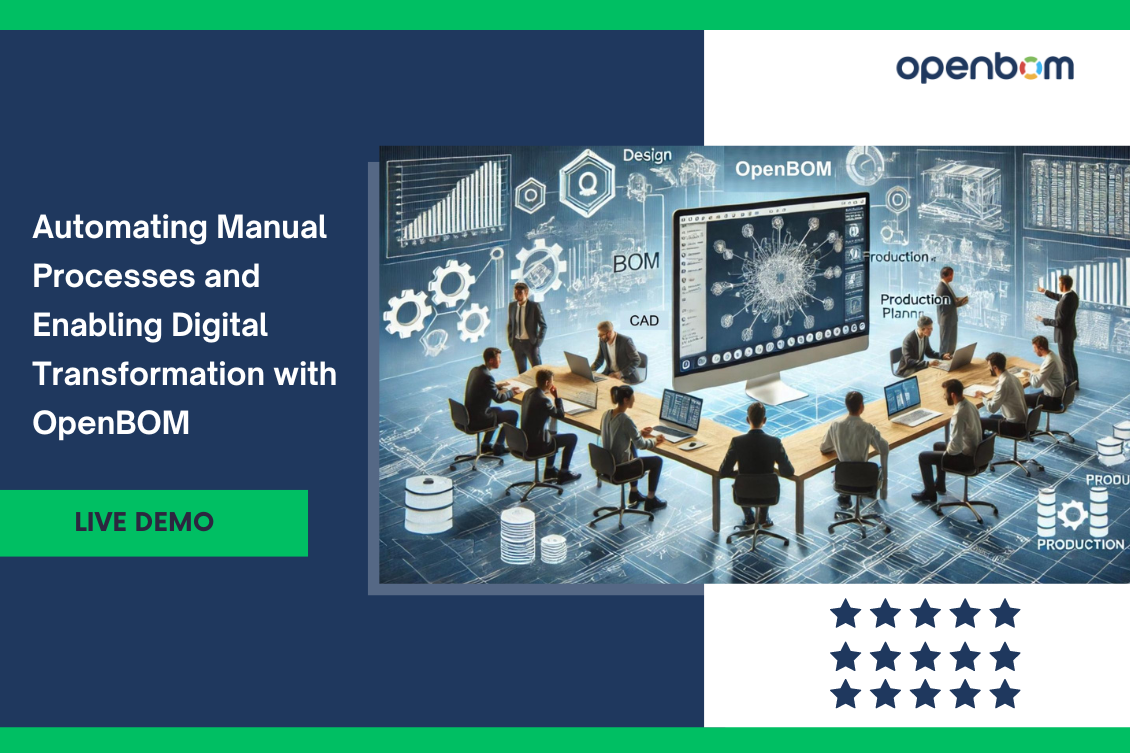
Modern manufacturing is about speed and agility. The key to success lies in automating manual processes and fostering collaboration between teams, contractors, and suppliers. OpenBOM online platform offers you the best tool for distributed teams to work together. But you should not take it for granted.
In this blog, we will walk through a live demo showcasing how OpenBOM not only automates these critical tasks but also plays a pivotal role in the digital transformation of companies—ensuring that all stakeholders are seamlessly connected throughout the product life cycle.
Introduction: Developing a Product from Scratch
Imagine you are working on a new product, and you’re starting from ground zero. The journey typically involves multiple tools, several teams, a lot of data exchange, and a hefty amount of manual effort. But what if you could automate many of these processes from the beginning, so your team can focus on what really matters—creating the product?
This demo will show how OpenBOM allows you to efficiently develop a product from scratch by connecting all necessary data, automating manual tasks, and ensuring everyone—inside and outside your company—is on the same page, every step of the way.
Getting Started with CAD: Seamless Integration and Data Management
The process kicks off with using your preferred CAD system to design the product. OpenBOM’s seamless integration with leading CAD tools ensures that as you create your design, all relevant data is automatically saved and synced in real-time.
Whether it’s design iterations, metadata, or specific part details, everything is captured without any extra manual data entry.
Managing versions and revisions is another critical aspect. OpenBOM’s version control allows you to go back in time to any previous design, compare changes, and revert if needed. This eliminates the chaos of managing file versions manually and reduces the risk of errors, allowing your team to remain agile while maintaining full control of the design lifecycle.
Automating the Release Process: From BOM to One-Click BOM
Once the design is in place, it’s time to move on to the release phase. Traditionally, generating a Bill of Materials (BOM) could be a time-consuming task prone to human error, especially if done manually. With OpenBOM, creating and managing BOMs is simplified to a one-click process. This automation reduces the time spent on administrative work and minimizes the risk of mistakes—allowing you to focus on delivering quality products faster.
By automating the release process, you can ensure that your BOM is accurate, up-to-date, and ready for the next stages of production and planning. The BOM becomes a central, digital asset that can be shared and used across various teams without any discrepancies.
Cross-Domain Integration: Connecting Engineering to Production
As product development progresses, it’s essential to ensure that the engineering designs flow smoothly into other domains such as ECAD and production planning. OpenBOM makes cross-domain integration seamless, ensuring that all teams—whether they’re working on mechanical designs, PCB layouts, or production planning—are working from the same set of accurate, up-to-date data.
One of the highlights of this demo will be how OpenBOM enables multi-disciplinary collaboration. You can create a multi-disciplinary BOM that includes both mechanical and electronic components, packaging, and more—all in one place. It allows multiple people (designers, engineers, production planners) to work together without the hassle of switching between systems or duplicating data.
This is crucial for maintaining consistency, especially when multiple teams are contributing to the same product. It also speeds up the development process by reducing communication bottlenecks and ensuring that no critical data is lost between domains.
Digital BOM: A Single Source of Truth
At the heart of this process is the concept of a Digital BOM. Think of it as a living, breathing document that brings together all aspects of your product’s development—whether it’s design data, part information, or procurement details. With OpenBOM, the Digital BOM ensures that every team member has access to the most accurate and up-to-date information in real-time.
This level of connectivity is crucial in today’s distributed and often remote-working environments. As multiple people collaborate on the same project, the Digital BOM becomes the single source of truth, preventing errors, miscommunication, or data loss. Everyone, from engineers to suppliers, is connected and working in sync, reducing time-to-market and ensuring a smooth product development process.
The Release Process: First Release “A”
When the design and planning are ready, it’s time for the first official release—Release A. In this demo, we’ll show how to create a change request, approve it, and generate a revision within OpenBOM. Once the release is approved, all data—including the BOM, CAD files, and derivative materials—are frozen in time. This guarantees that there is a historical record of this release, which is crucial for future revisions and audits.
OpenBOM’s release process ensures traceability and accountability at every stage, reducing the risk of errors during handoffs between teams and ensuring that everyone is working from the same, consistent version of the product data.
Build and Production Planning: Inventory Management and Procurement Gaps
Now that the product is ready for production, we move on to the next critical phase: production planning and inventory management. OpenBOM provides powerful tools to build and manage your planning BOM, identify gaps in procurement, and ensure that all necessary materials are available before production begins.
In this demo, we’ll demonstrate how OpenBOM can use order data to plan procurement and identify potential gaps in your inventory. By flagging missing or low-quantity parts early in the process, OpenBOM helps you avoid costly delays and ensures that production runs smoothly.
Automating RFQ/PO Creation and Integration with Suppliers
Procurement is another area where manual processes can slow down the entire production cycle. With OpenBOM, generating RFQs and Purchase Orders (POs) for all vendors is automated. You can export these orders to your accounting software, such as QuickBooks, or send them directly via email. By automating these tasks, OpenBOM ensures that the correct quantities flow digitally, reducing the risk of errors and speeding up the procurement process.
This level of automation ensures that your supply chain is always connected, with accurate data flowing from your product design teams all the way to your suppliers. The result? Faster turnaround times, fewer mistakes, and a more efficient supply chain overall.
Handling Design Changes: Real-Time Updates and Notifications
One of the important aspects of every product development is change. Design updates happen all the time, and without the right tools, managing these changes can be a nightmare. In this demo, we’ll show how OpenBOM helps you handle design changes—whether it’s adding more bolts or tweaking a component—and how these changes can be pushed to the release, approved, and reflected in your production planning and procurement processes.
All stakeholders are notified in real-time about these updates, ensuring that nothing slips through the cracks and that all teams are working with the latest information.
Video Demo
Check the following video for a comprehensive video demonstration.
Conclusion: Connecting Engineering, Production, and Supply Chain in One Platform
As demonstrated, OpenBOM provides comprehensive coverage of the entire product development lifecycle—from the earliest stages of design and data capture to release management, production planning, and procurement. By automating these processes, OpenBOM helps reduce errors, save time, and streamline collaboration between teams, contractors, and suppliers.
The digital transformation that OpenBOM enables is critical to modern manufacturing. It breaks down silos, connects every stakeholder in the product development process, and creates an environment where data flows seamlessly from engineering to production and beyond. In this demo, three key elements stand out:
- Digital BOM – A single source of truth for all product data.
- Seamless Design Integration – Ensures that data flows smoothly between design and production teams.
- Connected RFQ and Supply Chain – Automates procurement and connects suppliers directly to your product data.
Want to see OpenBOM in action? Register for free and start your journey towards automating product development and transforming your company’s digital capabilities today.Best,
Oleg Shilovitsky
CEO and Co-founder, OpenBOM
Join our newsletter to receive a weekly portion of news, articles, and tips about OpenBOM and our community.