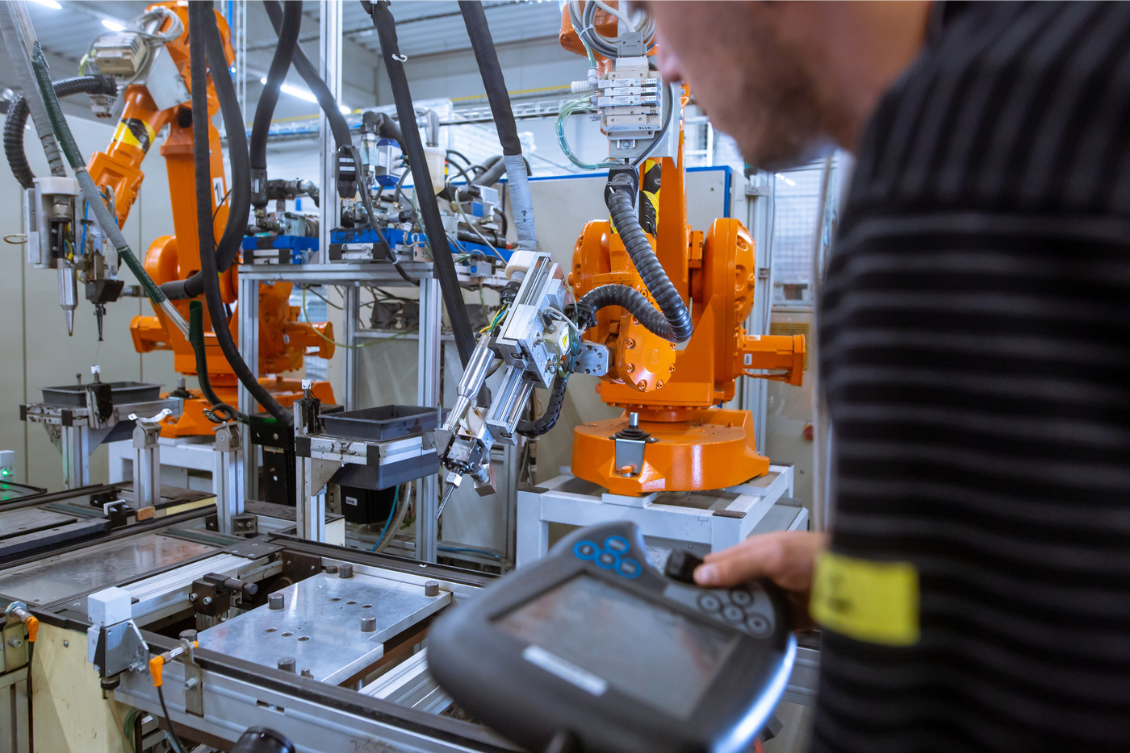
Managing maintenance and tracking data for products already sold to customers has become a vital function for many manufacturing companies these days. As companies grow and customers demand higher levels of service, the ability to maintain, track, and support products in the field is critical to customer satisfaction and business efficiency. Another aspect of tracking existing products is related to Industry 4.0, IoT, Preventive Maintenance Program and similar initiatives. All these needs and initiatives brings a question how to manage the data about each unit sold to the customers.
Whether it’s tracking the life cycle of a product or managing parts and components over time, having a solid system in place for Maintenance BOM (SBOM) and Serial Number (S/N) tracking is key. In this blog, we will explore how OpenBOM delivers this through its flexible data model, xBOM capabilities, and catalog management system, giving manufacturers the tools they need to succeed.
The Importance of Maintenance and Tracking Data
Modern business models allow companies to sell their products and then provide maintenance. Or even simpler – to lease a product. As products become more complex, manufacturers are increasingly expected to provide ongoing support and maintenance, even after the sale is made. Customers want to know that the products they’ve purchased can be serviced, repaired, and tracked through their entire lifecycle. This is where Service & Maintenance BOM (MBOM) comes into play. It ensures that all the necessary information about a product is captured, from the components used to the serial numbers associated with each item. This capability helps manufacturers to track, maintain, and service products effectively, ensuring long-term customer satisfaction and support.
The rise of Industry 4.0 and IoT (Internet of Things) means that products are now often smart, connected devices that require regular updates, diagnostics, and repairs. A robust system for managing Serial Numbers and Maintenance BOMs is essential for manufacturers looking to stay competitive in this space.
OpenBOM’s Flexible Data Model: A Digital Thread for All Product Information
OpenBOM is built to meet these new challenges head-on. Its flexible, cloud-native data model allows for the creation of digital BOMs that represent every aspect of a product’s information, connecting all the data pieces together in one cohesive system. Whether it’s engineering, manufacturing, or maintenance data, OpenBOM’s xBOM system can handle it all.
At the heart of OpenBOM’s architecture is the xBOM model, which provides the flexibility to organize and manage product data from multiple perspectives. This multiview BOM architecture allows manufacturers to represent different BOM types (EBOM, MBOM, and SBOM) to suit specific needs. With OpenBOM, users can easily create and switch between these views, ensuring that the right people have access to the right data at the right time. This dynamic and interconnected approach allows for greater accuracy and efficiency in managing product information across the entire product lifecycle.
The Power of xBOM: Connecting Different BOM Types
OpenBOM’s xBOM is designed to align with various BOM types, ensuring that manufacturers can manage product data seamlessly across different stages of the lifecycle. Some components may be common across all BOMs (such as standard parts), while others are unique to specific BOM types (like service or maintenance-specific parts). OpenBOM’s xBOM data model handles this effortlessly, enabling companies to keep all product data connected yet organized in a way that fits their specific business needs.
For example, EBOM (Engineering BOM) focuses on the design and engineering data, while MBOM (Manufacturing BOM) tracks the items needed during production. The SBOM (Serial BOM or Maintenance BOM), on the other hand, focuses on tracking products and their associated serial numbers during post-sale service. By offering this flexibility, OpenBOM enables manufacturers to stay organized and efficient at all stages of the product lifecycle.
Catalogs: The Backbone of OpenBOM’s Data Model
In OpenBOM, catalogs are the core element of the data model, serving as the foundation for managing items and components. Catalogs enable users to create structured collections of items that can be referenced in any BOM. These catalogs can be customized to include various types of items—whether it’s a standard part, an assembly, or a serial number.
For SBOM management, the catalog plays a crucial role in tracking serial numbers. OpenBOM’s catalog system allows users to automatically generate Serial Numbers (S/N) when needed, ensuring that every item in a maintenance BOM has a unique identifier. This is a game-changer for manufacturers, especially those with a large number of products in the field requiring ongoing maintenance and tracking.
Key Elements of a Serial (or Maintenance) BOM in OpenBOM
A Serial BOM (SBOM) in OpenBOM is more than just a list of parts. It’s an interconnected structure that links together critical data points, allowing for full traceability and serviceability of products in the field. Here are the key elements of a Serial BOM in OpenBOM:
- Catalog for Serial Numbers: A dedicated catalog for managing Serial Numbers ensures that every product or component has a unique identifier. This catalog can automatically generate Serial Numbers when new items are added to the system, simplifying the process of tracking and maintaining products.
- SBOM BOM Type: A separate structure is maintained for SBOM, linking products and components through object references. This allows for detailed tracking and servicing of products over time.
- Single Item Links and Object References: OpenBOM offers the ability to link specific items through URLs or object references, ensuring that the right components and data are connected. Future improvements will enhance this functionality, providing even greater flexibility in how manufacturers can manage their SBOM.
Bringing It All Together
OpenBOM allows manufacturers to define multiple BOM types and item types, making it an ideal solution for managing Serial Numbers and Maintenance BOMs. For effective S/N management, we recommend creating a separate item type and catalog specifically for Serial Numbers. Once catalogs are set up, properties can be added to link these Serial Numbers to other items in the SBOM, ensuring that every product and component is fully traceable and serviceable.
Serial BOMs in OpenBOM work by linking top-level Serial Number items with the related components, creating a fully connected structure that supports efficient maintenance and tracking.
For a deeper dive into how OpenBOM manages Serial Numbers and Maintenance BOMs, watch this video. Stay tuned for an updated video featuring new object property link mechanisms soon!
Conclusion
The demand for better systems to manage Serial Numbers and Maintenance BOMs is growing as manufacturers become more involved with customers after the sale. New business models such as “Product as Service”, leasing product, and others is another reason why the demand for so-called “As Maintained” management is growing. Managing Serial Numbers and Maintenance BOMs is no longer optional—it’s essential for businesses looking to maintain customer relationships and ensure the long-term success of their products.
Tell us more about your needs regarding Serial and Maintenance BOMs! We’d be happy to discuss how OpenBOM can help you better manage your product data.
REGISTER FOR FREE to check how OpenBOM can help you. Best,
Oleg
Join our newsletter to receive a weekly portion of news, articles, and tips about OpenBOM and our community.