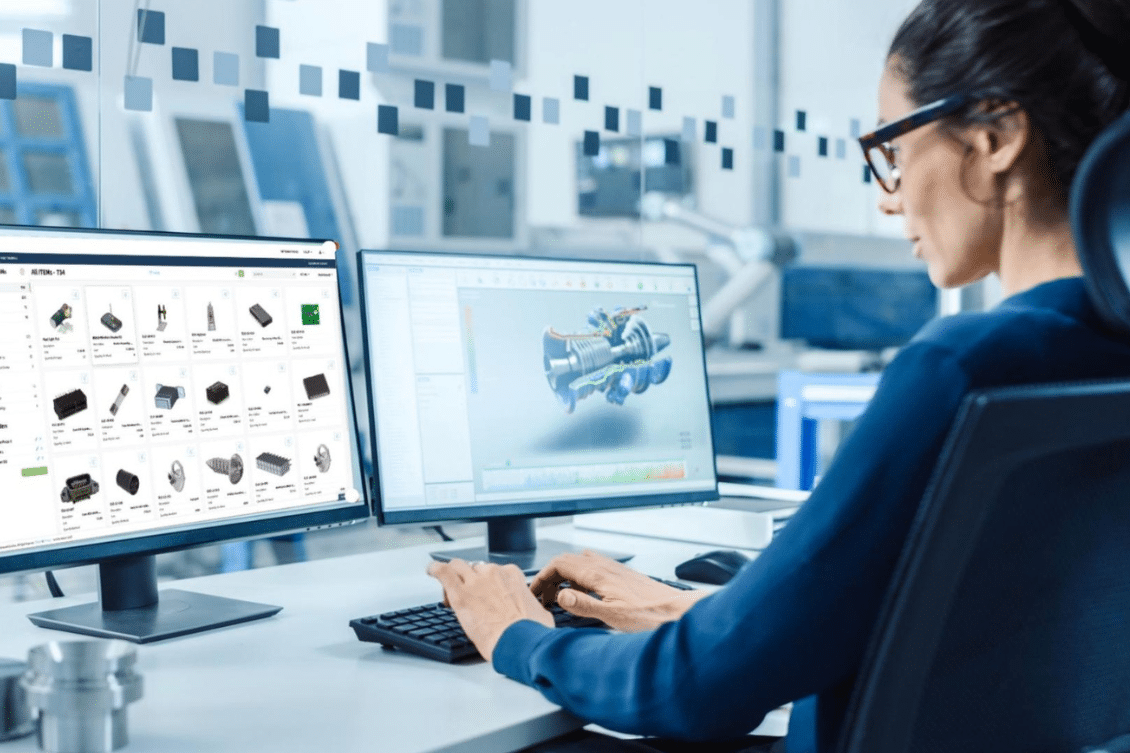
I have been working in the Software Industry for more than 20 years, helping companies in manufacturing go paperless, and digital, from designing consumer products like toasters, machines, trailers, bigger trailers, planes, high-speed boats, and even rockets.
I see myself as a citizen of the world and have worked and lived in different places in the world, from my Portuguese heritage and explorer DNA I lived 10 years in Australia and now am back in Europe in Ireland. During this journey, I met different people and ways of working, different state of art when developing and designing products with computer-aided technologies and resource planning software. Passionate about Data Management and dataflows, I have spent my career perfecting my vision of how this can be archived in the most simple and accurate way.
Excels and Inaccurate Product Data
I have worked with very small companies from “one-man band”, to large corporations with thousands of users to satisfy and keep happy. It gave me a great view of how one size does not fit all. Having embarked on complex integration projects, the integration of Bill Of Materials, the stuff you need to buy to build something and exchange this data to Purchases and Finance systems. I found that simplicity is key to taming complexity. Some products are very complex from mechanical parts, electronics, and wiring up to managing computer Software firmware for the smart bits and pieces. Now imagine managing all the vendors and suppliers to source components, build them and manufacture them.
Yes actually make it, over and over with the need to comply with increasingly demanding regulations. Over this journey I observed many companies using email, Excel, more Excel, and disconnected software tools to capture Product data, Bills of materials, even managing file links to technical drawings, and manually sending emails to suppliers with the latest (they thought so…) files.
Then changes come, change is part of life, and it’s present in product development too. Things change, ideas change, requirements change, and sizes of stuff change. Does it still fit? What impact will it have where this part is used? This question needs to be answered quickly to make the right decisions. I also found that using the wrong tools for the job can hurt your productivity. It’s like building Ikea furniture with a little wench, you can still build it but it will take forever. What about you now make a company to build Ikea furniture as a service, do you still use the wrench? What if a competitor is using power tools? Get the right tool for the job my father always said. Wise words.
Examples of inaccurate data, Excels for Bill Of Materials, filenames, and static text cells for data: ex Description, another problem: no visibility where used for change analysis, broken file links.
It is hard to escape from old Excel ideas and changes are hard. But working with inaccurate data leads to mistakes, increased costs, and delivery delays.
Managing Product Data In OpenBOM
Accurate BOM data. Login and you have the latest and greatest, no ambiguity on filenames. Properties like descriptions are dynamic and updated where used.
Accurate BOMs combining MCAD, ECAD, and non-modeled items like lubricants
Accurate BOM in CAD: Ex SOLIDWORKS ;), PDFs, STEPs created automatically, and Drawing links automatically to latest:
Full visibility where used for change management and impact analysis
Having played a leading role integrating CAD to business systems like MRP for Material resource planning using Advanced technologies like ETL, It means Extract Transform Load, (Load sometimes it’s catapult…) Not having the right data early on and tools to manage it, massage it, and cure data. It’s like having a garbage cannon from CAD to planning systems to source raw materials and parts in stock, having good practices from the start assigning part numbers, building augmented BOMs with mechanical items from SolidWorks, adding the spices, ie, Lubricants, seals, packing with accuracy.
Doing this early on in the development process vs throwing over the fence to procurement can reduce errors and efficiencies can be gained. OpenBOM is the right tool to help you archive an early continuous dataflow from Engineering/Design to Production/Procure, Build an Example of assigning Part Numbers early on in the process:
Send the right data to another system (ex: Quick Books) find all integrations here: OpenBOM Integrations – OpenBOM
Or send a PO to your suppliers by exporting to PDF:
I decided to join OpenBOM for their global vision and because I believed they have the power tools to accelerate building your products with continuous changes and updates from MCAD like Dassault Systemes SOLIDWORKS or PCB design tools like Altium Designer.
OpenBOM is a product development platform to keep manufacturing companies organized and to develop products faster by making the right decisions based on accurate data. You can build products faster with continuous and accurate dataflows from design to production doing agile changes. By doing this, companies designing and building products can achieve their strategic goals faster.
Conclusion
Strategy is not a plan. It’s a framework to make better decisions to achieve a desired outcome. Add the proper tools to your product development strategy, combine the tool with the knowledge of how to use it and you will gain a competitive advantage. I’m part of the customer onboarding and success team so help me to help you to be successful. Give OpenBOM a spin and see it for yourself.
REGISTER FOR FREE and start a 14-day trial to explore all OpenBOM features to learn how OpenBOM can help.
Pedro Branco
Join our newsletter to receive a weekly portion of news, articles, and tips about OpenBOM and our community.