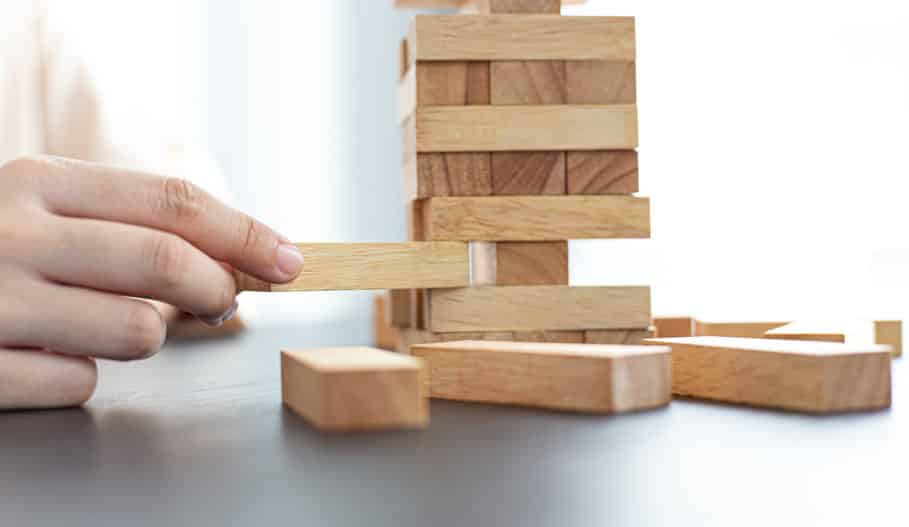
Development risks are inherent in any new product introduction. Unfortunately many engineering teams and manufacturing companies are underestimating the importance of taking care of the most important asset in their company – data. Speaking often to many engineers in manufacturing companies we found that an old fashion “over the wall engineering” methods are still very popular. It is an easy way of thinking – export BOM to Excel and send it over. However, this is how the problem starts.
By managing data properly, companies can mitigate many product development risks and improve their chances for success. In this article, I’d like to focus on 3 risk mitigations strategies and how proper data management can help you to streamline your products development process and be in control of the results more effectively. You’ll learn about the different elements of BOM management and how they can be used to mitigate product development risks. Plus, we’ll give you some tips on how to get started with BOM management.
What is a BOM?
Simplified thinking defines a BOM as a list of components you need to build a product. While it is true, the complexity of the Bill of Materials (or how I prefer to call it product structure) goes much beyond the simple list. A proper bill of materials contains tons of useful information about the product, organizes data in a single source of truth, prevents duplications, supports change history tracking and revision control, allows to calculate rollups (eg. cost), and enables data sharing between all teams and people that must be involved into the product development process.
Why would I need a BOM?
My favorite analogies to support manufacturing teams is to think about food and cooking. Think about the manufacturing process as a dinner project. You need to have a manufacturing plan (what dishes you want to cook), including demand generation (how many guests you expect to have). Your team (think about family) must be heavily involved in order to provide diverse feedback on your plan and requirements and you need to capture them. You need to have a list of meals and each one will have a recipe (keep in mind some recipes might use the same products). You need to make purchase orders (run to a supermarket) to buy all ingredients and you need to have a list of all purchases (this is your procurement task). If some of the ingredients are not available, you need to get ready for replacements (alternate parts and materials to comply with what you need). So, you will mitigate the risk of not getting what you need. A cooking process is your assembly line with machines (cooking tools) and the process of turning them to perform specific tasks. Some of them take time and some require preparations. Once you are done with the prep you need to check the quality and compliance (what if some of your guests have a food allergy, how do you know which products include specific ingredients). As you can see, having a proper BOM can be useful and will provide you with the foundation to solve all issues.
How do I create a BOM for my products?
The BOM can be increasingly complex because it contains many elements – components, assemblies, materials. There are multiple ways to create a bill of materials, but the most important thing is to start with your product design, which is the foundation of everything. By capturing design data, you mitigate the risks of creating an incomplete or inaccurate Bill of Materials. Then you take care of business information (eg. cost, suppliers, compliance, etc.). To separate business and design data is a good practice in which you can achieve collaboration between different stakeholders and not create dependencies of data (eg. Cost and Vendor information should not be stored with your design). Starting from design and adding/importing information from multiple sources is the way to go. One of the most important things is managing the process of changes once the product is leaving the engineering space and manufacturing, procurement and contractors are starting to be engaged.
How can OpenBOM help to mitigate risks in product development?
Manufacturers are underestimating the importance of having a complete materials list and managing data in a consistent way. There are three important risks you can mitigate with proper BOM management:
Cost Risk Mitigation
There is no single manufacturing company in the world that would not be interested in how to control the cost of the product. But, at the same time, companies rely on messy spreadsheets to calculate the cost. The data is often copied between multiple spreadsheets without proper control and, as a result, important cost factors can be just missed. I’ve seen so many mistakes of forgotten components, wrong cost information, wrong calculations, and many others. A shared BOM with all stakeholders can ensure you work on the correct data set and get predictable cost analysis.
Procurement
Siloed information is another risk and when it comes to procurement, it is a big one. How to ensure purchasing people are involved on time and getting proper information. Modern supply chain challenges just adding to this (already complex) problem. BOM management allows you to control purchasing process, to ensure the right information is provided on time and changes are propagated properly.
Regulation
Regulation and compliance are a big deal these days. Global market, changed regulation policies, risks for litigations, and increased consumer awareness – this is just a shortlist of possible risks. Without having a BOM with all information and, also very important, full history and track of changes, you have no way to know what happened in the product and how to report to regulators during the monitoring and (g-d forbid) emergent situations.
What are the benefits of using a BOM management system like OpenBOM?
Here is a short list of benefits you can get when managing the data about products using a system like OpenBOM:
- A single source of truth for all items, Part Numbers, BOMs, files, documents, and information
- Full traceability of history (changes, revisions, etc.)
- Automatic data capturing and updates (avoiding mistakes)
- Real-time data sharing ensures nobody works on the wrong data sets
- Automatic calculations (flattened BOM, cost rollups, etc.)
You can see how OpenBOM can elevate your processes, streamline the information flow and avoid mistakes.
What are the disadvantages of not using one?
My Excels are simple and give me what I need. This is the beginning of the disaster. Here is a short list of problems you will face in the case you continue to use spreadsheets to manage BOM and related data.
- Working on the wrong data
- Buying wrong parts
- Overpaying for last-minute shipments
- Miss your cost targets
- Failing in your regulatory compliance
- Overpaying to CM for sending wrong information
Conclusion
OpenBOM offers you a simple yet flexible and configurable platform to manage product information – items, BOMs, documents, purchases. OpenBOM helps you to organize a single source of truth for your product data, control history, revisions, and changes. OpenBOM automates calculations and always allows for your extended team – to stay on the same BOM.
Check out how OpenBOM can help – register for FREE and start a 14-day free trial for all features.
Best, Oleg
Join our newsletter to receive a weekly portion of news, articles, and tips about OpenBOM and our community.