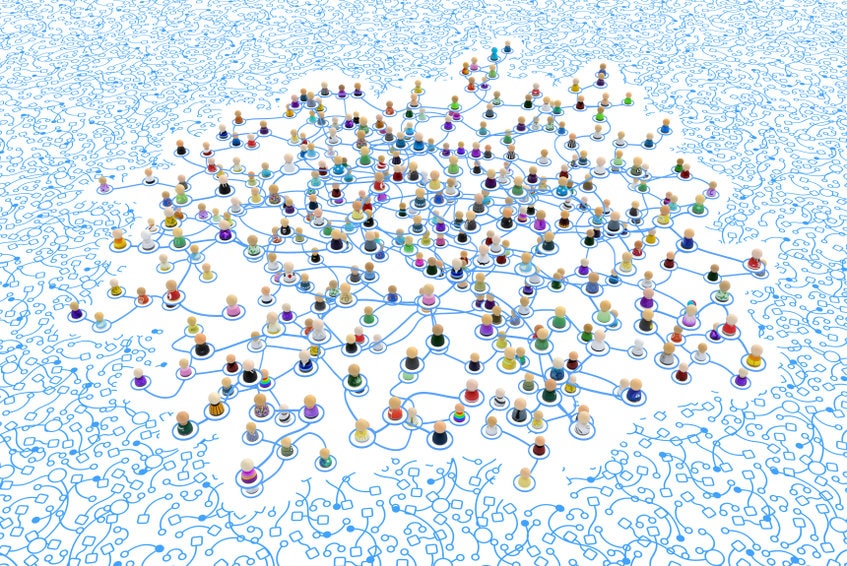
Modern manufacturing is a complex system. The time when a single manufacturing company was located in a big building making everything from glass, rubber, and steel to the end product is gone forever. Back in the old days when Henry Ford created a big Rouge Manufacturing complex in Detroit, the entire car was done in a single building. These days products are developed by multiple companies OEMs, multiple tiers of suppliers working together. The work is often done globally on multiple plants that make products in different configurations for different markets.
In the picture below you can see a difference in the automotive industry displayed with the distance of 100 years. You can see the complexity.
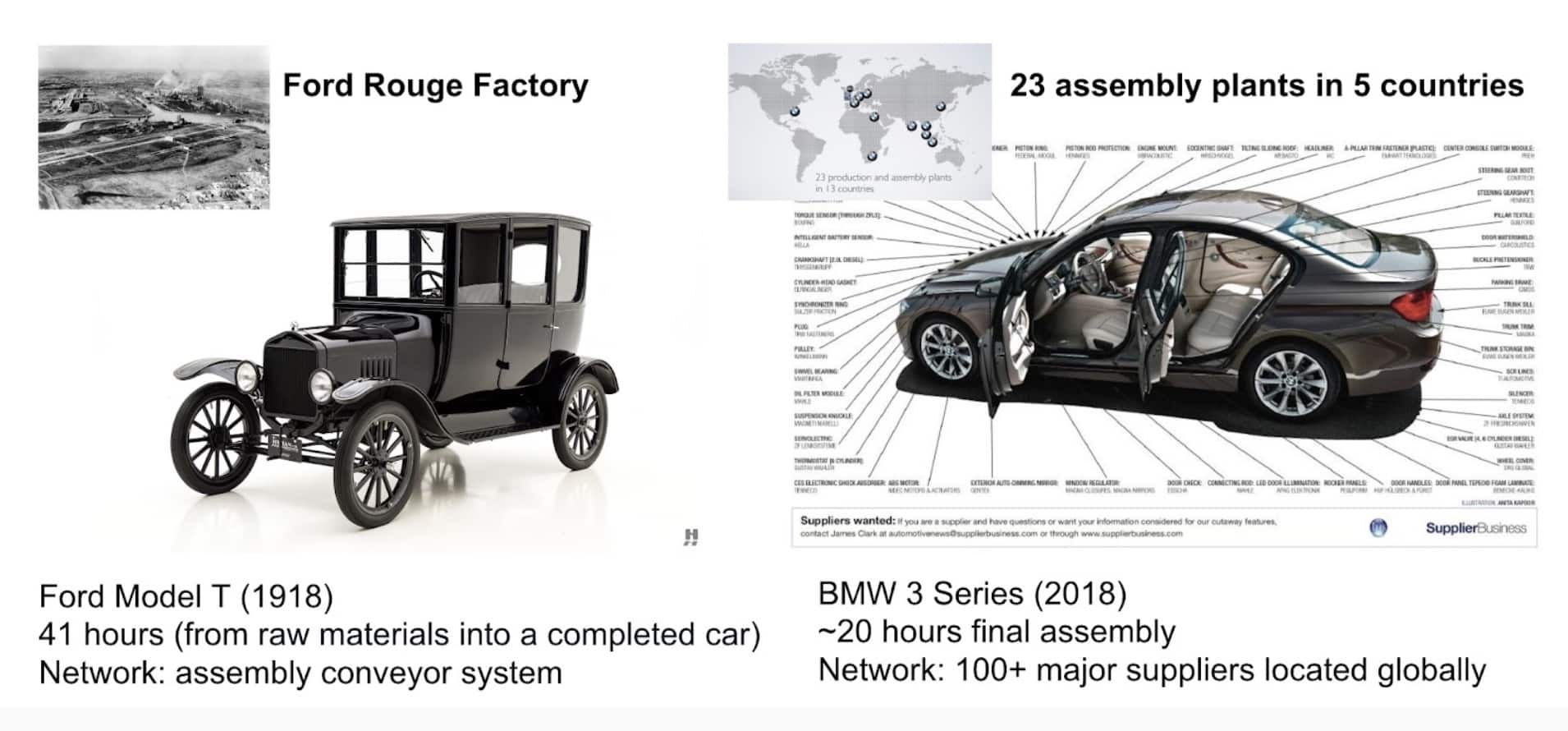
Cross Company Collaboration and Change Processes
How to organize the work in such complex systems of OEMs, multiple tiers of suppliers, and contractors. Many questions are coming here. Here are a few examples. An OEM – Tier 1 collaboration is a very complex process and involves decisions about changes that must be done on both sides (OEM and Tier1) while the production facility is running. There is a huge need to make this communication efficient, trace requests, approvals, and changes. The outcome of the change process is measured in time and $$$ that must be paid by both parties. Tracing a connected process is extremely time-consuming. Another example is communication between Tier 1 suppliers downstream. These Tier 2-n suppliers are demanding efficient data sharing and collaboration while dependent on the work that must be done with the information provided by upper Tier – also requirements as well as engineering and manufacturing data.
Manufacturing networks are complex systems that require the collaboration of multiple tenants in order to operate effectively. In a multi-tenant manufacturing network, each tenant has its own specific function within the overall system, and cooperation among all tenants is essential for success. This blog post will bring examples and the benefits of multi-tenant collaboration in manufacturing networks and discuss some of the key factors that contribute to success.
Challenges of Mainstream PLM Architectures
Existing PLM architectures that are widely adopted by large OEMs and enterprise companies are very limited when it comes to the collaboration between companies. The reason is very simple – all mainstream PLM architectures (from Teamcenter to Windchill and even Aras) are single-tenant architectures relying on SQL database platforms. Bringing these systems to the cloud (aka enterprise SaaS) doesn’t make a big difference besides saving IT time for installation, upgrades, and maintenance. Everything else remains the same. Either OEM should give access to its Tier1 to the same platform or data must be exported and transferred between systems. None of these solutions is good enough.
In my article SaaS vs Hosted PLM – Practical Differences for Manufacturing Companies, I demonstrated how modern multi-tenant architecture can provide a big advantage in sharing data between multiple companies and managing processes crossing companies’ boundaries.
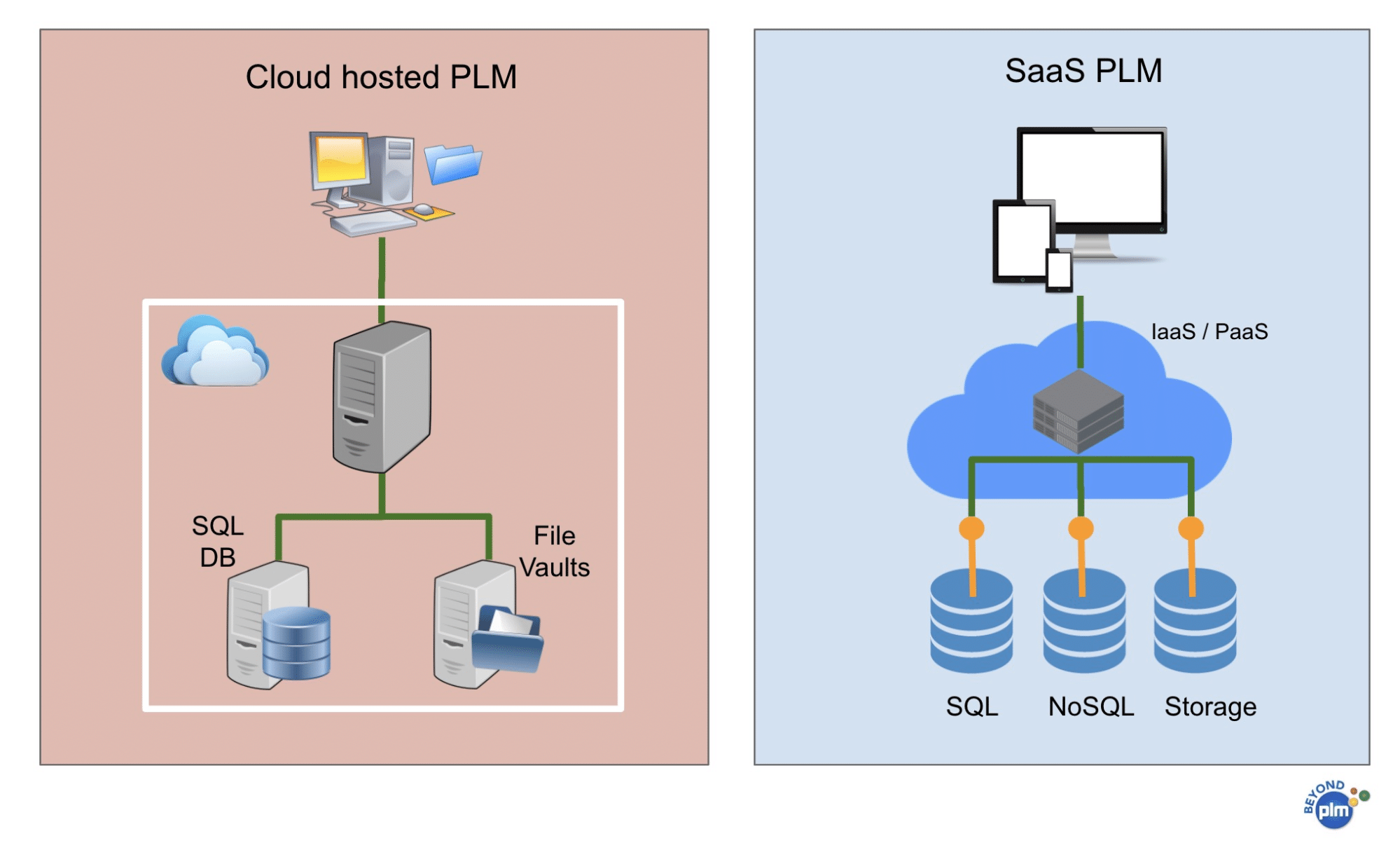
Here is the passage that explains what is the difference between single-tenant and multitenant architectures.
A foundation of SaaS product lifecycle management is a technological platform provided by a vendor and capable to serve multiple users and companies at the same time. From the technology standpoint, such a platform is optimized for online services, global access, security, and data retention. An important differentiator of a SaaS platform is multi-tenant technology allowing the use of shared computing resources, but also might have a multi-tenant data model. You need to spot the last one because it is really important. Can one user share the data with another user if they don’t work for the same company (eg. OEM and contractor)? If the answer is yes then you have a multi-tenant data model. Such a model provides a “network layer” in data management architecture, which is extremely important for cross-company business processes and data intelligence capabilities. Without a multi-tenant data model, multi-tenancy is very limited to the usage of shared computing resources that limit overall SaaS benefits for the customers.
Cross Companies Processes and Digital Thread
A multi-tenant data-management architecture is the foundation of the new solutions that can help to establish communication, collaboration, and organize processes between multiple companies. Such an architecture enables organizations to organize a common shared digital thread of information managed by multiple companies and organize a process that involves people and data from multiple organizations.
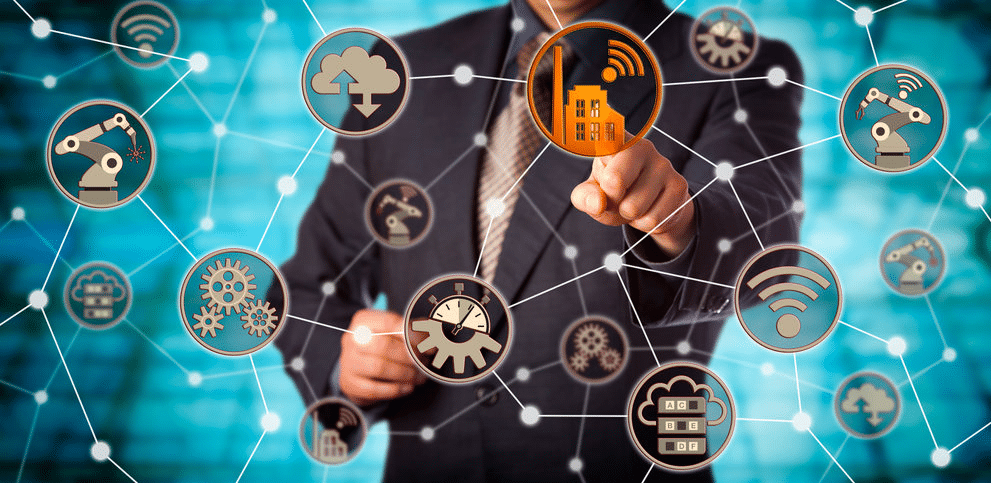
Getting back to my examples at the beginning of the article, Tier 1 suppliers can establish a change process that involves the approval of OEM and share a common piece of information that is needed for such a change process to be approved and executed. In a different example, the data can be shared by Tier 1 suppliers downstream to streamline the process and communication with subcontractors.
Infrastructure, Platforms, and Services
An important question is what infrastructure should be used for a modern platform? In the past, everyone in the PLM business used RDBMS systems, because it was a scalable platform that was approved by IT organizations. So, if you run on one of them, the IT approval is secured.
These days, AWS, Azure, GCP, and similar technologies are new platform foundations. Manufacturing companies are looking at how to get a digital stack built on top of these cloud platforms and using modern microservice architecture.
Conclusion
Modern manufacturing systems demand a new approach to managing data and processes between companies, streamlining communication, providing visibility on data, and the impact of changes. Mainstream PLM architectures fall short in supporting the desired level of process management and collaboration. As manufacturers are focusing on digital transformation, the questions about new architecture are becoming sound and clear.
OpenBOM is developing an innovative multi-tenant data architecture that is capable of providing flexible data modeling capabilities and allowing multiple parties in the change management process. Such new types of data sharing and communication can simplify process management, improve data transparency, allow cross-company data visibility and accountability, and, finally, optimize the process management in complex relationships between OEMs and multiple suppliers’ tiers.
OpenBOM architecture fits well as a modern IaaS platform infrastructure such as AWS, Azure, and GCP and can be used as a service to provide solutions to manufacturing companies and to support them in their digital transformation process.
The switch to multi-tenant architecture won’t happen overnight. However, it will provide a fundamental shift in data management and process orchestration that cannot be achieved using existing mainstream PLM systems. It is a time to remember Microsoft’s CTO Nathan Myhrvold’s quote – “If you want to have a great future you have to start thinking about it in the present because when the future’s here you won’t have the time.”
So, for many manufacturing companies, it is time to think about the future of manufacturing networks and how manufacturing companies will transform themselves using digital methods of collaboration and process management. Companies that will miss the time, might not be able to survive the digital revolution.
At OpenBOM, we discuss with manufacturing companies how modern digital infrastructure and data management platforms can help to streamline processes. Contact us today to discuss how OpenBOM can help you in your digital journey.
Best, Oleg
Join our newsletter to receive a weekly portion of news, articles, and tips about OpenBOM and our community.