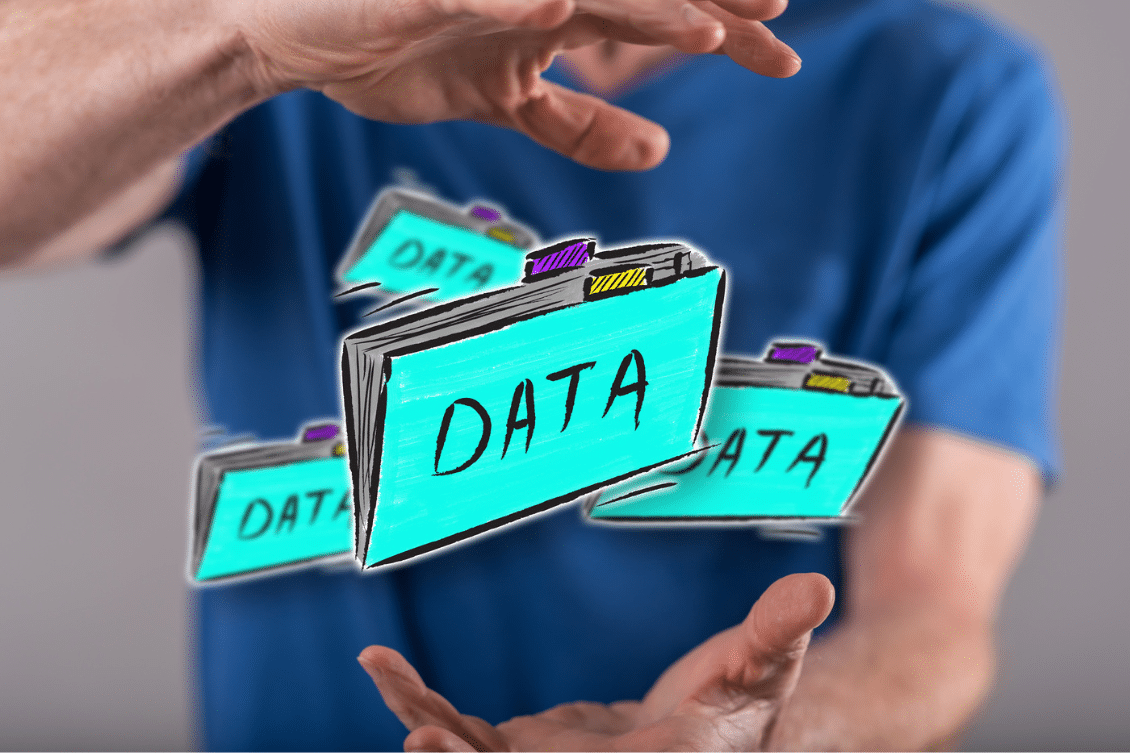
In today’s digital age, data management holds paramount importance, especially for engineering and manufacturing organizations. As everything transitions into the digital space, from initial product design to manufacturing processes, the need to efficiently manage vast sets of data becomes crucial. Whether it’s 3D geometry, material specifications, purchase orders, or work orders, every piece of information plays a critical role in the product life cycle.
In my article today, I want to help manufacturing startups and other engineering and manufacturing organizations avoid data management pitfalls and choose the right way to manage data. It will help you choose the right path in building robust data management and avoiding some data management traps. The strategy was used by many organizations implementing OpenBOM today and also for years of consulting organizations with PLM solutions.
Aligning Data Management with Complexity:
Just as the right tool is essential for a job, the proper data management strategy is imperative for handling the complexities inherent in engineering and manufacturing. Avoiding the risks of managing extensive datasets in inadequate platforms, such as Excel spreadsheets, or deploying enterprise PLM platforms is vital.
To navigate this, I’d like to outline six pivotal steps in product development and manufacturing, guiding organizations toward an optimized data management approach:
Idea Generation:
The initial stage of idea generation may require minimal data management or demand a comprehensive approach, depending on the complexity of the product. Simple product concepts might be adequately managed with basic CAD files or sketches. However, for projects involving the redesign of existing complex products, detailed data management becomes indispensable. Imagine you have a complex device or robotic equipment that has thousands of parts. The new product is a modified version of the old one. It is critical to put a detailed BOM in place from the beginning. Otherwise, you will be running for copies of your Excel spreadsheets, spending time, and effort and making mistakes.
Prototype Development and Small Batch Production:
Prototyping represents the early version of a product. Depending on its complexity, which may involve hundreds or thousands of components, managing data structures effectively is crucial. This stage necessitates swift decision-making regarding suppliers, component selection, feasibility, cost, and speed to avoid delays or setbacks in prototype development.
To make it happen, we recommend setting product records early in the process. It includes managing items with detailed information as well as setting up BOM (product structures). It will help you to estimate cost, do planning, and perform orders for prototyping in an organized manner.
Scaling and Outsourcing:
As products move towards mass production, managing traceability, communication channels, and other crucial aspects becomes paramount. Ensuring seamless data management facilitates smooth scaling and outsourcing processes, preventing bottlenecks and enhancing operational efficiency.
It is a great idea to set up a revision baseline that will allow you to track what revision was communicated to your contractors and suppliers. If you manufacture in-house, managing data for each lifecycle stage- Engineering, Planning, Production, Built, and Maintenance can be critical.
Avoiding Enterprise PLM Traps:
The complexity associated with enterprise Product Lifecycle Management (PLM) systems can sometimes outweigh their benefits, especially if implemented prematurely or excessively. Organizations must strike a balance between complexity and efficiency, steering clear of over-engineering solutions that do not align with their immediate needs.
The idea of Enterprise PLM scaled down was around for the last two decades, but it never materialized. So-called “light” out-of-the-box enterprise PLM knockoffs can be deployed, but the outcome is usually a huge organizational overhead and inability for flexible changes. So, check carefully, if you decide to take this path.
When to Integrate ERP:
Enterprise Resource Planning (ERP) systems offer comprehensive solutions for managing various aspects of manufacturing operations. However, integrating ERP should be approached with caution to prevent unnecessary complexities.
Evaluating scalability requirements and implementing ERP systems when truly needed ensures optimal resource utilization.
At OpenBOM, we provide basic “light ERP” functionality such as inventory management and purchase ordering. It helps to manage prototypes and small batches. Once you decide that ERP is the next step, OpenBOM will help you to manage EBOM and integrate with any ERP system.
Choosing the Right Time:
Timing is crucial when implementing data management solutions. Organizations should assess their specific requirements thoroughly and invest in appropriate tools and systems only when necessary. Avoiding premature investments in complex solutions allows for a more agile and cost-effective approach to data management.
Conclusion:
Crafting an effective data management strategy tailored to the unique needs of engineering and manufacturing organizations is paramount in today’s digital landscape. By aligning data management practices with the complexities inherent in each stage of product development and manufacturing, businesses can streamline operations, enhance productivity, and stay ahead in a rapidly evolving market.
The key question is how to embrace a pragmatic approach that prioritizes efficiency and scalability ensure long-term success in managing the wealth of data integral to modern manufacturing processes.
To be successful in data management, you need to prioritize the importance of digital information but take careful small steps forward to increase the complexity while preserving the efficiency of operation. Keep in mind that organizations of your process usually need to be done before you deploy computerized systems. If you have a mess, you need to clean the mess first and then bring data management systems.
At OpenBOM we help you to take small steps and improve your solution over time.
REGISTER FOR FREE and check out OpenBOM and see how it can help you today.
Best regards,
Oleg
Join our newsletter to receive a weekly portion of news, articles, and tips about OpenBOM and our community.