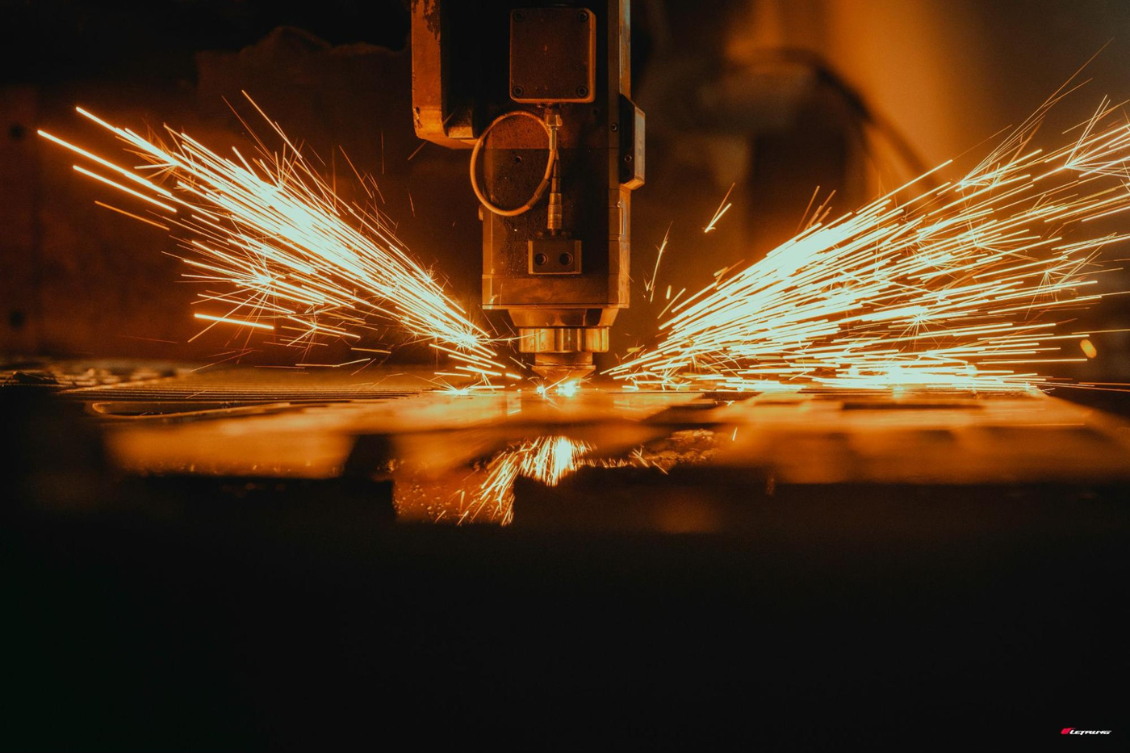
Transitioning from prototype to mass production is a pivotal moment in the lifecycle of any product. It’s the phase where innovative ideas and designs must transform into scalable, market-ready goods. This shift is crucial not only for the success of the product but also for the efficiency and profitability of the production process.
During the prototype phase, you’ve likely spent considerable time perfecting your design, conducting tests, and addressing initial feedback. However, as you move towards mass production, the stakes change. Now, it’s about ensuring that your product can be manufactured consistently, cost-effectively, and at scale. This involves working closely with your supplier to navigate a range of challenges, from refining the prototype for large-scale production to managing quality control and cost.
In this blog, we’ll explore the key steps and best practices for making this transition smoothly. We’ll cover how to select the right supplier and plan the transition effectively. By understanding these critical aspects, you can set yourself up for a successful mass production phase, ensuring your product meets market demands while maintaining high standards of quality and efficiency.
Understanding the Prototype Phase
The prototype phase is a critical stage in the product development process where ideas begin to take tangible form. It’s an opportunity to test, refine, and validate a concept before committing to full-scale production.
Definition and Purpose of Prototypes
Prototypes are early samples or models of a product used to test and validate design concepts, functionality, and market appeal. They serve several key purposes:
- Design Validation: Prototypes help verify that the product design works as intended and meets the initial objectives.
- Functionality Testing: They allow for real-world testing to ensure that the product performs its intended functions under various conditions.
- User Feedback: Prototypes provide a tangible product that stakeholders, including potential customers, can interact with, offering valuable insights into usability and user experience.
- Design Iteration: They enable designers and engineers to identify and address issues early, reducing the risk of costly changes later in the production process.
Key Objectives
The primary objectives during the prototype phase include:
- Refinement of Design: Testing the prototype helps identify design flaws and areas for improvement. This iterative process ensures the final product is both functional and aesthetically pleasing.
- Validation of Materials and Processes: Prototypes often use materials and manufacturing methods that are close to those intended for mass production, providing a preliminary sense of how these elements will perform.
- Cost Estimation: Early prototypes can help estimate production costs by highlighting potential challenges in materials or manufacturing processes.
Common Challenges
While the prototype phase is essential, it’s not without its challenges:
- Unexpected Issues: Testing can reveal unforeseen problems, such as design flaws or performance issues, which need to be addressed before moving to mass production.
- Limited Scalability: Prototypes are often produced in small quantities, which can differ significantly from the processes and costs involved in large-scale production.
- Iteration Delays: Frequent iterations and adjustments to the prototype can delay the overall development timeline, impacting the transition to mass production.
Choosing the Right Supplier
Selecting the right supplier is a critical decision that can significantly impact the success of transitioning from prototypes to mass production. The supplier you choose will be instrumental in scaling your product efficiently and effectively.
The ability to scale from prototypes to mass production is not just about increasing output; it involves a complex interplay of quality control, process optimization, and cost management. A supplier who excels in both small and large-scale production can:
- Ensure Consistent Quality: A supplier with experience in scaling up can maintain high quality and consistency throughout the production process.
- Adapt Quickly: They can efficiently adapt to design changes and manufacturing requirements that may arise during the transition.
- Optimize Costs: Experienced suppliers are adept at managing costs effectively, and finding ways to reduce expenses while maintaining product quality.
- Manage Timelines: They can better handle the ramp-up process, ensuring that production schedules are met without delays.
When evaluating potential suppliers, consider the following criteria to ensure they can handle both prototype and mass production phases:
- Capabilities: Assess whether the supplier has the necessary equipment, technology, and expertise to produce your product. This includes evaluating their manufacturing processes, production capacity, and ability to work with the materials and techniques used in your prototype.
- Technological Compatibility: Ensure that their technology aligns with your product requirements and can scale as needed.
- Production Capacity: Verify that they have the production capacity to handle increased volumes without compromising quality.
- Reliability: The supplier’s reliability is crucial for maintaining production schedules and meeting deadlines. Look for:
- Track Record: Review their history of meeting deadlines and delivering consistent quality.
- References and Reviews: Check references from other clients and read reviews to gauge their reputation and reliability.
- Communication: Evaluate their responsiveness and clarity in communication, as this will impact the efficiency of your collaboration.
- Experience: A supplier’s experience in your industry or with similar products can be a significant advantage. Consider:
- Industry Experience: Suppliers with relevant experience will be more familiar with industry standards and potential pitfalls.
- Previous Projects: Review their portfolio or case studies of similar projects to understand their expertise and problem-solving capabilities.
Choosing the right supplier who can effectively manage both prototype and mass production phases is essential for a smooth and successful product launch. By carefully evaluating suppliers based on their capabilities, reliability, and experience, and by assessing their ability to handle varying production scales, you can set the stage for a successful transition and long-term partnership.
Transition Planning
Transitioning from prototype to mass production is a complex process that requires planning and coordination. To ensure a smooth transition, focus on developing a clear transition plan, establishing effective communication with your supplier, and maintaining thorough documentation.
Developing a Transition Plan
A well-crafted transition plan acts as a roadmap for moving from prototypes to mass production. Start by establishing a detailed timeline that includes key phases such as completing prototype testing, finalizing the design, preparing for production, conducting pilot runs, and ramping up to full-scale manufacturing. Setting specific milestones, such as final design approval, completion of tooling, successful pilot runs, and the start of full production, helps track progress and ensure that the transition stays on schedule. Additionally, define measurable goals for the process, including quality targets, production efficiency, and cost management.
Setting Clear Expectations and Communication Channels
Effective communication with your supplier is essential for a successful transition. Clearly outline your expectations regarding production timelines, quality standards, and any critical requirements. Establish regular communication channels, such as scheduled meetings or calls, to review progress and address concerns. Define how updates and reports will be shared and designate primary points of contact on both sides to streamline interactions. Having a structured process for escalating and resolving issues ensures that any problems are addressed promptly and effectively.
Importance of Thorough Documentation
Thorough documentation is crucial for ensuring that the transition from prototype to mass production is seamless. Provide detailed design specifications that include dimensions, materials, and tolerances to ensure the supplier can accurately reproduce the product. Document quality standards and testing protocols to maintain consistency and adhere to required standards. Additionally, outline production processes clearly, including procedures, equipment requirements, and workflow, to align both your team and the supplier on how the product should be manufactured.
By focusing on these elements—developing a robust transition plan, setting clear expectations, and maintaining comprehensive documentation—you can effectively navigate the shift from prototype to mass production. This approach helps minimize risks, ensures quality, and paves the way for a successful product launch.
Conclusion
Navigating the journey from prototype to full-scale production in contract manufacturing requires a deep understanding of the prototype phase, careful selection of the right supplier, and thorough planning for a seamless transition to production. By prioritizing clear communication, establishing solid partnerships, and proactively managing each step, manufacturers can significantly reduce risks, ensure product quality, and accelerate time-to-market. Whether you’re a startup or an established company, a strategic approach to contract manufacturing can turn your innovative ideas into successful products.
By: Jared Haw
Join our newsletter to receive a weekly portion of news, articles, and tips about OpenBOM and our community.