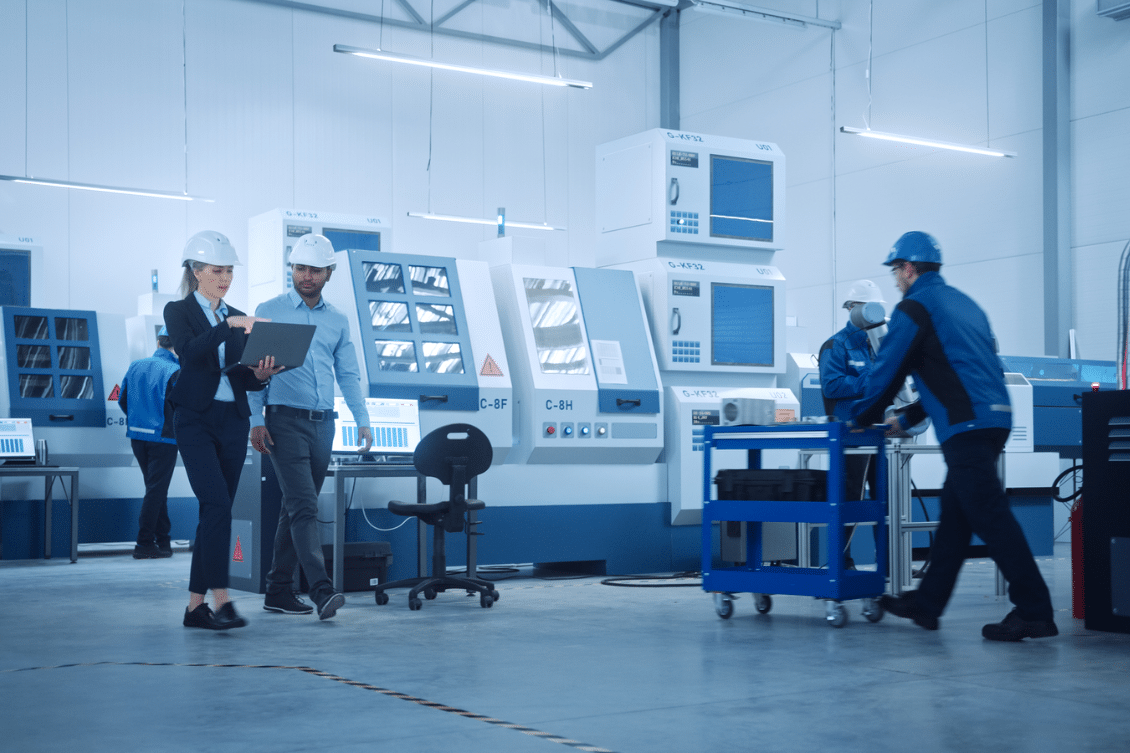
Earlier this week, I was talking about OpenBOM Agile New Product Development and What Differentiates OpenBOM from all other PLM systems. If you didn’t check these articles, please do it right now. If you have no time, here is my TL, DR – OpenBOM gives you a combination of services usually found in multiple enterprise systems – PDM, PLM, and ERP. At OpenBOM, we take a different approach from traditional enterprise systems – instead of focusing on how to implement multiple systems and integrate them together, we build a flexible platform and developed an integrated set of online services (SaaS) to focus on how to connect people into a cohesive business process. Our focus on New Product Development process is not random. Speaking with thousands of companies and engineers we found that New Product Development is a process where industrial companies are the most sensitive to time, efficiency of their work and effectiveness of their decisions.
In the wake of technological innovation, businesses worldwide are exploring novel methods to streamline their workflows and optimize product development. OpenBOM is a unified digital thread platform that seeks to revolutionize the way companies handle product development, engineering, and manufacturing.
In this article today, I want to walk you through the story step by step. Also, in the end, we will speak about why an integrated process makes sense to many companies and why you should consider switching to OpenBOM.
Why Replace Excel?
Excel has been the tried-and-true companion for many businesses in handling data management for years. However, with the complexity of modern product development processes, it’s becoming increasingly challenging for Excel to keep up.
One of the significant issues with Excel is the difficulty of maintaining data integrity. Mistakes can occur easily, and the lack of built-in validation means that errors can propagate through multiple documents before they’re noticed. This can lead to significant problems in planning and production.
Moreover, Excel lacks the collaborative features necessary for today’s distributed teams. On the other hand, OpenBOM offers a cloud-based, collaborative environment, enabling teams to access and edit the same documents in real-time.
Integrate with CAD (MCAD, ECAD, etc.)
Incorporating Computer-Aided Design (CAD) into product development has been a game-changer for many companies. OpenBOM’s seamless integration with popular CAD tools takes this a step further, ensuring a smooth flow of data from the design stage to production and beyond.
Seamless “one-click integrations” allows OpenBOM users to seamlessly integrate with CAD systems and extract data to be sent to OpenBOM Drive. Imagine the scenario where your design team modifies a product design. With CAD integration, these changes can be instantly reflected in your BOM, preventing costly errors and rework. ABC Manufacturing is an excellent example of this. After implementing OpenBOM, they reported a 50% reduction in time spent on design revisions and associated production adjustments.
Item, BOM Management and Unique Collaboration
OpenBOM provides robust item management, allowing you to track individual parts, assemblies, and their associated metadata. With this data, you can easily generate BOMs that accurately reflect your product structure.
Change management is another critical function that OpenBOM handles with confidence but differently. If a component needs to be updated or replaced, OpenBOM allows you to track these changes and their impacts on the overall product.
Integrated Change Management
OpenBOM’s PDM and PLM features provide a comprehensive view of your product data across multiple set of changes. OpenBOM automatically track history of changes, allows to capture revisions and control change process with collaborative approvals mechanism. An important aspect of these features is the ability to manage Item and BOM revisions and engineering change orders.
Inventory+Procurement
Lastly, OpenBOM offers batch-oriented inventory management and procurement features (RFQ/PO). It allows real-time tracking of stock levels, provides alerts for low stock, and can generate purchase orders automatically based on predefined rules.
This integration of inventory and procurement functions can lead to significant cost savings by reducing the risk of overstocking and ensuring you never run out of critical components.
Customer Stories
I want to end up the article by mentioning some notable quotes from OpenBOM customers, speaking about how OpenBOM helped them to streamline processes and improve the process workflow.
“it is right-sized for my company. Filling a niche that MRP systems are not. Other programs are too limited or cost too much. OpenBOM offers a lot of benefits to a company in a certain range and at a great value.“ John E, President, Gates Underwater. Read the story
“Just as Onshape is a single source of truth for the CAD design, OpenBOM does the same for manufacturing production planning, purchasing, and inventory control. It is a perfect relationship.” David Rubli, Senior Mechanical Engineer, Xtend Robotics. Read the story
Conclusion
In the ever-evolving landscape of product development, companies must leverage technology to stay competitive. OpenBOM presents a compelling option that combines powerful features with an intuitive, collaborative interface. By replacing traditional tools like Excel, integrating with CAD systems, and offering comprehensive PDM/PLM features, OpenBOM can streamline your product development processes and lead to significant improvements in efficiency and effectiveness.
REGISTER TODAY and start your FREE 14-DAY trial!
Best, Oleg
Join our newsletter to receive a weekly portion of news, articles, and tips about OpenBOM and our community.