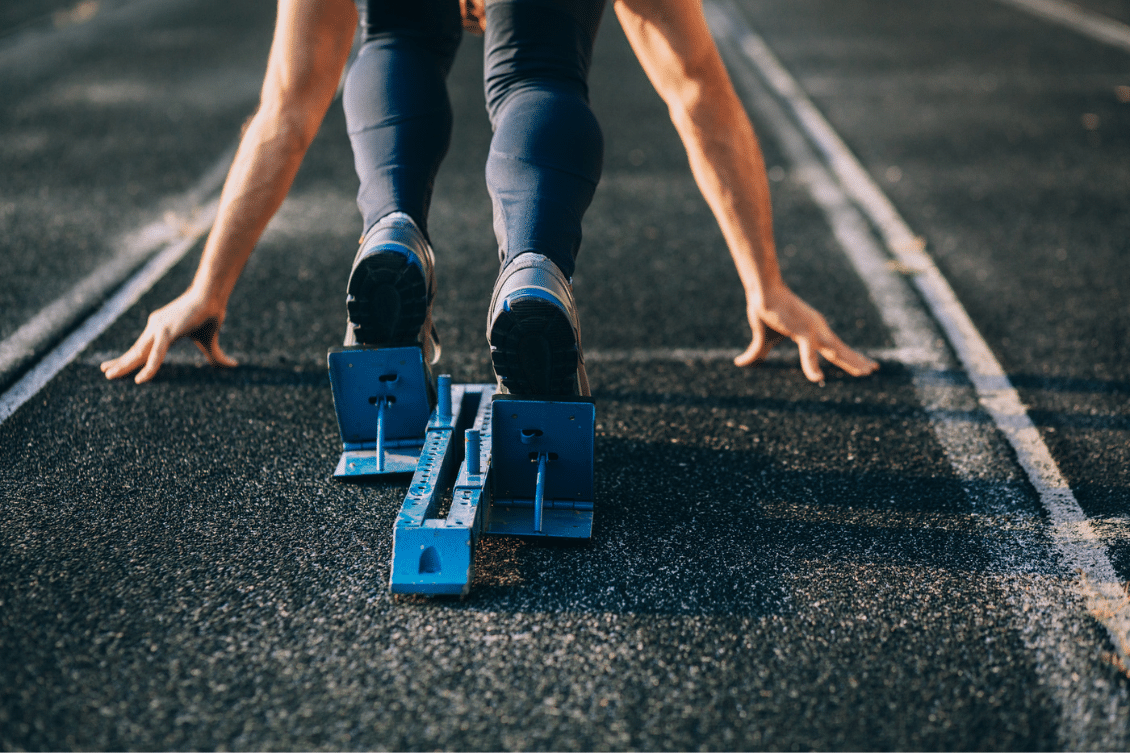
Learning new software is like drinking from a firehouse. I’m continuing a series of articles that helps you to start using OpenBOM in a more efficient way. If you missed the beginning of it, please navigate to the following articles where I provided OpenBOM Basics: Essential Guide, Introduction to Agile New Product Development, and Introduction to OpenBOM Product Model and BOM Types.
OpenBOM allows you to enhance your product development processes by allowing you to manage and track data, changes and perform procurement planning. As a new user, understanding OpenBOM’s functionality can be daunting. But don’t worry, we’re here to simplify it for you. OpenBOM training and support will help you.
Today, I want to take a non-systematic approach and talk about 7 OpenBOM features that continuously delight our customers when it comes to demonstrations, questions, and discussions.
1. “Where Used” and Graph Navigation
If you ever made an analysis of product data, you can understand why the “Where Used” feature is a lifesaver when you need to identify where a particular part or assembly is utilized across all your BOMs. If a part needs to be replaced or updated, “Where Used” shows you every BOM that would be affected. This feature saves time, reduces errors, and can contribute significantly to cost-saving measures.
OpenBOM gives you multiple options to navigate “where used” information. You can navigate to where you used the command in the OpenBOM dashboard, bill of materials, or catalogs, as well as use our newest addition to OpenBOM – Graph Navigation.
2. Flattened BOM Feature
The Flattened BOM Feature allows you to view your bill of materials in a simplified, single-level format. This is particularly useful when dealing with complex multi-level BOMs, as it provides a clear, linear representation of all parts and assemblies involved with quantity rollup calculating the occurrence of all components across multiple assemblies. You no longer have to navigate through various sub-assemblies to get a comprehensive overview.
The Flattened BOM is extremely useful when you work in procurement and need to quickly summarize the number of components in complex assemblies. It is an absolute lifesaver when you have multiple CAD assemblies that don’t have a common assembly but are used in the same project and have common parts.
3. Automatically Generated Derivatives (PDF, STEP, DWG, etc.) from CAD
One of the key highlights of OpenBOM is its ability to automatically generate a variety of derivative files directly from your CAD models. This includes popular formats like PDF, STEP, DWG, and more. This feature is a game-changer, as it saves time and ensures that your entire team, including non-CAD users, has access to the necessary design data in a format that suits their needs.
Imagine you need to create a package for your contract manufacturer. You need to get all your CAD data aligned, create STEPs, generate PDFs of drawings, etc. Doing all this manually is possible, but this is not an exciting task that every engineer likes to do. Also, it can lead to costly mistakes. Instead, OpenBOM can make it automatically, eliminating mistakes and saving engineering time.
4. Generate Part Numbers for CAD Data
One of the most loaded questions in any engineering and product development organization – is part numbers. We have a separate article that speaks about Part Numbers alone. But here I want to speak about the process of automatical Part Number assignment with CAD data.
OpenBOM helps to streamline and standardize your processes by automatically generating part numbers for your CAD data. This not only saves valuable time but also ensures consistency across your project. The generated part numbers are unique and can be customized to match your company’s part numbering system.
5. Create RFQs and POs
The OpenBOM tool also includes features that facilitate procurement processes. The ability to create Purchase Orders (PO) or RFQ directly within the system speeds up procurement and helps maintain a centralized record. This feature reduces miscommunication and increases efficiency, allowing you to keep your project on track and within budget.OpenBOM integrated inventory management allows you to manage Quantity on Hand (QOH) and calculate gaps in the inventory. Once you found it, you can turn gaps into RFQ/PO and send it to your vendor. OpenBOM allows you to organize this process easily and simple.
OpenBOM’s Purchase Order (PO) generation function is a vital asset for streamlining batch production. Directly utilizing data from your Bill of Materials (BOM), the feature automates the creation of a PO, specifying part numbers, descriptions, and quantities required for batch production. The PO can then be exported as a PDF or sent directly from OpenBOM, ensuring a seamless transition from order to delivery. This capability facilitates efficient tracking and management of your orders, thereby enhancing your batch production process.
6. Zip Export
While OpenBOM allows you to share data between engineers, contract manufacturers, and suppliers seamlessly and without extra effort. The OpenBOM share feature is powerful. However, for people that are “not ready” for real-time sharing, I have great news for you – Zip export.
The OpenBOM Zip Export feature is a valuable tool that enhances your data portability and sharing capabilities. It’s designed to provide you with a convenient method for extracting and exporting all your essential project data in one go. When you initiate a Zip Export in OpenBOM, the tool will automatically compile all the necessary data files associated with your Bill of Materials (BOM), including documents, CAD files, and derivatives. This compilation process results in a structured, organized ZIP file that is easy to navigate. The ZIP file will contain a folder for each BOM, sub-BOM, and Catalog in your project. Additionally, it will also include an Excel file representing the BOM or Catalog, allowing for offline access and review of your data.
This feature is incredibly beneficial for sharing information with team members, vendors, or clients who may not have direct access to OpenBOM. The ability to export an entire BOM, complete with all related attachments and data, in one ZIP file facilitates collaboration and ensures that everyone involved in a project has access to the necessary information.
Whether it’s for data backup, project handoff, or simple sharing needs, the Zip Export feature of OpenBOM is a simple yet powerful tool that can greatly enhance your data management and project collaboration capabilities.
7. Manage Revisions of Specifications
OpenBOM helps to manage files and, particularly in handling file attachments related to items and their revisions. This is achieved through an intuitive and structured system that is designed to maintain a clear record of all revisions and associated data.
When you create an item in OpenBOM, you have the option to attach any relevant files directly to that item. These files can include images, PDFs, CAD files, and any other type of document that provides valuable information about the item. The attachment process is as simple as uploading files from your computer or choosing them from a linked cloud storage service. Also, OpenBOM can upload files automatically via CAD systems.
Furthermore, OpenBOM maintains a clear and traceable link between each item and its corresponding attachments. This means that even as you revise items, the original attachments are retained and linked to the original version. When a new revision is created, you can add new attachments or update existing ones as necessary. This ensures that you always have access to the most current and relevant information for each item.
Revision control in OpenBOM provides a historical view of an item and its associated attachments. This allows you to see how an item has evolved over time and provides you with access to previous versions and their related files when needed.
Conclusion
OpenBOM provides a great spectrum of solutions and features that helps companies to manage data, streamline processes, save time, and eliminate mistakes. Each feature I described above in this article can lead you to improvement in the way you can make more money, save costs and mitigate the risks of making mistakes.
REGISTER FOR FREE and start your 14-day trial to learn how OpenBOM can help you today.
Best, Oleg
Join our newsletter to receive a weekly portion of news, articles, and tips about OpenBOM and our community.