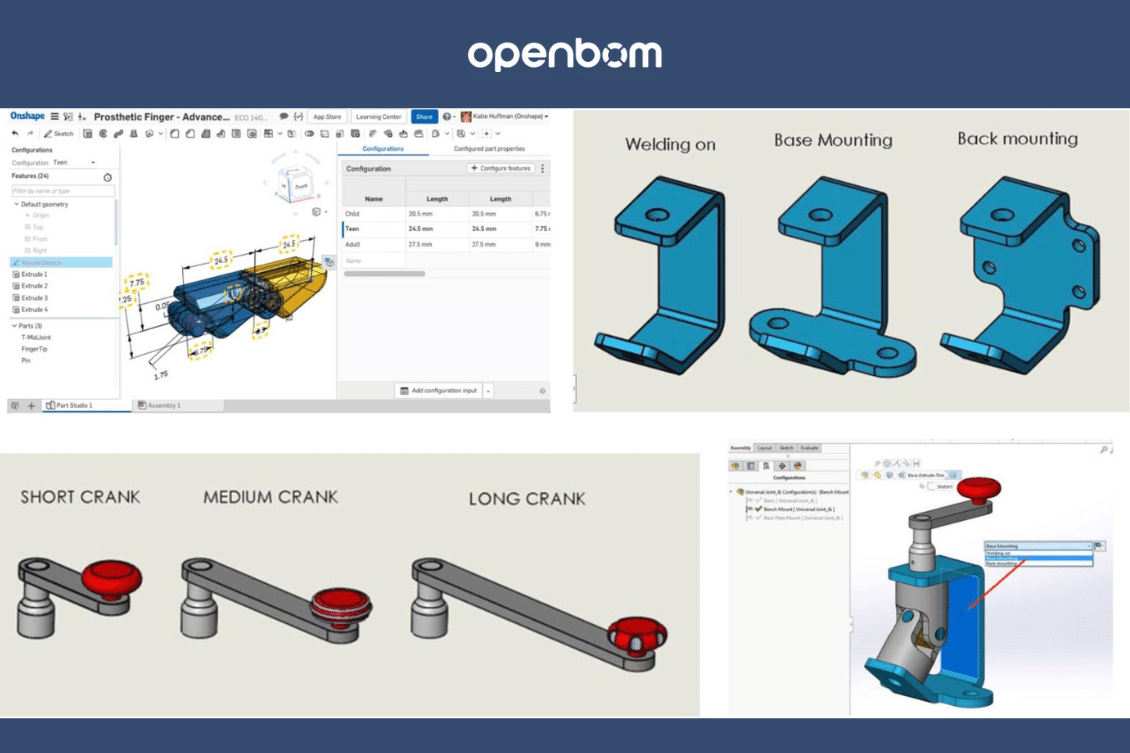
Modern product design and manufacturing involve a level of complexity that requires sophisticated tools and methods to manage. One of these complexities is the methods of design configurations, particularly in CAD systems. This article digs into the ways of handling design configurations in CAD and its interface with OpenBOM, using SOLIDWORKS as a model for our discussion.
CAD Configuration
To start with I would like to recommend you check CAD guidance about managing variants. Here are a couple of articles:
CAD (Computer-Aided Design) software, like SOLIDWORKS, PTC Onshape, and others, possesses advanced features that allow engineers to create multiple configurations of a design. Essentially, these configurations enable efficient design processes by allowing for variations of a single design.
The main motive behind configurations is to provide flexibility and efficiency in the design process.
There are two main paths an engineer can take to work with multiple design variants::
- Creating distinct configurations within a single CAD file: This method keeps multiple versions of a design in a single file, which can be selected and modified individually.
- Managing explicit designs for each separate configuration: This method involves creating separate CAD files for each design variant.
Regardless of the chosen method, it’s important that CAD users assign specific part numbers to each configuration. This step is crucial yet often overlooked by many users later on struggle with BOM creation.
Configurable and Resolved Product Structure
At a certain point, a design must be finalized, or “resolved”. This means settling on a specific configuration of the assembly with explicit part numbers.
If you’ve opted for separate designs for each configuration, your product structures are already saved in the CAD system, ready for retrieval by OpenBOM. However, if your CAD system dynamically resolves configurations, then during this “resolution” process, each configuration is crafted on-the-fly, and part numbers are assigned based on predefined CAD system settings. This dynamism offers the ability to generate multiple product structures based on different configurations.
From Design Structure to Product Structure
Transitioning from the realm of design to that of product manufacturing necessitates a shift from CAD structures to product structures, often referred to as Engineering BOMs (EBOMs). Here’s where OpenBOM comes into play. OpenBOM seamlessly retrieves the selected or resolved configuration from the CAD system, saving data for each specific configuration using its unique part number. With this information in hand, manufacturing processes can commence, and orders can be placed.
Video Demonstration
To provide a clearer understanding, we have a detailed video tutorial. In it, our expert, Pedro Branco, offers a visual guide on capturing configured structures from SOLIDWORKS into OpenBOM. This will give you a practical look at the steps and best practices involved.
Conclusion
Dealing with configurations can indeed be a daunting task. My best advice? Keep it as streamlined as possible. For many, using non-configurable design structures with explicitly set part numbers is the simplest and most straightforward method. Yet, with advancements in manufacturing and engineering services, the use of design configurations is becoming more prevalent. Thus, understanding how configuration resolution works is pivotal. It provides clarity in the transition from design to manufacturing, ensuring that your Bill of Materials (BOM) for configurable assemblies is precise and efficient.
REGISTER FOR FREE and check how OpenBOM can help you today.
Best, Oleg
Join our newsletter to receive a weekly portion of news, articles, and tips about OpenBOM and our community.