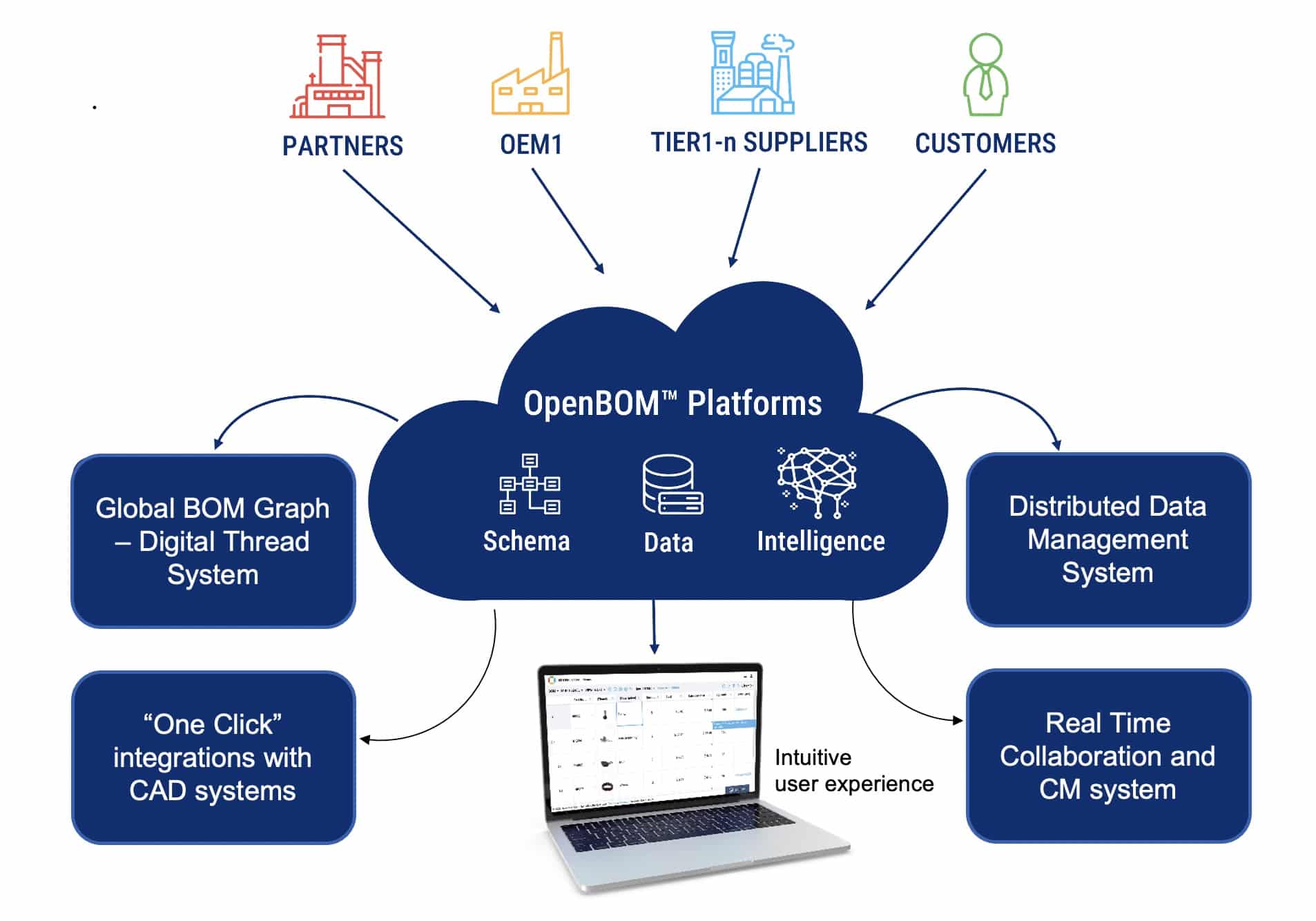
The greatest pain point for many manufacturers is the disorganization of data, as there is no single source of product records. Companies must optimize their organization’s processes using data. Data is often siloed in different physical locations — in engineering, procurement, supply chain management, and customer-facing databases such as disconnected PLM and ERP systems, spreadsheets, and email. This leads to miscommunication between engineers, contractors, and suppliers, causing mistakes, delays, excessive costs, lost orders, and other problems.
The reality of manufacturing and legacy PLM environments
The manufacturing industry is complex and integrated. The reality of many industrial companies is an extreme level of dependencies and various supply chain relationships. This brings many challenges and questions about how companies can organize communication and analyze data. The demand for more efficient data management is huge. Industrial companies are generating zettabytes of data and the ability to manage this information in a more efficient way is critical for the optimization of processes, coordination of supply chains, and helping companies to make the right decisions.
However, the reality of most manufacturing and industrial companies is legacy PLM software. Most of the existing legacy PLM software is 20+ years old and was architectured and designed back in time when SQL databases were the main element of enterprise data management. All these PLM systems are designed to perform their functions in an isolated environment and they have no capabilities to connect and communicate with other company systems. Even more, such siloes and isolation create a lot of difficulties for companies trying to analyze the potential impact of processes happening across multiple companies (eg. Suppliers and OEMs).
The answer to this problem is in creating modern multi-tenant data management systems capable to manage data and processes for multiple companies. At OpenBOM we’re building such a platform and looking at how to find the most innovative methods to help companies and people to collaborate and share information in multi-user and multi-company environments.
Collaboration in Multi-Member Environments
OpenBOM innovative technology allows multiple users to work simultaneously on the same project within OpenBOM without overwriting or corrupting data. It also ensures that each user has their own copy of the project data which can be accessed at any time. This latest development reinforces OpenBOM’s position as a leading provider of collaboration and data management tools for product developers worldwide.
Multi-Member Collaboration Patent
OpenBOM announced a patent award for multi-member collaboration methods. OpenBOM develops SaaS PDM and PLM products to help manufacturing companies solve the pervasive problems related to data management, data silos, and communication inside a company and across supply chains. OpenBOM allows users to manage data, files, and related changes across engineering, manufacturing, supply chain, contractors, and suppliers regardless of organizational and geographic boundaries.
The Invention (US Patent No. 11,315,08) enables multi-member collaboration and data management is focusing on the activity of people performing a specific set of collaborative tasks related to product structure and associated information. The method allows the control of user rights and tasks related to the contextual set of information and applies rules to define a set of associated operations and data based on each person’s (or company’s) settings.
“Manufacturing is in the midst of digital transformation. The influx of data, the distributed character of work, and the need to make better decisions faster are putting new pressure on manufacturers” says Oleg Shilovitsky, CEO of OpenBOM. “Data silos and the absence of a single source of product records are killing companies and processes. Data is often siloed in different physical locations — in engineering, procurement, supply chain management, customer-facing databases, legacy systems, and spreadsheets. This leads to miscommunication between engineers, contractors, and suppliers, causing mistakes, delays, excessive costs, lost orders, and other problems”.
“Before, we didn’t have a final BOM that was accurate or easy to share. We need a full product BOM. It was too much tribal knowledge. I absolutely love that now I can share accurate, complete BOMs with vendors, partners, customers and so many more. It is great for the team and great for the company” – Lead Engineer, Tomcar.
Conclusion
OpenBOM cloud-native PDM and PLM platforms allow data management across multiple sources and multiple companies, organizing and managing product data records, providing product data intelligence, and changing the way organizations work together. Multi-tenant data management provides a unique way to analyze data and connect people and processes. The innovation of the OpenBOM platform is to provide a collaborative network layer capable of helping industrial companies to collaborate in real time and share information. Check more about the OpenBOM patent award.
REGISTER FOR FREE and check out how OpenBOM can help you today.
Best, Oleg
Join our newsletter to receive a weekly portion of news, articles, and tips about OpenBOM and our community.