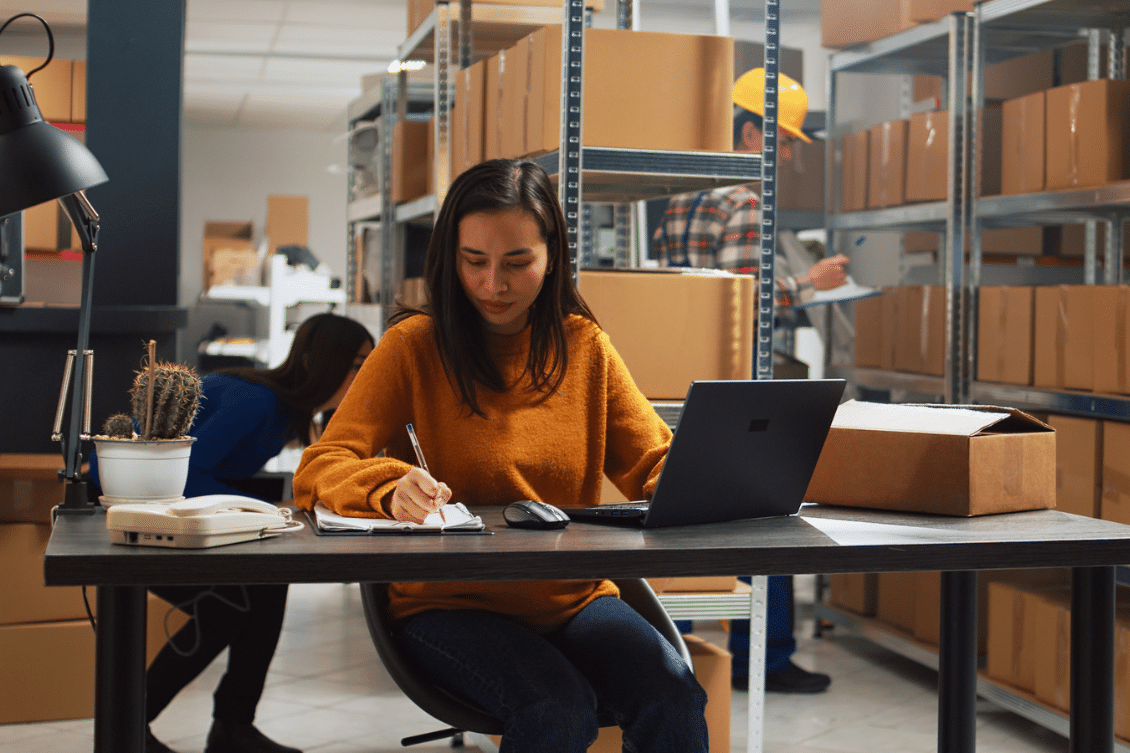
In today’s dynamic business environment, companies are looking at how to optimize processes and integrate the functions of team members and departments to achieve the desired results. Two of the most important processes in any manufacturing organization are engineering and production planning.
OpenBOM New Product Development tools integrated allow for seamless information flow and coordination of people from the early beginning of design and engineering and ending up with procurement, RFQ/PO, and inventory control.
It includes the following four stages of the product development lifecycle:
- Multi-disciplinary design including mechanical, electronic, and software
- Engineering Bill of materials planning
- Purchasing of components (both off the shelf and custom)
- Receive components, made sub-assemblies, and performing the final assembly
The main difference of OpenBOM is to provide seamless support to organize the process from the standpoint of integrated data management (items, BOMs, planning, RFQs, orders, inventory) as well as coordinating and communicating with people.
Agile New Product Development
A traditional waterfall process usually includes people responsible for each step of the overall product development process but is poorly connected and integrated. Think about multiple engineers working in MCAD, PCB design tools, and software development, and later, integrating and combining the results in a single BOM. The BOM itself is the input for procurement, which will get the data in the form of Excel or email and include everything that is needed to perform the RFQ/PO process and increase the inventory level. Later on, once shipments are received, the overall process follows the assembly, consumption of components, and inventory update (decrease for components, increase for final assembly)
OpenBOM allows companies to move from a traditional waterfall model to the agile process. It includes the capability to iterate faster with minimum effort.
OpenBOM differentiation factor describes the picture above to provide tools that create the entire data and set up collaboration and iteration in the process to make it “spin” faster and perform multiple circles of design-BOM-purchase-assembly process multiple times. The integration is key here because, without these tools, the agile process will not be feasible.
End-to-End Engineering, Inventory, Procurement
The process described above includes multiple stages and OpenBOM provides support on each of these four stages – Design, BOM, RFQ/PO, and Assembly. The system is integrated with existing engineering and enterprise tools allowing you to scale upstream and downstream when it is needed.
Four Process Steps
The following activities are effectively happening during these steps. They are covering functions of the OpenBOM system connected to different organizational roles. The key element of OpenBOM support here is the integrated fashion of operations, connection between data and people, and coordination with multiple people and departments.
Blue: Catalogs With Items, Quantity on Hand, and Vendor Information
OpenBOM’s digital catalogs function as a central repository for all product-related data, including items, their quantities, and vendor information. This feature not only standardizes data across the organization but also ensures real-time information access. These digital catalogs can be updated in real-time and shared with all stakeholders. They contain comprehensive data for each item, such as item specifications, current stock, and vendor contacts. This centralizes data management, simplifying procurement, inventory, and supplier management.
Green: BOM and Integrated Product Data
One of the key advantages of OpenBOM is its ability to integrate BOM with all product-related data. It provides a holistic view of all the elements necessary to manufacture a product, from raw materials to the final assembly. This includes data such as cost, weight, and measurements, creating an integrated and easy-to-navigate product roadmap.
Most importantly, OpenBOM supports multi-disciplinary product organization. Companies can have a holistic data set of all systems – mechanical, electronics, software, etc. No more siloed BOM in multiple systems. By utilizing the BOM and integrated product data, teams across the organization can access consistent and updated information, reducing the likelihood of errors and miscommunication.
Orange: Create Batch Order and Gap Calculation
The next phase in the digital thread is creating a batch order. The batch order is essentially a command to produce a specified number of units of a product. OpenBOM streamlines this process by allowing the batch order to be directly generated from the BOM.
Once the batch order is created, OpenBOM calculates the gap – the difference between the required and available inventory. This gap calculation assists the procurement team in understanding what materials need to be procured and in what quantity.
Red: Closing the Circle by Send/Recieve PO, and Updating Inventory
Finally, OpenBOM allows you to close the circle by sending and receiving purchase orders (POs), and updating the inventory accordingly. After the gap calculation, the procurement team can generate and send POs to the suppliers directly from the platform.
Once the goods are received, the POs are updated, and so is the inventory. This real-time updating of inventory levels assists in maintaining optimum stock levels and avoiding overstocking or stockouts.
Demo Process
In the following video, you can see a typical process covering engineering/BOM management tasks, inventory and PO planning, integration of the data, and collaboration between team members. The video describes the following commonly used steps:
- Create items and catalogs, assign vendors
- Calculate order quantities based on the bill of materials for specific product batches.
- Manage inventory of parts by controlling the quantity on hand (QOH)
- Organizing purchasing planning (Order) to provide a purchasing summary.
- Automate preparation of purchase orders to help to source parts and contract work
- Receive PO and adjust QOH on that event.
Conclusion:
OpenBOM integrates every aspect of the product lifecycle, creating a digital thread that stretches from the design and engineering phase, through inventory management, and finally to the ordering process. This holistic approach ensures that all stakeholders are working with the same, real-time information, promoting collaboration and efficiency. The outcome of this process is faster production planning, fewer errors, and performing purchasing and supply chain planning.
The process described above works well for SMB/SME companies as well as for the NPD departments of large enterprises, where OpenBOM helps to replace Excels used for NPD processes.
REGISTER FOR FREE and try all of OpenBOM’s features for 14 days with no commitment.
Best, Oleg
Join our newsletter to receive a weekly portion of news, articles, and tips about OpenBOM and our community.