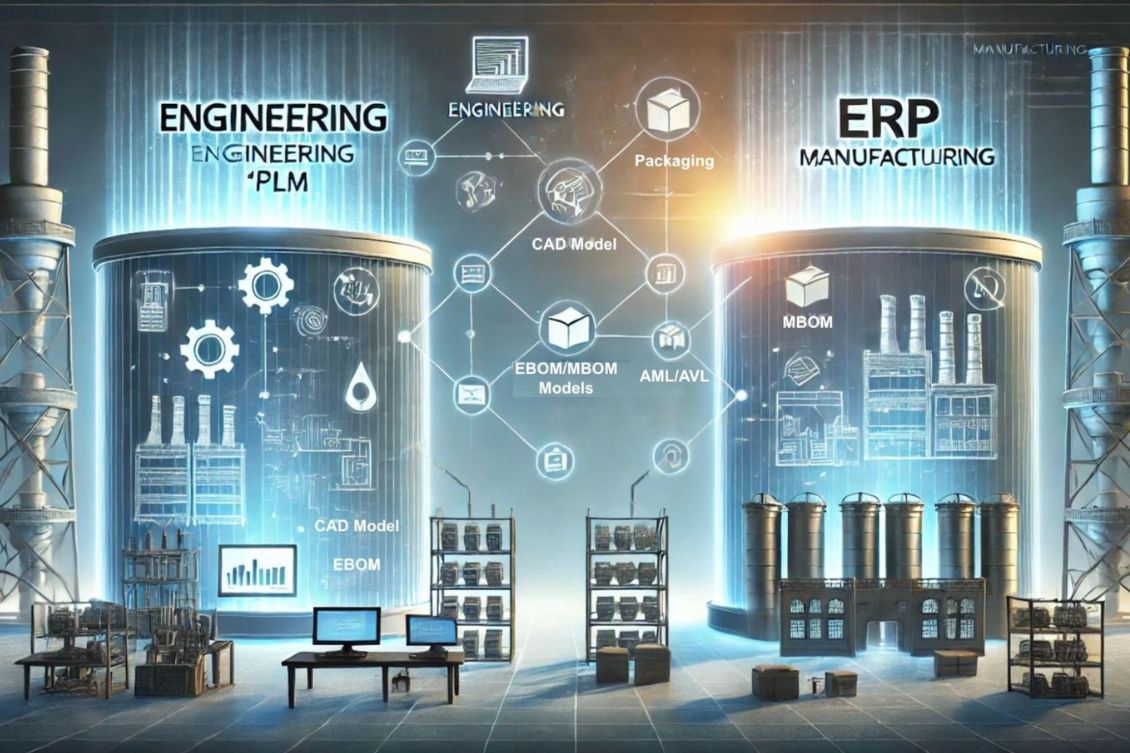
As manufacturing companies are going deep with digital transformation and process optimization, the data integration between engineering and manufacturing has become more critical. It is not a simple “through over the wall process” but an integration required to ensure data and processes are connected on both sides.
The ability to seamlessly connect CAD and ERP systems is essential for companies aiming to streamline their workflows, accelerate development, and reduce costs. With proper integration, teams can perform purchasing and procurement earlier, helping to minimize risks associated with supply chain disruptions.
At OpenBOM, we provide a wide range of solutions tailored to different customer needs. OpenBOM is flexible, providing multiple technologies and techniques to integrate data between systems.
In today’s article, we will cover OpenBOM’s CAD to ERP live demo that happened earlier this week. The demo showcases exactly how this integration can be achieved, enabling teams to work more efficiently by maintaining accurate, synchronized data across both systems.
In this comprehensive live demo, we dive into four key use cases that demonstrate how OpenBOM bridges the gap between CAD designs and ERP systems, bringing efficiency and collaboration to your product development process. We also reveal effective BOM modeling techniques to help you manage product data effortlessly.
Watch The Live Demo Video
Ready to jump ahead and watch the video. Here is the link.
Below, I share more details about integration techniques, examples and pros and cons of using each of them depending on your needs and situation.
Seamless CAD integration, BOM and Derivative Files
Before touching the integration topic, let’s speak about preparation steps. OpenBOM shines in this area by providing a seamless process to create an engineering BOM with all derivative information.
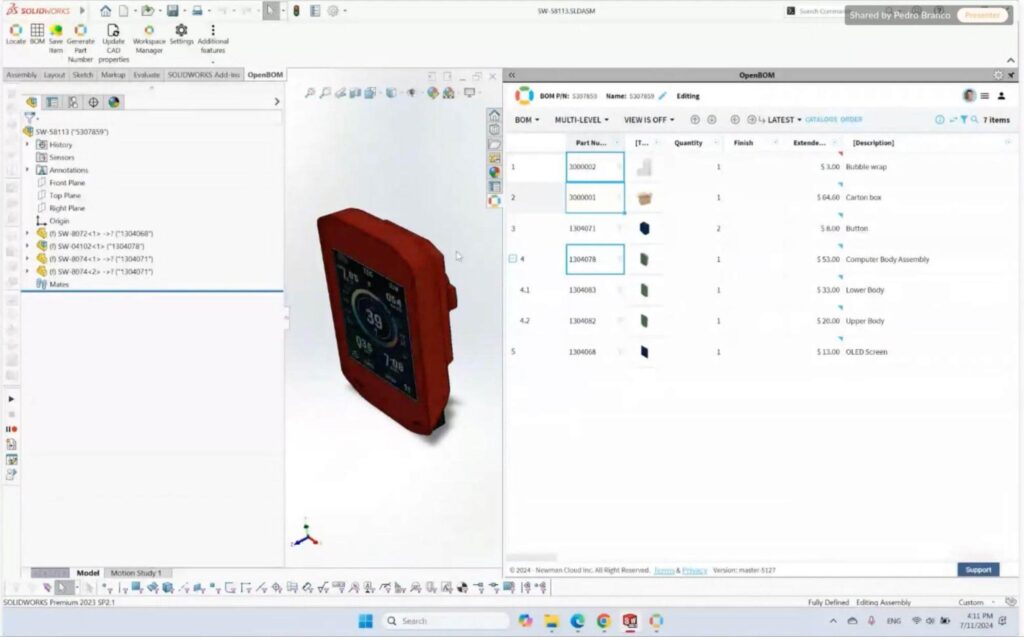
Seamless CAD integration is essential for bridging the gap between design and production, allowing for real-time data sharing and alignment between engineering and manufacturing teams. With OpenBOM’s CAD integration, design data, such as parts and assemblies, flow directly into the BOM (Bill of Materials), ensuring that the latest design information is always accessible for procurement and manufacturing without the need for manual data entry. This integration extends to derivative files, such as PDFs, STEP files, and other formats required by different departments, streamlining communication and reducing the risk of errors. By automatically generating these derivative files, OpenBOM enables teams to access all the necessary information to support sourcing, production, and quality control, ultimately driving a more efficient, synchronized development process.
Change control (ECO) is part of the product development process supported by OpenBOM. Before sending the data to ERP, it will be validated and released into immutable revisions including all data needed to connect to the manufacturing environment.
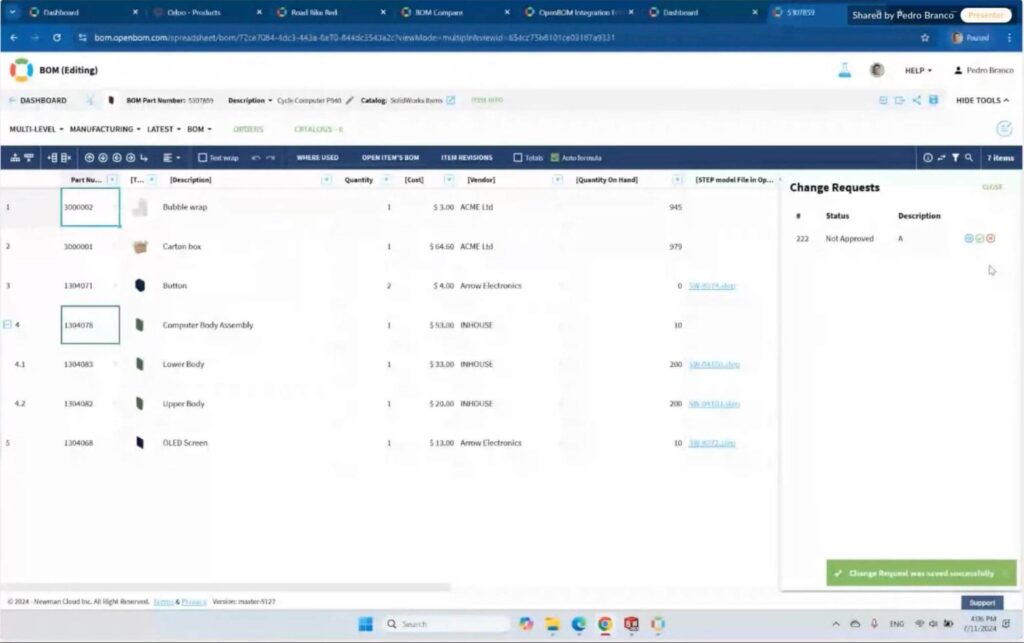
System of notifications, informs users about the need to approve the change or notifies about the approval that happened using regular email with the link.
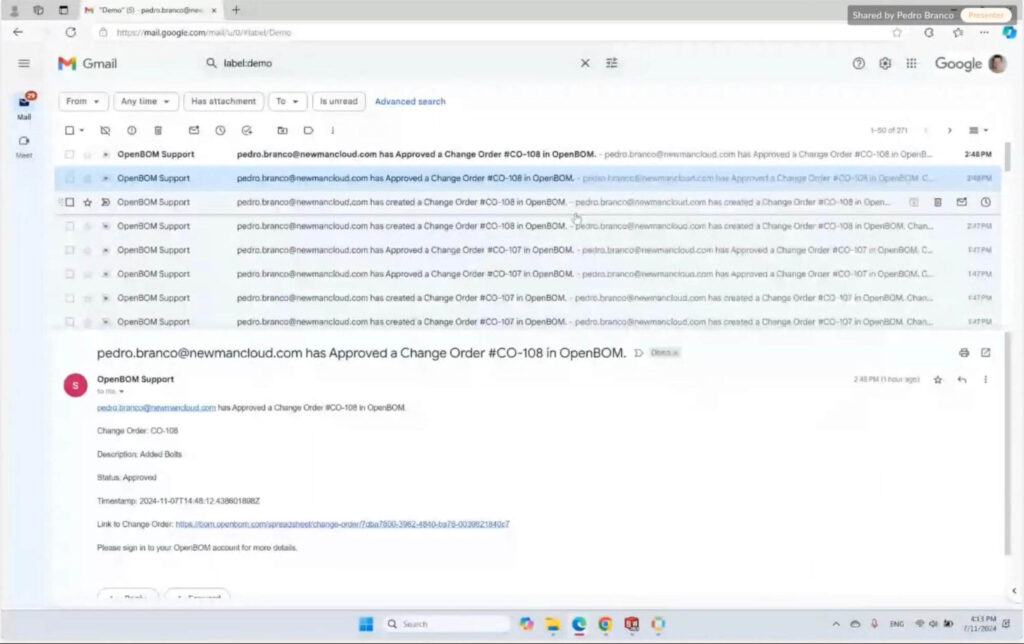
OpenBOM also allows different engineers, procurement, and planning to access the data they need via dynamically allocated views.
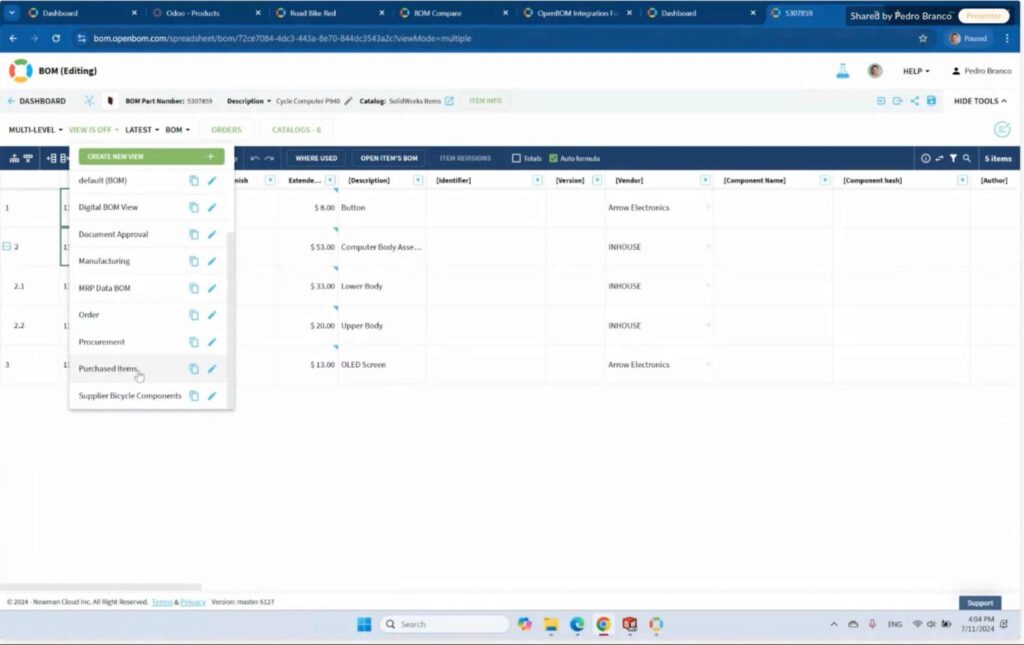
Key Use Cases in CAD to ERP Integration
Simple Out-of-the-Box Import/Export
Effortlessly transferring data between CAD and ERP systems is a fundamental requirement for smooth operations, and OpenBOM’s import/export capabilities make it simple. Our out-of-the-box tools allow users to import and export data with ease, reducing the need for manual data entry, which can be time-consuming and error-prone.
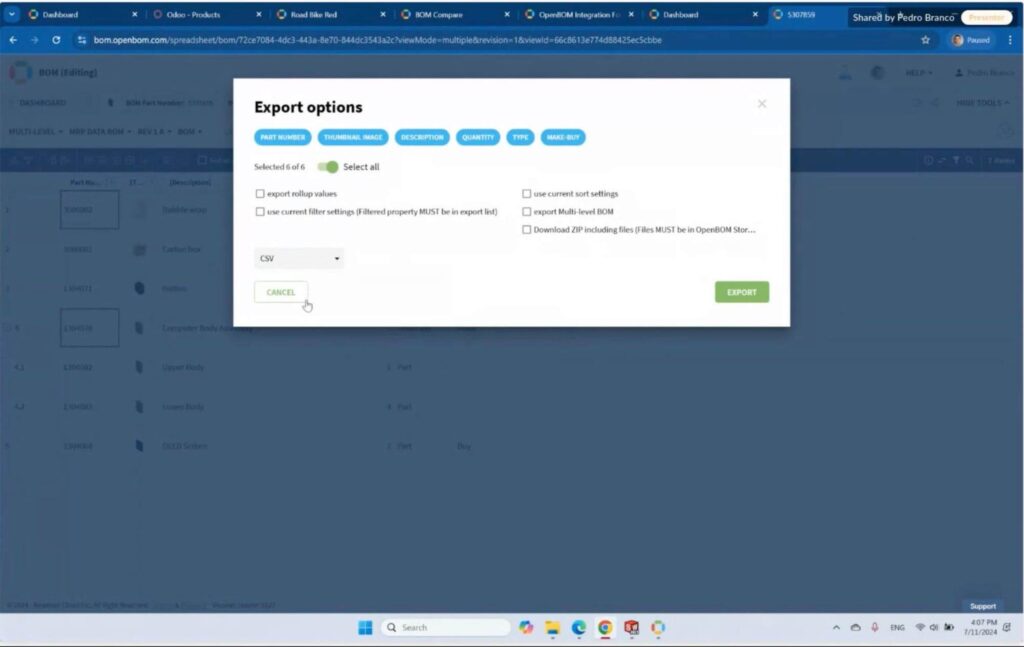
This capability not only saves time but also minimizes data discrepancies that can disrupt downstream processes.
Key Benefits:
- Streamlined data transfer between CAD and ERP
- Reduced human error through automated import/export functionality
- Time saved by eliminating redundant data entry tasks
User-Defined Commands with API Scripts
Customization is key for companies that require tailored workflows. OpenBOM’s API scripts allow users to create specific commands and automate repetitive tasks. This flexibility enables engineers and IT professionals to adapt OpenBOM to meet their unique requirements, enhancing productivity and ensuring smooth operations.
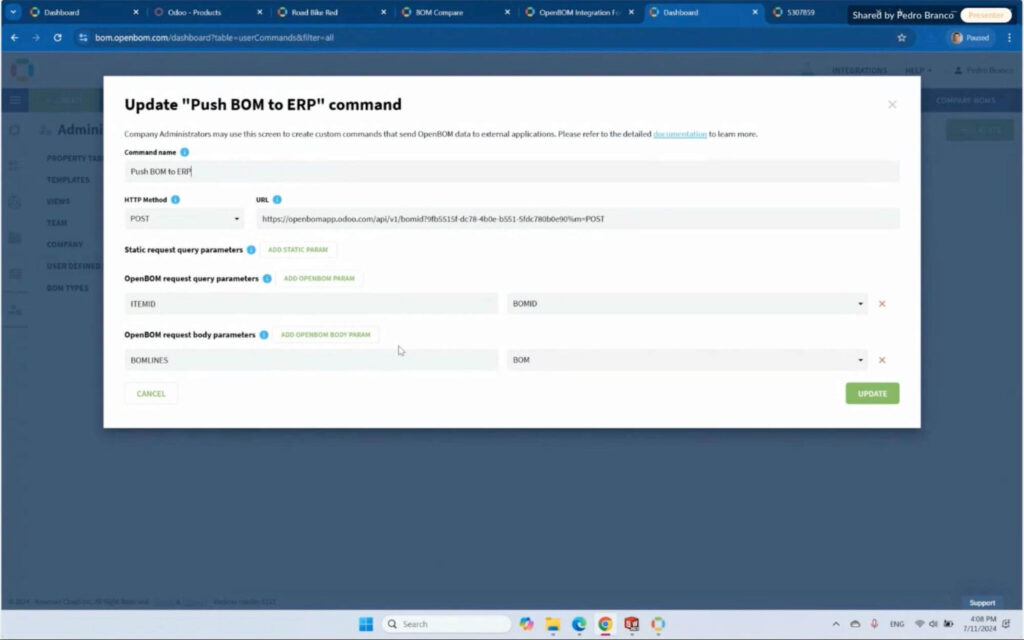
The data seamlessly integrates and transfers to the ERP system. Here is an example of ODOO integrated view.
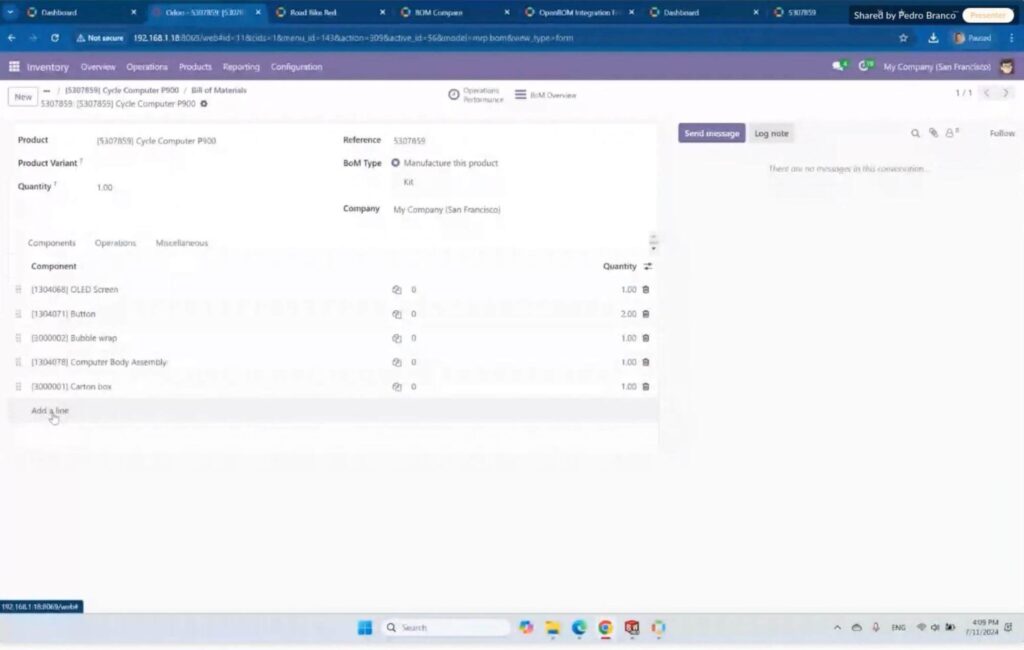
With the API, users can easily create scripts to transfer specific data or trigger automated workflows, improving process efficiency.
Key Benefits:
- Customizable workflows to suit unique project requirements
- Automation of repetitive tasks, saving time and effort
- Enhanced workflow efficiency with tailored commands
Out-of-the-Box Packaged Integrations
For many companies, setting up data integrations is a daunting task. OpenBOM offers ready-to-use integrations with popular CAD and ERP platforms, enabling seamless communication without additional development. The integration provided out of the box development by OpenBOM team (eg. Oracle Netsuite) or by OpenBOM IaaS partners (eg. vDR Nexus)
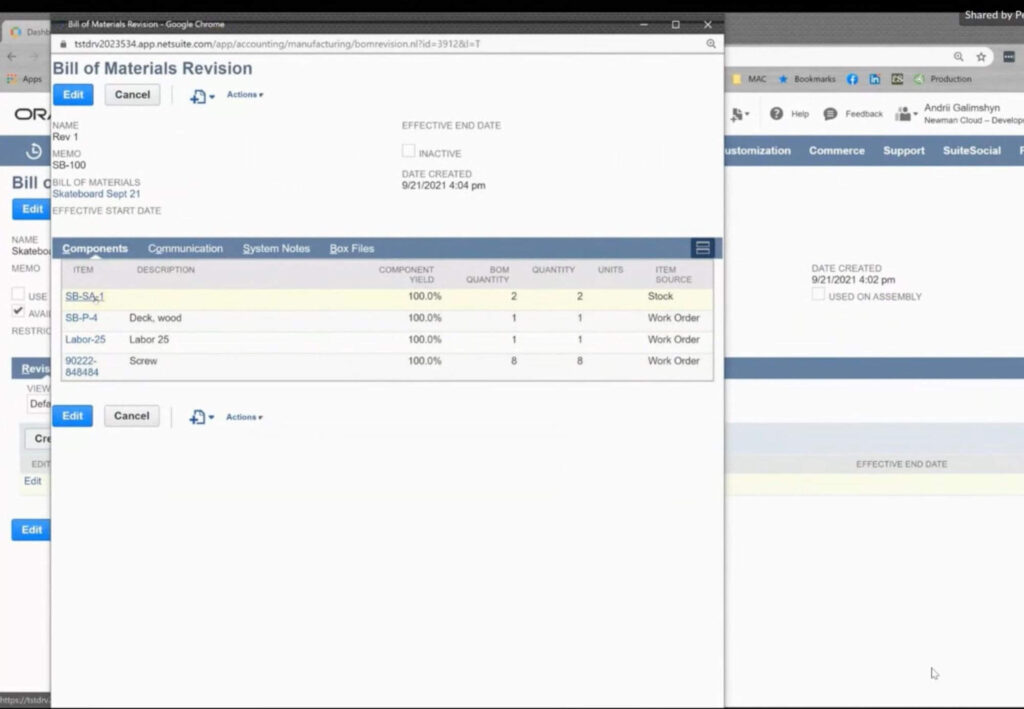
This out-of-the-box connectivity empowers companies to establish a unified data flow from design to manufacturing without heavy technical lifting.
Key Benefits:
- Quick integration setup, reducing implementation time
- Smooth communication between CAD and ERP without custom development
- Consistent data flow across departments and systems
Partners and API Solutions
OpenBOM works with a network of partners who offer specialized solutions for complex integration needs.
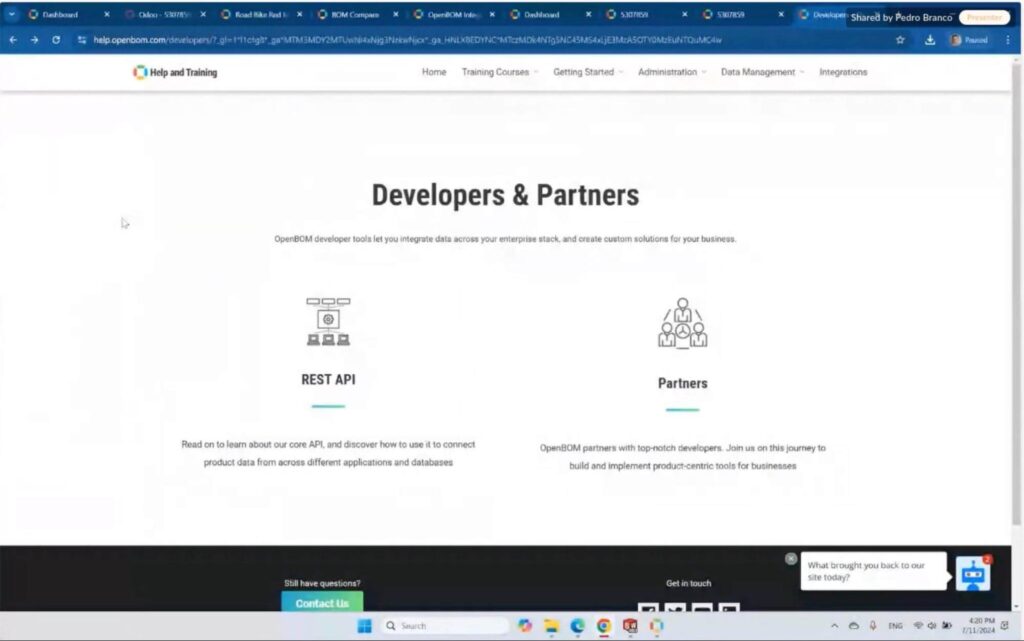
Our advanced APIs make it possible to extend OpenBOM’s capabilities and customize integrations to meet advanced, specific requirements.
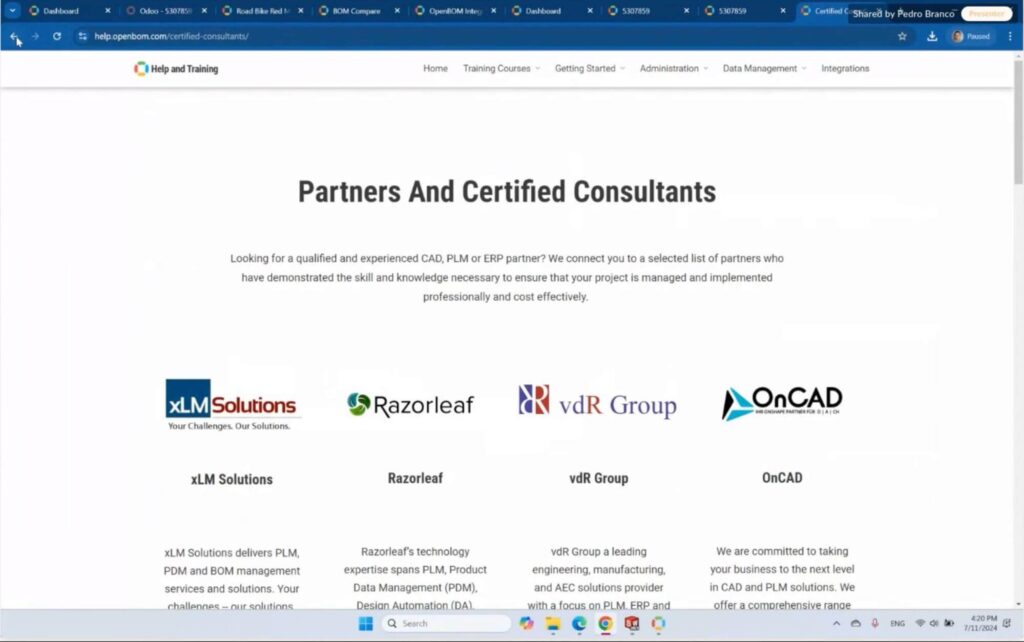
This collaborative approach empowers companies to scale and extend their integration capabilities beyond typical workflows, addressing unique manufacturing demands.
Key Benefits:
- Access to a wide range of specialized integration solutions
- Extendable API for sophisticated, custom workflows
- Increased scalability and flexibility with partner solutions
BOM Modeling Approaches – Single BOM vs Multi-View BOM
In addition to the core CAD to ERP integration use cases, OpenBOM’s demo showcases two essential BOM modeling techniques that optimize product data management across departments.
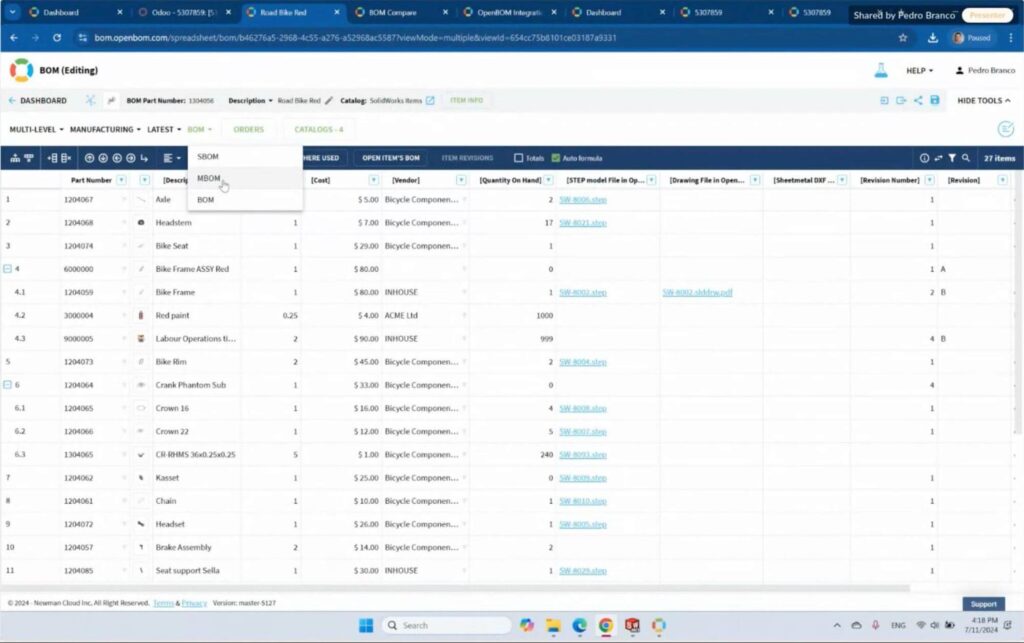
The Compare function allows you to always see the difference between both Bill of Materials.
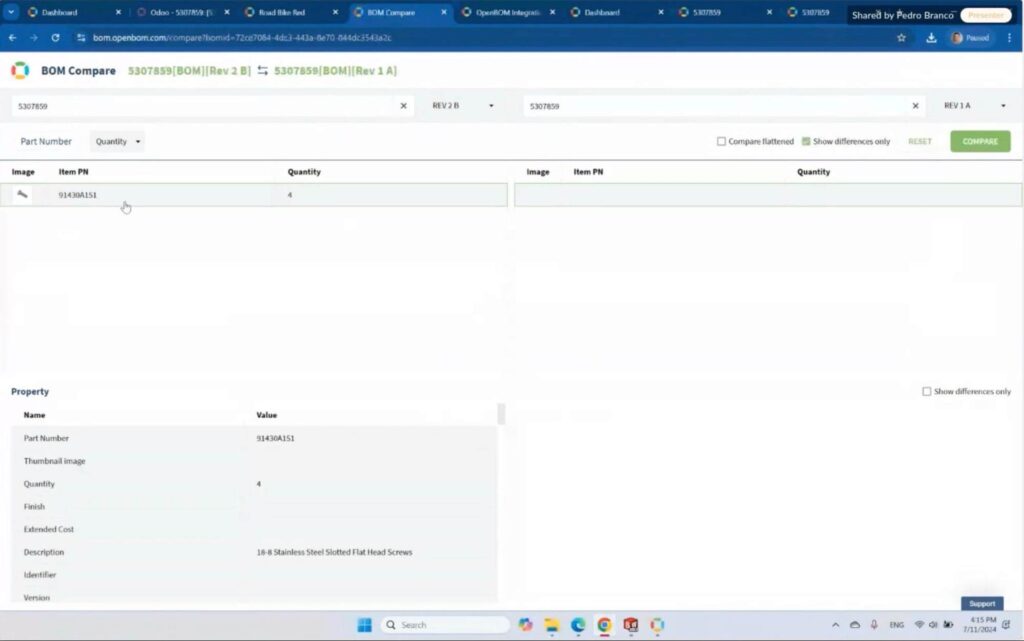
Single BOM Management
Managing all product data within a single BOM structure helps organizations track product information and maintain consistency throughout the lifecycle. This approach allows engineers, designers, and manufacturers to work from a single source of truth, simplifying updates, tracking, and communication.
Advantages:
- Centralized data management, reducing complexity
- Enhanced visibility across all lifecycle stages
- Streamlined tracking and updates
Multiple BOMs with xBOM Capabilities
For companies that need to distinguish between engineering and manufacturing BOMs, OpenBOM’s xBOM capabilities enable the management of multiple BOMs within the same system. This setup allows teams to maintain synchronized, yet distinct, BOMs for various departments, facilitating better collaboration and ensuring that each team works with the most relevant data.
Advantages:
- Enables distinct views for engineering and manufacturing BOMs
- Improves collaboration by maintaining synchronized data for each department
- Offers flexibility for companies needing varied BOM structures across teams
Who Should Watch This Demo?
The OpenBOM CAD to ERP live demo is perfect for:
- Engineers and designers looking to enhance their CAD to ERP workflows.
- Product managers aiming to improve BOM accuracy and overall process efficiency.
- IT professionals seeking robust integration solutions between CAD and ERP systems.
This demo will guide you through optimizing your BOM management, help you enhance data consistency across departments, and provide practical examples of the techniques described above.
Conclusion
As companies are moving towards transforming their operations to support digitally connected processes, these integrations connecting engineering and manufacturing silos are now becoming critical. You should think about three reasons why these integrations are necessary in a modern digital manufacturing environment: 1/ accelerate the development to adapt to customer demands and eventually sell more; 2/ save cost, by integrating data and getting timely access to all supplier, vendor, cost and procurement options; 3/ mitigate supply chain risks, by providing timely and accurate information to procurement and production planning teams.
By understanding these key use cases and BOM modeling approaches, you can unlock the full potential of your product data management with OpenBOM. With streamlined CAD to ERP integration, your organization can improve efficiency, reduce errors, and better adapt to the demands of modern manufacturing.
👍 REGISTER FOR FREE and check how OpenBOM can help you.
Best, Oleg
Join our newsletter to receive a weekly portion of news, articles, and tips about OpenBOM and our community.