![OpenBOM Design to Production Process [Advanced]](https://www.openbom.com/wp-content/uploads/2022/10/opebom-detailed-purchase-process.jpg)
The article gives you the fundamentals of the OpenBOM purchasing process. Check it out first. In this article, you will learn the details and best practices of managing Order BOM and planning to purchase. You will also learn how to manage Items data using OpenBOM catalogs and create vendor lists including Approved Vendor List (AVL).
The goal of the purchasing process is to create Purchase Orders that can be used to order standard components and sub-contractors’ work to build the product. Think about them as documents your company will be sending to vendors.
To get Purchase Orders, the entire process and data must be organized. You can refer to OpenBOM main data objects described here. These objects are representing the information model to manage items, Bill of Materials, Vendors, and purchases.
Check the top-level process looks at the diagram below. The diagram will give you an overall perspective of how data is flowing between each of these data objects. While the diagram takes you from the design to purchase order, keep in mind that the process is iterative and includes returns to BOMs, catalogs, and Order BOM as the maturity of the product is increasing. After all, manufacturing is never linear. You build an initial product, build prototypes, improve the design, fixes changes, and finally create a product description (including OpenBOM management bill of materials of the product that can be shipped.
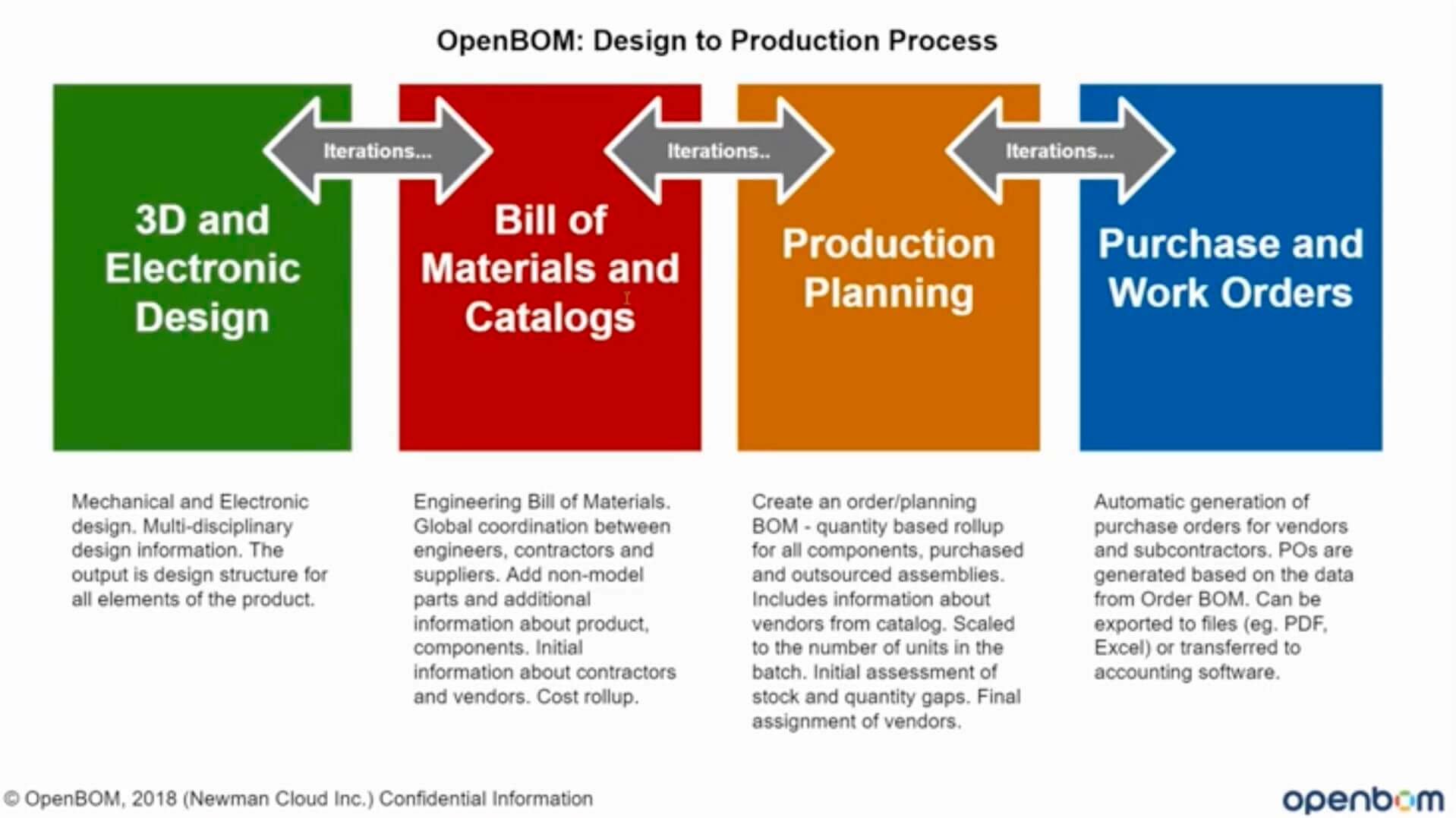
The entire process can be divided into 4 stages:
1- 3D Design and Electronic Design
2- Bill of Materials and Items (Catalogs)
3- Production planning
4- Purchase Orders.
Here are six pieces of information that need to be organized to manage the process.
1- Vendor List
A list of vendors includes all items you use in the product. In OpenBOM you can organize vendors in lists. You can create as many vendors lists as you need. Each vendor list includes basic information about the vendor (eg. number, name, address, contact information), but also can be enhanced to include any pieces of information you need to include there. Think about it as a database with the properties. OpenBOM properties can be used in Vendor lists exactly how you can extend BOM and Catalog, the same data management system is used to organize vendor data.
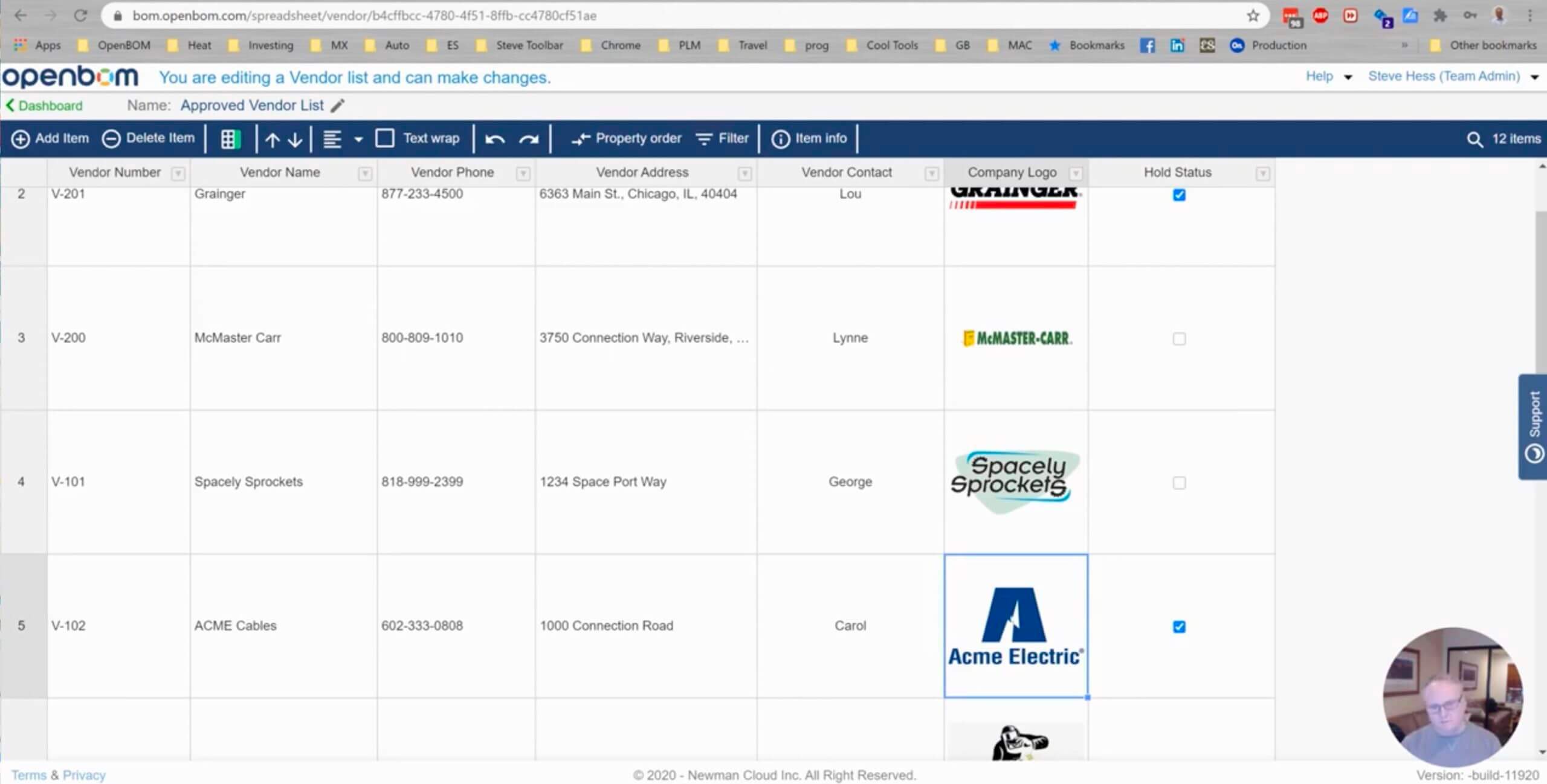
2- Catalog(s) containing all items
OpenBOM is organizing the database of all items as a set of catalogs. The catalogs are representing the classification of the items. The data model is fully flexible and you can define any data properties to items. Each catalog has a specific set of attributes, so it allows you to create a flexible classification model for your product data.
Here is an example of the catalog with properties including part number, description, image, and cost, comment, and bin location.
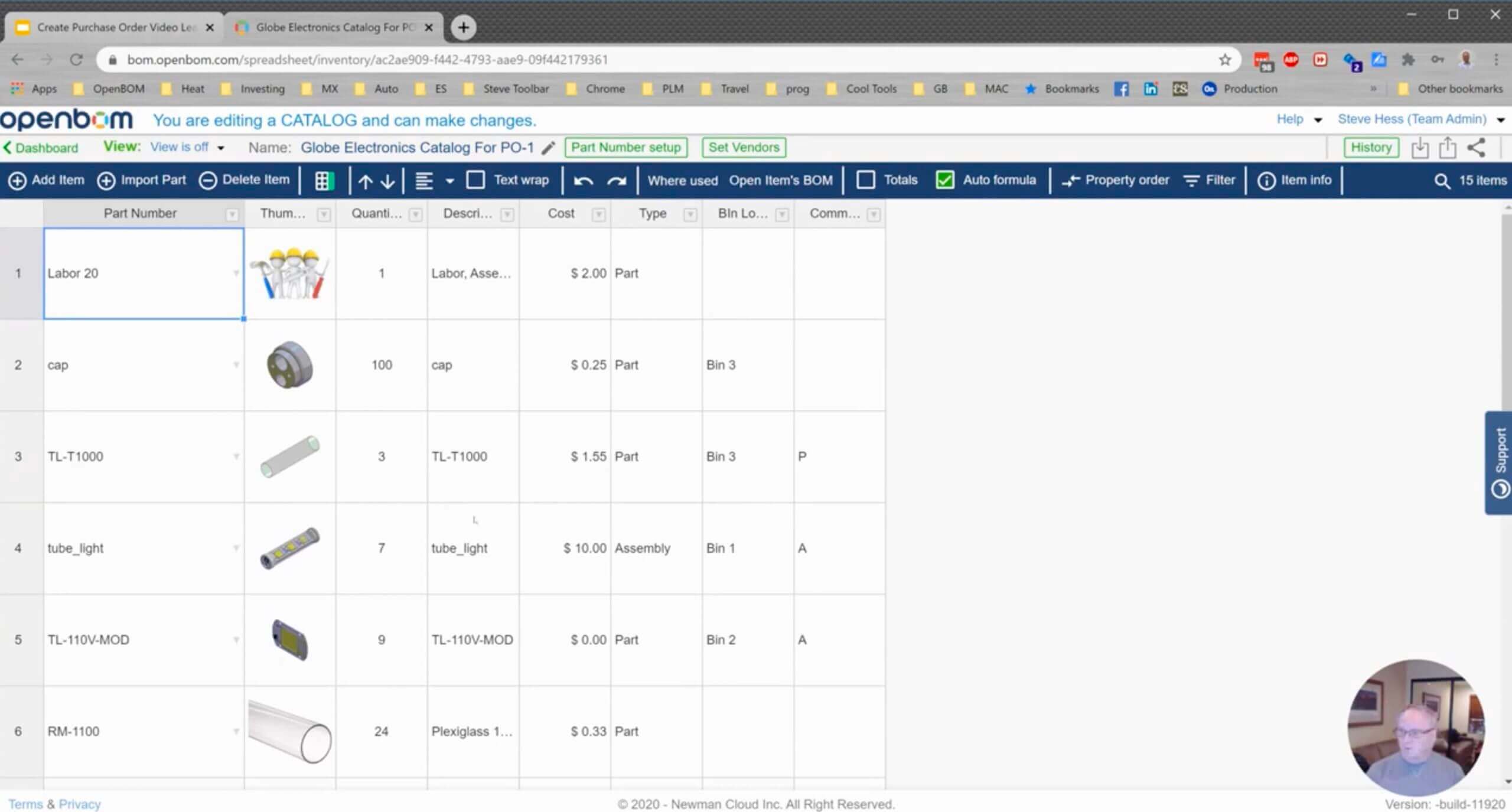
3- Vendor Assignment to All Items
The next step after organizing items in the system of catalogs, the relationship between items and vendors should be done. Each catalog can be using multiple vendor lists for such purposes. OpenBOM manages flexible relationships. Each item can have multiple vendors assigned to each part number. The information about each item can be different and depending on the vendor.
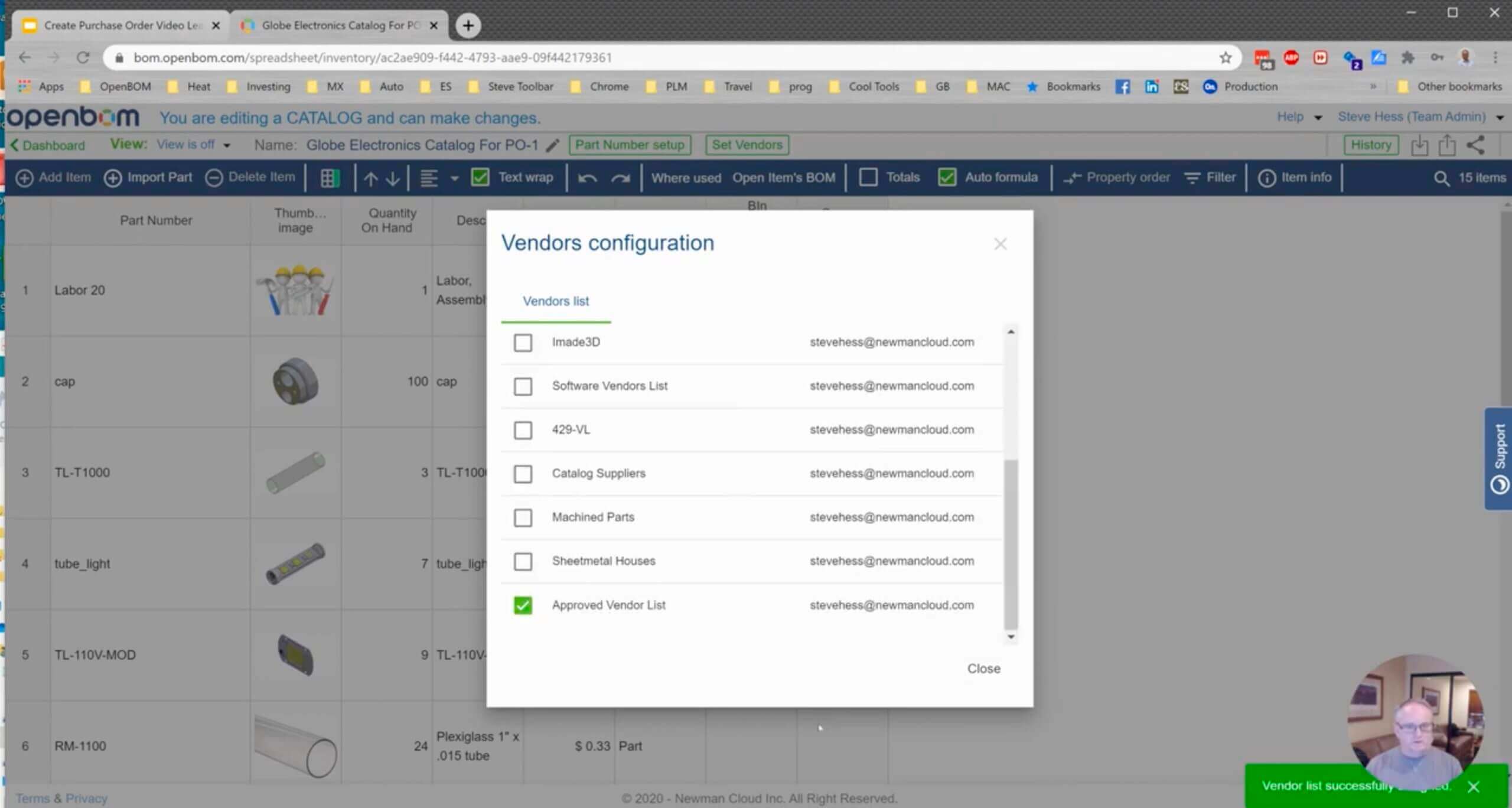
Preferred Vendor
One of the vendors will be defined as a preferred vendor and by checking preferred vendor checkbox, you define which item record information is used in all Bill of Materials. Such a model allows you the flexibility of items selection based on vendor information.
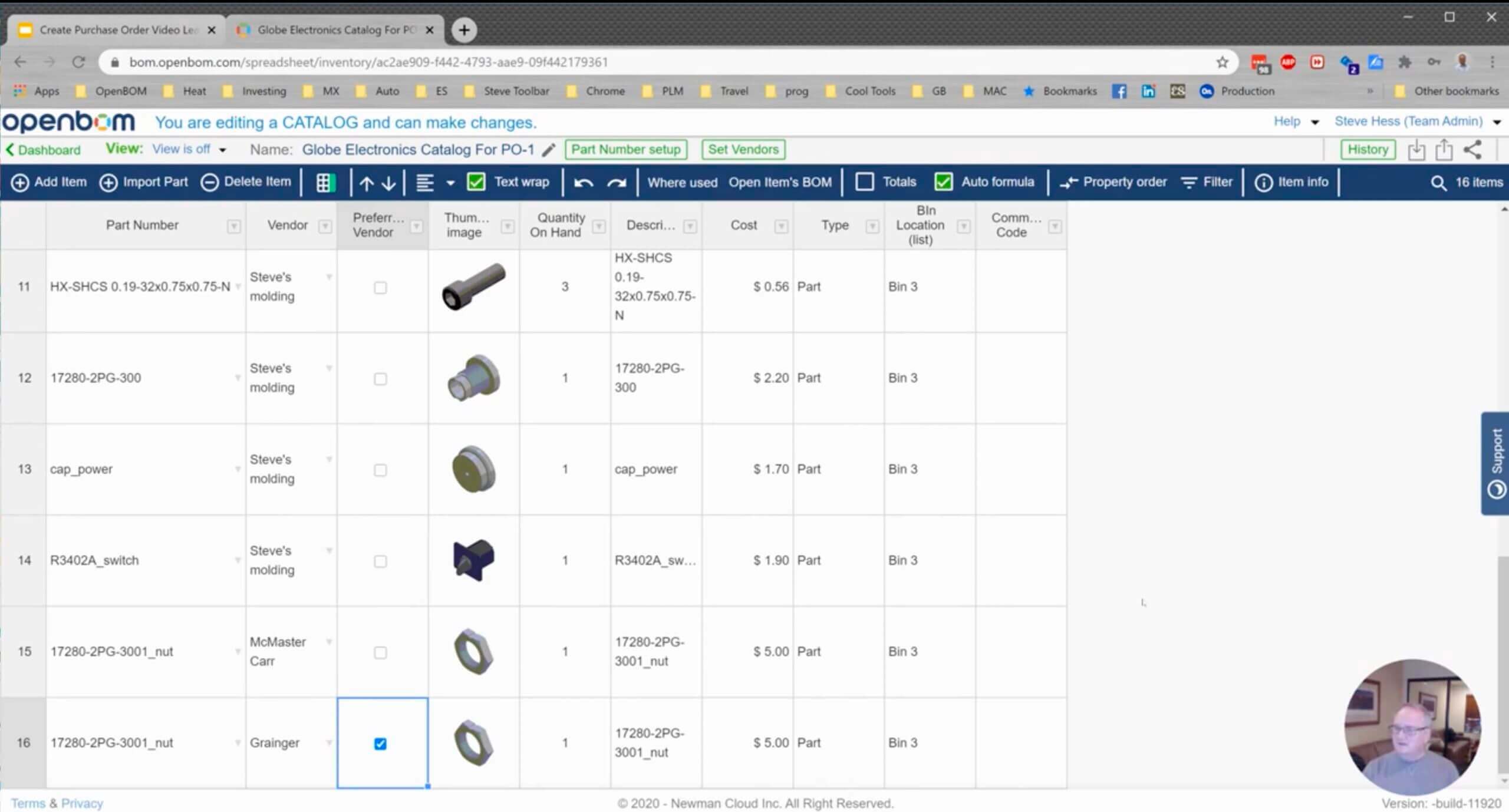
4- Quantity on Hand (QOH) and Inventor Control
Another piece of important information about the item is Quantity on Hand (QOH). You can define QOH for each item and by doing so to manage the inventory of items. Data model flexibility allows you to add more information to the item and by doing so make it useful and sufficient for simple inventory control functions in the company.
5- Creating Bill of Materials
To manage specific product data you start from the Bill of Materials. There are multiple ways to create BOM in OpenBOM. In the following example, we use manual BOM creation, but you can also create a BOM by importing Excel, Google Spreadsheet, or direct BOM import from a CAD system.
By adding items and corresponding Quantities you create a basic BOM that can be used for purchasing purposes.
OpenBOM formulas can be used to calculate and rollup cost, mass, and perform any other calculations needed for planning purposes. A typical calculation is to normalize the unit of measures for materials and items that consumed and ordered in different Units of Measure. Check out more here – Normalizing unit of measure for the ordering process.
Once you completed a bill of materials with quantities and cost information, it is ready for purchasing planning to create an Order BOM.
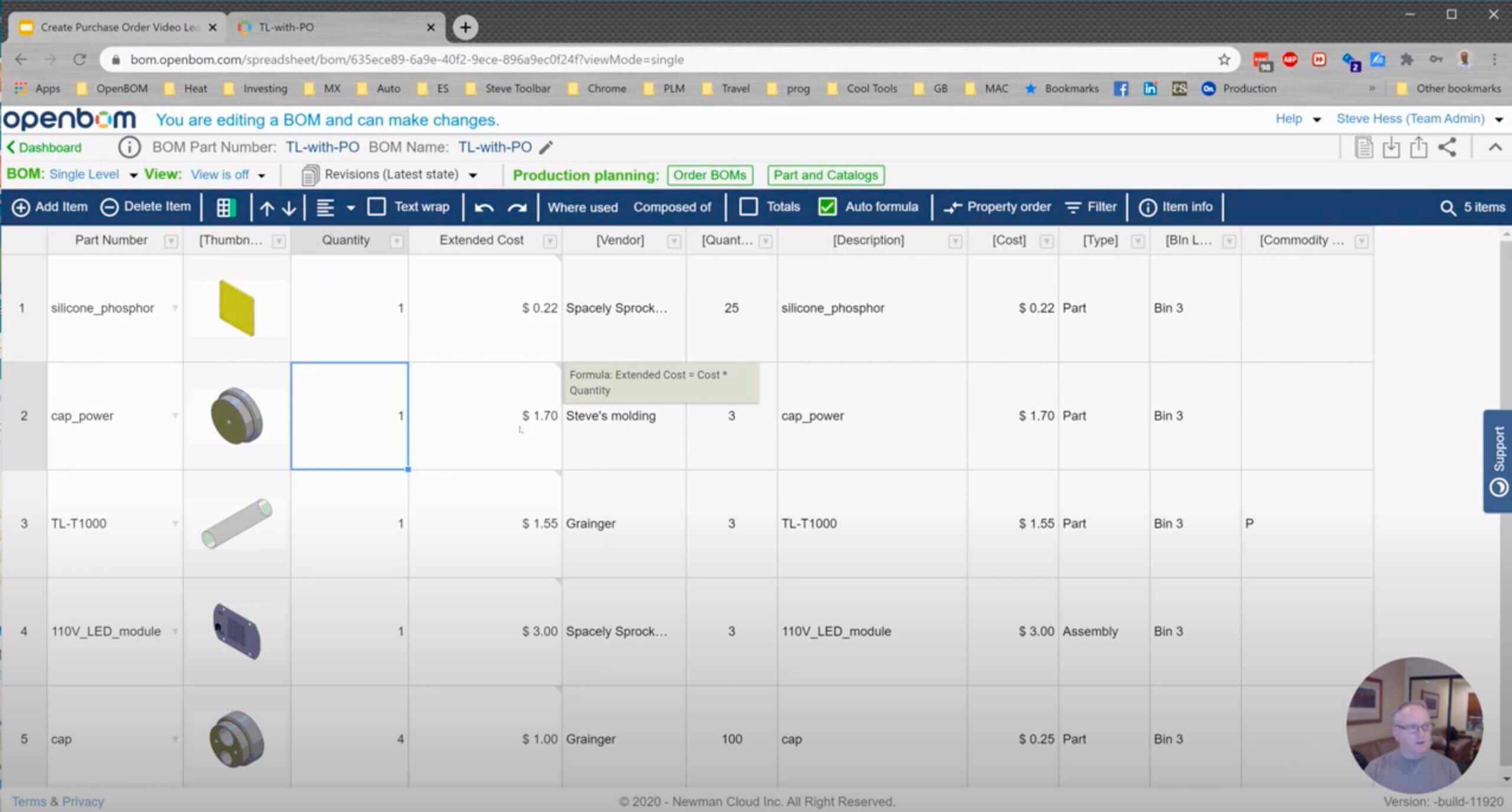
6- Creating Order BOM
Order BOM or how companies usually call it “Planning BOM” is a flattened list of assemblies and parts called to the number of units ordered for a specific customer or production planning event. OpenBOM allows you to organize it in units and you need to specify the number of units for production when you create an Order BOM.
Each Order BOM in OpenBOM called a “batch” and you can create as many as you need. The current limitation of OpenBOM is to keep a single Order BOM in the “open” status. Once the batch is “released to production”, you can create another batch.
Release to production is an event when OpenBOM takes the required quantities and decrement the QOH (quantity on hand) in the catalog. Keep in mind that it is an event that cannot be rolled back. So, if you released Order BOM to production and for some reason deleted it, you can not automatically back. Once it is done the QOH is lower and you will need to replenish stock (manually increasing Quantity on Hand) before you will be able to repeat the process.
In the picture below, you can see a typical Order BOM with all information needed for ordering process – Quantity Required, Quantity Gap, Quantity on Hand, and item information coming from BOM and catalogs.
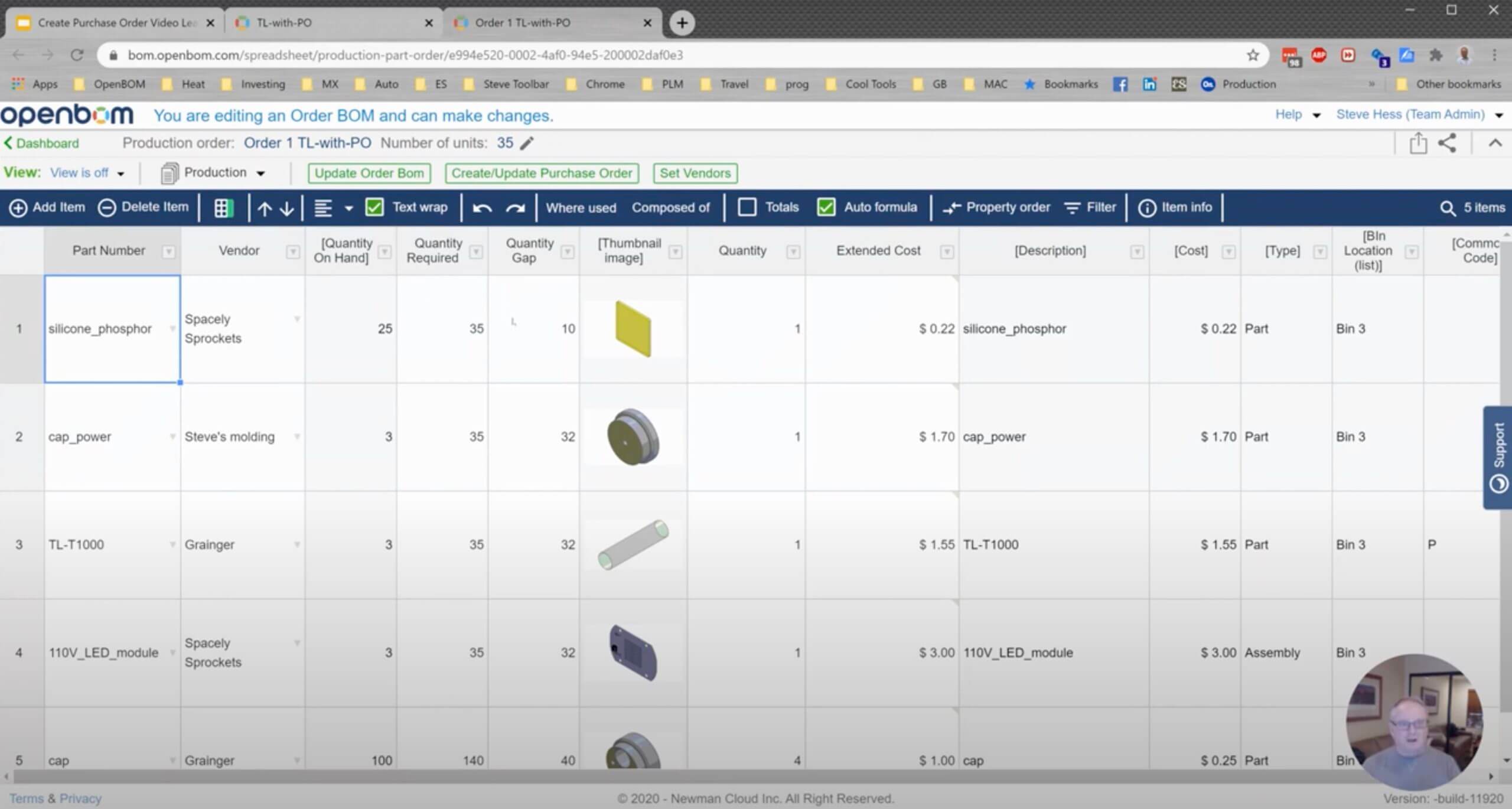
The first thing you need to do after the Order BOM is created is to ensure that all Vendor assignments will be done. An Order BOM without Vendor Assignments will not generate Purchase Orders. Once Order BOM is created, there are two processes to be managed: (1) to create purchase orders to send them to vendors or use them to direct orders from websites and catalogs; (2) maintain Order BOM updates and follow the changes in Bill of Materials – a source of Order BOM. .
By clicking on the Generate Purchase Order command, OpenBOM will generate POs and place them in the Purchase Orders dashboard.
A purchase order (PO) is a subset of the Order BOM filtered for a specific Vendor. OpenBOM generates them automatically and once they are generated you can use them to send POs to vendors or make orders. The data in each PO is synchronized with an Order BOM and each time you click on Create Purchase Orders, the content of POs will be updated with the information from Order BOM.
A good practice of working with Order BOM and Purchase order is to manage the information about purchases in Order BOM. Because of the flexible OpenBOM data model, Order BOM can be enhanced to support many additional pieces of information that needed to manage the ordering process – status, order progress, vendor information, and specific notes.
An interesting option is to use Views in Order BOM. You can achieve a view for items with a specific status or set of urgency.
Export functionality in Purchase Order is technically similar to all export functions in OpenBOM providing you the capability to select a set of properties to export, using filter and order of lines.
The outcome of the process is Purchase Order in PDF or Excel format that can be used with your vendors and online catalogs.
Check the video of an entire process here
Conclusion
OpenBOM Design to the Production process is a comprehensive way to manage a coordinated business activity including items, corresponding Bill of Materials, Batches to create an Order BOM and generating Purchase Orders. Such a process can streamline the ordering process and eliminate the need to manage multiple Excel spreadsheets and manually calculate the number of items that need to be ordered.
OpenBOM is a SaaS application, which allows you to manage this process across multiple teams and users located in different places in the world. OpenBOM allows you to bring people on the same BOM and keep the purchasing process fully integrated between engineers and people in the organization responsible for purchasing.
Check the story about how OpenBOM helped thousands of manufacturing companies to escape from Excel hell. Register to OpenBOM now to start your process of escaping Excels and Spreadsheets
Best, Oleg @ openbom dot com.
Want to learn more about PLM? Check out my Beyond PLM blog and PLM Book website
Read OpenBOM customer reviews on G2 Crowd to learn what customers are saying about OpenBOM.
Join our newsletter to receive a weekly portion of news, articles, and tips about OpenBOM and our community.