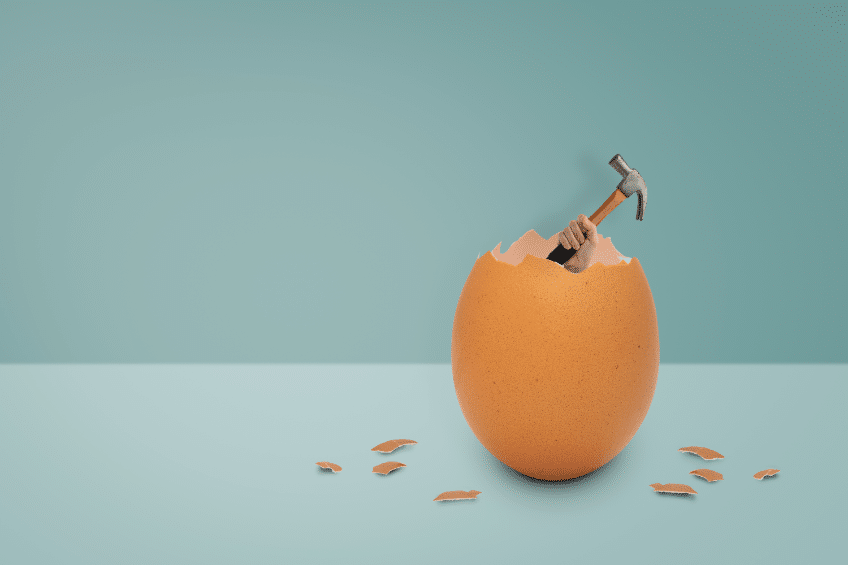
OpenBOM is a powerful, modern, cloud-native PDM & PLM tool that can help manufacturing startups streamline their businesses. PLM stands for Product Lifecycle Management, and it is a system that helps businesses manage the entire lifecycle of their products, from conception to delivery. By using OpenBOM, startups can centralize all of their product data in one place, making it easier to track and manage. In addition, OpenBOM can help businesses automate their processes and improve communication between team members.
I’m super excited to introduce a new special offering OpenBOM will provide for manufacturing startups. Working with thousands of engineers and companies, we learned about special needs and environment manufacturing startups have and how to help them..
Why Do Startups Fail to Adopt Traditional PLM Systems?
Talking to thousands of hardware entrepreneurs for the last few years, we learned about their challenges and complexity. A typical manufacturing startup is constrained by limited resources, short time, and the absence of a dedicated IT team (or even a single person) that can set up a PLM system, configure processes and maintain the operation. Therefore most startups are falling into a place where they have engineering data not organized, using spreadsheets to make their BOM analysis and purchasing components. The result is missed targets for the delivery time, cost, and technical mistakes.
While PLM vendors provide mature and expensive product lifecycle management (PLM) platforms, these established on-premise PLM solutions and their cloud-hosted variants are too expensive and too complex for a typical startup company to digest fast and start using them. As a result, product lifecycle management decision is pushed into the infinite “better future time” when they will have time and budget to invest in PLM.
This means never for most of them until one day they realize a gigantic failure resulted from not having product lifecycle management setup earlier and failing to manage data properly. It can come with communicating wrong design revisions to contractors, missing important components in the cost estimation, validating business models, or even worst, delays in regulation and compliance making a company delay their delivery time. The absence of up-to-date information kills product development and manufacturing processes. While everyone is talking about the importance of digital transformation, manufacturing startups are using stone age tools to build modern products.
OpenBOM Can Help You Save Time And Money.
Information is the foundation of every modern business. Product development is a process that requires a lot of information about products, processes, and communication to be orchestrated together. This is what product lifecycle management brings to companies. Emails and spreadsheets combined with files located in multiple places are a bad foundation to build digital products. Modern manufacturing requires product data management taking control of all information, and coordination with supply chain management efforts, and business strategy.
Even the smallest manufacturing startup is typically using dozens of contractors to deliver the product. It requires a digital foundation to manage data and connect everyone. This digital foundation includes the organization of a product value chain connecting your team with contractors and suppliers.
One of the benefits of using OpenBOM is that it can help you save time and money. By automating your processes, you can reduce the amount of time that you spend on tasks such as managing files, creating bills of materials, making cost assessments, and coordinating work with contractors and suppliers. In addition, by centralizing all of your product data in one place, you can reduce the amount of time that you spend searching for information. All of this adds up to more time that you can spend on developing your products and growing your business.
OpenBOM Can Help You Improve Communication Between Team Members
Product development is a team effort and OpenBOM can help you improve communication between team members. Mechanical, electronic, and software engineers, contractors, and suppliers, all need to work together and stay “on the same BOM” to deliver the product on time. OpenBOM collaboration capabilities allow you to share files, bills of materials, orders, and all related information, which will help your team to communicate.
By using OpenBOM, all of your team members will have access to the same product data. This means that they will be able to quickly and easily find the information they need when they need it. In addition, by using OpenBOM’s chat feature, team members can quickly communicate with each other about product issues and updates. This improved communication will lead to a more efficient workflow and fewer mistakes.
OpenBOM Can Help You Reduce Costs
In addition to saving time and improving communication, another benefit of using OpenBOM is that it can help you reduce costs. By creating a single source of truth, OpenBOM will help you to create a full digital representation of your products and tools. Cost rollup will provide you full visibility of product cost. By automating data reporting such as the creation of Bill of Materials, generation of STEP and PDF files, and sharing data with everyone who needs it, your engineers will spend less time on manual data entries and reports. This will save you money on labor costs. In addition, by creating item catalogs with inventory information, you will be able to more easily track your procurement efforts, optimize inventory levels and ensure that you are ordering components at the right time. All of this adds up to significant cost savings for your startup building process.
Conclusion
OpenBOM PLM opens the opportunity for young companies to start adopting modern business processes and manufacturing methods earlier in the process. If you are a startup business owner, then you know how important it is to streamline your operations. Thankfully, there is a tool that can help you do just that – OpenBOM PLM. By using OpenBOM PLM, you can save time and money, improve communication between team members, and reduce costs. So what are you waiting for?
REGISTER FOR FREE and start a 14-day trial to discover how OpenBOM can help you today.
Best, Oleg
Join our newsletter to receive a weekly portion of news, articles, and tips about OpenBOM and our community.