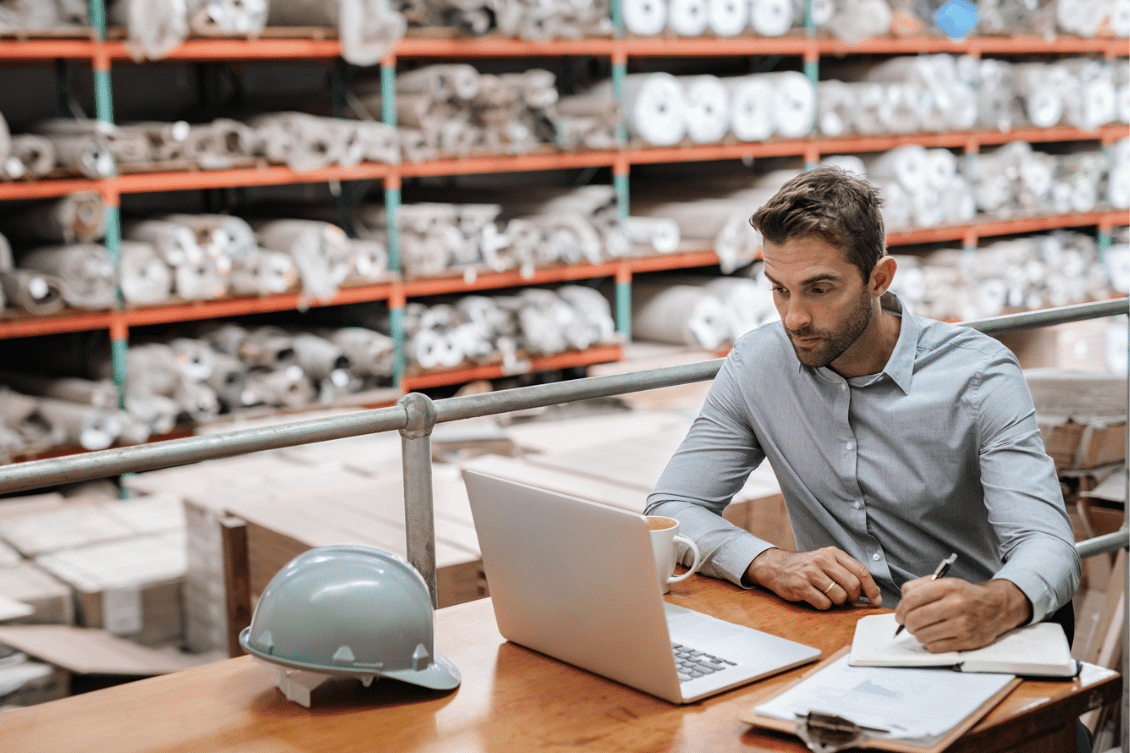
Are you an engineer or manufacturing professional struggling to manage inventory and optimize production operations? Do you need a simple, streamlined system for controlling the stock of individual parts in your facility and ordering additional components when necessary? OpenBOM’s Inventory Control feature gives manufacturing professionals an easy way to access needed resources quickly. Moreover, its sophisticated nested Bill-of-Material (nBOM) ordering process ensures that all required parts are tracked and ordered efficiently — saving you time and money!
Building machines and ordering components is not a simple task even if you build something simple. You need to create a manufacturing BOM and plan how to buy raw materials and components. Inventory management is complex even for simple products. While spreadsheets are (unfortunately) the second best tool for everything, we can see how very often engineers are trying to accomplish these tasks by using simple Excel files. Which turns out to be a devastating experience with missed components and delayed prototype or production timelines.
Supply chain management is complex and mistakes can be costly. Delayed raw materials and components will delay the entire production process. The finished product will not be shipped and your business will suffer. You need an easy way to organize the process to connect engineering BOM to the manufacturing bill of materials and connect product data from the design to the material requirements planning process.
OpenBOM gives you what you need – a connected engineering BOM (EBOM) to Order date flow and simple inventory control.
Sample – Order BOM with Sub-assembly BOM structure
In my article today, I will take you through the 5 simple steps you need to follow to perform the order in a very typical situation – ordering components and building assembly that has a sub-assembly inside.
1- BOM and Catalog
Here is our BOM hierarchy. We need to build a product.
Defining vendors for each component is important. I put “Vendor1” for nut and bolt and I use “Built” vendor to indicate that the assembly will be created “in-house”.
2- Create an Order and PO
Now I’m ready to create an order (aka planning BOM), which will include a sub-assembly (SA). The sub-assembly is needed (based on the EBOM), but we don’t need to order it.
Here is our order BOM. You can see that 2x P1 and 2x P2 are needed. We also need 2x SA, but they will be assembled in-house.
There are 2 POs created, but we will be using only one PO to order P1 and P2.
Here is the PO for P1 and P2
3- Recieve PO and Update Inventory
Once components are received, you can click on Recieve PO and the QOH (Quantity on Hand) will be updated.
You can see above that we have 2 components for both P1 and P2 and we are ready to start the build.
4- Update Order
Navigate to the order and click Update Order to ensure you don’t have any gaps. In a simple example like ours, it is clear, but in a complex order, you want to validate that gaps are zero for all components you need to purchase.
5- Release Order to Production (aka Build)
The final state is to release the order to production. When we do so, the components are consumed and the final product is built.
As you can see by the end all components QOH are zeroed and the final product is created.
Conclusion
We live in the era of manufacturing democratization. Manufacturing technologies and tools are becoming more affordable and available via different business models such as Manufacturing on Demand and Contract manufacturers where you can order products to be built online and ship them to the customers. However, planning is essential. New product development is a critical element in manufacturing and to be able to move fast and accurately is extremely important. To rely on spreadsheets to manage inventory and perform orders is a bad idea and leads to costly mistakes and delays. OpenBOM gives you an easy and simple way to manage EBOM in the Ordering process. Check this out.
REGISTER FOR FREE and start a 14-day trial to check how OpenBOM can help you today.
Best, Oleg
Join our newsletter to receive a weekly portion of news, articles, and tips about OpenBOM and our community.