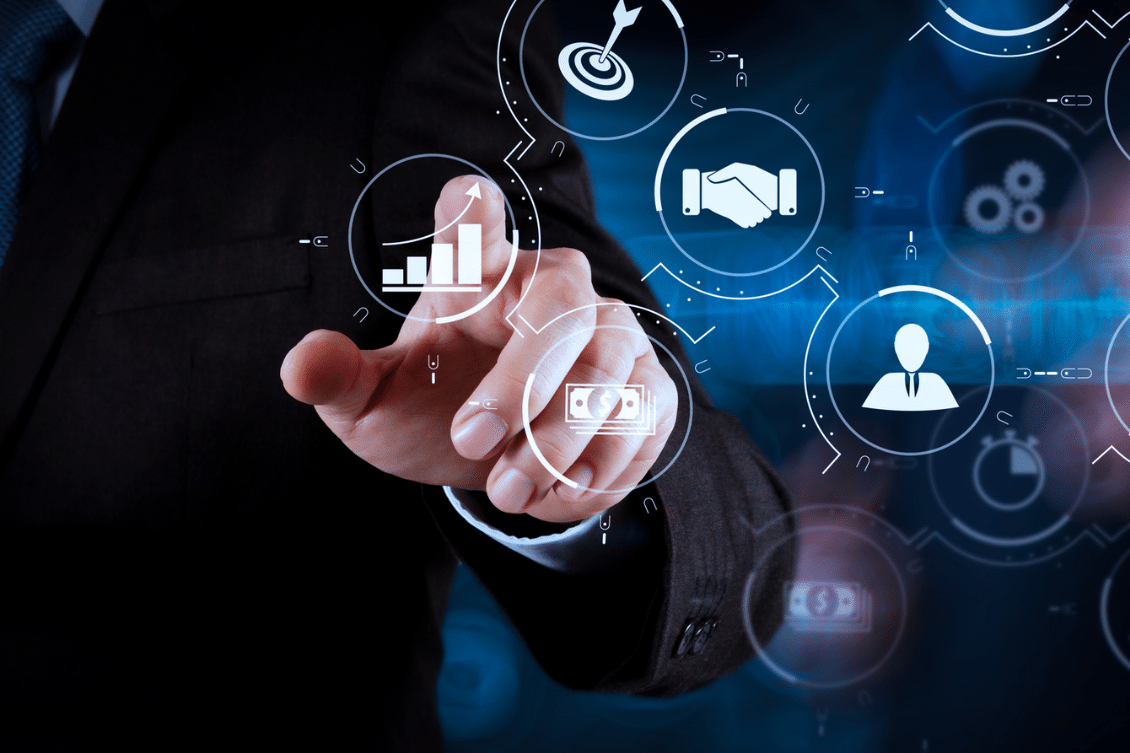
In today’s rapidly evolving product development landscape, agility in the procurement process has become more crucial than ever. It’s no longer about just bringing products to market; it’s about how swiftly and efficiently you can do it while ensuring the highest quality and cost optimization. It includes requests for quotes (RFQ), product and service specifications, pricing, and payment terms.
Every step in the product development cycle, from 3D CAD design, RFQ process, product or service specifications, and procurement to supply chain management, must be streamlined and error-free. As the digital age progresses, there’s an increasing demand for connectivity in product development, contract management, and supply chain operations. Vendor responses need to be captured, terms and conditions need to be aligned and procurement is looking at how to optimize and streamline the product for more competitive pricing.
Companies are moving from “sending a request for quote documents via email” to connect with a data approach. This demand is fueled by the need for real-time data sharing, collaboration, and transparency across all stages. The cloud not only offers accessibility but also introduces a level of dynamism that’s indispensable for modern businesses. It includes product and service specifications, all the details about materials, and the formal process of purchase approval.
In my article today, I’d like to cover how OpenBOM helps to organize and optimize the RFQ and Purchasing process. I will compare a traditional way with the OpenBOM way and bring examples.
The Traditional Way
A traditional environment includes CAD systems and a manual way to export data to create an RFQ document. Here is how it works. Managing CAD files the conventional way often resembles a complex jigsaw puzzle:
- Exporting an Excel sheet with the part list.
- Saving individual CAD files.
- Manual export of derivative files, including PDFs, STEP, and DXFs.
- Trying to correlate file names with part numbers—a painstaking task.
- Methodically organizing and collecting this data into requests for quotation of a product or service.
- Validating vendor details, descriptions, or raw materials or components and then prepping for the arduous emailing and sharing process with all other vendors to ensure competitive pricing.
To call this process tedious would be a gross understatement. You need to use the RFQ template, pull data manually, and attach detailed information. It includes a manual combination of pricing tables in case multiple vendors are involved to find the best price. It includes an analysis of differences between various options, comparing traditional suppliers and prospective suppliers. It’s fraught with potential pitfalls, highly manual, and very time-intensive. The outcome is many mistakes, the need to repeat tasks many times, and eventually long time delays with the need to update vendor-based files for qualified vendors and potential vendors and data once engineers are making changes. The overall procurement process is a mess with a lot of manual work.
The New “OpenBOM” Way
Things can be organized differently using OpenBOM. The overall landscape shifts dramatically with the usage of OpenBOM tools and the Production Planning and Purchasing process. Here is what it includes.
- Integrated CAD Add-ins: OpenBOM offers seamless CAD integration, simplifying the creation of BOMs filled with all requisite data and quantities.
- Automatic Derivative File Generation: Automated exports reduce human intervention, curbing potential errors.
- Centralized Item Management: With vendor and cost data centralized, redundancy becomes a thing of the past.
- Order Planning: Efficiently strategize and scale orders based on unit requirements.
- Automated POs and RFQs: Automated generation ensures your Purchase Orders or RFQs are always ready for swift sharing or export.
- Automatic Updates: Design modifications? OpenBOM dynamically updates all relevant data.
A new automated mechanism opens a new way to prepare a request for a proposal and optimize the overall project overview. It includes automatic file generation, cost estimation, and quick turnaround in case changes are required.
Embracing Real-time Collaboration with OpenBOM:
The new “OpenBOM” ways streamline the process and eliminate the silos that once segmented engineers, procurement teams, and vendors. The key is flexible data management and real time collaboration. With OpenBOM tools. Here is what is becoming possible.
- Stakeholders can share data in real time.
- The Agile Product Development framework is not just supported but optimized.
Think of it as trading in the linear, drawn-out waterfall processes for the speed and efficiency of agile cycles. The following picture demonstrates how it can be done.
Conclusion:
Transitioning from conventional CAD email workflows to OpenBOM opens a new way of procurement and product development—one that values efficiency, precision, and collaboration. With OpenBOM, the emphasis is not just on adopting a new tool but on refining workflows and redefining collaboration between Engineering, Procurement, and Vendors. Welcome to the future of procurement, where mistakes are minimized, processes are streamlined, and the cloud paves the way forward.
REGISTER FOR FREE and start a 14-day trial to check how OpenBOM can help you today.
Best, Oleg
Join our newsletter to receive a weekly portion of news, articles, and tips about OpenBOM and our community.