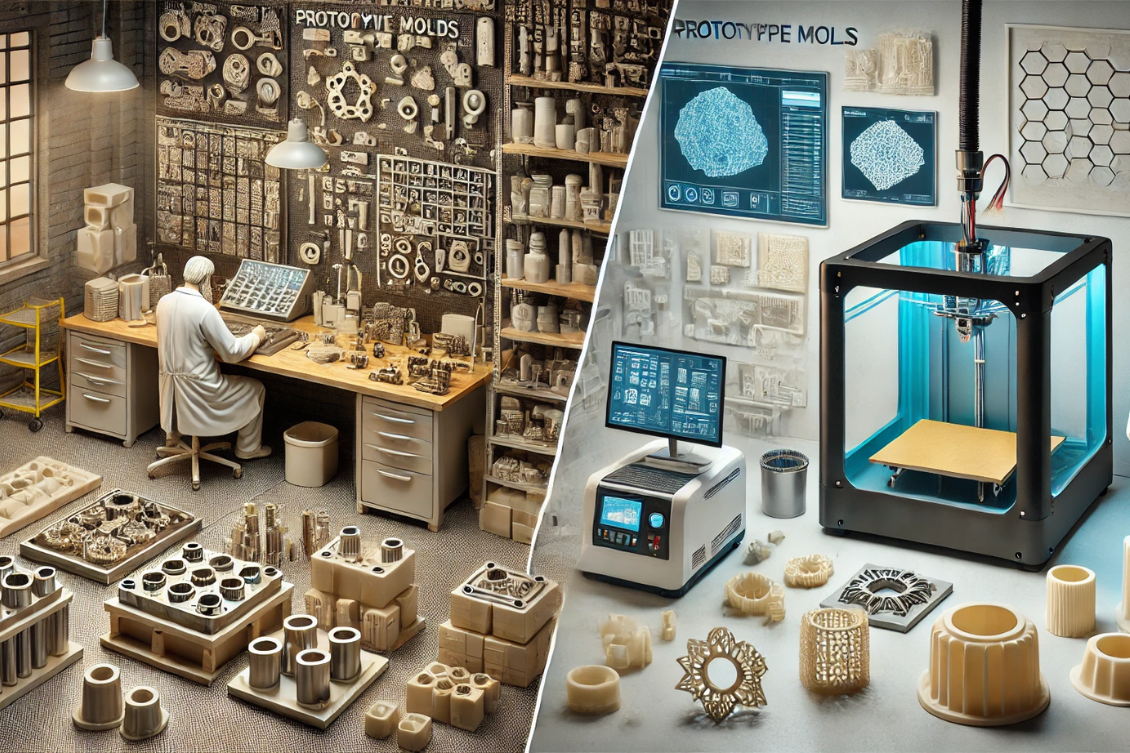
When it comes to turning ideas into plastic parts, there are two common types of prototypes: prototype molds and 3D printing. Each of these approaches offers distinct benefits depending on factors like budget, complexity, and production needs. Prototype molds, known for their precision and durability, are ideal for low-volume production, while 3D printing allows for quicker iterations and more design flexibility.
In this blog, we’ll compare these two methods, explore their differences, and look at the types of materials suited for each. Understanding how these processes work can help you make informed decisions when choosing the best method for your project.
Overview of Prototype Molds
Prototype molds are temporary molds created to produce plastic parts in small quantities, typically for testing and early-stage production. These molds are commonly used when manufacturers need to assess a part’s functionality, fit, or performance before committing to full-scale production. Unlike mass production molds, which are built for long-term use, prototype molds are designed for lower-volume runs, making them a quicker and more cost-effective solution during the development phase.
Process Overview
The process of creating prototype molds usually involves using CNC machining or casting techniques to form the mold itself. The mold is then injected with plastic to create parts that closely resemble the final product. Since the mold only needs to endure a limited number of cycles, manufacturers often opt for softer, less expensive materials like aluminum or silicone rather than the more durable steel used for mass-production tools.
While the setup time for creating a prototype mold is longer than for 3D printing, the resulting parts tend to have high dimensional accuracy, good surface finishes, and material properties that are more representative of what will be used in full-scale production.
Common Applications
Prototype molds are often chosen when manufacturers need to produce parts that closely mimic the characteristics of mass-produced items. This includes functional testing, market testing, and design validation, where the part’s strength, durability, and material performance are critical. Industries such as automotive, consumer electronics, and medical devices frequently use prototype molds to ensure their designs are production-ready.
Overview of 3D Printing for Plastic Parts
3D printing, also known as additive manufacturing, is a process where plastic parts are built layer by layer from digital designs. Unlike traditional manufacturing, which typically involves subtracting material (e.g., cutting, drilling), 3D printing adds material only where it’s needed. This technology is ideal for quickly creating prototypes, allowing designers to test form, fit, and function without the need for expensive or time-consuming molds. There are various types of 3D printing technologies used for plastic parts, including Fused Deposition Modeling (FDM), Stereolithography (SLA), and Selective Laser Sintering (SLS), each with unique advantages depending on the material and part requirements.
Process Overview
The 3D printing process begins with a digital 3D model, typically created using CAD software. This model is sliced into thin layers, and the 3D printer deposits material layer by layer to build the final part. For FDM, a plastic filament is melted and extruded to form the part, while SLA and SLS use lasers to cure resin or sinter powder into solid shapes. The beauty of 3D printing lies in its flexibility as designers can create complex geometries, intricate details, and internal structures that would be impossible or costly to achieve using traditional molding techniques.
Because there’s no need for tooling or molds, 3D printing allows for faster iterations and design changes. This makes it particularly useful for rapid prototyping and low-volume production, where speed and flexibility are critical.
Common Applications
3D printing is widely used in industries that require fast design iterations, custom parts, or complex geometries. It’s commonly employed in the automotive, aerospace, and medical fields, as well as in consumer products and education. For plastic parts, 3D printing excels in creating visual models, functional prototypes, and even end-use parts for low-volume production runs. It’s also an excellent choice for testing multiple design variations without the upfront cost and time commitment of making molds.
Key Differences Between Prototype Molds and 3D Printing
When deciding between prototype molds and 3D printing, it’s important to understand the key differences that can impact your project’s timeline, cost, and part quality. Both methods have distinct advantages and limitations depending on factors such as production speed, part complexity, surface finish, and material properties.
Production Speed
Production speed varies significantly between prototype molds and 3D printing. Prototype molds require longer setup times because of the mold fabrication process, which involves machining or casting the mold before it can be used for part production. However, once the mold is made, parts can be produced relatively quickly in batches.
In contrast, 3D printing allows for faster initial part creation since no tooling or mold setup is required. A design can be printed almost immediately, making it ideal for rapid prototyping and quick iterations. However, for large quantities, 3D printing can be slower as it produces parts one layer at a time.
Cost
Prototype molds tend to have a higher upfront cost due to the need to create the mold itself. This investment can be justified when producing multiple parts, as the cost per unit decreases significantly after the mold is made. For low-volume production, this can be cost-effective, but it may become expensive if frequent design changes are required, as a new mold would need to be made for each iteration.
On the other hand, 3D printing has lower initial costs since no molds are needed. The cost per part remains relatively constant regardless of the quantity, making it a better option for one-off prototypes or small production runs. However, as production volumes increase, 3D printing can become less economical compared to molding, especially when considering material and time costs.
Part Complexity
3D printing excels in producing highly complex geometries that would be difficult or impossible to achieve with traditional molding methods. Intricate designs with undercuts, internal cavities, and fine details can be easily printed without the limitations imposed by mold design. This makes 3D printing ideal for experimental or intricate parts.
Prototype molds, however, are more restricted in terms of complexity. Molds must be designed to allow for part release, which can limit design freedom. Complex geometries may require expensive multi-part molds or special techniques, adding to the overall cost and time.
Surface Finish and Precision
Prototype molds generally produce parts with superior surface finishes and higher dimensional accuracy. Since the molding process involves pressing molten plastic into a cavity, the resulting parts tend to have smooth surfaces and consistent dimensions, closely resembling the final production versions.
3D printing parts may have visible layer lines, particularly with FDM technology, and often require post-processing to achieve a smoother finish. While technologies like SLA and SLS offer better surface quality, they still may not match the precision and finish of parts produced with a mold.
Durability and Material Properties
Parts made using prototype molds typically offer better mechanical properties since the plastic used is often closer to that used in full-scale production. Molded parts can be made from a wide variety of plastics, ensuring strength, flexibility, and durability that align with production goals.
3D printed parts, while improving in material options, may not always match the strength and durability of molded parts. FDM parts, in particular, can have weaker mechanical properties due to the layered construction, which may lead to weaker bonds between layers. However, advanced 3D printing technologies like SLS and SLA offer stronger, more durable parts, though they may still be limited in material choice compared to molding.
When to Use Prototype Molds vs. 3D Printing
Determining when to use prototype molds versus 3D printing is essential for optimizing your product development process. Each method offers unique advantages tailored to different project needs, making it crucial to assess factors such as production volume, design flexibility, and cost. In this section, we will explore the scenarios in which one approach may be more beneficial than the other, helping you make informed decisions based on your specific requirements and objectives. Whether you’re looking to rapidly prototype a concept or prepare for higher-volume production, understanding these distinctions will guide you toward the most effective solution for your project.
Volume Considerations
Prototype Molds are most advantageous for low- to medium-volume production runs. If you need to produce anywhere from a few dozen to several thousand parts, molds offer cost efficiency after the initial setup. Once the mold is created, producing each part is relatively quick and affordable, making it a smart choice for scaling up production or making pre-production runs for testing and validation.
3D Printing excels in rapid prototyping and small batch production. It’s ideal for creating one-off prototypes or small batches (usually up to a few dozen parts). For low-volume runs, 3D printing can be more cost-effective because there’s no need for expensive tooling or molds. It’s also well-suited for projects that require frequent design changes, as printing a new part is much faster than modifying or creating a new mold.
Design Iterations
3D Printing is the clear choice when frequent design iterations are needed. Because there is no tooling involved, changes can be made quickly by simply adjusting the digital design and reprinting the part. This flexibility is especially important in the early stages of product development when designs are still evolving and being tested.
Prototype Molds, on the other hand, are less adaptable to design changes. Once a mold is fabricated, modifying it to reflect a new design can be expensive and time-consuming. Each mold change requires additional machining or a complete rebuild, leading to higher costs and delays. Therefore, molds are better suited for designs that are close to finalization, where only minor tweaks, if any, are expected.
Cost and Time Trade-offs
3D Printing offers significant advantages in terms of speed and initial cost. It allows designers to go from concept to physical prototype in a matter of hours or days, with minimal upfront investment. However, 3D printing can become cost-prohibitive for larger quantities due to the longer production time per part. Additionally, depending on the technology and material used, printed parts may not always meet the durability and performance requirements of the final product.
Prototype Molds, while more expensive to create, become more cost-efficient for higher volumes. The higher upfront cost of mold fabrication is offset by lower per-part costs in production, making it a better choice for projects where part performance, surface finish, and material properties are critical. Once the mold is ready, the time to produce each part is much shorter than 3D printing, making it ideal for scaling up production after initial prototyping.
Conclusion
Both prototype molds and 3D printing serve valuable roles in the product development landscape, each with its own set of advantages and limitations. Prototype molds are best suited for projects that require durability, high-quality surface finishes, and cost-effective production at larger volumes, making them ideal for the later stages of product development.
Conversely, 3D printing excels in rapid prototyping and small batch production, offering unmatched flexibility for design iterations and faster turnaround times. By carefully considering factors such as production volume, design complexity, and cost-efficiency, you can determine the most appropriate method for your specific needs. Ultimately, leveraging the strengths of both approaches can enhance your development process, leading to innovative products that meet market demands effectively.
By: Jared Haw
Join our newsletter to receive a weekly portion of news, articles, and tips about OpenBOM and our community.