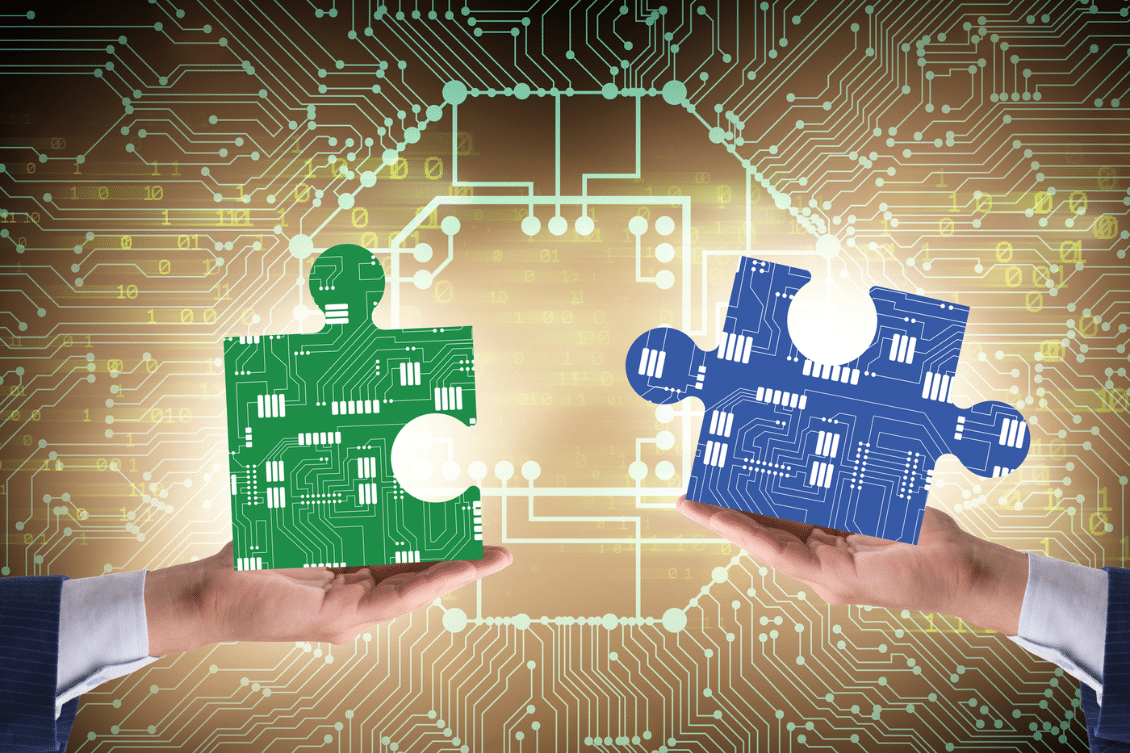
These days everyone wants to accelerate their activities. The speed of the business is growing. We need to have a faster response and react faster to problems and challenges. And one of the outcomes in the industrial and manufacturing world is the need to develop faster. An old product’s lifecycle is replaced by the demand to build products faster.
There are many reasons why speed is a critical factor in new product development and engineering. Here are some of them: (1) the faster a product can be developed, the sooner it can be brought to market, giving a company a competitive advantage over its rivals; (2) speed can help reduce costs by minimizing the time and resources required to develop a product. (3) speed can also help companies respond more quickly to changes in the marketplace, customer needs, or technological advancements.
Furthermore, by accelerating the development process, engineers and designers can identify and correct issues more quickly, leading to a higher-quality end product. Ultimately, speed is crucial in new product development and engineering activity because it can make the difference between success and failure in today’s fast-paced business environment.
Need More Speed – Where is the problem?
So, we need more speed in engineering. There are many reasons for that – the market is changing, complexity is growing and demanding more efficiency, cost pressure is growing, and everyday life is demanding faster innovation.
Data management is a fundamental reason why engineering is slowing down. Here is an example of how bad data management creates friction and slows down engineering departments or groups working on new product development.
Despite conventional thoughts that CAD (and design) is where innovation happens, it is not the entire truth. Of course, the company will have to use CAD systems to design parts, but for most companies, product development is not starting with engineers opening their CAD system to design parts. It might be the case for a very small number of new hard tech companies. But even for them, product development is starting from understanding what you have already done, existing products, existing product lines, component libraries, and existing component base that can be re-used, re-purposed, and re-combined to create a new product.
And this is where the first problem is. To get access to all information about the product, existing components, dependencies, etc., companies need to have very good data management. I’ve heard the terms design items or engineering items many times. This is part of product lifecycle management and this data management capability should support the collaborative effort of engineers to build new products.
Unfortunately, for many companies, such a product lifecycle management effort either doesn’t exist or is barely available for engineers. You can see how the engineering department cares about the management of CAD file versions, but that’s where most of the traditional engineering data management methods end. Data might be located in ERP and PLM systems. But these systems are usually not available (for engineering) or too complex to use for new product development and engineers genuinely hate them.
And this is where the problem begins. In engineering teams, a fundamental source of friction can be the management of design items. Every product development cycle involves a complex set of design data, such as CAD models, drawings, electrical schematics, purchase requests, engineering change orders, and reports. Each design item has specific properties, such as item number, revision, lifecycle status, and cost, and can be associated with other items. Items can have a relationship structure, where they can be parents or children of other items, forming a bill of materials (BOM).
But the data is not available in easy form. For production, companies are using ERP and legacy PLM systems. They manage inventory, supplier orders, costs, effectiveness, and work orders. PLM systems are managing CAD files. Both systems are either not available for engineers or too complex or not collaborative enough or altogether during the early product development stages.
A typical approach Engineering is taking (at the best) is to dump all data into Excel and start working using this Excel (or other spreadsheets) data to create a new product data structure , estimating cost, managing prototype inventory, coordinating suppliers and contractors. And this is extremely inefficient and laborious. This is why engineers need to have new systems to help them with data management, collaboration, engagement and intelligence.
From PLM Database To Knowledge Graphs
Efficient item and product data management are crucial for engineering teams to optimize their processes and speed up product development. Without a centralized system that defines items, especially in the early design stages, engineering teams can struggle to make good and rapid decisions. It can be difficult to manage the complexity of item management as the design evolves through various stages of product development, such as proof of concept, prototyping, engineering product release, pre-production release, and production.
Inefficient item management can lead to a lack of visibility and perspective, which can, in turn, paralyze the design process. Engineering teams require visibility and perspective to make informed and timely decisions to move the design forward. The lack of a centralized system that is capable to contain all knowledge and be collaborative can make it challenging to coordinate team efforts and manually manage item complexity across the engineering team. And this is what happens for many manufacturing companies and engineering teams. At OpenBOM we can see Fortune 500 companies “sitting” on the large legacy PLM and ERP software stack managing new product development using Excel.
This is where the new digital thread begins and new collaborative platforms are coming. These systems are focusing on problem-solving by providing a data management platform for an efficient product launch, collaborative BOM analysis, and BOM management, visualizing and navigating digital threads, and creating AI models for digital twins.
Engineering teams require a front-end database that can store and manage all design items, including CAD models, drawings, electrical schematics, purchase requests, engineering change orders, and reports. While design tools like Onshape, Fusion 360, Solidworks, Confluence, and JIRA can be excellent for certain tasks, they are not suitable for item definition and BOMs, especially for complex multidisciplinary products with mechanical, electrical and software items.
New product lifecycle systems of engagement and intelligence can help engineering teams work faster. A new system can establish a company-wide data platform to speed up product development and enable efficient collaboration between internal supply chain teams and external contract manufacturers and partners. Clear and rapid communication earlier in the design process can result in cost-effective products and faster time-to-market.
Data Analysis and AI – Next Step?
Once the company established a broad platform to manage product data and collaborate, the next step will be to bring AI models into the game. Read more about manufacturing use cases for AI and how it can be beneficial to create new data platforms. Data is hardly available in legacy systems and stops companies from their data innovation. At OpenBOM we are doing research on how model data management and large language models can be used for artificial intelligence – read more about OpenBOM Copilot research.
Conclusion:
Efficient data management and collaboration are crucial for engineering teams to optimize their processes and speed up product development. Engineering teams require a centralized intelligence system that defines and manages all product items to coordinate team efforts and make informed and timely decisions. A new collaborative company-wide data management platform capable to organize the entire data and to support efficient collaboration and clear communication across internal supply chain teams and external partners will speed up new product development and will help manufacturing companies move faster with their NPD efforts. By empowering engineering teams with the right tools, companies can remove the fundamental source of friction impeding their progress and speed up their product development.
REGISTER FOR FREE to check how OpenBOM can help you.
Best, Oleg
Join our newsletter to receive a weekly portion of news, articles, and tips about OpenBOM and our community.