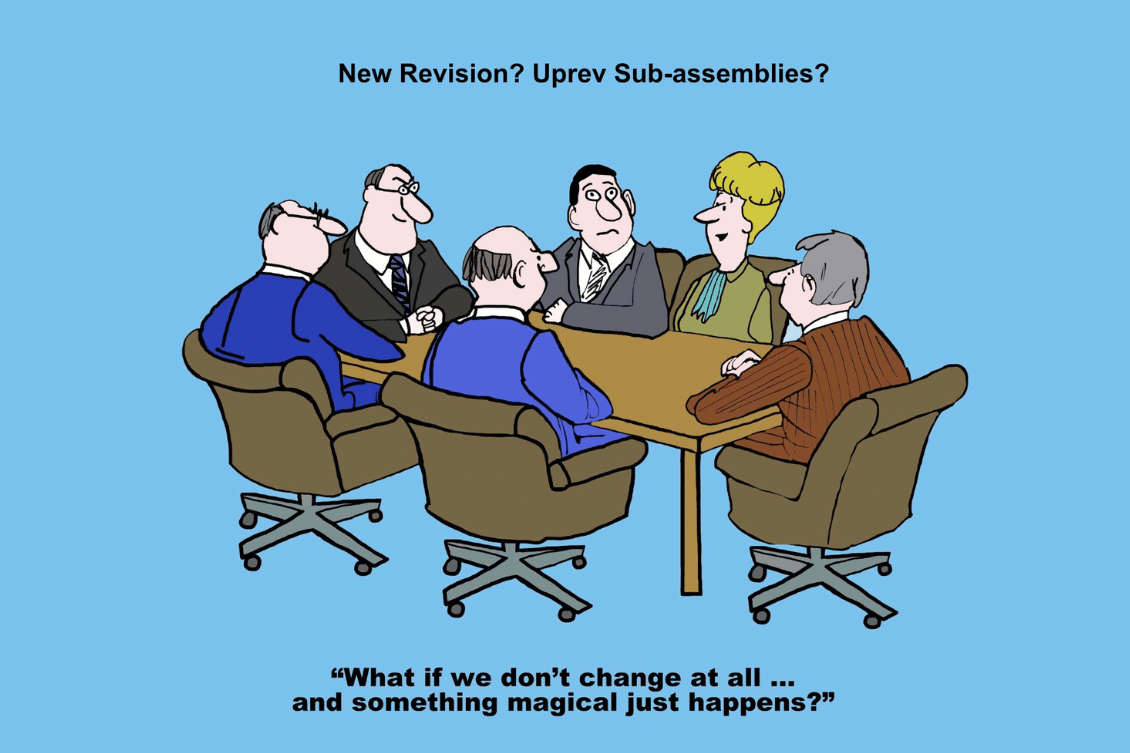
Making modifications can be challenging, which is why the subject of revision management often prompts a great deal of inquiry. This is particularly difficult and crucial for firms transitioning from a revision management system primarily based on “Excel ware.” In the context where your only tool is a hammer, all issues, including those related to revision control, are treated as nails.
A Bill of Materials (BOM) is a comprehensive list of raw materials, parts, assemblies, and sub-assemblies required to manufacture a product. A multi-level BOM, in particular, represents the hierarchy of components and sub-components in complex assemblies, extending from the finished product to its simplest parts. However, as with any complex system, a multi-level BOM’s maintenance can pose significant challenges. The complexity increases manifold as each level has its own revisions, leading to a critical need for an effective revision control system.
The Complexity of Multi-Level BOMs and Revision Control
A multi-level BOM is not just a single list but a set of BOMs for each level, each associated with its unique assemblies or sub-assemblies. Every assembly, sub-assembly, or part within this structure might have numerous revisions due to various factors like design changes, quality improvements, vendor changes, etc.
This multilayered structure demands a meticulous, robust, and scalable revision control system. This system would need to consider each level’s unique revisions, ensuring that the changes reflect accurately across all dependent and associated elements.
Top-Down Revision Control
The Top-Down approach is an overarching revision control system. It is simple but brutal. In this method, if a revision occurs at any level of the BOM, the change triggers an automatic downward revision for all associated sub-levels. This strategy ensures consistency and unity across all levels of the BOM. But the cost of this method is high. You will be creating many-many revisions.
For example, if a component within a sub-assembly is revised, all the associated BOM levels – right up to the top – are automatically updated with this revision. This mechanism is good when you need to create a first revision baseline. It can work in some scenarios, especially with contract manufacturers.
However, while the top-down method maintains comprehensive synchronization, it may also lead to unnecessary revisions where they are not directly relevant.
Bottom-Up Mixed Revision Control
Unlike the top-down method, the bottom-up mixed revision control approach offers greater flexibility. Here, each item or BOM is edited independently, and the upper-level BOM only captures the latest saved revision.
This approach allows for specific, granular changes without disturbing the entire BOM structure. For instance, a minor change in a component does not necessarily trigger a revision in the entire product line, preventing unnecessary paperwork or system updates.
In the picture below you can see 6 changes that were done to the same structure of the multi-level BOMs as before, but it didn’t cause the creation of extra revisions to all levels.
Yet, this method’s flexibility can also lead to challenges in maintaining comprehensive control and visibility across all BOM levels. Without diligent management, it could result in inconsistencies, especially in large and complex BOM structures. One of them is to apply FFF (Form, Fit, and Function criteria). We will talk about it later in future articles.
The Necessity of a Revision Management Strategy
Given the complexities of multi-level BOMs, it becomes evident that an ad-hoc approach to revision control, such as simple mechanisms applied in Excel, would fall short of the robustness required in managing changes.
In the absence of a well-planned revision management strategy, organizations risk inconsistencies, delays, and errors that could negatively impact product quality, production timelines, and overall business performance. A proper granular-level revision control strategy can thus be a cornerstone of a robust change management system.
There isn’t a ‘one-size-fits-all’ approach to managing revisions in multi-level BOMs. Depending on the specific requirements, an organization might find the top-down, bottom-up, or a hybrid approach most effective. Regardless of the strategy chosen, it is essential that the solution provides real-time visibility, consistency, and traceability across all levels of the BOM.
Conclusion:
When a company is coming from “simple” but messy Excel revision control, we recommend making some analysis in the strategy of revision control. Your BOM is not an Excel file with all lines, but a robust product structure. It is granular and each level is defined as a separate BOM with its own revisions. A successful revision control in multi-level BOMs is a balance between flexibility and control. It requires criteria definition when a component (or BOM) needs to be changed and up-rev to the next level. Remember, a carefully designed and executed revision control strategy is not just about managing changes – it’s about ensuring the integrity of your product and the sustainability of your business.
At OpenBOM we help you to develop a strategy to build a robust revision control system in complex multi-level structures, but still keep it simple and manageable.
REGISTER FOR FREE to check how OpenBOM can help you today.
Best, Oleg
Join our newsletter to receive a weekly portion of news, articles, and tips about OpenBOM and our community.