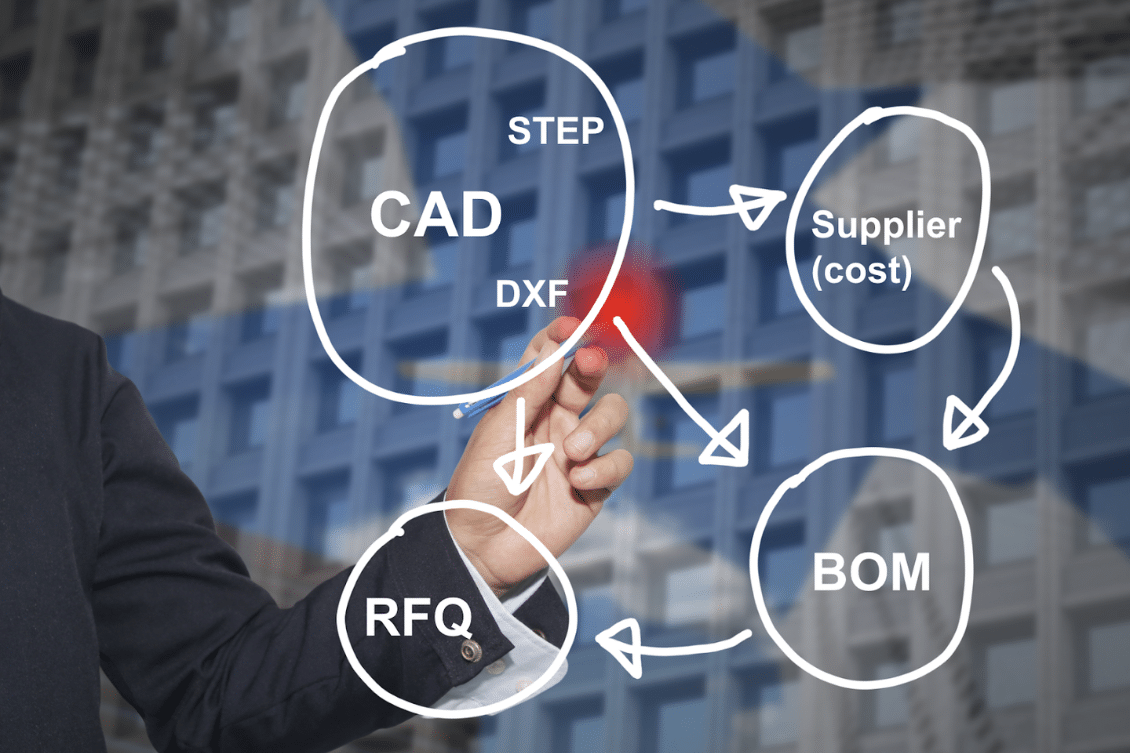
In the world of CAD design and downstream processes like production planning and supply chain management, the question of where to store data often triggers many conversations and sometimes heated debates.
As the saying goes, “If all you have is a hammer, everything looks like a nail.” The same applies to engineers using CAD systems. If your primary focus is CAD and data, it might seem tempting to store all data within the CAD model, including supplier information and costs. However, this practice can lead to various challenges and drawbacks. In this blog, we’ll explore the pros and cons of storing all data in CAD files and suggest alternative solutions.
Pros of Storing Data in CAD:
Simplicity: Storing data in the CAD model is straightforward. For example, in SolidWorks, you can easily add attributes for supplier information, cost, and part numbers.
Easy Management: Individual engineers can manage and update the data within CAD files, making it convenient for small-scale projects.
Reporting: Storing data in CAD facilitates the generation of reports, such as drawing Bill of Materials (BOM), which can be valuable for procurement purposes.
Cons of Storing Data in CAD:
Difficulty in Handling Changes: When changes occur purely on the supplier or cost side, it can be challenging to update the information in CAD files without affecting the design. This can lead to unnecessary revisions and delays.
Approval Bottlenecks: Including supplier part numbers in CAD files can lead to an excessive number of drawing approvals, especially when a supplier change is necessary.
Lack of Supply Chain History: Storing all data in CAD restricts your ability to maintain a comprehensive history of supply chain processes outside of engineering, limiting your insights into cost fluctuations and supplier performance over time.
So, What Can Be Done?
To address these challenges, here are some ideas on how to improve the management of supplier-related data in CAD design processes:
Use PLM/BOM Data Management Tools: Implement online data management tools that allow you to manage product structures and item information independently of CAD files. This separates engineering data from supplier-related data and enables more efficient management.
Generate Part Numbers Separately: Instead of using part numbers as CAD file names, generate them independently in your data management system. This allows for easier supplier changes without affecting the design.
Seamless Data Integration: Establish seamless data integration between CAD files and your data management system, ensuring that information such as supplier details and costs can be easily updated without disrupting the design process.
How OpenBOM Can Help?
At OpenBOM, we help you to set up a product structure (BOM) that easily captures data from the CAD system, automatically transforms information into derivative files (PDF/STEP/DXF/etc), and combines it all. It allows you to add all “non-design” items, and finalize all information that goes in the BOM including item information, suppliers, multi-sourcing and more.
Sourcing data is extremely important because it allows you to externalize cost/supply data in a granular form outside of CAD design documents.
The outcome is the ability to make suppliers/cost management decisions without changes in 3D design and CAD drawings.
Conclusion:
Effective data management is becoming increasingly crucial for manufacturing engineering, design, and supply chain operations. While storing all data in CAD files may have once been a practical approach, the growing complexity of information and processes calls for a more optimized approach to data storage and management. By implementing robust data management tools and workflows, organizations can better organize, manage, and optimize their data flow, leading to improved efficiency and competitiveness in today’s manufacturing landscape.
REGISTER FOR FREE and check how OpenBOM can help you today.
Best regards,
Oleg
Join our newsletter to receive a weekly portion of news, articles, and tips about OpenBOM and our community.