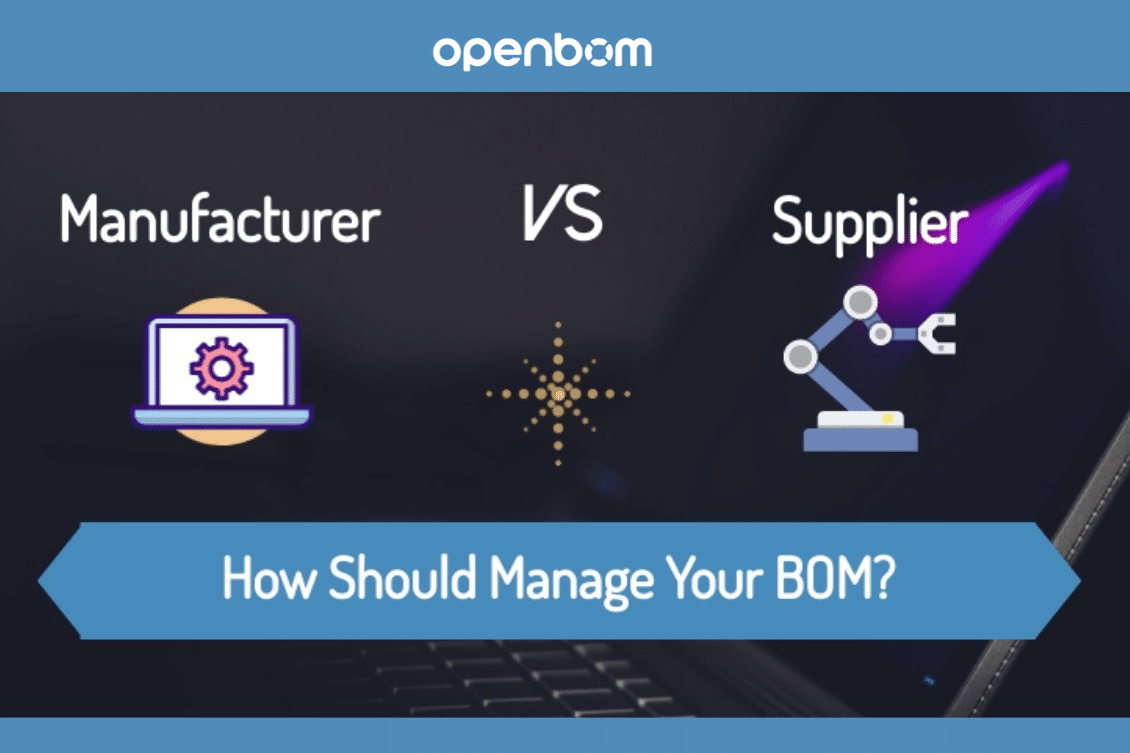
In the complex world of development and manufacturing, there exists one part that holds the knowledge of the product – the Bill of Materials (BOM). The BOM is an important part of any product as it details all components, materials, colors, textures, and more that go into the product. It is the blueprint that is used to build your product.
The BOM is passed from person to person, team to team, and from company to contract manufacturer (CM) or supplier. As the BOM is being bounced back and forth, manufacturers often lose sight of who is responsible for the upkeep of the BOM. This often causes confusion and you can lose track of what the current state of your BOM should look like.
If your CM is supporting you with development then should they control your BOM? This blog will outline the importance of managing your BOM during development and share some risks of what might happen if your CM takes on the responsibility of managing your BOM during development and even production.
The Importance of Managing Your BOM During Development
During development, there are constant changes. All of these changes need to be tracked and documented, if not then who knows what the most updated parts are. Without a clear BOM during development, how are you supposed to know what to prototype vs. what you already prototyped?
As you transition closer to production and start design for manufacturing (DFM), managing your BOM will grow in importance so you can navigate quickly into production. If the BOM is not updated then you know you can’t start production.
Managing your BOM during the agile product development process is important for several reasons.
Product Iterations
Long gone are the days of the traditional waterfall process, which usually includes people responsible for each step of the overall product development process that is not connected or integrated. Agile development allows quick iterations that are based on feedback from customers. All of these iterations need to be tracked.
Managing the BOM ensures that all changes to components and materials are accurately documented, preventing discrepancies or oversights that could lead to production errors.
Cost Control
Have you ever developed a product with your CM without tracking production costs?
Agile development often involves evolving design concepts and features. By maintaining control over the BOM, you can closely monitor the cost implications of design changes. This allows you to make informed decisions about whether a particular design iteration aligns with your cost objectives.
Supply Chain Agility
In agile development, you need to respond swiftly to changes in market demand, customer feedback, or unforeseen challenges. Having control over the BOM gives you the agility to adjust the supply chain, source alternate components, or switch suppliers as needed to meet changing requirements.
Traceability
Agile development often involves cross-functional teams and collaboration with various stakeholders. An accurate and well-managed BOM provides traceability, helping you track the history of changes, identify contributors, and ensure accountability throughout the development process.
Enable Collaboration
Agile development relies on effective collaboration among team members and stakeholders. A well-managed BOM serves as a central reference point that facilitates communication and collaboration by providing a shared understanding of the product.
But Who Controls Your BOM During Development?
During the development phase of a product, the responsibility for managing the BOM should typically lie with the manufacturer rather than the CM or supplier.
Manufacturers have an obligation to ensure that the product aligns with their vision, quality standards, and cost objectives. They are ultimately accountable for the success of the product in the market, which includes meeting customer expectations, regulatory compliance, and profitability. While CMs play vital roles in component sourcing and production, allowing them to control the BOM can introduce risks related to quality, transparency, and intellectual property protection.
Manufacturers are better positioned to oversee the BOM, maintain clear communication with suppliers and CMs, and make informed decisions that align with their overall product strategy and goals. However, effective collaboration and communication between all stakeholders remain essential to successful BOM management during development. But why do CMs manage the BOM for their customer?
There are a few reasons why a manufacturer allows the CM to manage their BOM. They are the following:
- The CM has the expertise
- Reduces the administrative burden of the manufacturer
- Costing convenience
- They have a little bit too much trust in their CM
The Risks of Your CM Managing the BOM
Since the CM is often supporting the development of a product and will be the one manufacturing the product, there are risks with allowing your CM to control the BOM.
Quality Control Issues
One of the goals of DFM is to optimize the way parts are fabricated in order to reduce costs. While reducing costs is a goal, it can jeopardize the quality of the product. While the CM might have good intentions, it can result in a loss of quality, something the manufacturer will need to decide whether those risks are acceptable or not.
Lack of Transparency
When the CM controls the BOM, you may have limited visibility into the sourcing and procurement processes. This lack of transparency can make it challenging to track costs, verify component quality, and ensure compliance with your specifications.
Intellectual Property Concerns
Your BOM may contain sensitive information about your product design and proprietary components. Allowing the CM to manage the BOM could expose your intellectual property to risks of theft, unauthorized replication, or use in competing products.
Supply Chain Dependency
Depending on your CM to manage the BOM can create a significant supply chain dependency. If the CM faces disruptions or goes out of business, it could severely impact your ability to source components and continue production.
Limited Control Over Changes
CMs may make changes to the BOM without your approval or proper documentation. These changes, even if well-intentioned, can lead to quality problems, production delays, or unexpected costs.
Difficulty in Switching CMs
If you decide to switch CMs or bring production in-house, transitioning control of the BOM can be complex and costly.
Loss of Cost Control
While CMs can offer cost advantages, they may not always align with your long-term cost-saving strategies. You may lose control over negotiations with suppliers and miss out on opportunities to reduce costs.
What to do Today
Companies are always looking for ways to bring products to market and improve their overall competitiveness. During the development process, manufacturers are looking to transition from prototypes to production as quickly as possible. While these manufacturers need to be agile through development, they are left using legacy systems and traditional spreadsheets which do not support their evolving demands.
Digital transformation will help you to transform your processes and help you share data with your supplier during development. To have a centralized platform that connects your team with your contractors is extremely important to set up modern digital processes to save time and money.
OpenBOM is a cloud-based PDM & PLM platform to manage your engineering and manufacturing data. Companies from startups to Fortune 500s use OpenBOM to create a centralized database to bring in, store, and manage their manufacturing data. With this infrastructure, users also use OpenBOM to streamline both their change management and PO processes.
If you need to improve the way you manage your data and processes, share data instantly, or collaborate with contractors and suppliers, contact us today for a free consultation.
Join our newsletter to receive a weekly portion of news, articles, and tips about OpenBOM and our community.