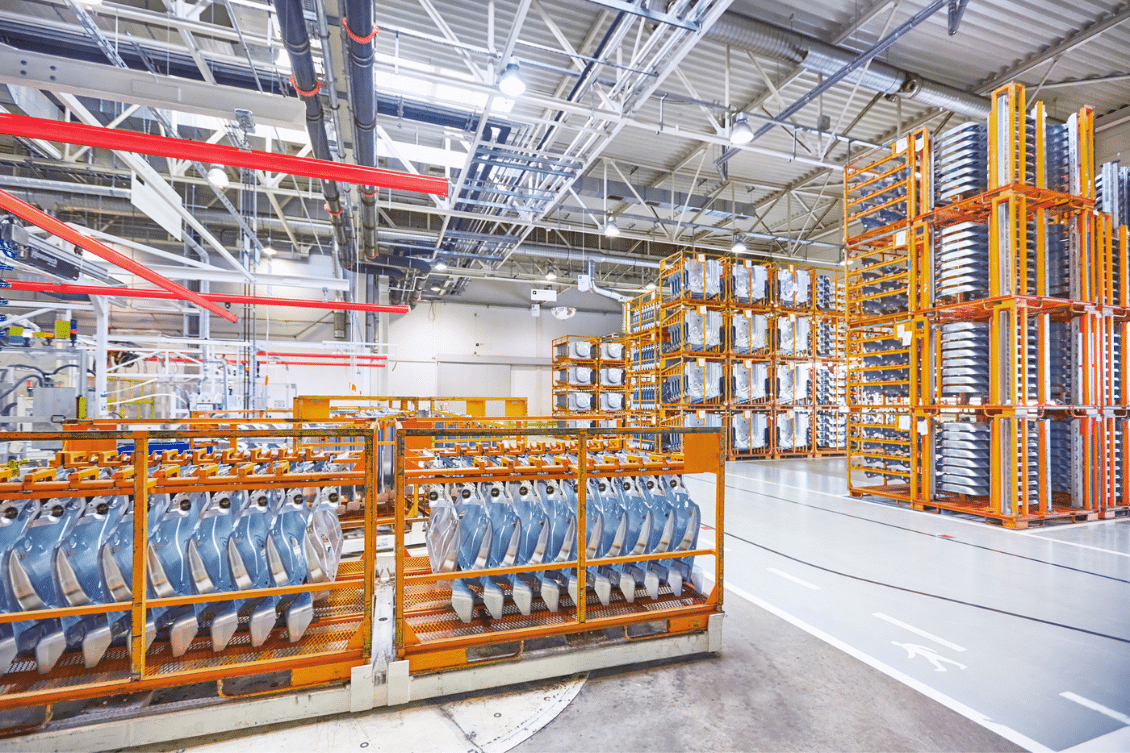
I’m coming up with another article about OpenBOM best practices. Today, I want to talk about data management for the supply chain. More specifically, I want to address the data model for multi-sourcing in OpenBOM that will allow you to manage multiple sources (vendors) where you can purchase components and organize custom information about manufacturers, suppliers, costs, specs, etc.
In today’s fast-paced business environment, efficient data management is critical to streamlining purchasing and supply chain processes. Managing data about sources to purchase components and outsourced units can be complex and time-consuming, leading to errors, delays, and increased costs. However, with the right tools and technologies, businesses can simplify data management and enhance their purchasing and supply chain operations.
OpenBOM will help you to do this. OpenBOM is a modern cloud-based digital thread platform that manufacturing companies, suppliers, and contractors can use to manage product information. It provides robust multi-sourcing data management capabilities that help to extend Item catalogs with information about where you are going to purchase components or outsource your work.
OpenBOM Core – Item Catalogs
The foundation of OpenBOM data management is item catalogs providing you with the capability to define any group of items with part numbers and manage different types of items. In other words, you can manage your fasteners, prefabricated units, electronics, plastic parts, electronics, etc. in a granular way.
OpenBOM doesn’t prescribe the way you need to organize your data. The catalog is a flexible mechanism that every company can use to manage their item, distribute unique part numbers and add any attributes.
Item Multi-Sourcing
One of the key features of OpenBOM is its ability to handle multi-sourcing scenarios efficiently. Multi-sourcing is a common practice in manufacturing and supply chain management, where businesses source components or materials from multiple suppliers to ensure continuity of supply, reduce risk, and optimize costs. However, managing data from multiple suppliers can be challenging, as it involves tracking prices, lead times, availability, and other critical information. OpenBOM simplifies this process by providing a centralized platform where businesses can manage data from different suppliers in a structured and organized manner.
OpenBOM allows companies to extend catalogs with “sourcing” information where they can define and maintain a list of approved suppliers for each component or material in their BOMs. Businesses can also specify preferred suppliers and alternate suppliers for each item, enabling them to easily switch between suppliers based on availability or other factors. This helps businesses to quickly respond to changes in the supply chain and make informed decisions to optimize their purchasing process.
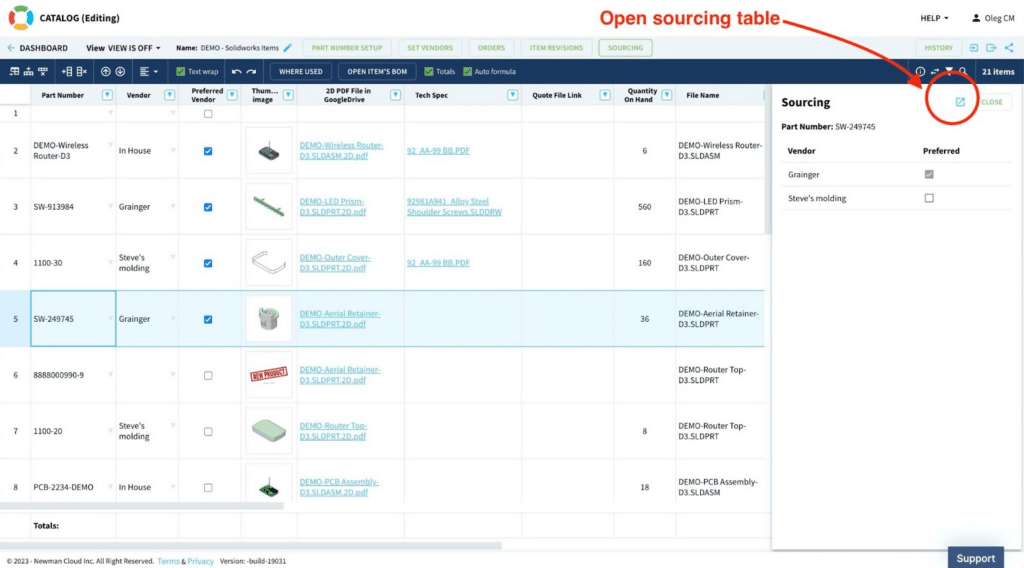
The sourcing command helps to define multiple records for different approved manufacturers. These sourcing records allow the managing of different attributes for different manufacturers – manufacturer part number, supplier, cost, etc. Keep in mind that all information can be customized and any attributes can be added.
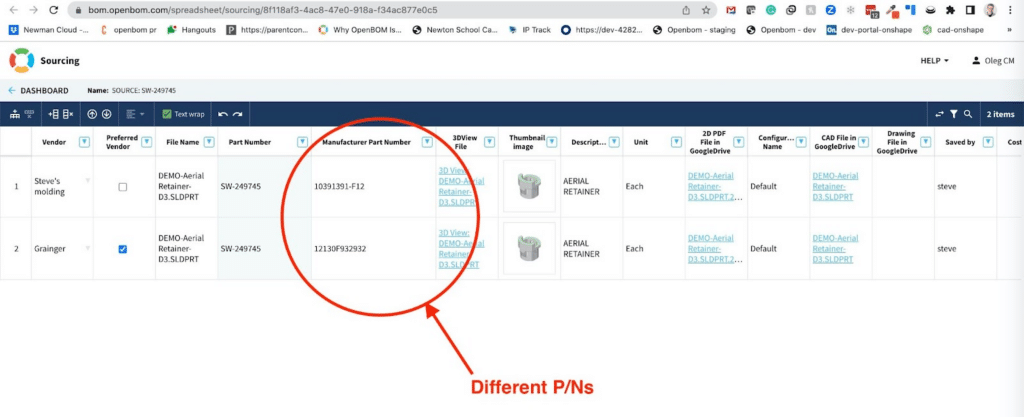
Integrations and downstream processes
OpenBOM allows integration with popular CAD systems, such as SOLIDWORKS, Autodesk, and PTC Creo, allowing businesses to seamlessly transfer BOM data from CAD systems to OpenBOM. Once transferred OpenBOM can merge this information with the supplier’s data in such a way you will be able to easily create a spec and manage purchasing in a very efficient way. This eliminates the need for manual data entry, reducing errors and saving time. OpenBOM also integrates with popular ERP systems, such as NetSuite, QuickBooks, and others, enabling businesses to synchronize BOM data with their ERP system, ensuring data consistency across the organization.
Conclusion:
Efficient multi-sourcing item management is crucial for businesses to streamline their purchasing and supply chain processes. OpenBOM allows you to manage multiple vendor records in the sourcing process. With its unified platform and robust data management capabilities, OpenBOM enables businesses to streamline and optimize their purchasing and supply chain operations. By providing a centralized repository for vendor data, OpenBOM helps eliminate data inconsistencies, duplication, and errors that can occur when managing data from multiple sources. It allows businesses to easily track, coordinate, and update vendor information, resulting in improved efficiency, accuracy, and communication in the sourcing process. With OpenBOM, businesses can confidently manage their multi-sourcing data and ensure a smooth and streamlined procurement and supply chain operation.
REGISTER FOR FREE to check OpenBOM out with a free 14-day trial.
Best, Oleg
Join our newsletter to receive a weekly portion of news, articles, and tips about OpenBOM and our community.