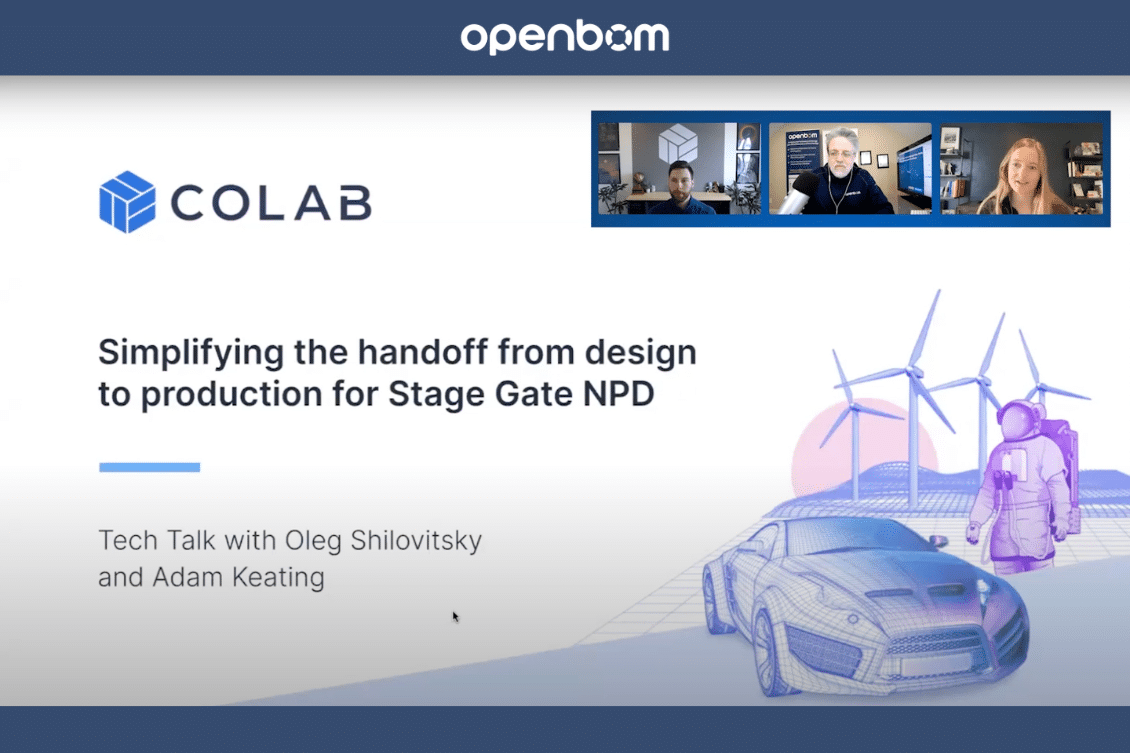
The handoff from engineering to manufacturing is often the most nerve-wracking stage in the product development process. It’s the point of no return – the point where significant investments, such as tooling, are made, and design errors can lead to costly and time-consuming consequences. Engineering to manufacturing processes is one of the most complex and their stories are written about the implementation complexity of EBOM to MBOM, Design Freeze, ECO, and MCOs.
I’ve been discussing the topic of transitioning engineering to manufacturing for many years on my blog Beyond PLM and also OpenBOM. I connected with Adam Keating, CEO of CoLab Software to discuss handoff from engineering to production (thank you CoLab for organizing the webinar, and thank you, MJ Smith, VP of Marketing of CoLab for moderating this tech talk). During the tech talk, both Adam and I shared our insights to help businesses navigate this critical topic. I hope we also were able to offer some practical advice on how to make the New Product Introduction (NPI) process more efficient and less stressful. For sure, we will come back to this topic again in our future webinar. Meantime, I want to offer you some of my notes and also a recording of the webinar.
Design Freezes: An Incomplete Solution
We kicked the conversation with a discussion on why design freezes often fall short of expectations. While they are intended to prevent late-stage design changes that can disrupt production, in practice, they can often lead to overconfidence that ignores the potential for unforeseen problems. Both Adam and I emphasized the importance of iterations (opposite to freeze) and communication between both the Engineering and Manufacturing teams. This requires a more holistic approach to product development, focusing on comprehensive planning, effective communication, and the use of reliable digital tools to manage and track design changes.
Mitigating Risk in Stage Gate Processes
The next topic we discussed is risk management in Stage-Gate processes. The main idea in a modern collaborative environment is to start doing things earlier in the process. You should not wait until the design is done to start transferring things to production. The main feature of modern stage gates is to give early exposure of the design to manufacturing teams to plan production, supply chain, and manufacturability of the product. These are the top three things to focus on. By identifying potential challenges early on, teams can develop risk mitigation strategies and make informed decisions that reduce the likelihood of costly errors or delays.
ECO Management and Cross-Tier Supplier Collaboration
Change management and the ECO process are extremely important. In the modern environment, they are not limited to one organization only. The complexity is a big factor. Today’s products have more components and systems than ever before. Impact analysis is an important element of a successful ECO process. Knowing about relationships in context can help you find the right scope of the data to change. To gather all information about potential change impact and making it available at your fingertips is a big goal for every successful ECO management program. Digital threads and knowledge graphs are modern tools that can help companies and teams to connect data points. It is important that clear communication and robust data management in coordinating changes across various levels of the supply chain is the foundation of cross-tier change management processes. This is crucial to ensure that all parties are on the same page and that changes are accurately reflected in the final product.
Operating in Complex Environment
The last discussion point was about how to operate in complex engineering and manufacturing data environments and processes. The key element here is information accuracy to enable better decision-making processes. Here is an important list of problems that must be addressed – information accuracy, improved decision by bringing connected data from multiple data and application silos; the need for speed (especially in new product development, and finally, support for new manufacturing business models (XaaS).
The key element of the future manufacturing environment is to move from focus on application to focus on data. Capturing data and producing intelligent insight is paramount in modern complex manufacturing organizations.
System of Engagement and Intelligence
Adam and I concluded the webinar by noting a common thread in all the topics discussed: the need for effective systems of engagement capable to help people in different organizations to work together and make things faster. The second thing is data and intelligence. AI is moving forward and we can see soon these tools show up in product development companies.
Video Recording
Please watch the tech talk recording here.
Conclusion
The transition from engineering to manufacturing is not a one-time event and cannot happen overnight. With the level of complexity, we can see in modern product development, the engineering-to-production move is an iterative process, which includes multi-faceted collaboration and communication between engineering and manufacturing teams moving it close to the point when engineering activities are finished and manufacturing activities are starting. It is extremely important to have the right data management and collaboration tools to help manufacturing and engineering teams to work together.
With the right strategies and tools, businesses can navigate this critical stage more confidently and efficiently, leading to better outcomes in their NPI processes. I hope you enjoyed my and Adam’s conversation and were able to capture one or two ideas on how to improve processes in your organization. I promise we come back with more webinars in the future.
REGISTER FOR FREE to check how OpenBOM can help you today.
Best, Oleg
Join our newsletter to receive a weekly portion of news, articles, and tips about OpenBOM and our community.