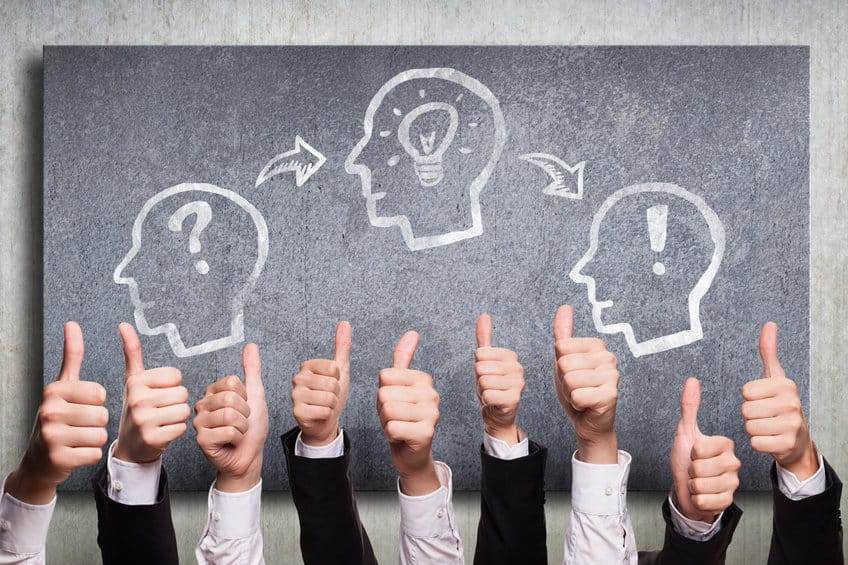
Supply chain shortages and disruption can create a lot of challenges for product development and manufacturing firms. While the procurement team is working on getting available materials and components, it is absolutely important to keep in touch with engineers and get quick approval on new materials, components, or changes. Fortunately, OpenBOM change management capabilities can allow you to organize a simple yet efficient process of making the approval process work. Don’t underestimate the complexity of management here – even the simplest change of component, might require the involvement of somebody from engineering to get approval and this activity needs to be tracked.
In my blog today, I will speak about best practices of organizing the change process for a single item change. What I will do is create a change for the item, add a new part spec and ask for approval. You can find full documentation about change management and how to do it on our training website later. Let’s get started.
STEP 1: Item and Revisions
OpenBOM is managing items using a catalogs database. The data is located in catalogs including Part Numbers, all attributes, links, and documents. This is where you can put any data or make a change (eg. change supplier or cost). In my case, I will be adding a spec sheet to the item to provide a new supplier source.
As you can see from the screenshot below, I added a spec sheet to the LED prism part (PN: SW-913984). As an engineer, I proposed the change and attached the spec sheet.
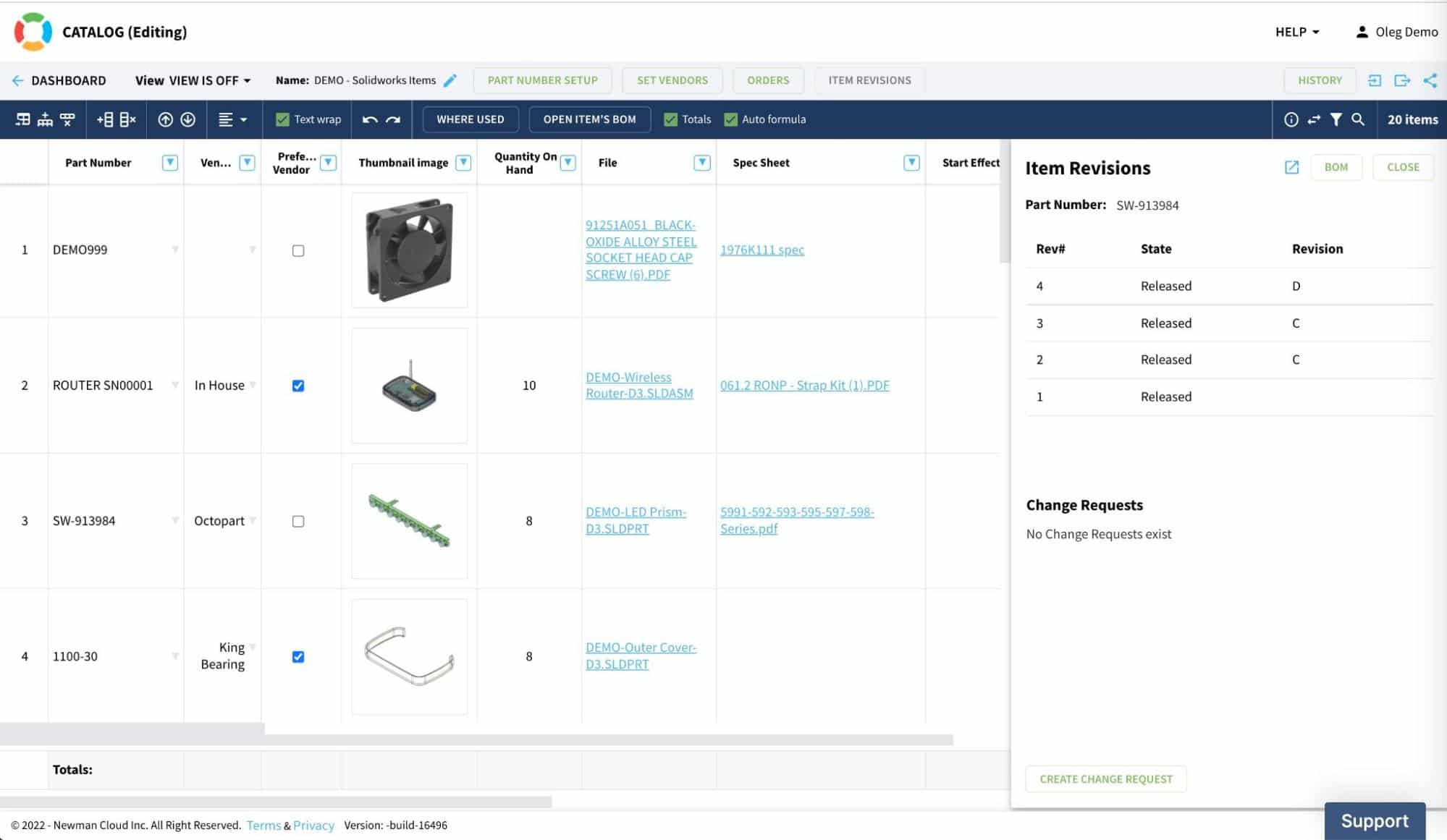
STEP 2: Making a change
To get things approved, I need to create a change request (CR). OpenBOM CR is the way to create an approval step before Item revision will be created. In my case, I created a CR and mentioned the change reason – spec sheet update.
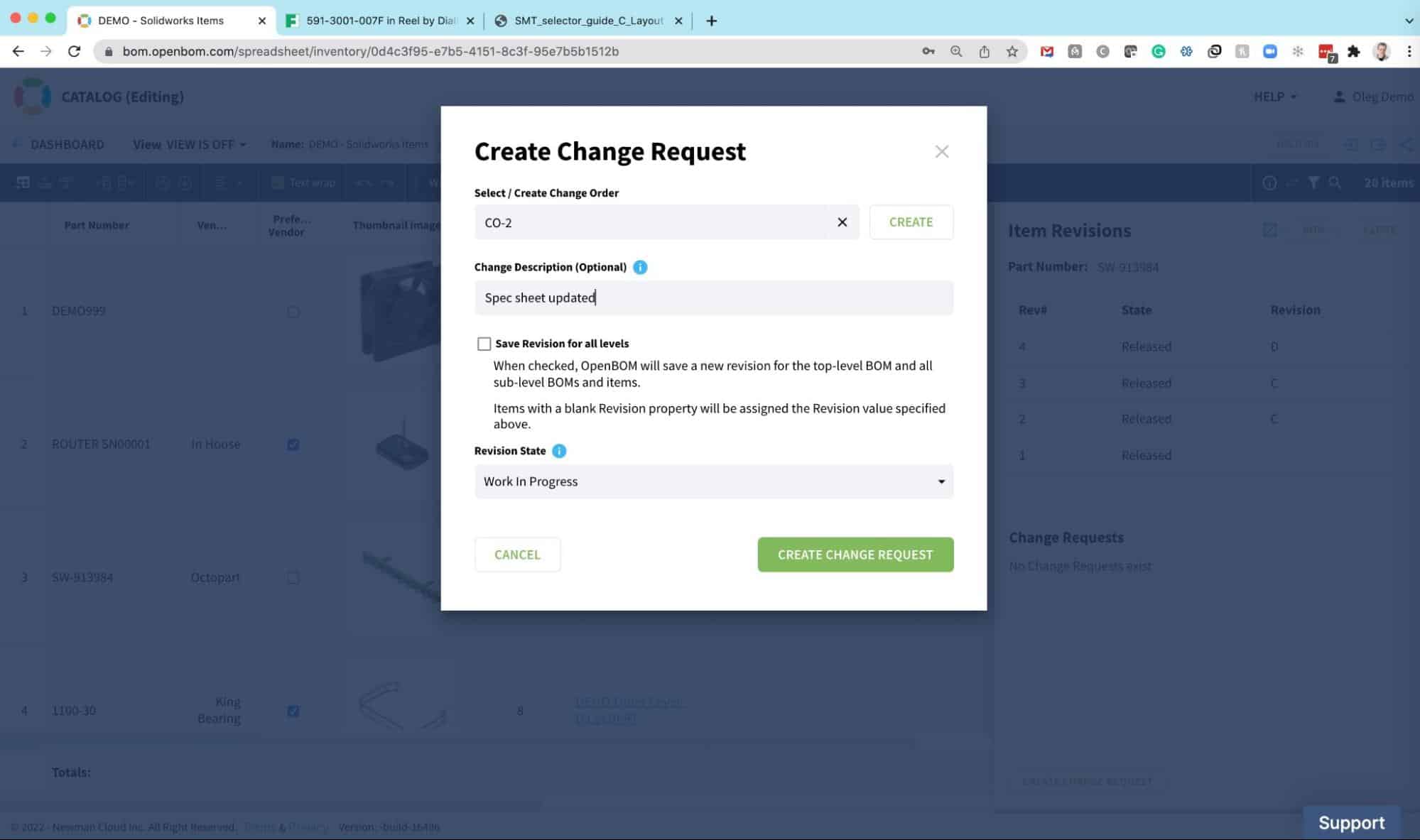
STEP 3: Reviewing a change
Once, the change was proposed, everyone can get to the data and review it. Thanks to the OpenBOM collaboration and data sharing mechanism, everyone can get on the same BOM and item without the need to send the BOM (or catalog) to the supplier for approval.
The review can happen at this stage as everyone gets to review it.
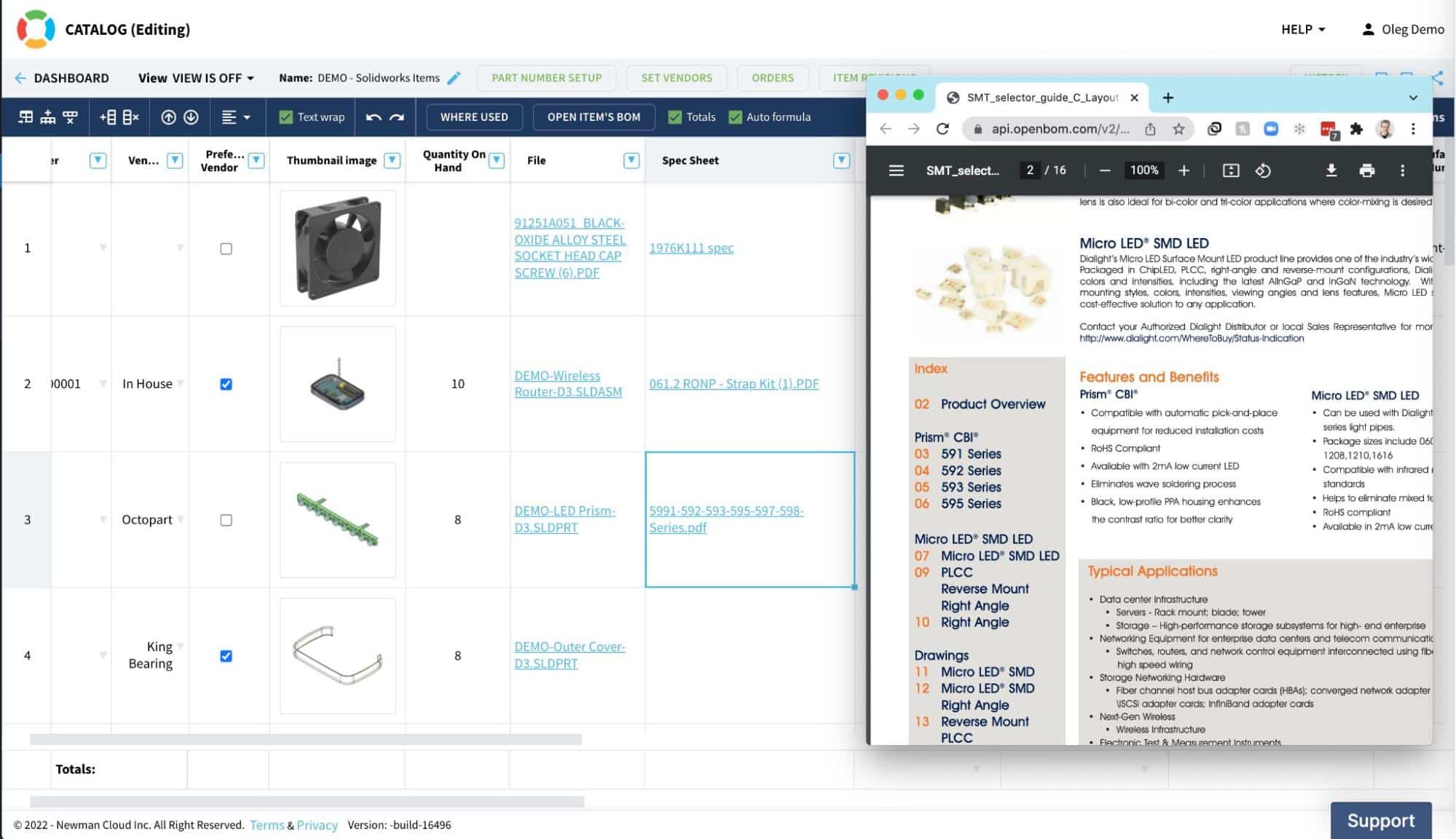
The next step is actual approval. A person with approval rights (to be defined by the end-user), will be able to review CR(s) and let it go to the approval. Check my earlier blog to see how to organize your approval process etc. Everything will be transparent and traceable.
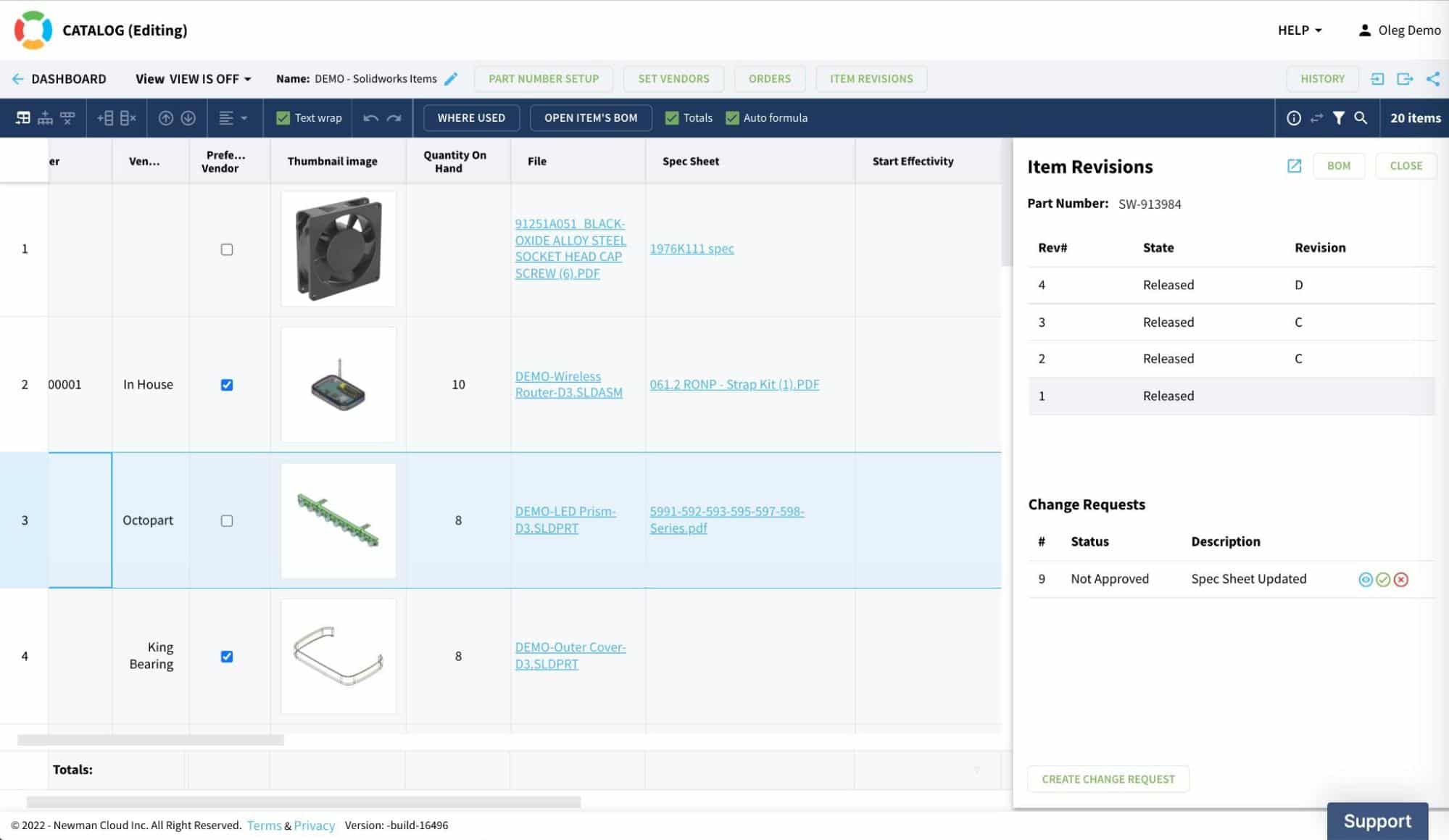
STEP 4: Approval and history trace of changes
One engineer approves the material (component) change, the admin or another person with the approval rights, will approve the change and the video will be created.

Here is the list of revisions which allows seeing all revisions that have already been saved.
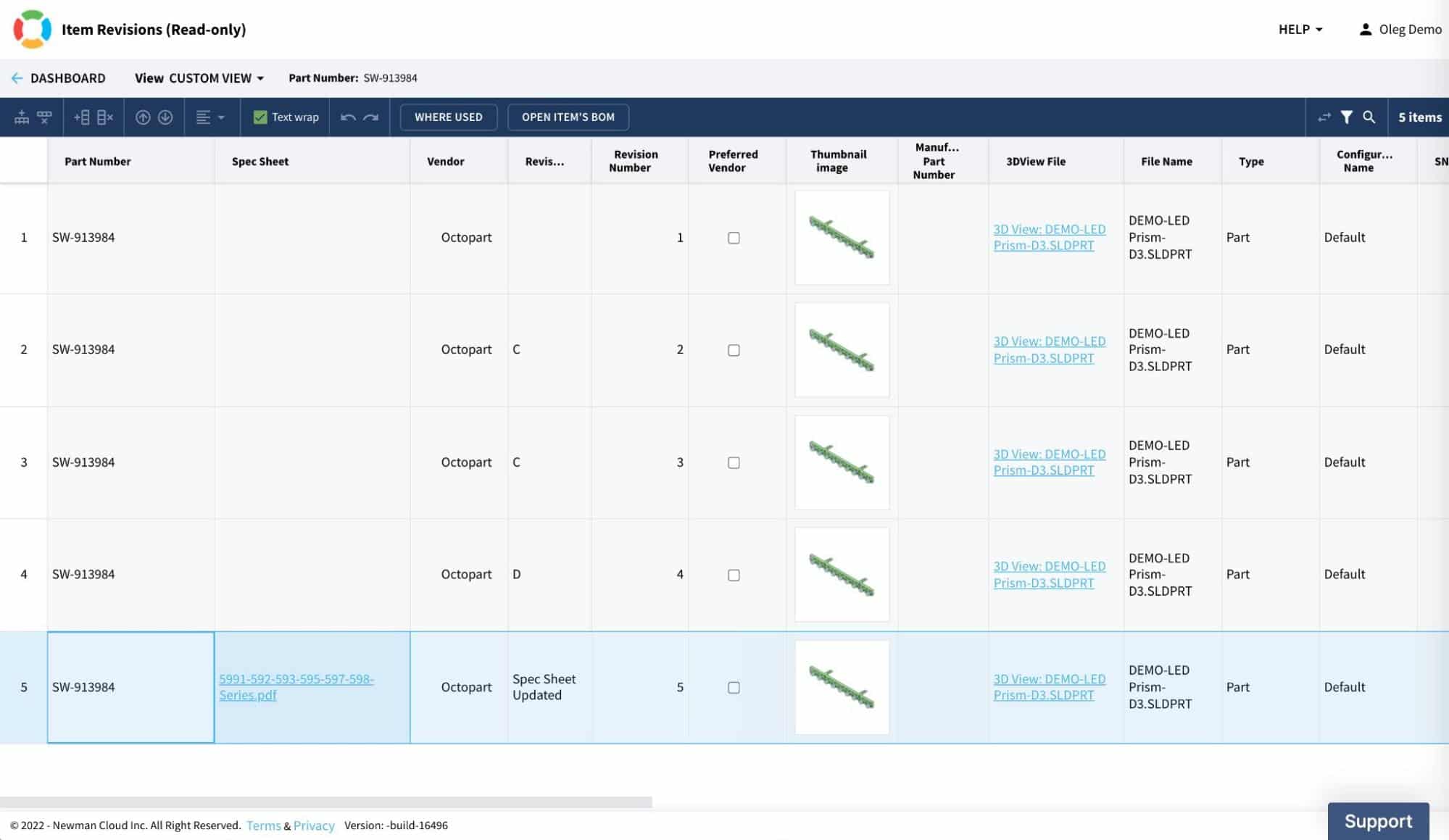
Conclusion
Providing a quick and efficient mechanism for change management is extremely important. Companies are struggling with engineering changes, manufacturing changes, and other disciplines and forcing themselves to work in sub-optimal conditions using Excel. What was right 10-20 years ago is not true anymore. You don’t need to send requests via email and struggle with Excel. OpenBOM is a modern and online system that will allow you to manage data, history about items, review and approve changes.
REGISTER FOR FREE to check out what OpenBOM can do for you. Try our 14-days trial today.
Best, Oleg
Join our newsletter to receive a weekly portion of news, articles, and tips about OpenBOM and our community.