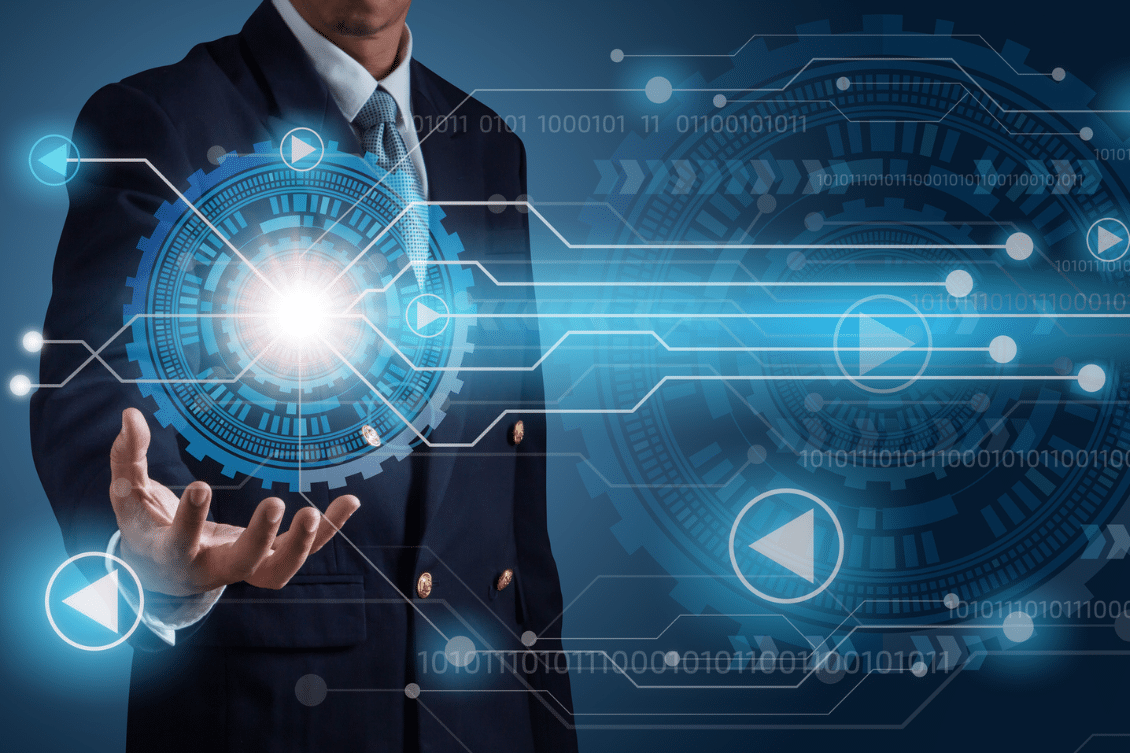
I attended the CIMdata PLM Roadmap 2023 event that was held last week in Washington, DC. The event brought together industrial companies, PLM experts, industry analysts, and software vendors in the field of Product Lifecycle Management (PLM) to discuss the theme of “Digital thread in heterogenous, extended enterprise reality“. The event aimed to explore perspectives on how industrial companies can use the digital thread concept and its potential to transform the way products are designed, manufactured, and serviced. Check my Beyond PLM articles for more information – Exploring CIMdata PLM roadmap agenda and CIMdata PLM Roadmap – Notes from customer presentations.
It was a great meeting to share and learn about experiences, insights, and best practices on how organizations can leverage the digital thread to enable greater collaboration, innovation, and agility across the entire product lifecycle.
The manufacturing industry is evolving rapidly, and during the last three years, we’ve been watching a lot of changes (and challenges) in the way manufacturing companies operate in the new “after COVID” world. Old and new manufacturing challenges demand immediate attention. Manufacturing is a place with a lot of technological competition and as technology advances, manufacturing companies are looking at how to adapt their strategies and processes to stay ahead.
The event made me think about the top 5 major data management challenges in modern manufacturing that require immediate attention from software vendors, service companies, and all PLM practitioners. In my blog today, I want to give my perspective on these problems and the ways to resolve them.
Information Accuracy: Operating with Inaccurate or Incomplete Data
In the age of big data and advanced analytics, information accuracy is crucial to the success of any engineering and manufacturing company. Operating with incorrect or insufficient data can lead to poor decision-making, reduced efficiency, and increased costs. Manufacturing companies are operating with complex data sets in their PLM, ERP, and MES systems. But connecting the data is hard. Manufacturers must invest in robust data management systems that ensure data integrity and allow for real-time analysis. By implementing accurate data collection, validation, and analysis processes, manufacturing companies can make informed decisions and minimize the risks associated with inaccurate data.
Possible solutions include implementing a comprehensive data management strategy that includes automated data collection, validation, and analysis processes. Invest in advanced analytics tools and machine learning algorithms that can identify data discrepancies and offer real-time insights. Also, train your workforce on the importance of data accuracy and establish a culture of data-driven decision-making.
Improve Decision-Making Process: Breaking Data Silos and Enhancing Collaboration
Manufacturing companies often struggle with fragmented data sources and complex supply chains, making it difficult to make informed decisions. Data silos can lead to inefficiencies, miscommunications, and missed opportunities. To improve the decision-making process, manufacturers should invest in integrated data systems that centralize information from different sources, breaking down silos and fostering collaboration across departments and teams. Additionally, adopting digital tools and platforms that promote information sharing and facilitate communication among distributed teams can significantly streamline decision-making processes.
Possible solutions include investment in integrated data systems that centralize information from different sources, breaking down silos, and fostering collaboration across departments and teams. Manufacturing companies must adopt digital tools and platforms that promote information sharing and facilitate communication among distributed teams. In addition to that, industrial companies must look into the implementation of data visualization techniques to make complex data more accessible and understandable to decision-makers.
Accelerating Processes: Streamlining New Product Development (NPD) and Change Management
In a rapidly changing market, the ability to quickly develop and launch new products is essential for staying competitive. Manufacturers must streamline their new product development (NPD) processes to accelerate time-to-market and improve responsiveness to customer demands. Implementing agile methodologies and leveraging digital tools can help companies optimize their NPD processes and quickly adapt to changes in the market. Additionally, effective change management strategies must be put in place to ensure a smooth transition as new products are introduced and processes are refined.
The solution is to adopt agile methodologies and lean principles to optimize the NPD process, enabling faster iterations and more flexible responses to market changes. Implement project management software that can help track progress, allocate resources, and monitor deadlines. Companies must establish cross-functional change management solutions responsible for coordinating and implementing process improvements, ensuring that changes are smoothly integrated and well-communicated throughout the organization.
Risk Mitigation: Strengthening Supply Chain, Compliance, and Other Risk Management Practices
The manufacturing industry is fraught with risks, from supply chain disruptions to compliance issues. To minimize these risks, manufacturers must develop robust risk management practices and adopt a proactive approach. This includes regularly monitoring and analyzing risks, implementing contingency plans, and investing in supply chain diversification. Manufacturers should also ensure that they adhere to regulatory requirements and industry standards to mitigate compliance risks.
A possible solution is to develop a robust risk management framework that includes regular risk assessments, contingency planning, and supply chain diversification. Utilize technology solutions, such as supply chain management software and predictive analytics tools, to gain better visibility into potential disruptions and proactively address them.
Supporting New Manufacturing Business Models: Embracing ‘X-as-a-Service’ (XaaS)
As manufacturing companies explore new business models, such as ‘X-as-a-Service’ (XaaS), they must be prepared to adapt their operations and processes accordingly. This shift requires companies to focus on digital infrastructure to support these new processes in addition to just selling products. To successfully adopt these new business models, manufacturers must invest in digital transformation initiatives, reevaluate their value propositions, and develop new skills and competencies among their workforce.
The solution is to invest in digital transformation initiatives that enable a seamless transition to new business models, such as cloud-based platforms, IoT technologies, and data-driven services. Reevaluate your value proposition and identify opportunities for providing value-added services and outcomes. In addition, companies must foster a culture of continuous learning and innovation, providing training and development programs to help employees acquire the necessary skills and competencies to thrive in the new business environment.
Conclusion:
As the manufacturing landscape continues to change, companies must be prepared to address the challenges that come with it. By focusing on improving information accuracy, enhancing decision-making processes, accelerating new product development and change management, mitigating risks, and supporting new business models, manufacturers can better position themselves for success in an increasingly competitive market.
At OpenBOM, we are working to bring new types of data management systems and solutions to help manufacturing companies overcome these tough decisions. Check with us to learn more about the OpenBOM Digital Thread Platform.
REGISTER FOR FREE to check how OpenBOM can help you today.
Best, Oleg
Join our newsletter to receive a weekly portion of news, articles, and tips about OpenBOM and our community.