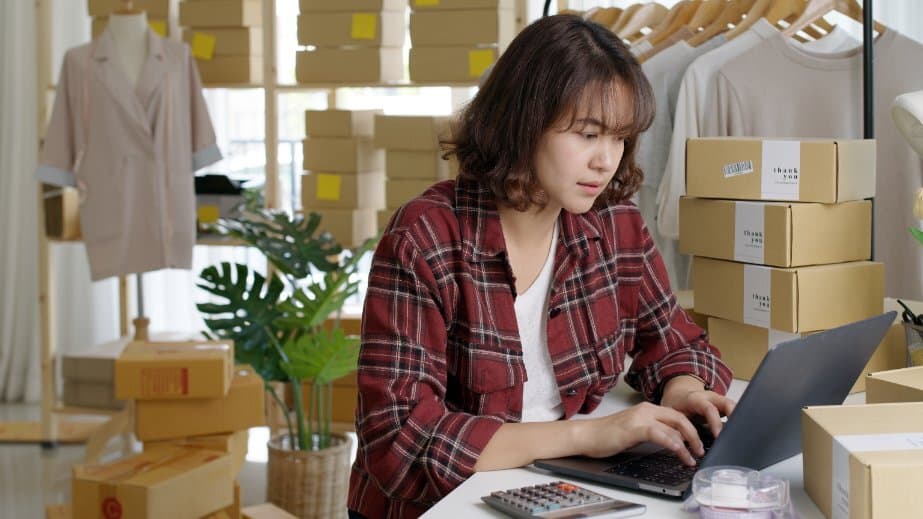
Everything in manufacturing is interconnected. There are reasons for defects, late shipments, material shortages, and more. It’s up to you and your team to capture these issues early and deal with them accordingly. With the state of the supply chain, how you manage all of the parts, bill of materials (BOMs), POs, lead time, quality, fabrication steps, and everything else that goes into your product is more important than ever.
Also, all departments are reliant on each other. Engineering needs to pass the BOM to purchasing. The supply chain needs to align all the parts to arrive at the assembly line. Production needs to follow the work instructions outlined by engineering and more. If any of the data is not transferred properly from one department to another or even from one person to another within the same department then expect issues. These issues increase costs, eat into your profits, and make you look bad.
Here are the top issues that stem from poorly managing your product data.
Pricing Problems
The most common problems resulting in poorly managing your product data are pricing problems or not knowing your costs. Not communicating changes that result in costs to your procurement and marketing teams will result in loss of margins and pointless back and forth with your supplier.
A common example is a change to the product to improve product reliability. As a result of this change, the price increases. If marketing and sales are not made aware of this then they will be selling the product for the same price. Resulting in a decrease in your margins.
Purchasing/Fabricating Incorrect Parts
Throughout the lifecycle, there will be many changes made to your product. If these are not communicated to production, procurement, and all the other teams, then you will fabricate incorrect parts with incorrect quantities. Increased costs are not the only result of purchasing/fabricating incorrect parts. You also have lead time problems due to the increased amount of time needed to re-fabricate or re-purchase the correct parts.
As a result, you wasted money on incorrect parts and risk not having enough supply to keep up with the demand of your customers.
Longer Lead Times
On the BOM, each line item should have a lead time associated with it. This is how your team will plan final assembly, shipping, and yearly forecasts. These lead times also fluctuate due to the chip shortage and the economic and global environment.
If the lead times are not updated then your purchasing and supply chain teams can not purchase parts at the correct time which will lead to either excess inventory or not enough inventory.
Why Does this Happen?
There are many reasons why manufacturing companies fail to manage their product data while in production. The main reason is that there is a lack of a centralized system to store this data. Oftentimes, managing this data is done using Excel or spreadsheets. While everyone is comfortable with these tools, they were not made for manufacturing teams. There are a few reasons why excels and spreadsheets fail to manage your product data but here are a few:
- No CAD integrations
- No change management workflow
- Does not store history of revisions
- Not convenient to share
What is the Solution?
In this age of manufacturing when some employees are remote and you need to share data with contractors and suppliers around the world, a system to help you share this data is needed. Also, a system to support your workflows and to provide everyone with the most up-to-date data along with the history is needed. The solution is building a single source of truth.
OpenBOM is a cloud-based PDM & PLM platform to manage your engineering and manufacturing data. Companies from startups to Fortune 500’s use OpenBOM to create a centralized database to bring in, store and manage their manufacturing data. With this infrastructure, users also use OpenBOM to streamline both their change management and PO processes.
If you need to improve the way you manage your data and processes, contact us today for a free consultation.
Regards,
Jared Haw
Join our newsletter to receive a weekly portion of news, articles, and tips about OpenBOM and our community.