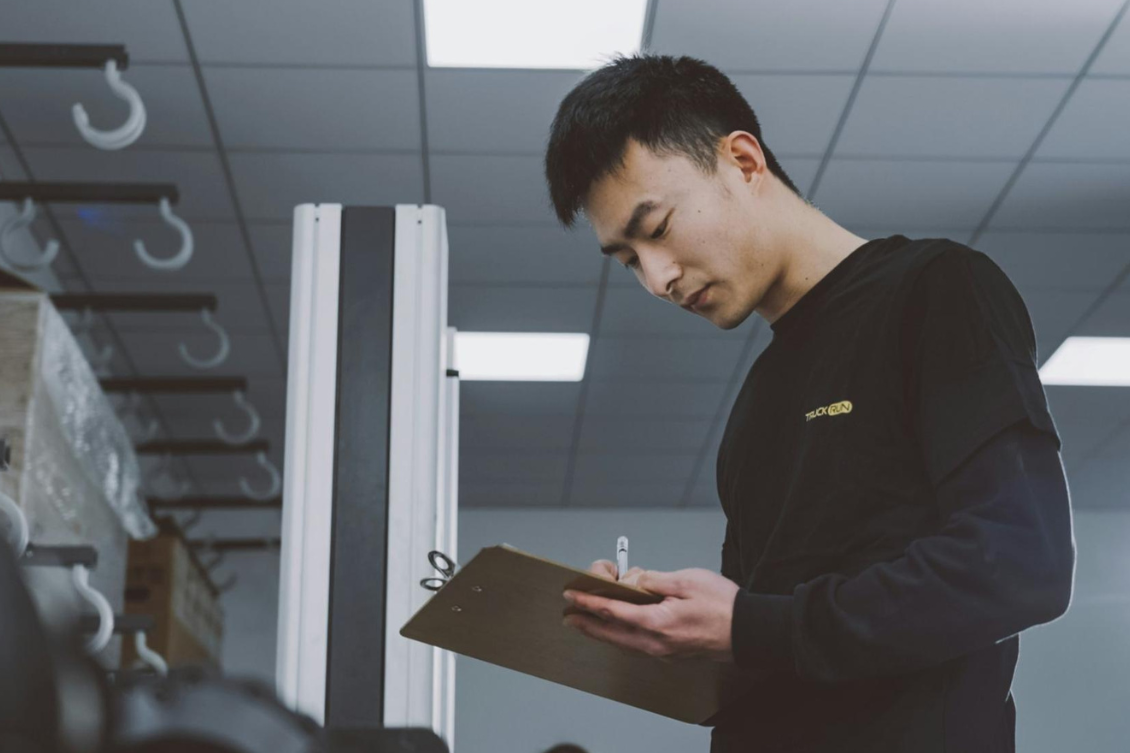
In manufacturing, where every detail counts, quality standards often get overlooked in the rush to meet deadlines. But let’s face it—without solid quality standards, you’re playing a risky game that could cost you big in the long run.
Whether you’re an engineer, a project manager, or a manufacturer, you know that even the slightest deviation in quality can lead to big problems—product failures, unhappy clients, and costly recalls. That’s why quality standards aren’t just about meeting regulatory requirements; they’re about maintaining consistency, building trust, and ultimately, securing the success of your business.
In this blog, we’ll dive into why quality standards are so critical in the manufacturing process. We’ll explore how they impact everything from product integrity to regulatory compliance, and why they can be a real game-changer for your business.
Understanding Quality Standards in Manufacturing
When we talk about quality standards in manufacturing, we’re referring to a set of well-defined criteria that ensure products meet certain levels of quality, consistency, and safety. These standards are the guidelines that keep everyone—from engineers to manufacturers—on the same page, ensuring that what’s designed is exactly what gets produced, without any unwelcome surprises.
What Are Quality Standards?
Quality standards are essentially the rules and benchmarks that define what “good” looks like in manufacturing. They can be industry-wide, like ISO 9001, or they can be specific to certain products or processes, like GMP (Good Manufacturing Practices) for pharmaceuticals. In manufacturing, these standards are crucial because they provide a clear framework that both the manufacturer and the client can rely on to ensure that the final product is up to par.
Why Are Quality Standards Important?
For contract manufacturers, quality standards are the foundation upon which successful projects are built. They ensure that every product coming off the production line meets the exact specifications required by the client. This is especially important in manufacturing, where the stakes are high, and any slip in quality can lead to significant financial losses, not to mention damage to your reputation.
But it’s not just about meeting specifications—quality standards also help in maintaining consistency across different production runs. Whether you’re producing a small batch or scaling up to mass production, sticking to these standards ensures that each unit is virtually identical to the last. This consistency is key to building trust with your clients and establishing long-term relationships.
Common Quality Standards in Manufacturing
There are numerous quality standards out there, but some of the most commonly used in manufacturing include:
- ISO 9001: A widely recognized standard that outlines the criteria for a QMS, focusing on meeting customer requirements and continuous improvement.
- ISO 13485: Ensures that your product development processes meet the stringent quality management standards required for medical devices, reducing the risk of non-compliance and enhancing product safety.
- GMP (Good Manufacturing Practices): These are regulations that ensure products are consistently produced and controlled according to quality standards, particularly in industries like food, pharmaceuticals, and medical devices.
- Industry-Specific Standards: Many industries have their own specific standards, such as ISO/TS 16949 for automotive quality or AS9100 for aerospace.
By adhering to these standards, manufacturers can not only meet regulatory requirements but also assure their clients that the products they receive will be of the highest quality, every single time.
The Impact of Quality Standards on the Product?
When it comes to manufacturing, product integrity isn’t just a buzzword—it’s the difference between success and failure. Quality standards play a crucial role in ensuring that every product not only meets but often exceeds the expectations of both the manufacturer and the client. Let’s break down how these standards directly impact the integrity of the products you’re putting out there.
Ensuring Consistent Product Quality
Consistency is king in manufacturing. Whether you’re producing a run of a hundred units or a hundred thousand, each one needs to meet the same high standard. Quality standards provide a clear blueprint for achieving this consistency. By following these guidelines, you ensure that every unit produced is virtually identical, with no unexpected variations that could affect performance or reliability.
For example, if you’re manufacturing electronic components, even a slight deviation in material quality or assembly can lead to malfunctions or, worse, complete product failure. Adhering to stringent quality standards means that each component is produced to the exact specifications needed, ensuring that the final product functions as intended.
Preventing Defects and Failures
Defects and failures are the nightmares of any manufacturer. They can lead to costly recalls, damaged client relationships, and a tarnished reputation. Quality standards are your first line of defense against these issues. By setting clear expectations and stringent guidelines for each stage of production, you minimize the chances of errors creeping into the process.
For instance, during the manufacturing of a medical device, a small defect could have life-threatening consequences. Quality standards in this context aren’t just about avoiding defects; they’re about ensuring that every device is safe, reliable, and effective. By following these standards, you significantly reduce the risk of defects, protecting both your business and your clients.
Building Trust with Clients
In manufacturing, trust is everything. Your clients need to know that they can count on you to deliver products that meet their exact requirements, every time. Adhering to quality standards is one of the most effective ways to build and maintain this trust. When clients see that you consistently meet these standards, they’ll have confidence that their products are in good hands.
Over time, this trust can lead to long-term partnerships and repeat business. Clients will know that they can rely on you not just to meet their current needs, but to consistently deliver high-quality products as their demands grow and evolve. In a competitive market, this level of trust is invaluable and can set you apart from other manufacturers.
In short, quality standards are the foundation of product integrity in manufacturing. They ensure consistency, prevent defects, and build the trust that’s essential for long-term success. By making quality standards a core part of your manufacturing process, you’re not just producing products—you’re producing confidence in your brand.
Implementing and Maintaining Quality Standards
Establishing and maintaining quality standards in manufacturing is essential for ensuring consistent product excellence. But it’s not just about having these standards in place; it’s about integrating them into every facet of your operations and continually refining them to meet the evolving demands of your clients and the market.
Training and Continuous Improvement
Quality standards are only as effective as the people implementing them, so it’s essential that everyone, from management to production floor staff, understands their role in maintaining these standards.
Regular training sessions should be conducted to keep everyone updated on the latest procedures and any changes to the quality standards. Additionally, fostering a culture of continuous improvement is vital. Encourage your team to identify potential areas for improvement and implement changes that enhance quality. This proactive approach ensures that your quality standards evolve alongside your operations, keeping you ahead of potential issues.
Monitoring and Feedback Loops
Implementing quality standards isn’t a one-and-done task; it requires ongoing monitoring to ensure they are consistently met. Regular audits, both internal and external, are essential for identifying any deviations from the standards and addressing them promptly.
In addition to audits, establishing feedback loops is critical. Collecting feedback from your clients and internal teams provides valuable insights into how well your quality standards are being maintained and where adjustments might be needed. Use this feedback to refine your processes, improve product quality, and address any emerging challenges before they become significant issues.
Embracing Technology for Quality Control
In today’s manufacturing landscape, technology plays a crucial role in maintaining quality standards. Implementing digital tools such as real-time monitoring systems, automated inspection equipment, and data analytics can significantly enhance your ability to track and control quality throughout the production process.
These tools provide you with real-time data, enabling you to detect and address issues as they arise, rather than after they’ve caused problems. By integrating technology into your quality management practices, you can improve efficiency, reduce errors, and maintain the high standards your clients expect.
Challenges in Maintaining Quality Standards
Maintaining quality standards in manufacturing is no small feat. While having these standards in place is essential for ensuring consistent, high-quality products, upholding them throughout the production process presents a unique set of challenges. Understanding and addressing these challenges is crucial for staying competitive and meeting client expectations.
Variability in Raw Materials
One of the most significant challenges in maintaining quality standards is the variability in raw materials. Even slight variations in the composition, quality, or source of raw materials can impact the final product’s consistency and performance. This is particularly challenging in industries where precision is critical.
To mitigate this, it’s essential to work closely with suppliers to ensure that the raw materials meet your specific quality standards. Regular inspections, certifications, and stringent supplier audits can help maintain consistency. However, managing this variability often requires constant vigilance and the ability to quickly address any issues that arise.
Complexity in Supply Chains
Global supply chains add another layer of complexity to maintaining quality standards. With multiple suppliers, subcontractors, and logistics providers involved, ensuring that everyone adheres to the same high standards can be difficult. Miscommunication, delays, and inconsistencies at any stage of the supply chain can lead to deviations from the required quality.
To overcome these challenges, robust supply chain management practices are needed. This includes clear communication of quality expectations to all stakeholders, regular monitoring of supplier performance, and contingency planning for potential disruptions. Implementing technology solutions like supply chain management software can also provide greater visibility and control over the entire process.
Workforce Training and Turnover
Another challenge is ensuring that all employees, especially those on the production floor, are adequately trained in maintaining quality standards. High turnover rates or a lack of proper training can lead to inconsistencies in production, as new or untrained employees may not fully understand or adhere to the established standards.
Addressing this requires ongoing training programs that keep all employees up to date on the latest procedures and quality requirements. It’s also important to foster a workplace culture that values quality and encourages employees to take ownership of their role in maintaining these standards. Regular refresher courses and performance assessments can help reinforce this culture and ensure that everyone is on the same page.
Keeping Up with Regulatory Changes
Quality standards are often closely tied to regulatory requirements, which can change over time. Keeping up with these changes and ensuring compliance can be challenging, particularly in industries like medical devices or automotive manufacturing, where regulations are stringent and frequently updated.
To navigate this challenge, manufacturers must stay informed about the latest regulatory developments and be prepared to adapt their quality standards accordingly. This may involve updating procedures, retraining staff, and investing in new technologies or equipment to meet the latest requirements. Working with regulatory experts or consultants can also help ensure that your operations remain compliant and that any changes are implemented smoothly.
Balancing Cost and Quality
Maintaining high-quality standards often comes with increased costs, whether through more expensive raw materials, advanced technology, or additional training. Balancing these costs while remaining competitive in the market is a significant challenge for many manufacturers.
To manage this, it’s important to focus on efficiency and waste reduction throughout the production process. Implementing lean manufacturing principles, optimizing supply chain operations, and using data-driven decision-making can help minimize costs without compromising on quality. Additionally, clear communication with clients about the value of maintaining high standards can help justify any additional costs and reinforce your commitment to delivering top-quality products.
Conclusion
Maintaining high-quality standards in manufacturing is not just a goal; it’s a necessity for achieving long-term success and building strong, reliable relationships with your clients. From understanding the core principles of quality standards to implementing them effectively and overcoming the inevitable challenges, the journey to excellence requires dedication, vigilance, and continuous improvement.
By prioritizing quality at every stage of the manufacturing process, you ensure that the products you deliver not only meet but exceed client expectations. This commitment to quality safeguards your reputation, enhances product integrity, and ultimately sets you apart in a competitive marketplace. As challenges arise, remember that maintaining these standards is an ongoing process—one that pays off in the form of trust, repeat business, and a robust, resilient operation. Quality isn’t just about compliance; it’s about creating value for both your clients and your own business, paving the way for sustained success in the dynamic world of manufacturing.
By: Jared Haw
Join our newsletter to receive a weekly portion of news, articles, and tips about OpenBOM and our community.