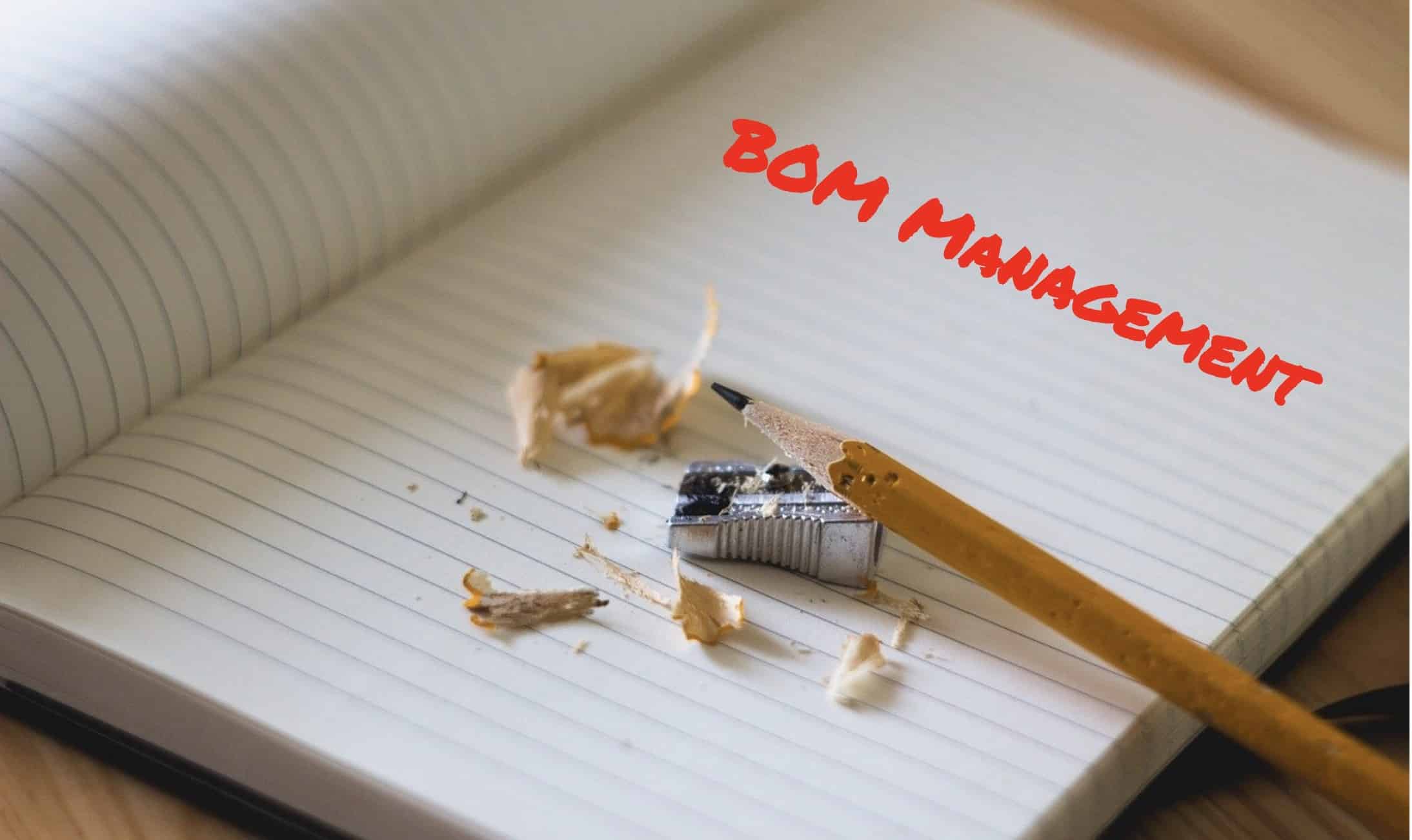
The bill of materials is something that often considered a simple thing. After all, what can be complex in a list of parts? However, as we can see in practice, manufacturing companies are usually underestimating the complexity and fail to manage it properly. The results are usually very painful and coming faster than you can think – missed components, wrong cost estimation, delayed product deliveries, and frustrated engineers and customers running around trying to figure out where is the last and most updated bill of materials.
In modern product development, the Bill of Materials represents a complex multi-disciplinary information structure combining mechanical, electronic, software, and system information. Openness and simplicity are the main drivers to help companies to get up to speed with data management science behind the Bill of Materials. It should be easy to create a Bill of Materials and manage all aspects of it.
What is the Bill of Materials or Product Structure?
The Bill of Materials is a structure representing all items needed to make a product. Depending on the product and business it includes a different level of details about how the product is engineered, manufactured, assembled, sold, and maintained. Every engineering and manufacturing business should be concerned if parts and assemblies, as well as any other related data, are not managed properly.
Who needs BOM?
Everyone needs BOM in the engineering team and manufacturing company. Here is a simple breakdown of why everyone needs a BOM and what specific needs are demanded by different people and teams. Additionally, quickly changing markets are friendly to product development and life cycle management. Simply because product information is a foundation of design, planning, and manufacturing and careful management of it is required.
Product Development needs to track the information about the product to manage what is needed and what is a possible impact from changes.
Manufacturing planners need to have a BOM to organize production planning and assembly processes.
Procurement usually needs BOM to make cost estimation and find the best suppliers and contractors.
Sales usually need a Bill of Materials for sales configurations and features in the products.
Dependent on the type of manufacturing – Engineering to Order, Configure to Order or Build to Stock sales need BOM for different reasons including order details, forecasts or project management.
Support and Maintenance need BOM to know exactly what was sold to the customer, how to maintain it and how to manage the ordering of spare parts.
What to include in BOMs?
A very simple answer to this question is EVERYTHING. The idea of not having something in a BOM is bad and to hope that you will remember what is needed is a recipe for disaster. Very often, we’ve been asked about what is a typical data set of Bill of Materials. Here is a quick summary of what I think is absolutely essential.
Part Number: This is a unique string that identifies every single component in the product. Not all part numbers are the same. You probably heard about OEM, Manufacturing, Suppliers, and many other part numbers. Those are additional pieces of information. You might not use all of them. But, to have a unique Part Number for every single item is a must to have to keep things organized.
Description: It usually gives the organization a simple way to look at the details about parts and components. Used for search, simple identification Description is not unique and must not be used to reference parts for any purposes except human interaction. Part Number is used for everything else.
Part Name: Names make it easier for organizations to track components. Many systems have internal names with specificity useful to Operations, Test, and Engineering teams. A separate nomenclature might be with customers in Sales organizations. Unlike part numbers, part names aren’t necessarily unique. Consistent use of part names like connector, adapter, and cable, can help keep everyone on the same page.
Unit of Measure: A very important piece of information that helps to identify how to measure the quantity of the part.
Type (s): Usually absorbs the different types of information to classify part of help to identify how to manage the part. Organizations can apply multiple types to classify parts and how data about part can be processed.
Revision and Phase: This is used to identify the level of maturity and specific changes. Companies are using various practices when to create new part numbers of revise existing parts.
In addition to these parameters, organizations are usually including information about manufacturers, suppliers, cost,s and other pieces of data in BOMs.
Part vs Usage of the Part (instance).
The information I mentioned above is usually the same about the item (part, purchased assembly). However, another group of information is typically included in BOMs and it represents a specific part usage.
Quantity: it is the ultimate way to say how many pieces of the part you need in this product. Note, in some cases (instance BOM), quantity can be only calculated.
Reference Designator: Typically used in the electronic Bill of Materials usually represents a uniquely identified instance of the part (assembly).
Location: It is typically used in mechanical BOMs to differentiate between instances of the part/ assembly.
Effectivity
A very important element of the Bill of Materials. Effectivity is usually representing specific characteristics saying if a part (or assembly) can be used and under what conditions. There are different types of effectivity – date, configuration, serial number.
Configurations, Configured vs Resolved BOM
Last, but not least piece of information is related to complex products having multiple configurations. A BOM that contains information about multiple configurations usually called “configured BOM” and the BOM that represents information about a single configuration is called resolved.
SIngle-level, Multi-level, Flattened.
A list of components represented as one level is usually the basic way to plan the BOM. However, components are connected into assemblies and those usually have sub-assemblies. This is a simple single-multi-level structure. A flattened BOM is a report that summarizes the usage across multiple levels.
BOM Data Management
Flexibility and the ability to configure applications are two main things for engineers and manufacturing to work with Bill of Materials, Catalogs, Vendors and Order planning.
Therefore to have a robust data model to support the Bill of Materials data management is very important. It’s called the reference-instance model. The idea of this model is to create a granularity around two elements Item reference, Itema Instance and Bill of Materials.
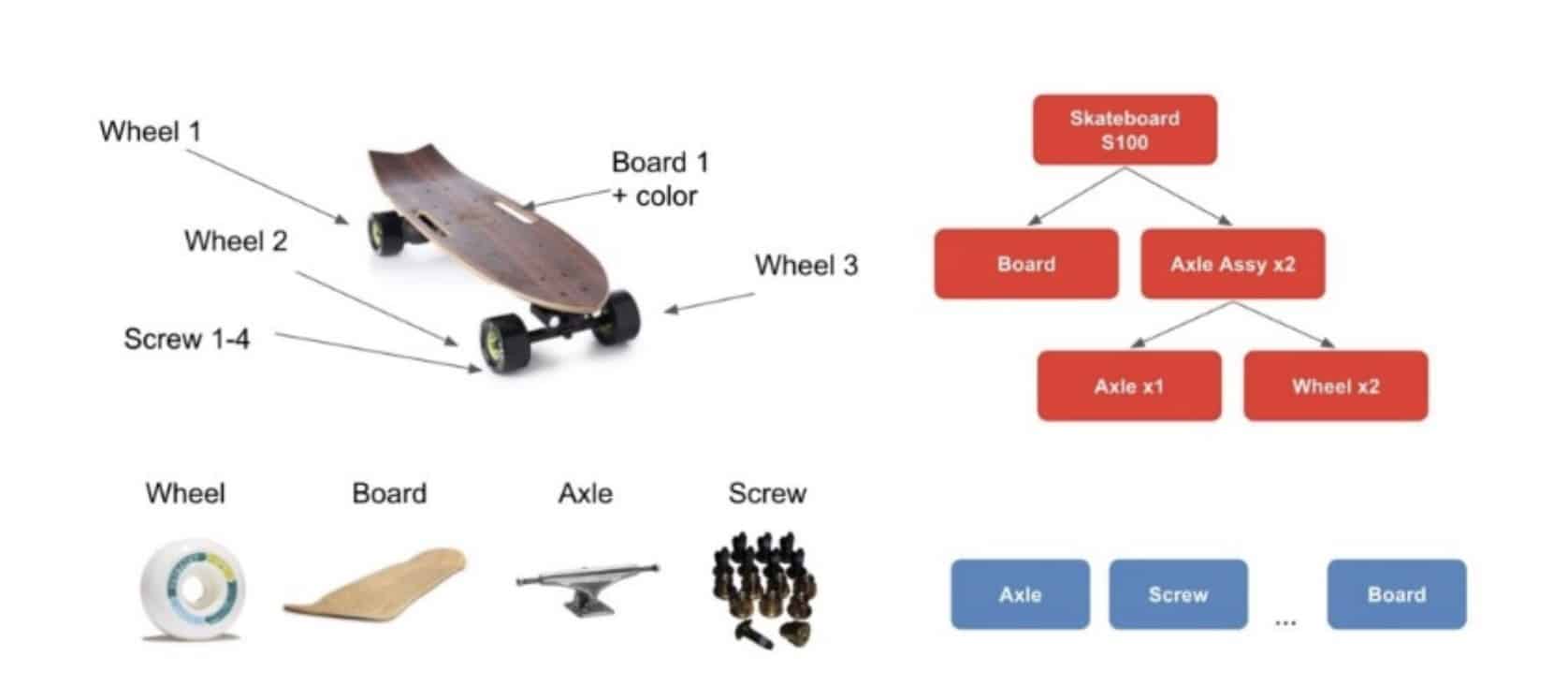
Think about a simple skateboard in the picture below. You can think about a collection of items (components) that are available to build a product – wheels, boards, axles, screws, etc. You can build multiple products from the set of components. Think a skateboard is one of them.
A reference is an abstract object that can be modeled in OpenBOM. This object has a set of properties and represents any part, assembly, or component (terms are sometimes different in different companies). I prefer standard and engineering parts. However, if you have a better name, please let me know.
So, reference can be a nut, a bolt, a screw, an electric motor, or any piece of equipment you buy, manufacture, or outsource. OpenBOM is using catalogs to define references and configure data properties.
An instance is an actual part used in a specific product (engineering product or built product) or an entire product you build. So, if you create a skateboard, which has 4 wheels, then you have 1 reference of a wheel and 4 instances of a wheel.
A picture below shows how data is managed in OpenBOM to support Reference-Instance Model.
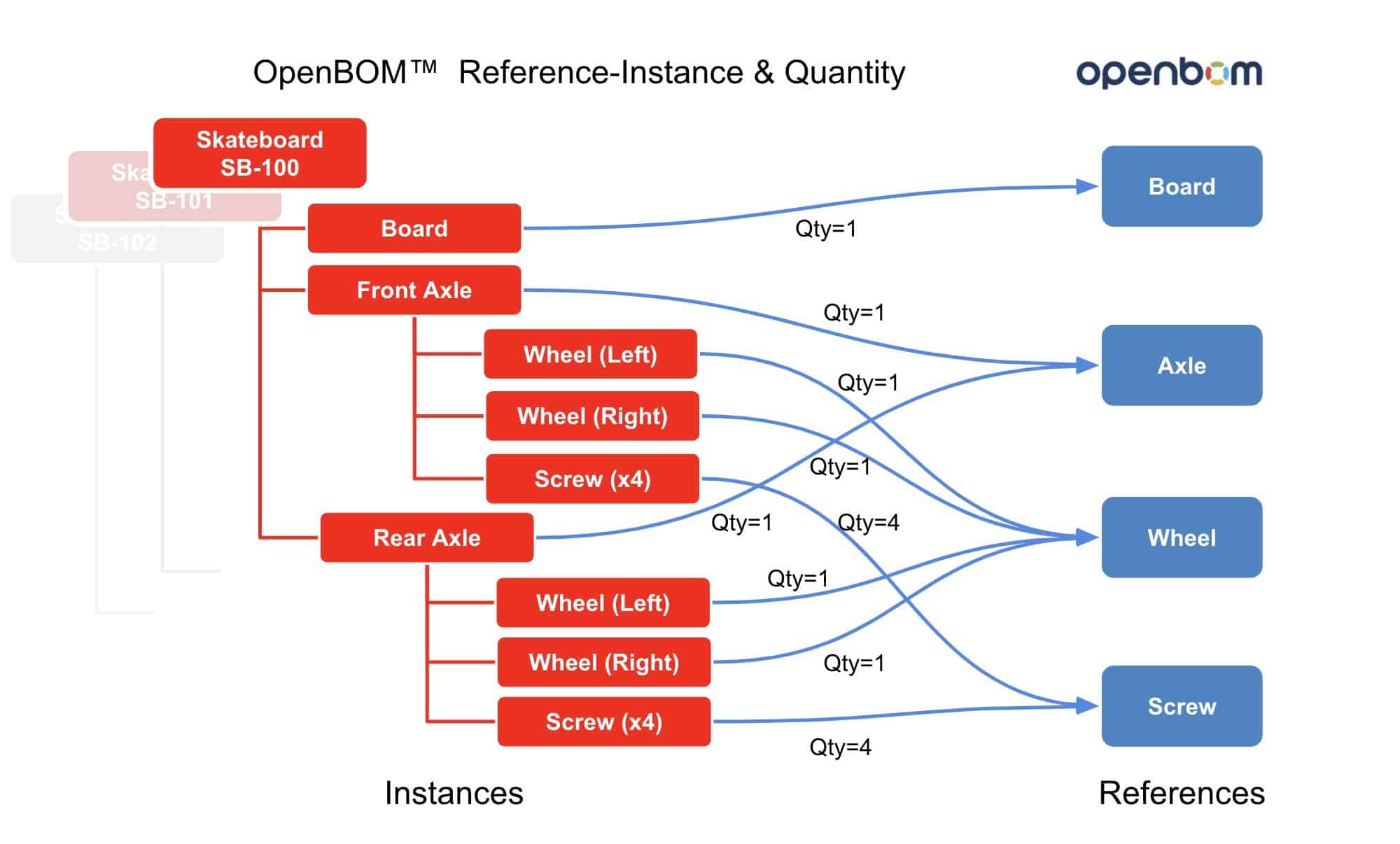
As you can see in the picture, references are represented as nodes, while instances are represented as links. OpenBOM allows you to create and customize properties on both reference and instance model. As an example, you can add a property to a catalog (Eg. Cost) and all Items of this catalog will get this property immediately regardless of what BOM this item is used. At the same time, you can add instance property (eg. Reference designator) to a BOM, which will be only used for electronic BOMs and won’t be available and used for mechanical parts. Bottom line – you can define any product data using this model.
Properties are building blocks of information. You describe any characteristics of the product using properties of different types – text, numbers, references, cost, lists, date, etc.
BOMs and Items (Catalogs)
These are two fundamental elements of the BOM information model. Here is the example of OpenBOM – Catalog(s) are used to store information about Items and BOM are used to create a structure of item instances. The following picture gives you an idea of how it works.
How to set up a BOM management system
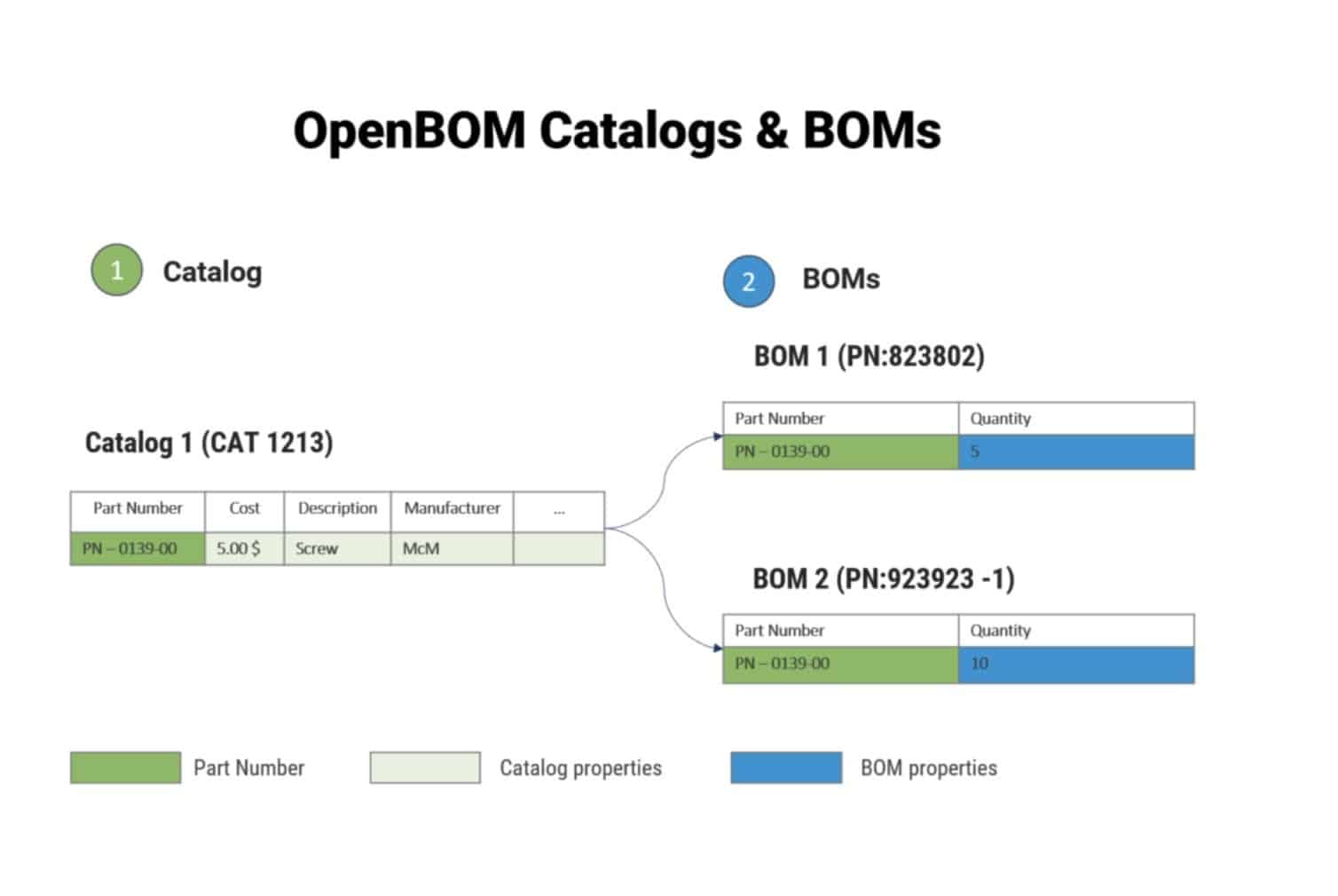
You need to have some planning made before you start to manage the Bill of Materials. Don’t try to “figure it out as you go”. It usually ends badly. Therefore our recommendation to have some planning time to figure out what is needed for your organization and how to manage it using OpenBOM. Complete flexibility will give you full control over the Bill of materials and related tasks.
Conclusion
Bill of Materials will play a key role in the organization of information about a product, product development, and manufacturing process. To have the information organized in the right is a foundation of various business processes – change management, cost management, production planning, procurement, and many others.
OpenBOM provides free registration and an on-demand free 14-days trial to explore all system features and functions. REGISTER TODAY.
Best, Oleg @ openbom.com
Want to learn more about PLM? Check out my Beyond PLM blog and PLM Book website. Read OpenBOM customer reviews on G2 Crowd to learn what customers are saying about OpenBOM.
Join our newsletter to receive a weekly portion of news, articles, and tips about OpenBOM and our community.