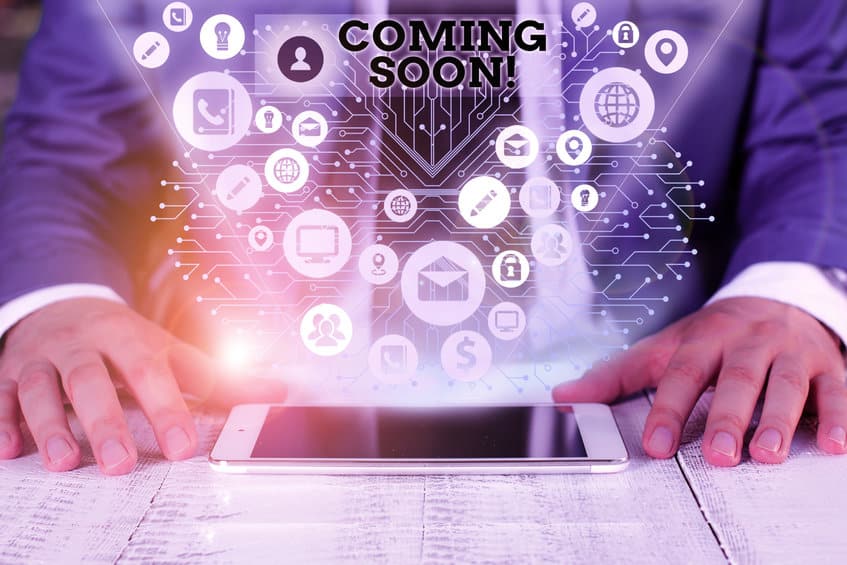
Whether you are launching your first product or expanding a product line for a fortune 500 company, there is one similarity. This similarity is improving your new product introduction (NPI) process.
Carrying out a successful NPI will provide you and your company with multiple advantages. However, with changing trends, evolving technologies, and, more, it is hard to stay ahead of the competition. The only process that can keep you ahead of your competition chasing you is by the way you bring products to life. And as we know, this way is evolving.
The goals of launching a new product remain the same as they have been.
The main goals of NPI are:
- More Cost-effective development
- Quicker speed to market
- Higher customization
- A product that can be made repeatable in production
While the final NPI goals remain the same, the tools and software used to execute these goals have evolved. If you are on a team responsible for bringing a new product to life, you need to focus on the following:
Say Goodbye To Outdated Software
The most common software you should part ways with would be excel and spreadsheets. While they do serve a purpose and I use them myself, they serve no purpose to manage your engineering data that goes into bringing a product to life.
During an NPI process, there will be multiple changes, the first version is never the final one. Your product will go through multiple revisions and parts will constantly change. As we know, the only constant is change.
As your product matures, you will bring in additional partners, such as your contract manufacturing partner. Managing your parts in Excel while making multiple revisions per part leads to mistakes.
Constantly updating and sending out excel spreadsheets will lead to multiple problems. If you are using Excels or Spreadsheets then expect the following:
- A longer and more drawn-out development speed.
- More frequent mistakes that should have been avoided.
- Use of time to manually update spreadsheets and updates.
- Forgetting to email the most recent revision, BOM, 3D drawing, specifications to your team, stakeholders, supplier, or other contractors.
Embrace Remote Work
One of the biggest changes introduced by COVID is working remotely. Whether you like it or not, remote working is most likely here to stay. And since we respect and appreciate our remote workers, we need to adjust our infrastructure for them.
Something else that is introduced with remote working is the idea that talent can be found anywhere. Previously, you needed to find someone local or someone willing to relocate to the necessary city. Sometimes this resulted in losing good prospects because they were not willing or unable to relocate.
Working remotely has made it so you can hire and work with the best team no matter where they are.
The issue that comes up with this is how to share your data with other colleagues or partners that might not be in the same, city, state, or country as you are. If you are still using spreadsheets or excels, you will find it difficult to keep everyone on the revisions and BOM.
How To Add More Partners
As your product matures, you will bring in additional partners. The most common partner you will bring in will be your contract manufacturing or other supply chain partners. My main purpose in bringing these suppliers on early is to support you with design for manufacturing (DFM).
The goal of DFM is to optimize your product for production. During this step, there will be multiple changes affecting your product to optimize assembly, fabrication of the part, and overall tooling.
Bringing in a new contractor or supplier who will collaborate with you on optimizing your product will lead to further confusion. Thus managing your data properly becomes more and more important so nothing gets lost or nothing gets changed that should not be changed.
In the new era of NPI, having a single source of truth becomes crucial to fulfilling your NPI goals
Conclusion and How OpenBOM Can Help
OpenBOM offers the infrastructure and workflows to manage parts, revisions, BOMs, and changes from NPI to mass production. We believe engineering, supply chain, and manufacturing teams should be able to seamlessly manage their parts, vendors, bill of materials, purchase orders, and change orders. All BOM, engineering, and manufacturing information are stored in the cloud which you can share with your team, contractors, suppliers, or anyone else that has access to your account.
OpenBOM keeps everyone on the same BOM while providing you with the tools to streamline your development to production & scale up operations.
To get an inside look at how OpenBOM works, Register for your free 14-day trial and get access to all of our features.
Best,
Jared Haw
Join our newsletter to receive a weekly portion of news, articles, and tips about OpenBOM and our community.