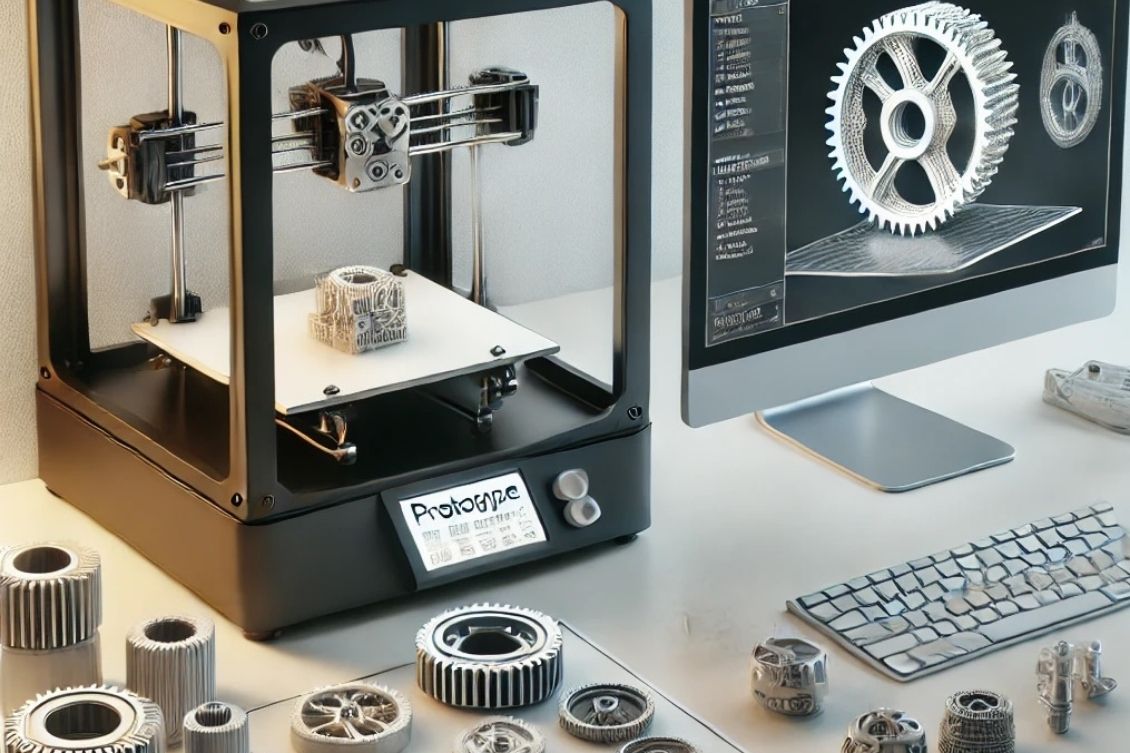
Design for Manufacturing (DFM) is a critical step in product development, ensuring that a design is optimized for efficient and cost-effective production. However, making the right decisions during DFM requires more than just engineering expertise. It requires clear traceability, structured change management, and a reliable historical record of design iterations. This is where a Bill of Materials (BOM) becomes essential and must not be forgotten about during development.
A BOM is more than just a list of parts; it serves as the single source of truth for tracking every component, material, and subassembly throughout the design process. By integrating the BOM during DFM, teams can maintain a transparent development process, efficiently manage change requests, and store historical data for future reference. In this blog, we’ll explore why a BOM is a crucial tool in DFM and how it helps manufacturers streamline their workflows while reducing costly errors.
The BOM Ensures Traceability During the Development Process
During the DFM process, keeping track of design iterations and component choices is crucial. A BOM provides a structured, detailed record of every part used in a product, ensuring full traceability from prototype to production. Without a BOM, teams can quickly lose visibility into which components were used, what changes were made, and how those modifications impact manufacturability.
A well-organized BOM allows engineers and manufacturers to:
- Track Component Usage: Every part, material, and subassembly is documented, ensuring that teams always know which components are included in a particular version of the product. This eliminates guesswork and reduces the risk of using outdated or incorrect parts.
- Monitor Design Changes: As modifications occur during DFM, the BOM acts as a historical reference, recording which components were changed, when, and why. This allows teams to compare different iterations and make informed decisions based on past revisions.
- Improve Collaboration Across Teams: A centralized BOM ensures that engineers, manufacturers, and suppliers are all working with the same up-to-date information, reducing miscommunication and improving coordination.
- Identify and Resolve Issues Quickly: If a manufacturing or performance issue arises, teams can refer to the BOM to pinpoint the affected components and trace potential sources of the problem. This helps streamline troubleshooting and minimizes production delays.
Without a BOM, teams may struggle to trace which version of a design was used, leading to confusion, costly mistakes, and delays in production. By ensuring clear traceability, a BOM helps maintain consistency, accountability, and efficiency throughout the DFM process, ultimately leading to smoother product development and a more reliable transition from prototype to full-scale manufacturing.
The BOM Simplifies the Approval of Change Requests
DFM is an iterative process that often requires multiple design revisions based on manufacturing constraints, material availability, and cost considerations. Without a structured system in place, managing these changes can become chaotic, leading to confusion, miscommunication, and costly errors. This is where the BOM plays a crucial role in simplifying the approval and management of change requests.
A well-maintained BOM ensures that every design modification is documented, tracked, and approved before implementation. Here’s how it helps:
- Standardizes the Engineering Change Order (ECO) Process: A BOM serves as a central reference for all component-related changes, ensuring that every modification follows an established approval workflow before being incorporated into the design.
- Prevents Miscommunication: Since multiple teams, including engineering, procurement, and manufacturing, rely on design data, having a BOM ensures that everyone works with the most up-to-date information. This minimizes the risk of using outdated parts or incorrect specifications.
- Speeds Up Change Approvals: When a change request is submitted, stakeholders can quickly reference the BOM to understand the impact of the proposed modification on cost, lead time, and compatibility. This enables faster decision-making and avoids unnecessary delays.
- Improves Regulatory and Quality Compliance: Many industries require strict documentation of design changes for compliance and quality assurance. A BOM provides a clear audit trail that records when changes were made, who approved them, and why they were necessary.
Without a BOM, design changes can become disorganized and difficult to track, leading to unapproved modifications, production delays, and unexpected costs. By using a BOM as a structured system for managing change requests, companies can maintain control over their designs, streamline approvals, and ensure that all modifications are well-documented and properly executed.
The BOM Stores Historical Data for Future Reference
In the fast-paced world of product development, having access to historical data is invaluable. The BOM serves as a detailed record of every design iteration, ensuring that teams can look back at past versions, analyze changes, and make informed decisions for future projects. Without a structured way to store this information, valuable insights can be lost, leading to redundant work, design inconsistencies, and inefficiencies.
A well-maintained BOM provides several key benefits when it comes to historical data storage:
- Preserve Design Iterations: Every version of the product, from initial prototypes to final production models, is documented in the BOM. This allows teams to revisit previous designs, compare component choices, and understand why specific changes were made.
- Facilitates Troubleshooting and Quality Control: If a product experiences performance issues or failures, having a historical BOM enables engineers to trace back to earlier versions and identify potential causes. This is especially useful in regulated industries where maintaining a clear audit trail is essential.
- Improves Future Product Development: Lessons learned from past designs can directly influence future projects. By analyzing previous BOMs, teams can identify successful component choices, avoid known issues, and streamline the development process for new products.
- Enhances Supplier and Manufacturing Coordination: A historical BOM provides insight into past procurement and manufacturing decisions. This helps teams make better sourcing choices, compare pricing trends, and negotiate with suppliers based on previous orders.
Without a BOM, teams risk losing critical design history, making it difficult to track why certain decisions were made or how past issues were resolved. By maintaining a comprehensive historical record, a BOM ensures that product development remains organized, traceable, and data-driven, ultimately leading to better decision-making and more efficient manufacturing processes.
Conclusion
A BOM is more than just a list of parts—it is a critical tool for ensuring a smooth and efficient DFM process. By integrating a BOM early in product development, teams can maintain traceability, streamline change management, and preserve historical design data for future reference.
With a well-structured BOM, engineers and manufacturers can track every component, ensure that design changes follow a clear approval process, and access past iterations to make informed decisions. This level of visibility and control not only reduces errors and miscommunication but also improves overall efficiency, making it easier to transition from prototype to full-scale production.
Ultimately, a BOM bridges the gap between engineering and manufacturing, helping teams stay organized, reduce costs, and bring high-quality products to market faster. If you’re not leveraging a BOM in your DFM process, now is the time to start—because better data leads to better manufacturing decisions.
By:
Jared Haw
Join our newsletter to receive a weekly portion of news, articles, and tips about OpenBOM and our community.