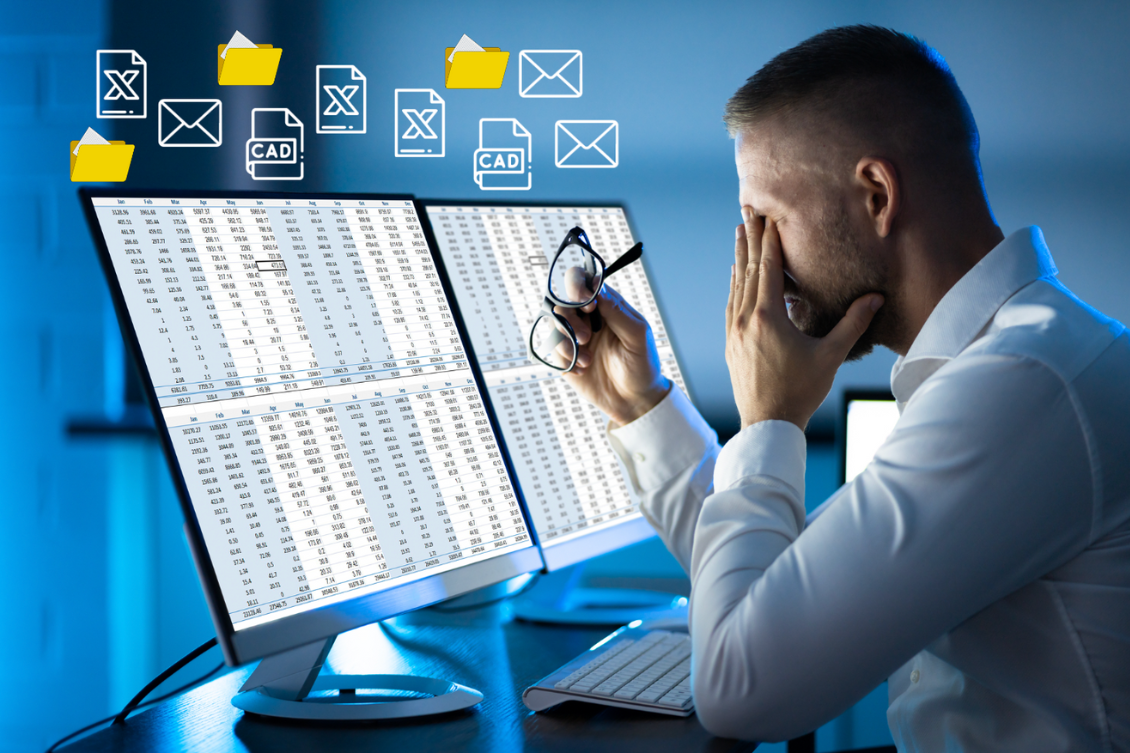
Getting your product from concept to reality often means working closely with a contract manufacturer (CM). Sharing detailed product data is crucial to ensure everyone is on the same page and things run smoothly. Yet, many manufacturers still rely on spreadsheets to pass this vital information back and forth.
Let’s be honest: spreadsheets are great for quick calculations or simple lists, but when it comes to sharing complex product data with your CM, they fall short in many ways. From data inaccuracies and version control headaches to security risks and integration nightmares, spreadsheets can create more problems than they solve.
In this blog, we’ll dive into the risks of using spreadsheets for data sharing and explore how OpenBOM can provide a much-needed upgrade to streamline and secure your data-sharing process.
The Risks of Sharing Data via Spreadsheets
Using spreadsheets to share product data with your CM might seem convenient, but it’s a bit like using a rubber band to hold a car together—it might work for a while, but it’s not exactly reliable. Here are some of the major risks you face when relying on spreadsheets for this critical task.
Data Inaccuracy and Errors
One of the biggest headaches with using spreadsheets to share product data is the high risk of data inaccuracy and errors. There are two reasons for this:
Manual Entry Errors: Spreadsheets rely heavily on manual data entry, and let’s face it, everyone makes mistakes. A simple typo in a part number, quantity, or specification can snowball into major issues down the production line. Imagine sending your CM the wrong dimensions for a crucial component—they produce a batch of parts that don’t fit, and now you’ve got delays, increased costs, and a lot of frustration on both sides.
Version Control Issues: When multiple people are working on the same spreadsheet, keeping track of the latest version becomes a nightmare. You might have “final_version_v3” and “final_final_version_v4” floating around, and before you know it, someone’s using outdated data to make decisions. This kind of mix-up can lead to miscommunication, duplicated efforts, and ultimately, more errors.
Spreadsheets simply aren’t built to handle the complex, collaborative nature of manufacturing data. The more people involved, the higher the risk of inaccuracies and errors, which can lead to costly production mistakes and strained relationships with your CM.
Lack of Real-Time Updates
Another significant downside of using spreadsheets to share product data is the lack of real-time updates. This issue can cause delays and inefficiencies that impact the entire production process.
Delayed Information: Spreadsheets don’t update in real-time, meaning any changes made by one party aren’t instantly visible to others. Let’s say you update a part specification and email the new spreadsheet to your CM. By the time they receive and open it, they might have already started working based on the old data. This lag can lead to decisions being made on outdated information, causing delays and potentially costly mistakes.
Inefficient Collaboration: When you have multiple team members needing to access and edit the data, spreadsheets become cumbersome. Only one person can typically edit a spreadsheet at a time, meaning everyone else has to wait their turn. This not only slows down the workflow but also increases the risk of miscommunication and errors. Plus, keeping track of who made what change and when can be a logistical nightmare.
The inability to collaborate in real-time means you’re always playing catch-up, trying to ensure everyone is working with the most current information. This inefficiency can hamper your ability to respond quickly to changes and challenges, ultimately affecting your productivity and bottom line.
Integrated Data Ecosystem
Spreadsheets are notorious for creating information silos. This lack of integration with other systems can severely hamper your ability to get a comprehensive view of your production process. Here’s how spreadsheets fall short and how OpenBOM can help.
Siloed Information: When using spreadsheets, data often gets trapped in isolated documents that don’t communicate with each other. You might have different spreadsheets for inventory, production schedules, and part specifications. Keeping all these documents updated and synchronized is a monumental task. Important information can get lost in the shuffle, leading to misinformed decisions and inefficiencies.
Inconsistent Data: Manually transferring data between spreadsheets and other systems like ERP (Enterprise Resource Planning) increases the risk of inconsistencies. Each time data is manually entered or copied, there’s a chance for errors. These discrepancies can cause confusion and require time-consuming corrections, delaying the production process and affecting the quality of your products.
Using spreadsheets might seem like a simple solution, but the lack of integration can create significant roadblocks in your manufacturing operations. OpenBOM offers an integrated data ecosystem that streamlines your workflow, ensures data consistency, and enhances collaboration, ultimately leading to a more efficient and effective production process.
How OpenBOM Solves These Issues
Given all the risks and headaches associated with using spreadsheets for sharing product data, it’s clear that a more robust solution is needed. OpenBOM offers exactly that. Here’s how OpenBOM can transform your data-sharing process, making it more accurate, efficient, and secure.
Accurate and Error-Free Data Management
When it comes to managing and sharing product data, accuracy is paramount. Even small errors can lead to significant issues down the line, from production delays to increased costs. Here’s how OpenBOM ensures that your data is accurate and error-free.
- Reduction of Human Error: OpenBOM automates the data entry process, which dramatically reduces the risk of human error. Instead of manually typing in part numbers, quantities, and specifications, OpenBOM pulls this data directly from your design files and other integrated systems. This automation ensures that the data is entered correctly the first time, eliminating the typos and mistakes that can occur with manual entry.
- Single Source of Truth: OpenBOM stores all your product data in a centralized location, creating a single source of truth. This means there’s only one version of each document or data set, and everyone involved in the project can access the most up-to-date information. This centralization prevents the confusion that arises from multiple versions of the same spreadsheet floating around.
- Automatic Updates and Tracking: Any changes made to the data are automatically updated and tracked in OpenBOM. This tracking system not only ensures that the latest information is always available but also provides a clear history of changes. You can see who made what changes and when, making it easier to audit and verify data.
- Elimination of Duplicate Data: With OpenBOM, there’s no need to create multiple copies of the same data. This eliminates the risk of having duplicate or conflicting information, which is a common problem with spreadsheets. Everyone works from the same data set, ensuring consistency and reliability.
Real-Time Collaboration
In the dynamic world of manufacturing, the ability to collaborate in real-time is essential. Delays and miscommunications can lead to costly mistakes and inefficiencies. Here’s how OpenBOM enhances real-time collaboration, ensuring your team and your CM are always in sync.
- Live Data Synchronization: OpenBOM updates data in real-time, meaning any changes made are immediately visible to all stakeholders. Whether it’s a design tweak, a change in part specifications, or an update to the bill of materials, everyone involved gets instant access to the latest information.
- Live Access and Editing: Multiple users can access and edit data simultaneously in OpenBOM. This feature is crucial for collaborative efforts where different team members need to contribute their expertise. Instead of waiting for one person to finish before another can start, everyone can work together in real-time.
- Shared Access with Permissions: OpenBOM allows manufacturers to share specific data sets with their CMs, with customizable permissions. This means your CM can access the data they need while you retain control over sensitive information. It fosters a collaborative environment without compromising security.
Integrated Data Ecosystem
Spreadsheets are notorious for creating information silos, where data is isolated and disconnected from other systems. This lack of integration can severely hamper your ability to get a comprehensive view of your production process. Here’s how OpenBOM transforms your data-sharing process into an integrated data ecosystem.
- Disconnected Systems: When using spreadsheets, data often gets trapped in isolated documents that don’t communicate with each other. You might have different spreadsheets for inventory, production schedules, and part specifications. Keeping all these documents updated and synchronized is a monumental task. Important information can get lost in the shuffle, leading to misinformed decisions and inefficiencies.
- Limited Accessibility: Spreadsheets stored on individual computers or shared via email are not easily accessible to everyone who needs them. This limited accessibility can slow down decision-making and impede collaboration, especially when team members are working remotely or across different locations.
- Enhanced Collaboration: By integrating with other systems, OpenBOM facilitates better collaboration among teams. Everyone has access to the same accurate data, making it easier to coordinate efforts and maintain alignment throughout the production process.
- Real-Time Synchronization: OpenBOM ensures real-time synchronization of data across all integrated systems. Any updates or changes made in one system are instantly reflected in OpenBOM and other connected platforms. This real-time synchronization keeps everyone on the same page and reduces the risk of working with outdated information.
- Elimination of Redundancies: With a single, integrated data ecosystem, OpenBOM eliminates redundant data entries. This streamlining reduces the risk of errors and ensures that everyone is using the same, accurate data. It also saves time and effort, as there’s no need to update multiple spreadsheets manually.
Using spreadsheets might seem like a simple solution, but the lack of integration can create significant roadblocks in your manufacturing operations. OpenBOM offers an integrated data ecosystem that streamlines your workflow, ensures data consistency, and enhances collaboration, ultimately leading to a more efficient and effective production process.
Conclusion
When it comes to sharing product data with your CM, relying on spreadsheets can be more trouble than it’s worth. The risks of data inaccuracies, version control issues, security concerns, and integration problems can lead to costly delays, production errors, and frustrated teams.
With OpenBOM, you get accurate, error-free data management, real-time collaboration, and a connected data ecosystem that keeps everyone aligned and informed. This leads to more efficient workflows, fewer mistakes, and a stronger partnership with your contract manufacturer.
If you’re tired of the headaches that come with spreadsheets and ready for a more reliable and effective way to manage your product data, it’s time to make the switch to OpenBOM. Experience the benefits of a streamlined, integrated approach and see how it can transform your manufacturing operations.
By: Jared Haw
Join our newsletter to receive a weekly portion of news, articles, and tips about OpenBOM and our community.