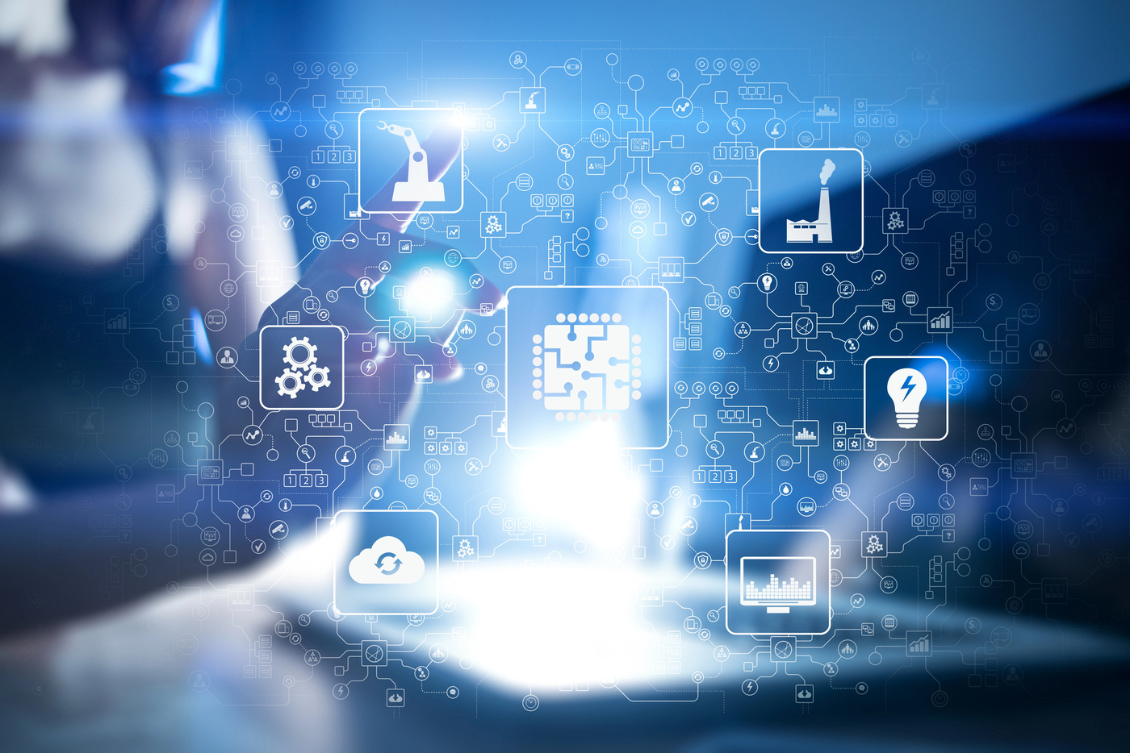
In today’s competitive landscape, manufacturing companies are increasingly looking to make the shift toward digital operations. The drive towards digitalization is not just a trend but an essential strategy for staying ahead in a world of complex products, B2B customer demands, and intricate supply chains. A connected factory floor, where machines communicate seamlessly, and a streamlined, connected supply chain are critical components of this digital transformation. But where is the problem?
The Data Dilemma: Why Excel is Still the King
Despite the push towards digitalization, many manufacturing companies still struggle with data inefficiency. The way data is managed can significantly impact the future potential of any business. At the heart of all manufacturing processes is data, and specifically, the Bill of Materials (BOM)—in fact, multiple BOMs (xBOMs), including engineering BOMs, manufacturing BOMs, procurement BOMs, sales BOMs, and more. Unfortunately, the way many companies handle this data is far from efficient.
There is a significant gap in how data is currently used and the opportunities it presents for future optimization. Data is not used efficiently and Excel is still the king, which impacts future business opportunities. Here is how it works. The lifeblood of all manufacturing processes is data. And BOM (Bill of Materials), actually multiple Bill of Materials (xBOM, such as engineering BOM, manufacturing BOM, procurement BOM, sales BOM, etc) are part of the process. Unfortunately, the way many customers are dealing with the data is still very inefficient. According to the article Manufacturing 2030 and white paper Data Mastery: A Key to Industrial Competitiveness there is a big gap in how data is used and future opportunities to optimize the processes based on the data.
One of the biggest challenges? Spreadsheets. Despite the advanced technologies available, 70% of manufacturers still rely on manually entered data in spreadsheets, and 68% use them to analyze this data. While 44% of manufacturing leaders report that the amount of data they collect has doubled in the past two years, with expectations that it will triple by 2030, there is still a heavy reliance on outdated methods like Excel. Most troubling, less than half of manufacturers have a solid understanding of the dollar value of their data, and only 25% are confident that the right data is being collected.
However, the data shows a silver lining: 95% of manufacturers acknowledge that data drives faster and higher-quality decision-making. The challenge lies in harnessing this data effectively, and that’s where the digital BOM comes in.
Data as the New Capital: How a Digital BOM Lowers Manufacturing Costs
Data is rapidly becoming the new capital in manufacturing, with the potential to reverse the recent decline in the industry. According to the Forbes article – Data As The New Capital In Manufacturing, data can have a profound impact on reversing the recent decline in the manufacturing industry.
Automation has significantly reduced the need for human labor, especially as machines become more sophisticated and capable of performing a broader range of tasks. This shift has decreased the demand for low-cost labor, leading to a reduction in manufacturing jobs, especially visible in Asia.
However, automation brings with it a critical requirement: data. While humans can work with Excel spreadsheets, automation systems cannot. They require BOMs and related product information to be available in a digital form that can be easily used by automated processes. Here are three reasons why the role of digital data, particularly a digital BOM, will continue to grow in manufacturing:
- Efficiency and Productivity: Digital BOMs allow for better efficiency and productivity by ensuring that the right data is available at the right time, in the right format, and to the right people or systems.
- Cost Reduction: By optimizing processes through data-driven insights, companies can reduce costs, minimize downtime, and prevent costly mistakes or equipment breakdowns.
- Innovation: A digital BOM fosters innovation by enabling better product design and development through the analysis of real-time data from manufacturing processes, customer feedback, and field performance.
The Imperative for Digital Transformation in Discrete Manufacturing
The discrete manufacturing sector, facing unprecedented challenges from megatrends, evolving customer demands, and new competitors, is at a crossroads. The EY research – Is your digital strategy fit for the manufacturing future shed the lights on how discrete manufacturing can be more competitive in the future. Here is an interesting summary I capture from EY article:
According to research by EY, digital data is a mandatory prerequisite for transformation in this sector. Discrete manufacturers must leverage digital data to stay competitive, improve operational efficiency, and develop new business models that align with future market needs.
The complexity of digital transformation can be overwhelming, especially for large enterprises with diverse operations. However, breaking down the digital strategy into manageable components—such as reimagining the business model, transforming assets and solutions, and shifting digital operations—can make the process more approachable and effective.
Two significant trends affecting discrete manufacturers are the (1) increasing access customers have to data (including supply chain customers) and (2) the rise of cloud manufacturing solutions (which will make all B2B services connected). Customers now have access to more data across their value chains, challenging traditional suppliers. Meanwhile, cloud manufacturing platforms are transforming how components and assemblies are ordered, offering instant quotes and reducing lead times.
OpenBOM strategy is aligned with the demand to embrace digital transformation. Many innovative manufacturing companies are using OpenBOM to switch from traditional Excel-like and document drive approaches towards digital transformation, digital models, and the core of OpenBOM innovation – multi-tenant product knowledge graph. .
To remain competitive, discrete manufacturers must embed digital data into every aspect of their operations. The growing importance of data analytics, cloud computing, and connected technologies offers new avenues for growth but also increases the risk of disruption by more agile, tech-savvy competitors. Digital data is not just a tool for incremental improvement; it’s a fundamental enabler of transformation.
Conclusion: Embrace Digital BOMs for Future Success
The journey towards digital manufacturing demands a robust digital data foundation. This foundation allows manufacturers to analyze, optimize, and predict future business and technological operations, shortening design-to-RFQ time, optimizing machine workloads, and identifying supply chain challenges before they happen. Managing data with Excel spreadsheets and files in folders won’t suffice in the digital age.
Now is the time to rethink your digital foundation, and OpenBOM is the modern platform that can help you make this transition gradually, ensuring the fastest ROI.
REGISTER FOR FREE and schedule a call with OpenBOM experts to discuss your digital BOM strategy.Best,
Oleg
Join our newsletter to receive a weekly portion of news, articles, and tips about OpenBOM and our community.