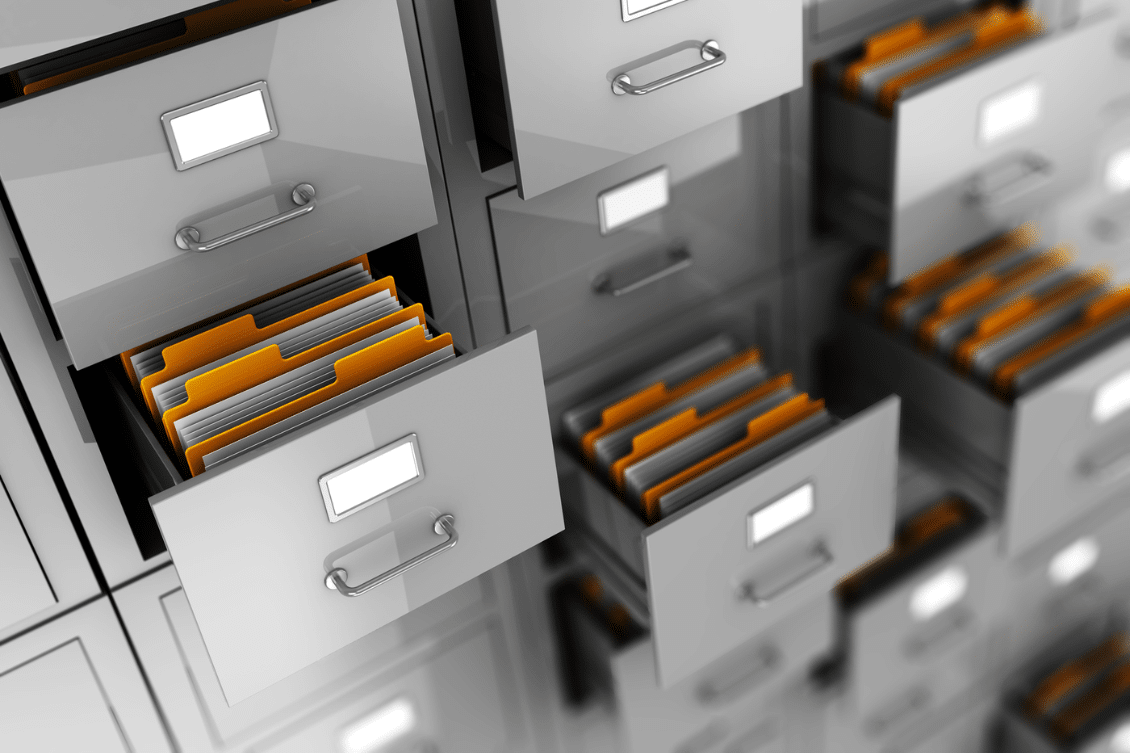
I’d like to continue the OpenBOM painkillers series of articles. If you missed the beginning, navigate here to discover four groups of painkillers delivered by OpenBOM: (1) Engineering Design & Data; (2) Organizing product development process management; (3) data sharing and collaboration; and (4) Flexible integrations. Check the article here.
In my blog today, I’d like to speak about the first one – the inefficiency of engineering data management and capturing data in a single source of truth. In the modern fast-paced world of engineering and manufacturing, data management is a critical aspect of ensuring efficiency and success.
However, for many organizations, product lifecycle management, product data management, CAD data, supply chain (sourcing and vendor) information is not organized as desired. It can be a source of frustration and inefficiency. In this article, we will explore some common pains associated with engineering data management and discuss the importance of addressing these issues for the overall success of engineering and manufacturing projects.
I’d like to speak about 7 areas of inefficiency in engineering and product data management I discovered in manufacturing companies while I was working on OpenBOM implementations.
Not Organized Design Data
One of the most significant challenges in engineering data management is the lack of organized design data, particularly CAD files and their derivatives. Often, these essential files are scattered across various places, local drives, and network/cloud storages, making it difficult to locate, track changes, and view the history of designs. Without a well-structured system in place, engineers and designers may inadvertently work on outdated versions, leading to errors, wasted time, and increased project costs.
Tons of Excels with Parts, Catalogs, and BOMs
Spreadsheets have become the go-to solution for managing parts, catalogs, and Bills of Materials (BOMs) in many engineering organizations. While Excel can be a powerful tool, it is not designed for efficient data management in engineering. Managing data in multiple spreadsheets can lead to data inconsistencies, data fragmentation, version control issues, and a lack of visibility into the entire product structure for both CAD design and Bill of Materials.
Manual Processes for Extracting and Managing Design Data
Another significant pain point in engineering data management is the reliance on manual processes to extract design data and create full product structures. This manual effort is time-consuming, error-prone, and often results in delays in project timelines. Additionally, managing revisions and keeping a comprehensive history of design changes can be challenging without a proper automated system in place. What we learned here is the way a traditional approach works by capturing files, product structure, and all contextual information.
Lack of Single Source of Change
I found many engineering and manufacturing organizations suffer from the absence of data organization in the way that gives everyone access to the data, but at the same time, allows distributed systems, teams, and organization to perform their management and change control process.
While the old idea of a single source of truth suggests that all data will be stored in a single centralized repository, the reality is that providing data for changes and collaboration is much more powerful. The need to distribute access between multiple people and teams is creating a huge problem with information management. This lack of a “single source of information” makes it challenging to access accurate and up-to-date information about what has been ordered, released, and shipped. This can lead to miscommunication, delays in production, and increased costs.
Difficulty in Cost Rollup
I have never seen any manufacturing company that will say that “cost is not important”. But in reality, companies are using Excel to calculate costs and preserve separate spreadsheets for that. Engineering projects often involve complex cost structures, with components and subassemblies contributing to the overall product cost. Without proper data organizations, companies struggle to find all elements of the product cost. And without an easy way to roll up costs, organizations struggle to understand the cost breakdown at various levels of the product structure. This lack of visibility can interfere with cost management and optimization efforts.
Managing Supplier Sources and Alternate Items
In today’s global supply chain, it is essential to manage multiple supplier sources and alternative items for components. But organizing suppliers’ data is hard. There are multiple sources where components or materials can be purchased. Excels and legacy databases provide a poor mechanism to organize this supplier’s information. Without a robust data management system, organizations may struggle to identify and qualify alternate suppliers quickly, leading to supply chain disruptions and delays.
Data Sharing & Distribution Challenges
Engineering data is typically distributed across multiple users, computers, and even different organizations. This distribution can lead to data inconsistencies, security risks, and difficulties in collaboration. Without a structured data management strategy, ensuring that the right people have access to the right information can be a significant challenge.
Conclusion
We’ve been talking to thousands of engineers, manufacturer planners, procurement managers, and managers. Data organization and management is a pain point for many teams and companies involved in engineering and manufacturing projects. The scattered, unorganized nature of design data, reliance on spreadsheets, manual processes, and the absence of a single source of truth all contribute to inefficiencies, errors, and increased project costs.
In today’s competitive landscape, the ability to efficiently manage engineering data is not just a luxury but a necessity for organizations aiming to stay competitive and deliver high-quality products on time and within budget. A PLM software capable of providing a solution to manage engineering data is not a luxury, but a necessity. It connects computer-aided design (CAD) systems, integrates data, and organizes a digital thread of information that can be used in the production process.
REGISTER FOR FREE and check OpenBOM for the next 2 weeks to see how it can help you and your organization.
Best, Oleg
Join our newsletter to receive a weekly portion of news, articles, and tips about OpenBOM and our community.