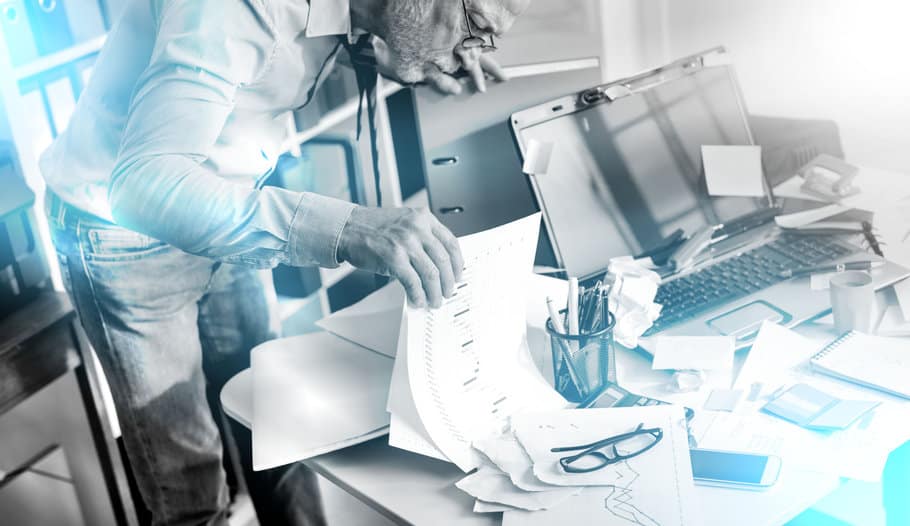
As we all know a low-quality product will cause high costs. The same stands true with your process. If you have a low-quality process then you can also expect higher costs. Most of us are practicing lean manufacturing which looks at eliminating waste, optimizing processes, cutting costs, and more. However, most of us do not look at the importance of managing the bill of materials (BOM) and the effect it has on costs.
One of the most essential piece of information for manufacturing companies is the BOM. If the BOM is not updated, if it is not detailed, or if different departments are working on different versions then you can expect errors, extra costs, and extended lead times in your manufacturing process.
If you do not manage the BOM, have multiple versions floating around, do not update it, and fail to properly share it, you can expect the following:
Material Shortages
We all know there is a chip shortage. Having a BOM that shows the part info from 2 months ago might no longer be relevant. Once your purchasing teams start to procure these parts, you will find out that the price is no longer valid or the lead time is much longer than before. The result is scrambling to find suppliers for alternative components. This leads to other engineering challenges such as updating the firmware. All of these lead to extra costs and potentially create additional errors.
Longer Lead Times
If the lead time for each item is not up to date, you can assume you will be waiting for parts to arrive or you will be waiting longer than expected. This affects everything else downstream. If you are working with a contract manufacturer (CM) then their production and material control (PMC) team will not be able to accurately specify when final assembly can begin. This results in a few other issues:
Holding Inventory
Depending on the environment of the warehouse, holding inventory can potentially harm the goods. Whether you are storing paper for packaging, raw material for further processing, or PCBs, holding onto inventory can be a liability if you don’t have the correct environment.
Higher Overhead Costs
There are costs associated with holding inventory. You need space to store these goods and workers for the warehouse. All of these small inefficiencies add up.
Purchasing Incorrect Parts/Materials
If there are different versions of the BOM or if the BOM was updated and not properly shared, you will most definitely have purchased incorrect parts or materials.
For example, let’s assume there was a quality issue in the field. After analyzing the failure, you decide to change the grade of aluminum from aluminum 3003 to aluminum 6061.
If quality and engineering create this change but it is not communicated and shared with the purchasing team then you will continue to purchase aluminum 3001. The result is additional failures, growing warranty issues, and more.
Product Made Incorrectly
The engineering BOM (EBOM) and manufacturing BOM (MBOM) are usually quite different. The engineering team creates the BOM and hands it off to the manufacturing team. The manufacturing team decides they can’t make the product based on the specs from the engineering team and creates some tweaks and changes. However, these changes are usually not pushed back to the engineering team. Thus creating inconsistencies between what engineering experts and what manufacturing can make.
This can also affect the quality requirements that are created and the standards used with checking the quality of the parts.
What Can You Do Today?
These errors and increased costs occur because everyone is working on their own document. In the remote world and using suppliers and contractors around the world, the need for a centralized, shareable database is essential.
OpenBOM is a cloud-based platform that helps you manage your engineering and manufacturing data. Companies from startups to Fortune 500’s use OpenBOM to create a centralized database to bring in, store and manage their manufacturing data. With this infrastructure, users also use OpenBOM to streamline both their change management and PO processes.
If you need to improve the way you manage your data and processes, contact us today for a free consultation.
Regards,
Jared Haw
Join our newsletter to receive a weekly portion of news, articles, and tips about OpenBOM and our community.