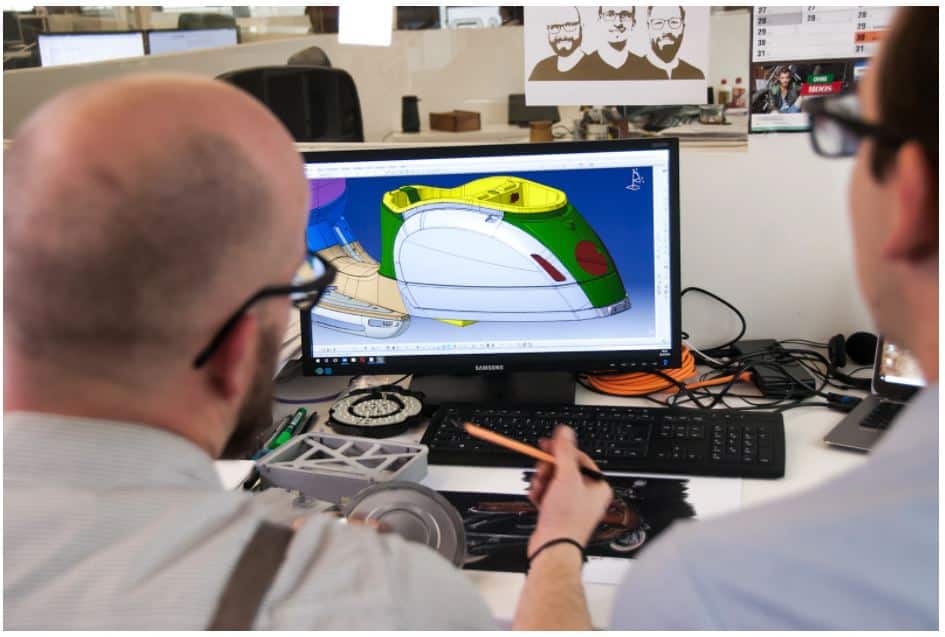
Today, I’ll be continuing a series of blogs about contract manufacturing. In today’s blog post I want to talk about DFM (Design For Manufacturability) and how you should think about DFM in the context of Contract Manufacturing.
Let’s assume you have a new product you’re looking at bringing to the market. You have gone through all of the proper steps to evaluate a few suppliers, provide them with an RFQ, and finally choose who you want to work with.
But, unless you are making a commoditized product, you can’t move straight into production. There is a transition from later stage development to production. This is called design for manufacturing (DFM) or design for manufacturing and assembly (DFMA).
What is DFM and DFMA?
According to Quality-One, DFM and DFMA “enables a product design to be efficiently manufactured and easily assembled with minimum labor cost. Through the use of DFM/A, a company can prevent, detect, quantify and eliminate waste and manufacturing inefficiency within a product design.”
DFMA becomes increasingly more important as you get closer to manufacturing. Going through the proper DFMA steps will transition you from later stage development to product launch and then scale up. Not taking the proper steps will cause a slow down in each of these steps.
Here are a few steps and processes DFMA looks at.
Tooling Design
One of the leading aspects of DFM is reviewing the tool design. For a plastic part, you have to look at multiple parts of the design. Such as, draft, sink, gates, ridges, ejectors, and more. Usually, when a part is originally designed, it’s designed to work and that’s it. DFM at the tooling stage will make sure the parts can be made well without any quality issues.
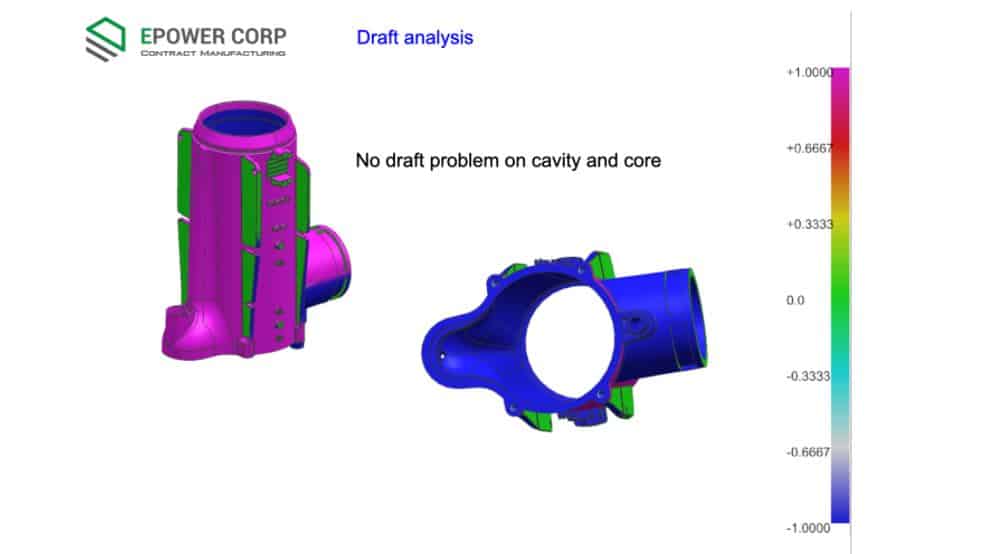
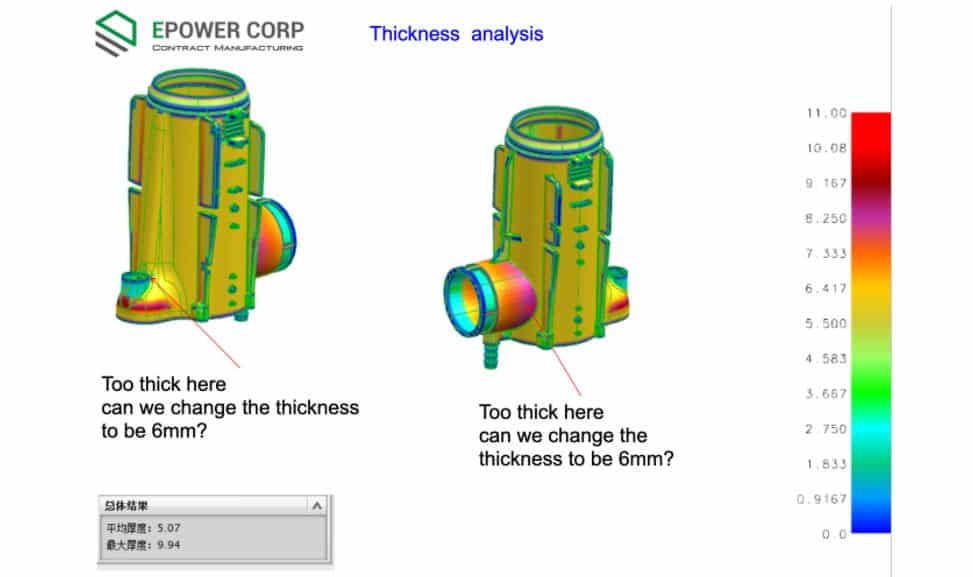
Below are pictures of a plastic pipe that went through DFM.Quality
Quality is built into the design of a product. Therefore, if the design is not optimized for production, the product will have numerous quality problems which lead to extended lead times, pricing problems, and customer complaints.
DFM and DFMA is carried out to minimize the risk of quality issues occurring during material procurement, fabrication, and during the assembling of the product.
During fabrication you also have waste. DFM will look at ways to eliminate (or reduce) waste by optimizing your design.
Price
Prices are not necessarily fixed depending on whether or not you can find alternative parts or by changing the design, materials, and processes. In this case, DFM will look at the cost-effectiveness of changing the design, material, and processes or finding alternative components, especially helpful during the chip shortage. Of course, this is done while analyzing the quality as well.
Who can Help?
In my next post, I’ll cover this in much more detail. But for now, I’ll give you my short answer. My simple logic is that it makes sense for the contracted company to carry out the DFM. So, for example, if you hired a contract assembly company for final assembly, they should look at DFM for final assembly. On the other hand, your plastic injection molding supplier should review the DFM for tool design and part optimization. And so on for all the parts.
However, this can cause confusion and blame might be pushed around from supplier to supplier. Stay tuned for my next post as I’ll dive into this more.
Conclusion
OpenBOM improves the process of how you work with your CM, contractors, colleagues, and other team members. We provide you with the capabilities to seamlessly manage your parts, vendors, bill of materials, purchase orders, and change orders. All BOM, engineering, and manufacturing information are stored in the cloud which you can share with anyone.
Register for FREE to create your OpenBOM account and reach out to us via support @ openbom dot com if you have any questions.
Regards,
Jared Haw
Join our newsletter to receive a weekly portion of news, articles, and tips about OpenBOM and our community.