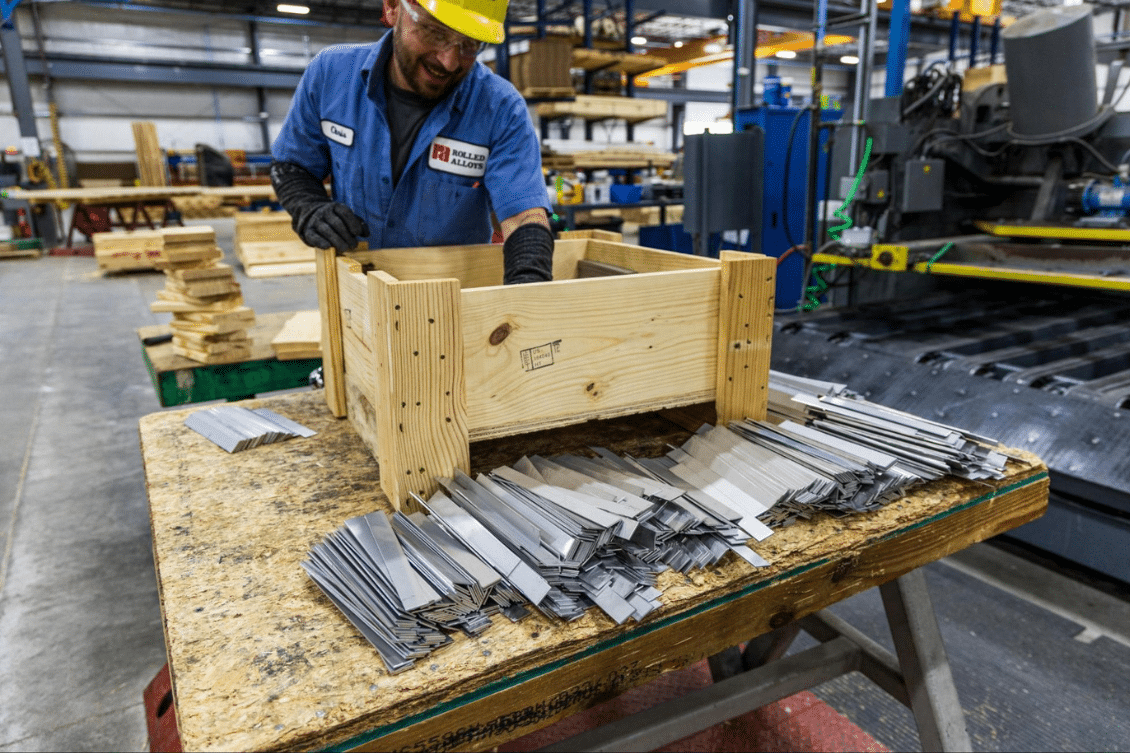
Dealing with mistakes made by suppliers is a crucial aspect of managing manufacturing processes and ensuring product quality and timely delivery. In manufacturing, challenges will always come up and mistakes will be made. But it’s good to differentiate those honest mistakes from those excuses that should have been avoided.
Understanding the common excuses made by suppliers when mistakes occur is essential for effectively navigating these challenges. By recognizing these excuses and learning how to address them proactively, manufacturers can mitigate risks, minimize disruptions, and develop stronger partnerships with their manufacturing counterparts.
In this blog, we will explore the top five excuses commonly made by non-local suppliers for mistakes in manufacturing processes. Each section will dive into the specific excuse and offer practical tips and strategies for handling these situations effectively.
Excuse #1: Miscommunication
Miscommunication is a prevalent issue in manufacturing, particularly when collaborating with suppliers that are not in the same region. Language barriers and cultural differences often contribute to misunderstandings between clients and manufacturers, leading to errors, delays, and dissatisfaction with the final product.
Here are the top causes of miscommunication:
- Language Barriers
- Cultural Differences
- Unclear Specifications
- Lack of Effective Communication Channels
Tips to Overcome Miscommunication:
If you are collaborating with suppliers then communication gaps will arise. However, if you decide to share your product data using Excel and emails then you can expect those issues to increase.
Here are some tips on how to overcome miscommunications:
Use Clear and Detailed Specifications
Provide comprehensive and precise specifications for your products, outlining requirements, dimensions, materials, and quality standards in detail. Clear documentation helps mitigate ambiguity and ensures that expectations are clearly communicated to the supplier.
Establish Open Communication Channels
Foster open and transparent communication channels with your supplier, encouraging dialogue, feedback, and clarification throughout the manufacturing process. Encourage factory personnel to seek clarification when instructions are unclear, and be proactive in addressing any concerns or questions raised by the manufacturer.
Create Your Single Source of Truth
In manufacturing, establishing a single source of truth is paramount to mitigate miscommunication and ensure alignment between clients and suppliers. A single source of truth refers to a centralized repository of accurate and up-to-date information that serves as the definitive reference point for all parties involved in the manufacturing process.
Excuse #2: Quality Control Issues
Quality control is a critical aspect of manufacturing processes, yet issues can arise due to varying standards and production processes, leading to errors, defects, and dissatisfaction with the final product. When working with suppliers, quality control issues may be cited as excuses for mistakes in manufacturing.
Here are the excuses that cause quality control issues:
- Varying Standards
- Ineffective Process Control
- Equipment Malfunctions
- Inadequate Training of Operators
Tips to Overcome Quality Control Issues
When you find a quality issue then you take preventative actions. However, no matter which supplier you are working with, there will be quality issues, it’s just going to happen. However, you would like these to be rare and non-recurring.
Here are some tips on what you can do to overcome quality control issues.
Conduct Regular Inspections
Implement a robust quality control program that includes routine inspections at various stages of the manufacturing process. Inspections should encompass raw materials, work-in-progress, and finished goods to identify defects, deviations, and non-conformities early on.
Set Clear Quality Standards
Establish clear quality standards and specifications for your products, outlining criteria for acceptable quality, tolerances, and performance requirements. Communicate these standards effectively to the supplier and ensure alignment with your expectations.
Invest in Training and Skill Development
Invest in training programs and skill development initiatives for factory personnel to enhance their knowledge, skills, and competencies in quality management and manufacturing best practices. Training programs should focus on quality assurance techniques, defect prevention strategies, and adherence to established quality standards.
Utilize Quality Control Tools and Techniques
Leverage quality control tools and techniques such as Six Sigma methodologies to monitor and improve manufacturing processes. These tools enable data-driven decision-making, identify areas for improvement, and optimize production efficiency.
Excuse #3: Production Delays
Production delays can significantly impact manufacturing timelines, leading to disruptions, increased costs, and dissatisfaction among clients. Suppliers may cite various reasons for production delays, ranging from raw material shortages to equipment malfunctions, which can hinder the timely completion of orders.
Here are the top excuses that cause production delays:
- Raw Material Shortages
- Equipment Malfunctions
- Logistics and Transportation Delays
- Supplier Performance Issues
Tips to Overcome Production Delays
Production delays can be costly for your business. Worst case scenario, you have a customer come to your website to purchase something, see you don’t have it available, and purchase something from your competitor. You end up losing this sale and perhaps returning customers as well.
Here are some tips on what you can do to overcome production delays.
Establish Realistic Timelines
Set realistic production timelines that account for potential delays, lead times, and contingencies. Collaborate closely with the supplier to establish achievable production schedules based on capacity, resource availability, and operational constraints.
Maintain Open Communication with the Supplier
Foster transparent and proactive communication channels with the supplier to address potential issues, anticipate challenges, and mitigate risks to production schedules. Encourage regular updates, status reports, and feedback mechanisms to facilitate timely decision-making and problem resolution.
Diversify and Qualify Backup Suppliers
Identify and qualify alternative suppliers or production sources for critical components or materials to mitigate the impact of supplier disruptions. Diversifying the supply chain reduces dependency on single suppliers and provides flexibility to navigate unforeseen challenges.
Excuse #4: Uncontrolled Costs
Uncontrolled costs pose significant challenges in manufacturing operations, impacting profitability, budget, and overall financial performance. Suppliers may encounter various factors contributing to uncontrolled costs. No matter the reason, these issues can cause significant strain between you and your supplier.
Here are the top excuses that cause uncontrolled costs:
- Unexpected Expenses
- Changes in Production Requirements
- Inefficient Resource Allocation
Tips to Overcome Uncontrolled Costs
Costs are usually subject to fluctuations whether it’s with currency conversions or component inflation. However, poorly managed production and not following the correct processes can lead to increased costs.
Here are some tips on what you can do to prevent costs from being uncontrollable.
Negotiate Clear Pricing Agreements
Establish clear and transparent pricing agreements with all suppliers, outlining cost breakdowns, payment terms, and pricing adjustments based on production volumes and market conditions. Clarify expectations regarding additional costs, change orders, and dispute resolution mechanisms to mitigate misunderstandings and minimize cost disputes.
Conduct Thorough Cost Analyses
Conduct comprehensive cost analyses to identify cost drivers, assess cost structures, and evaluate cost-saving opportunities throughout the manufacturing process. Analyze direct and indirect costs, overhead expenses, and cost drivers to optimize cost efficiency and enhance profitability.
Implement Cost Control Measures
Implement robust cost control measures to monitor and manage expenses throughout the production process. Establish budgetary controls, variance analysis mechanisms, and expense tracking systems to identify deviations from budgeted costs and implement corrective actions promptly.
Streamline Supply Chain Management
Optimize supply chain management practices to minimize procurement costs, reduce lead times, and enhance supplier collaboration. Consolidate purchasing volumes, negotiate favorable terms with suppliers, and leverage economies of scale to lower procurement costs and improve supply chain efficiency.
Excuse #5: Shipping and Logistics Issues
Shipping and logistics play a critical role in the global supply chain, facilitating the movement of goods from manufacturers to end customers. However, challenges such as customs delays, transportation disruptions, and logistical bottlenecks can impact the timely delivery of products manufactured by factories, leading to frustrations and excuses for delays.
Here are the top excuses for shipping and logistics issues:
- Customs Delays
- Transportation Disruptions
- Logistical Bottlenecks
Tips to Overcome Shipping and Logistics Issues
Production is completed, the products are about to leave the warehouse and then you get the dreaded email that your products will not be delivered to when expected. These are just as bad as production delays but they tend to shoot up out of nowhere.
Here are some tips on what you can do to prevent shipping and logistics issues.
Work with Reliable Freight Forwarders
Partner with reputable freight forwarders and logistics providers with expertise in navigating international shipping and customs clearance processes. Select providers with a proven track record of reliability, efficiency, and responsiveness to mitigate the risk of shipping delays and logistical challenges.
Plan for Potential Delays in Advance
Anticipate potential shipping delays and logistical disruptions by incorporating buffer times into production schedules and delivery timelines. Factor in lead times for customs clearance, transit delays, and unexpected contingencies to minimize the impact of unforeseen challenges on delivery schedules.
Diversify Shipping Routes and Carriers
Diversify shipping routes and carriers to reduce reliance on single transportation channels and mitigate the risk of disruptions. Explore alternative shipping options, transit routes, and carrier networks to optimize shipping efficiency and enhance supply chain resilience.
Monitor Shipment Status and Track Shipments
Implement shipment tracking and monitoring systems to track the status and location of shipments in real-time. Utilize tracking technologies, online shipment tracking portals, and automated alerts to stay informed about shipment progress, transit times, and potential delivery delays.
Conclusion
Navigating the complexities of manufacturing processes with suppliers requires proactive measures, strategic planning, and effective communication to address common challenges and ensure successful outcomes.
Setting up the correct processes while using technologies to support your processes is a step toward limiting miscommunications with your supplier.
OpenBOM is a cloud-based platform to manage your engineering and manufacturing data. Companies from startups to Fortune 500’s use OpenBOM to create a centralized database to bring in, store, and manage their manufacturing data. With this infrastructure, users also use OpenBOM to streamline both their change management and PO processes.
If you need to improve the way you manage your data and processes, contact us today for a free consultation.
Regards,
Jared Haw
Join our newsletter to receive a weekly portion of news, articles, and tips about OpenBOM and our community.